The Application Of Magnesium Alloy CNC Machining Technology For Notebook Computer Shell
At present, 3C products are developing rapidly and competition is fierce. Consumer groups have a particularly strong demand for the "light and thin" characteristics of 3C products. This has prompted 3C product machining and manufacturing technology to seek breakthroughs in materials and cnc machining techniques. Among them, magnesium alloy materials have become the new favorite of raw materials in the processing and manufacturing of 3C products.
- First of all, magnesium alloy is the lightest metal among practical metals. Its specific gravity is about 2/3 of that of aluminum and 1/4 of that of steel. It caters to 3C products; customer groups demand "light and thin" characteristics. In addition, magnesium alloy also has the characteristics of high specific strength, large elastic modulus, and good shock absorption, which is very suitable as a structural part of 3C electronic products. According to the data, if magnesium alloy is used to replace ABS plastic on the shell of 3C products, the weight of the material can be reduced by 36% and the thickness by 64%.
- Secondly, magnesium alloy has good heat dissipation. The thermal conductivity of magnesium alloy is 350 to 400 times that of ABS plastic. For electronic products that generate high temperatures inside, if magnesium alloy is used on the casing and heat dissipation components, there is no need for heat dissipation fans or heat dissipation holes in most cases.
- Finally, magnesium alloy has good electromagnetic shielding properties. Magnesium alloy has better magnetic shielding performance than aluminum alloy, better electromagnetic wave blocking function, and is more suitable for making precision electronic products that are easily interfered by the outside world. It can also be used as the casing of electronic products that generate electromagnetic radiation such as computers and mobile phones to reduce the radiation harm of electromagnetic waves to the human body.
Advantages Of Magnesium Alloy CNC Machining Technology In 3C Products
Magnesium alloy materials have the characteristics of being flammable and corrosive in machining. Compared with traditional metal materials such as iron and aluminum, they are not suitable for cutting. Therefore, in the initial stage of application of magnesium alloy materials, die-casting, die-casting and other process methods are more widely used for forming. However, with the development of 3C product technology, such a forming method is difficult to meet the demand. First of all, with the increasing miniaturization and integration of 3C products, the shell structure of 3C products is becoming more and more complex, and it is difficult to accurately form the process methods such as die-casting and die-casting; secondly, the development and manufacturing cycle of 3C products is getting shorter and shorter. The mold opening cycle of die casting and die casting severely restricts its production cycle.
Finally, there is a serious contradiction between the consumer group's zero tolerance for product appearance defects and the almost inevitable casting defects. Therefore, more and more attention is paid to the CNC machining technology of magnesium alloy.
The Analysis of Magnesium CNC Machining Notebook Computer Shell.
- Process analysis: A notebook computer shell made of magnesium alloy ME20. The part has a complex structure and high dimensional accuracy requirements, so it is formed by milling the magnesium alloy sheet as a whole. Magnesium machining is very different from traditional aluminum alloy machining in terms of tool selection, cutting parameter selection, cutting plan selection, cutting fluid selection and anti-corrosion measures, and chip treatment.
- Tool selection: Magnesium alloy has good thermal conductivity, soft material and low cutting force, so the heat dissipation rate during machining is very fast, and the amount of sticking is small, so the tool life can be very long. However, cutting tools used for magnesium alloy machining are required to keep the cutting edges sharp, because tools with larger cutting edges will increase the friction during the cutting process, which will lead to a significant increase in cutting temperature, causing magnesium chips to flash or even burn, resulting in Unsafe factors in the cutting process increase. Therefore, magnesium alloy machining generally requires the selection of new carbide tools, and old tools that have been processed with other materials cannot be mixed. The general tool design principles for machining steel and aluminum are also applicable to tools for machining magnesium alloys. Because the cutting resistance of magnesium alloy is low, and the heat capacity is also quite low, the number of teeth of the milling cutter used for magnesium alloy machining is larger than that of other metals. Reducing the number of teeth can increase the chip space and the amount of feed, which can reduce friction heating and increase chip clearance, reduce the distortion of chips, and reduce power consumption and heat generation. The author's company generally prefers three-edged carbide end mills when machining magnesium alloys. In special circumstances, such as insufficient blade length of the three-blade tool, unsuitable diameter specifications, etc., four-blade carbide end mills can also be used.
