Gravity Casting
What is Metal Gravity Casting
There are many process methods to make metal materials into required products, such as casting, forging, extrusion, rolling, drawing, stamping, cutting, powder metallurgy and so on. Among them, casting is the most basic, most commonly used and most extensive process.
The molten metal is poured into a hollow mold made of high temperature resistant materials, and the product with the desired shape is obtained after condensation. This is casting. The resulting product is a casting.
Casting can be divided into ferrous metal casting (including cast iron, cast steel) and non-ferrous metal casting (including aluminum alloy, copper alloy, zinc alloy, magnesium alloy, etc.) according to the material of the casting. The non-ferrous precision casting factory specializes in non-ferrous metal casting, focusing on aluminum alloy and zinc alloy casting.
Casting can be divided into sand casting and metal casting according to the material of the casting mold. Minghe Precision Casting Factory is very comfortable with these two casting processes, and designs and manufactures these two types of casting molds by itself.
Casting can also be divided into gravity casting and pressure casting according to the pouring process of molten metal. Gravity casting refers to the process of injecting molten metal into a mold under the action of the earth's gravity, also known as gravity casting. The generalized gravity casting includes sand casting, metal casting, investment casting, lost foam casting, mud casting, etc. The narrow gravity casting mainly refers to metal casting.
The narrow meaning of gravity casting specifically refers to metal casting.
Pressure casting refers to the process of injecting molten metal into the mold under the action of other external forces (excluding gravity). Die casting in a broad sense includes pressure casting and vacuum casting of die casting machine, low pressure casting, centrifugal casting, etc.; pressure casting in a narrow sense refers to metal die casting of die casting machine, referred to as die casting. The precision casting factory has long been engaged in the gravity casting of sand and metal molds. These casting processes are the most commonly used in non-ferrous metal casting and the lowest relative price.
With decades of years in the gravity casting industry, Minghe Gravity Casting services can meet the needs of customers in the production of high-volume & low-cost casting parts. Custom Gravity Castings with simple or complex shapes can be handled at our factory. Endless gravity casting possibilities are allowed. Once you selected us, our engineers will start with understanding your demands, select the gravity casting design suits the application, figure out the gravity casting shapes, dimensions, specifications, tolerances, and all of the details before production. We have accomplished operators in the workshop to execute each operation in a correct way to ensure the products meet or exceed international standards and customer expectations. Strong, lightweight, and corrosion-resistant casting products can be obtained through a fast and efficient gravity casting process.
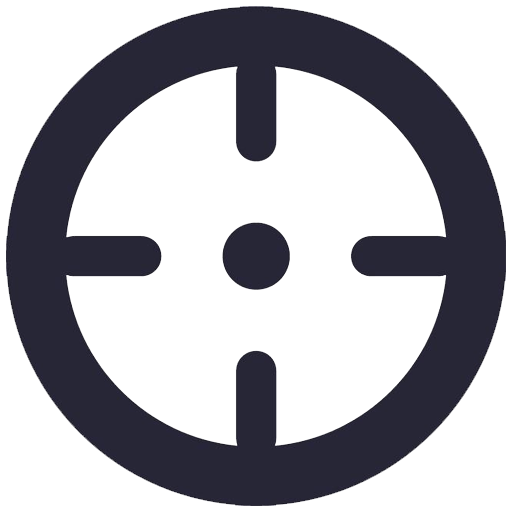
Benefits of Gravity Casting Process
The functions of Gravity casting can be summarized as follows:
- – Can produce large parts
- – Can form complex shapes
- – High strength parts
- – Very good surface finish and accuracy
- – High production rate
- – Gravity Casting seems to be especially useful when dealing with aluminum and other light alloys
- – One of the most common uses for gravity casting is when permanent molds are going to be used.
- – Gravity casting is used for the permanent mold process with pleasing results.
- – Relying on gravity will take patience, although it will be needed for larger products.
- – Corrosion resistance, high pressure resistance, durable, suitable for heating systems of different water quality.
- – The heat transfer resistance and tube expansion composite process are simplified, and the overall heat dissipation performance of the heating system is improved.
- – Excellent thermal performance and high metal thermal strength.
- – Avoid the wall of heat dissipation and airflow, and the heat dissipation effect is the best.
- – Free assembly, flexible assembly and convenient installation.
- – Simple, beautiful and generous, can coexist and coexist harmoniously with die-casting, and die-casting is reliable
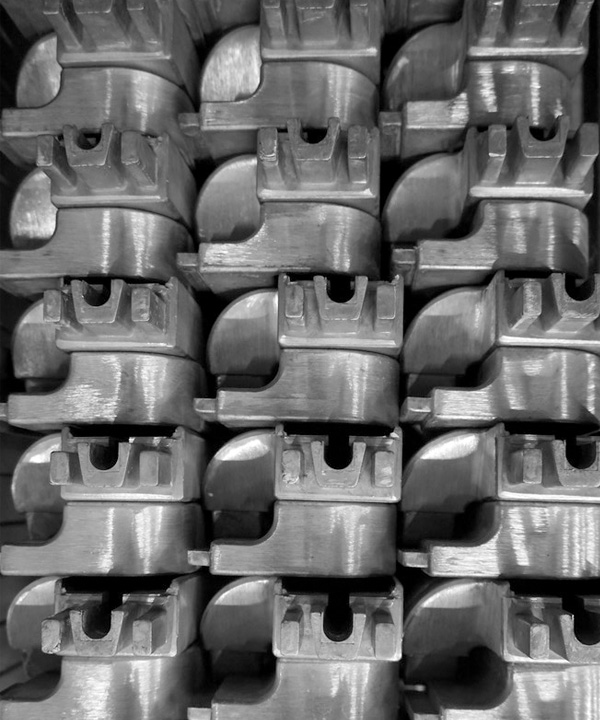
Different Types Production Equipment Of Gravity Casting
Strictly speaking, casting machinery equipment is a machine that uses this technology to smelt metal into a liquid that meets certain requirements and pour it into a casting mold. After cooling, solidification, and cleaning, castings with predetermined shapes, sizes and properties are obtained. On the other hand, machinery and equipment related to casting can also be classified as casting equipment