- Cutting fluid selection: Magnesium alloy material is soft and easy to cut. Whether using high speed or low speed, with or without cutting fluid, a very smooth surface can be achieved. Dry machining without cutting fluid can reduce machining costs, and waste chips can be easily collected, stored and transported. Therefore, in many references, dry machining is recommended.However, there is a risk of fire when dry machining uses high speed and forms fine chips. This requires the CNC operator to observe the machining conditions at any time, and in case of a fire, it can be extinguished immediately, but this method still has immeasurable risks. This limits the operator's inability to achieve the one-person multi-machine working mode, which is not cost-effective in terms of overall processing cost and efficiency. In addition, magnesium alloys tend to expand when heated. According to the data, the linear expansion coefficient of magnesium alloy in the temperature range of 20℃~200℃ is 26.6~27.4μm/(m·℃) (related to alloy composition). Taking the length dimension of 200mm as an example, if the temperature rises by 10°C during processing, the processing error will be 0.0532~0.0548mm. It can be seen that if dry cutting is used, there is no cutting fluid drop.Temperature, magnesium alloy parts will expand due to the rapid increase in temperature, which will affect the machining accuracy. The notebook casing has high requirements for dimensional accuracy, and such temperature effects cannot be ignored. Based on the above two considerations, the CNC machining of this magnesium alloy adopts "wet" machining using cutting fluid. For this reason, we specially introduced Castrol MG type magnesium alloy cutting fluid.
- Selection of cutting parameters: The cutting parameters of CNC milling include spindle speed, feed rate, tool depth of cut and tool width of cut. We chose a domestic machine tool for magnesium alloy machining. The theoretical high speed of the machine tool can reach 8000r/min, the maximum feed rate is 15m/min, and the machining accuracy is 0.01mm. Using this machine tool to maintain the highest speed for a long time is detrimental to the machine tool. Too fast feed rate, for single-piece small batch production, does not save too much time, but greatly increases the quality risk and the probability of equipment failure. Therefore, we use large cutting depth and small feed to determine our cutting parameters. According to many years of CNC machining experience, when the carbide end mill is machining different materials, the speed and feed in the cutting parameters change, but the depth and width of cut generally do not change much: for rough machining, the recommended width of cut is 50% ~100%D (D is the tool diameter), the recommended cutting depth is 0.3~0.5D. For finishing, the recommended cutting width is 0.1~0.5mm and the cutting depth is 0.5~1D.
- Anti-corrosion measures in the CNC machining of magnesium alloys. It is generally believed that magnesium alloys are chemically active and easy to corrode. Especially after "wet" machining, magnesium alloy parts contaminated with cutting fluid are more likely to corrode. In fact, according to the machining experience of this unit, if effective anti-corrosion measures are adopted for magnesium alloy in a relatively short machining cycle, it will not cause serious corrosion that affects the structural strength or surface roughness.
We take the following measures to alleviate magnesium alloy corrosion
- The magnesium alloy CNC machining process must be operated continuously, and the parts covered with cutting fluid cannot be placed on the workbench for a long time, let alone overnight.
- The finished magnesium alloy parts are washed several times in clean water to fully dilute the residue of the chipping liquid.
- The washed magnesium alloy parts should be quickly blown dry with a high-pressure air gun, and then wiped dry with a clean cotton gauze.
- The finished parts can be placed in the foam box for a short time, and it is forbidden to touch other metals.
- When the parts are placed for a long time or are delivered for turnover, put them in a dry plastic bag with the bag mouth folded to ensure that the air in the bag is relatively uncirculated.
In fact, although the above method is simple and easy to implement, it cannot completely prevent magnesium alloy corrosion. Even if the surface of the part is dark or has a small amount of black spots, it can be removed by spraying dry sand. To define whether the corrosion degree of the magnesium alloy surface is acceptable or not, it is necessary to fully communicate with the technical personnel in the magnesium alloy surface treatment link to formulate corresponding markings and specifications.
Please keep the source and address of this article for reprinting: The Application Of Magnesium Alloy CNC Machining Technology For Notebook Computer Shell
Minghe Casting Company are dedicated to manufacture and provide quality and high performance Casting Parts(metal die casting parts range mainly include Thin-Wall Die Casting,Hot Chamber Die Casting,Cold Chamber Die Casting),Round Service(Die Casting Service,Cnc Machining,Mold Making,Surface Treatment).Any custom Aluminum die casting, magnesium or Zamak/zinc die casting and other castings requirements are welcome to contact us.
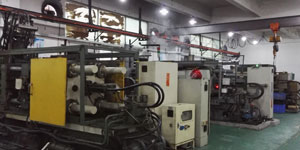
Under the control of ISO9001 and TS 16949,All processes are carried out through hundreds of advanced die casting machines, 5-axis machines, and other facilities, ranging from blasters to Ultra Sonic washing machines.Minghe not only has advanced equipment but also have professional team of experienced engineers,operators and inspectors to make the customer’s design come true.
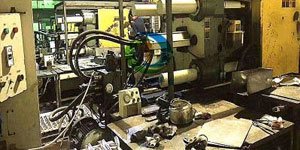
Contract manufacturer of die castings. Capabilities include cold chamber aluminum die casting parts from 0.15 lbs. to 6 lbs., quick change set up, and machining. Value-added services include polishing, vibrating, deburring, shot blasting, painting, plating, coating, assembly, and tooling. Materials worked with include alloys such as 360, 380, 383, and 413.
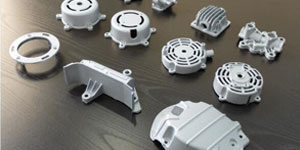
Zinc die casting design assistance/concurrent engineering services. Custom manufacturer of precision zinc die castings. Miniature castings, high pressure die castings, multi-slide mold castings, conventional mold castings, unit die and independent die castings and cavity sealed castings can be manufactured. Castings can be manufactured in lengths and widths up to 24 in. in +/-0.0005 in. tolerance.
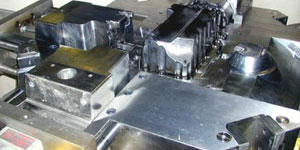
ISO 9001: 2015 certified manufacturer of die cast magnesium, Capabilities include high-pressure magnesium die casting up to 200 ton hot chamber & 3000 ton cold chamber, tooling design, polishing, molding, machining, powder & liquid painting, full QA with CMM capabilities, assembly, packaging & delivery.
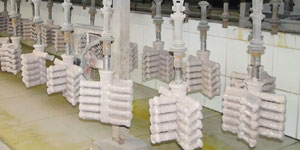
ITAF16949 certified. Additional Casting Service Include investment casting,sand casting,Gravity Casting, Lost Foam Casting,Centrifugal Casting,Vacuum Casting,Permanent Mold Casting,.Capabilities include EDI, engineering assistance, solid modeling and secondary processing.
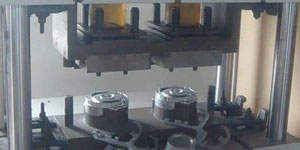
Casting Industries Parts Case Studies for: Cars, Bikes, Aircraft, Musical instruments, Watercraft, Optical devices, Sensors, Models, Electronic devices, Enclosures, Clocks, Machinery, Engines, Furniture, Jewelry, Jigs, Telecom, Lighting, Medical devices, Photographic devices, Robots, Sculptures, Sound equipment, Sporting equipment, Tooling, Toys and more.
What Can we help you do next?
∇ Go To Homepage For Die Casting China
→Casting Parts-Find out what we have done.
→Ralated Tips About Die Casting Services
By Minghe Die Casting Manufacturer |Categories: Helpful Articles |Material Tags: Aluminum Casting, Zinc Casting, Magnesium Casting, Titanium Casting, Stainless Steel Casting, Brass Casting,Bronze Casting,Casting Video,Company History,Aluminum Die Casting |Comments Off