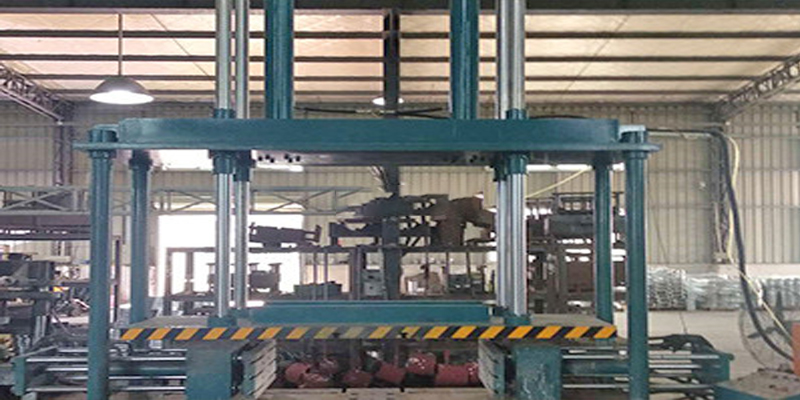
Gravity casting equipment ▶ |
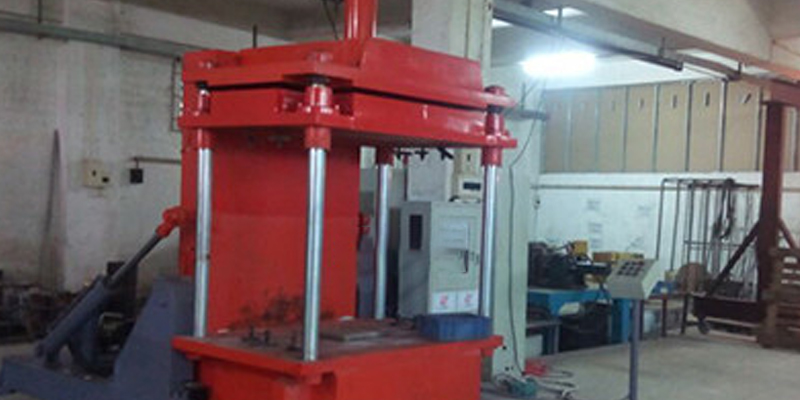
Gravity casting equipment2 ▶ |
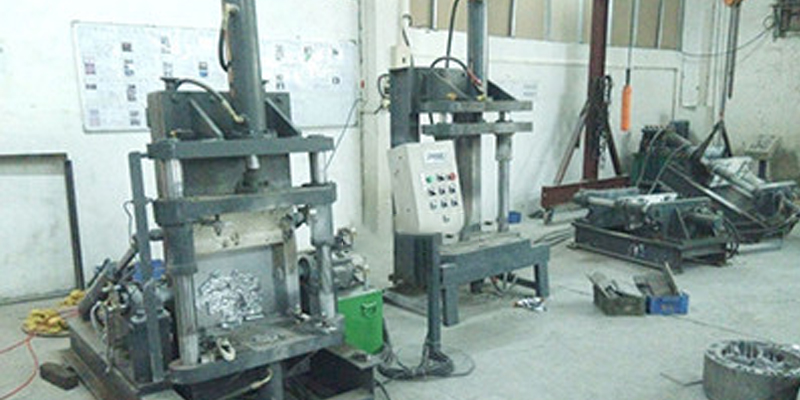
Gravity casting equipment3 ▶ |
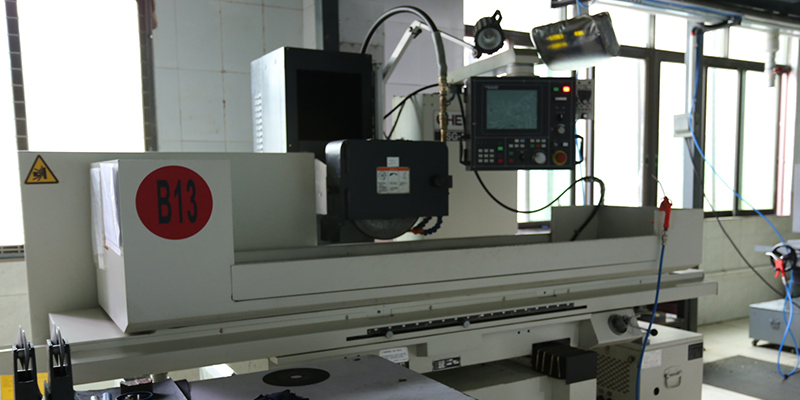
Lager grinder ▶ |
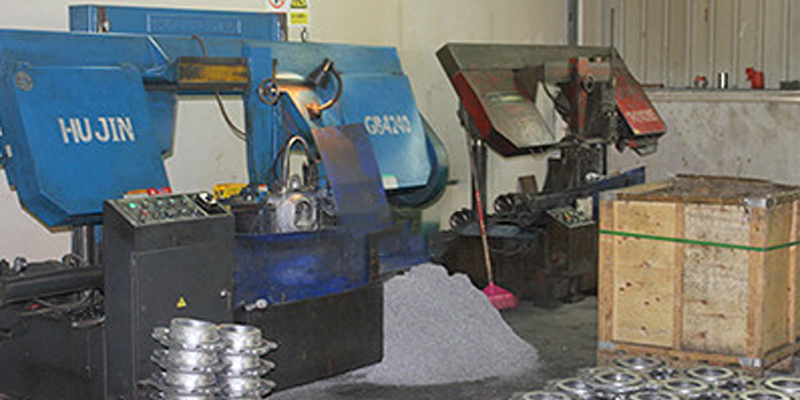
Riser cutting machine ▶ |
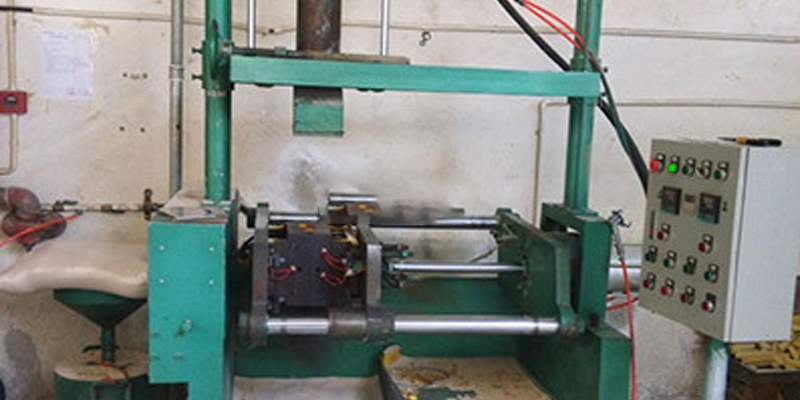
Sand core machine▶ |
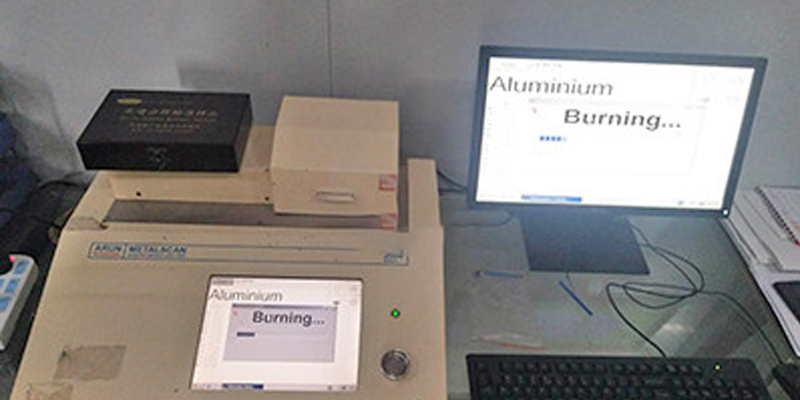
Spectrometer ▶ |
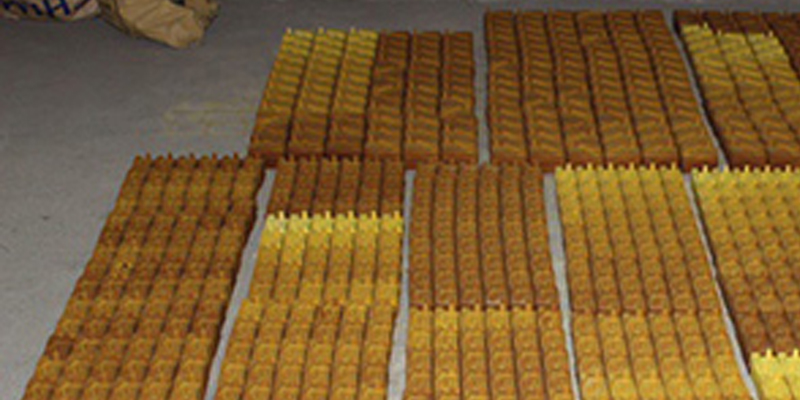
Sand core▶ |
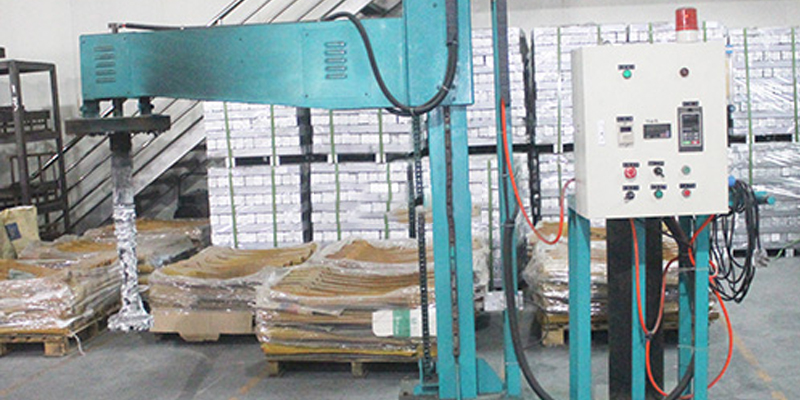
Aluminum liquid refining machine ▶ |
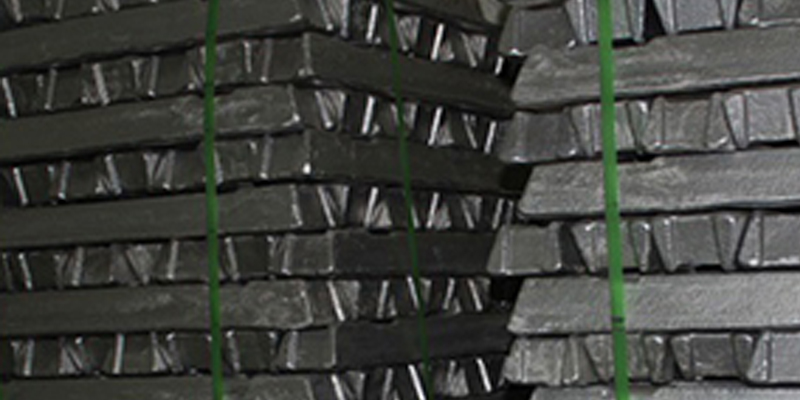
Aluminum ingot▶ |
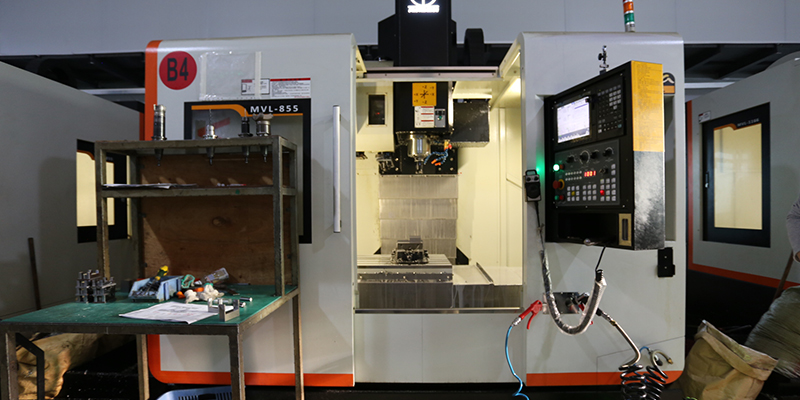
Cnc machine ▶ |

Electric stove▶ |
The Minghe Case Studies Of Gravity Casting
Minghe Casting fabrication services are available for both design to reality and low to high volume production runs of your die casting parts,sand casting parts,investment casting parts,metal casting parts, lost foam casting parts and more.
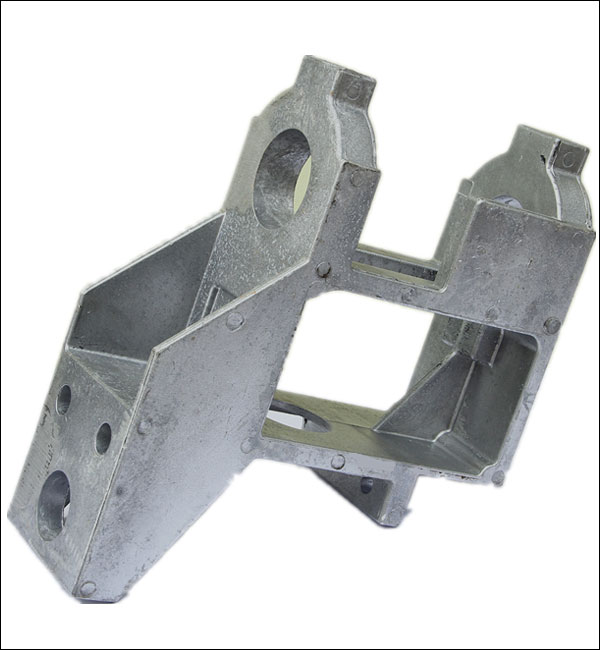
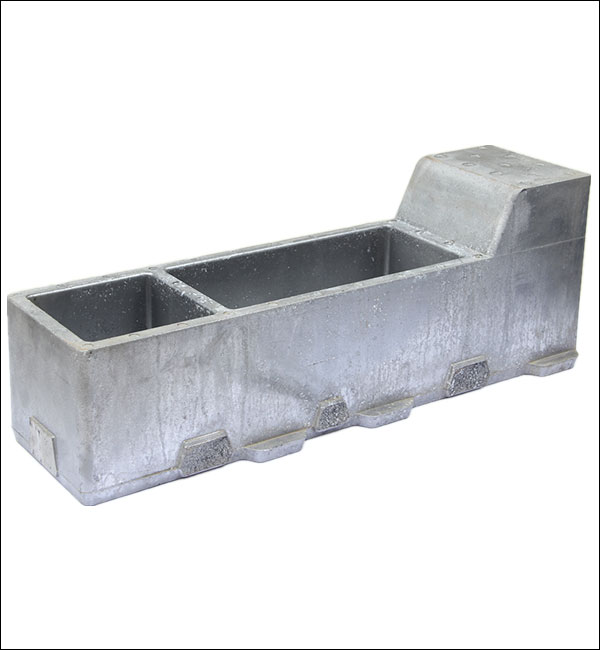
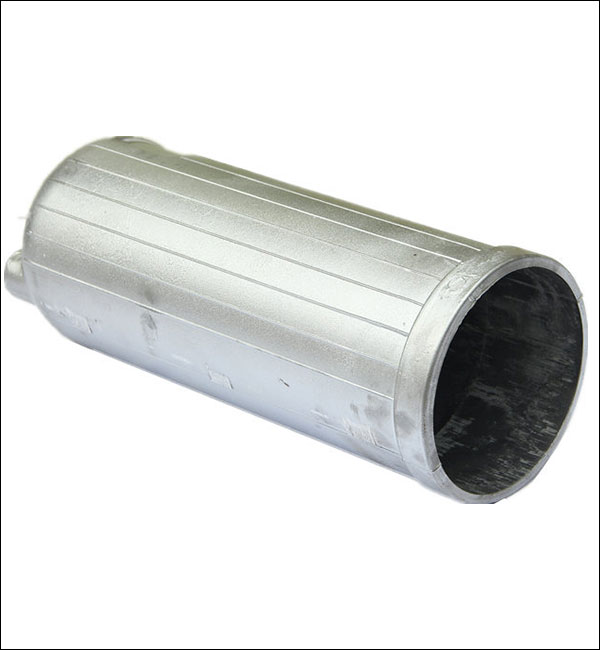
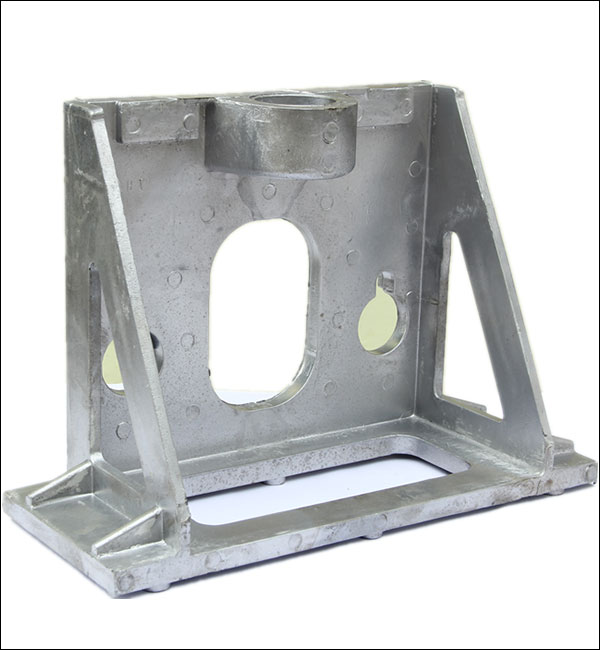
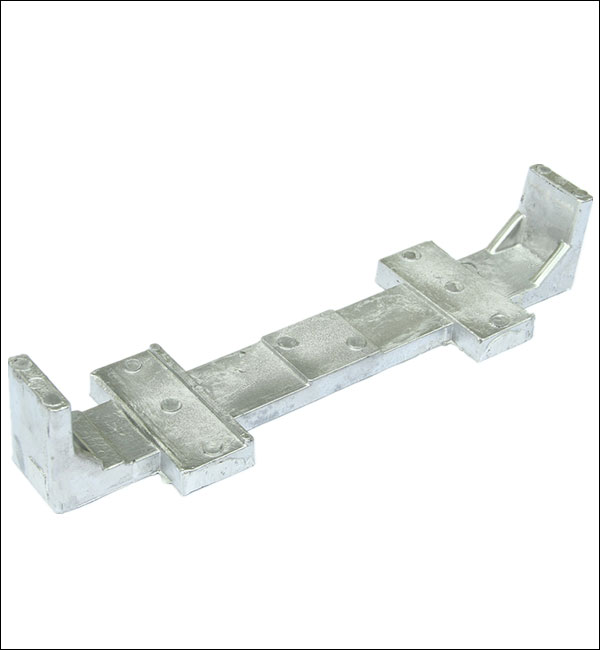
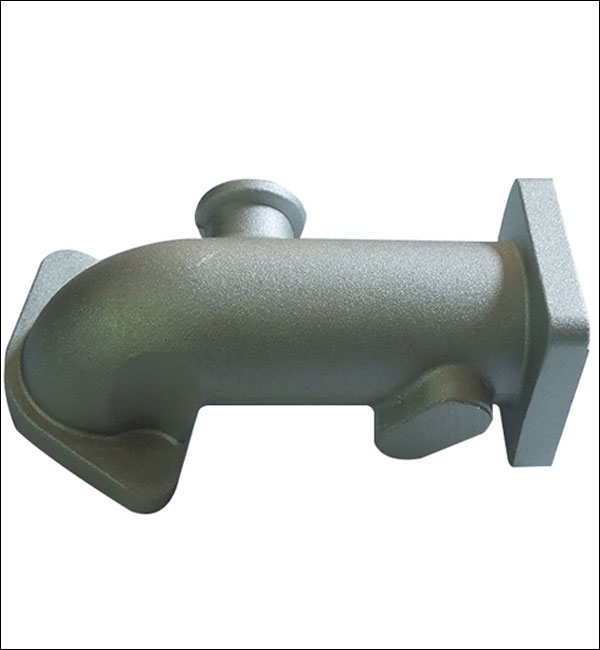
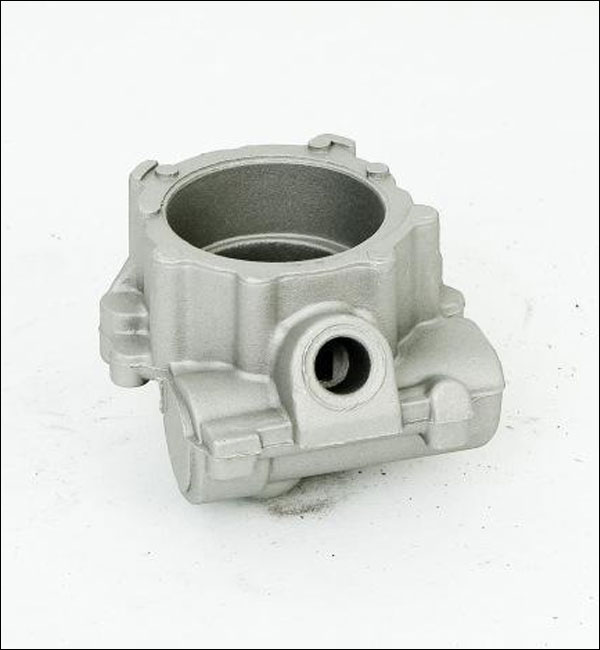
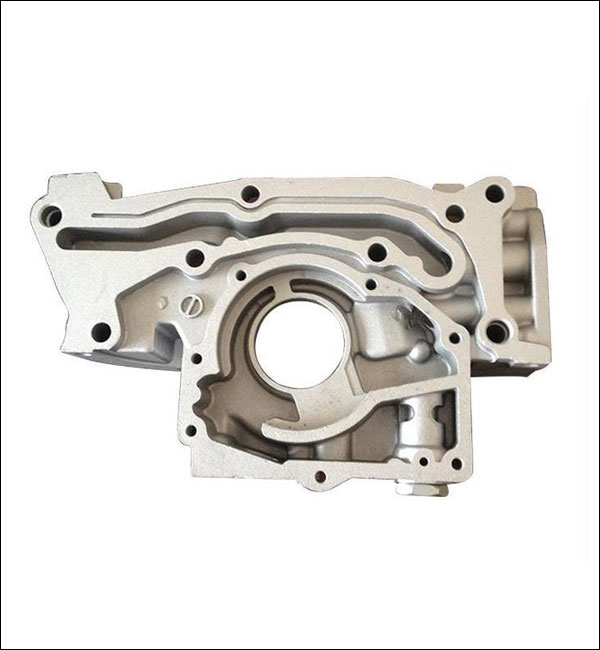
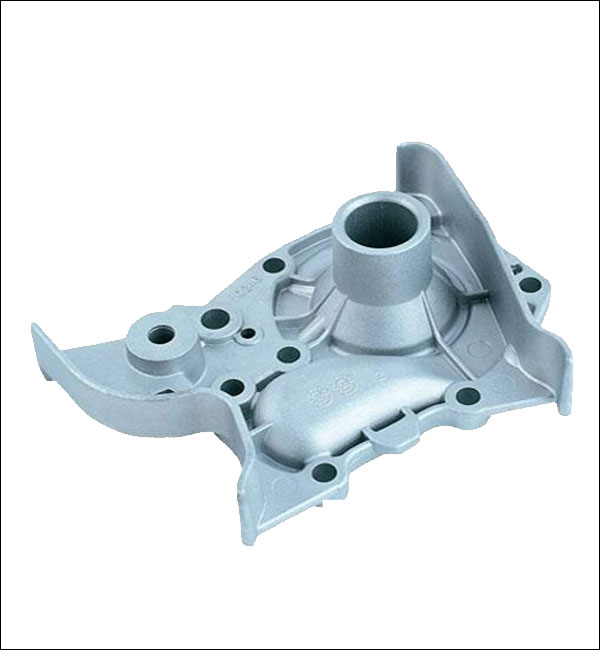
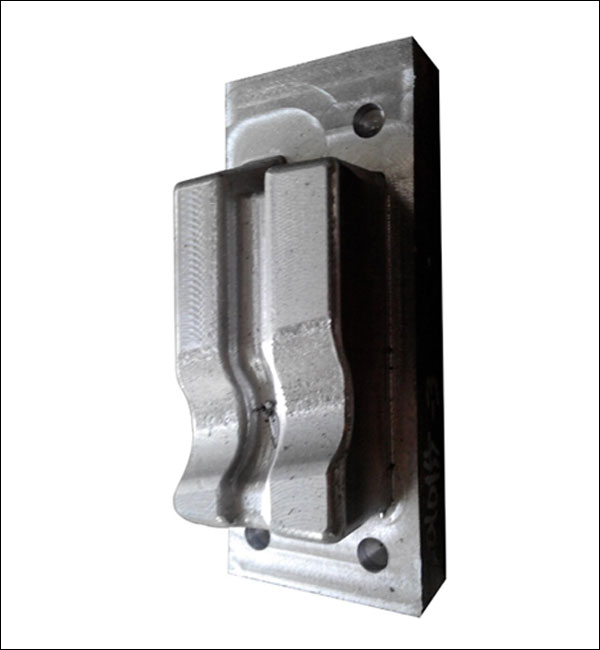
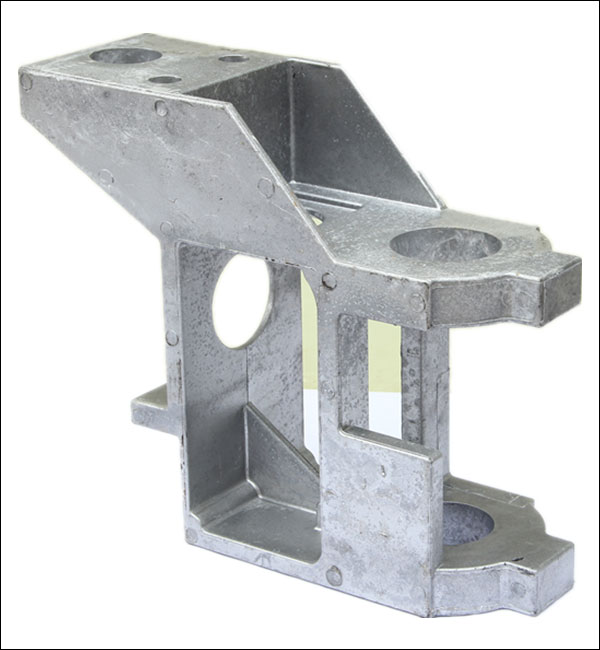
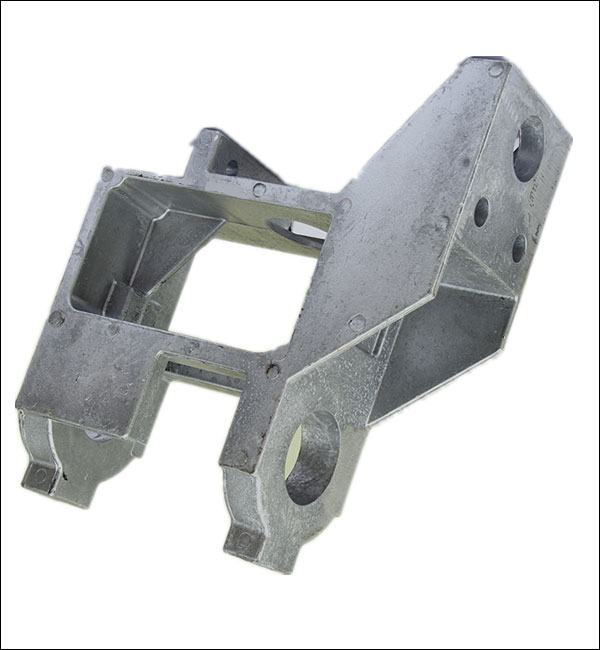
Go To View More Casting Parts Cases Studies >>>
Choose the Best Gravity Casting Supplier
As a full-service metal gravity casting foundry, we support you from the pattern design to finished casting and machining through investment casting (lost wax process), sand casting, CNC machining, engineering design and heat treatment as well as surface treatment for the stainless steel castings, alloy steel castings, carbon steel castings, grey cast iron castings, ductile cast iron castings and non-ferrous metal castings. The industries we are serving mainly cover valve and pumps, auto parts, agricultural machineries, railroad freight cars, logistics equipment, construction machineries, etc.
Contact us or Email sales@hmminghe.com to see how our people, equipment and tooling can bring the best quality for the best price for your gravity casting project.
We Provide Casting Services Include:
Minghe Casting services working with sand casting、metal casting 、investment casting lost foam casting, and more.
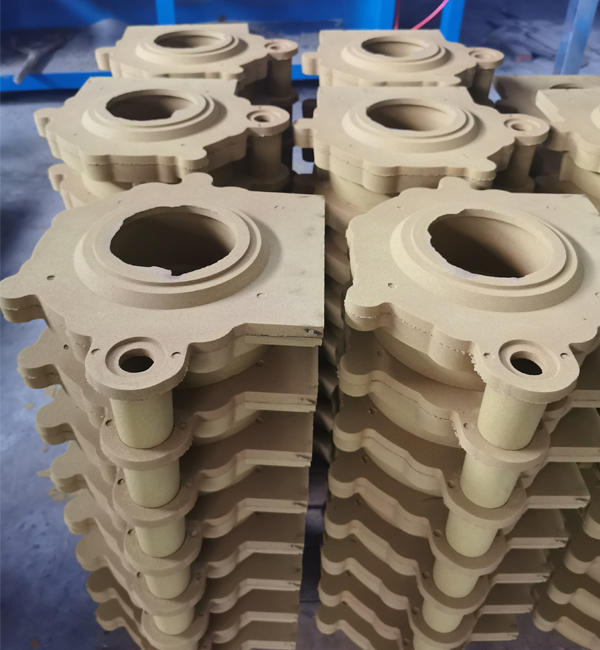
Sand Casting
Sand Casting is a traditional casting process that uses sand as the main modeling material to make molds. Gravity casting is generally used for sand molds, and low-pressure casting, centrifugal casting and other processes can also be used when there are special requirements. Sand casting has a wide range of adaptability, small pieces, large pieces, simple pieces, complex pieces, single pieces, and large quantities can be used.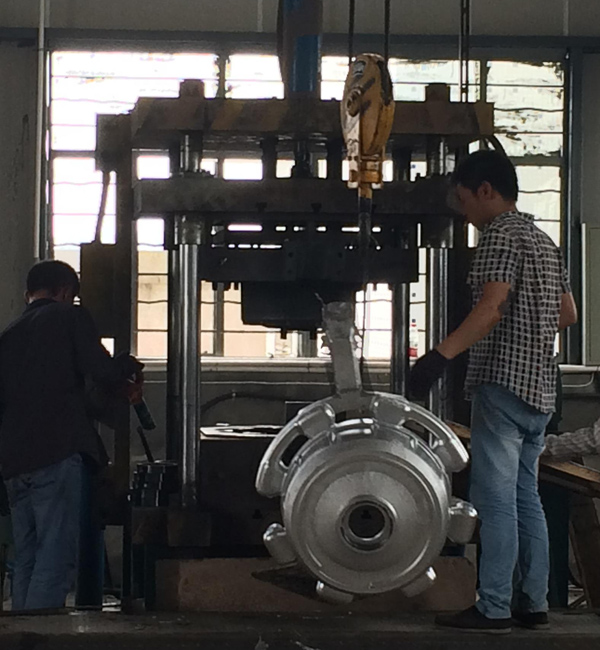
Permanent Mold Casting
Permanent Mold Casting have a long life and high production efficiency, not only have good dimensional accuracy and smooth surface, but also have higher strength than sand castings and are less likely to be damaged when the same molten metal is poured. Therefore, in the mass production of medium and small non-ferrous metal castings, as long as the melting point of the casting material is not too high, metal casting is generally preferred.
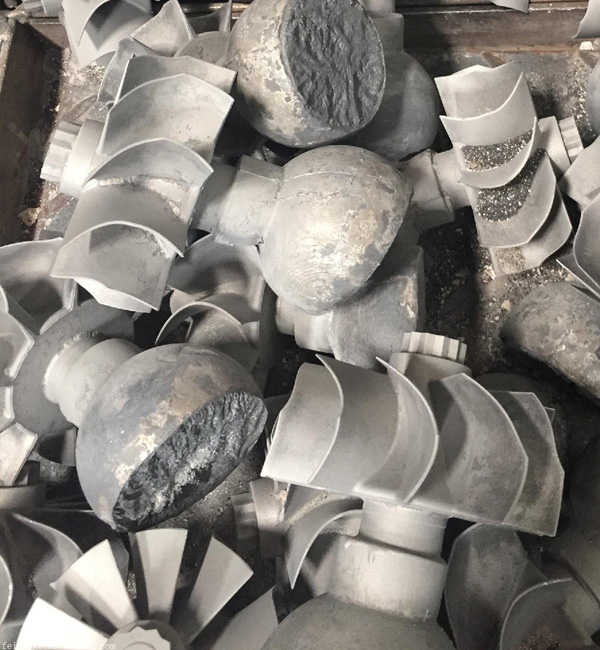
Investment Casting
The biggest advantage of investment casting is that because investment castings have high dimensional accuracy and surface finish, they can reduce machining work, but leave a little machining allowance on the parts with higher requirements. It can be seen that the use of investment casting method can save a lot of machine tool equipment and processing man-hours, and greatly save metal raw materials.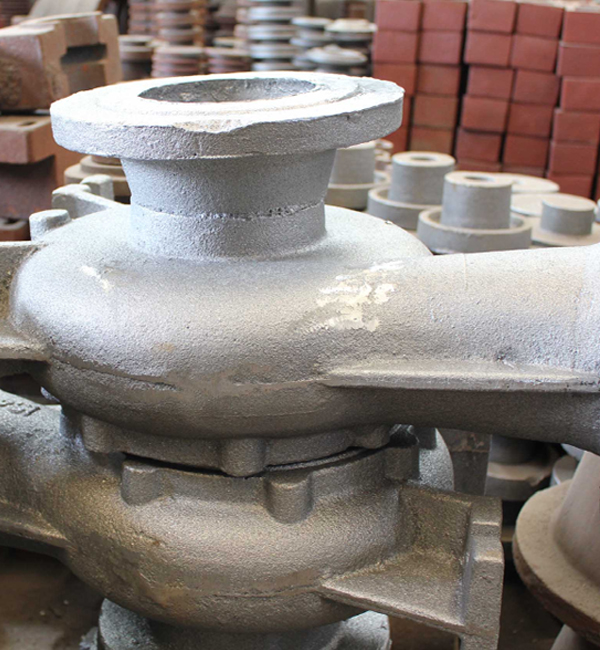
Lost Foam Casting
Lost foam casting is to combine paraffin wax or foam models similar to the casting size and shape into model clusters. After brushing and drying refractory coatings, they are buried in dry quartz sand for vibration modeling, and poured under negative pressure to gasify the model. , The liquid metal occupies the position of the model and forms a new casting method after solidification and cooling.
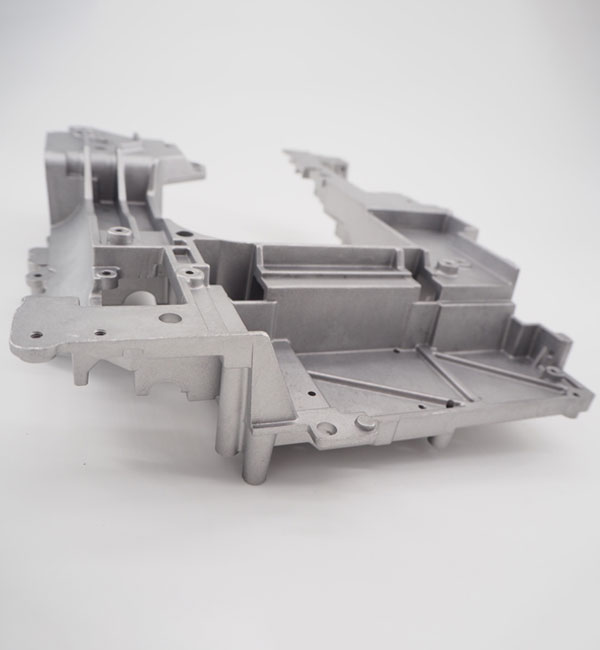
Die Casting
Die casting is a metal casting process, which is characterized by applying high pressure to the molten metal using the cavity of the mold. Molds are usually made of higher-strength alloys, and this process is somewhat similar to injection molding. Most die castings are iron-free, such as zinc, copper, aluminum, magnesium, lead, tin, and lead-tin alloys and their alloys. Minghe has been China's top die casting service since 1995.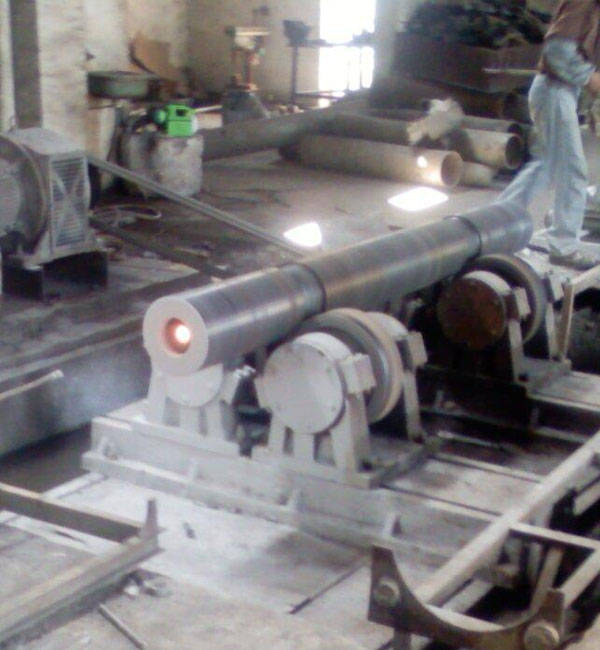
Centrifugal Casting
Centrifugal Casting is a technique and method of injecting liquid metal into a high-speed rotating mold, so that the liquid metal is centrifugal motion to fill the mold and form a casting. Due to the centrifugal movement, the liquid metal can fill the mold well in the radial direction and form the free surface of the casting; it affects the crystallization process of the metal, thereby improving the mechanical and physical properties of the casting.
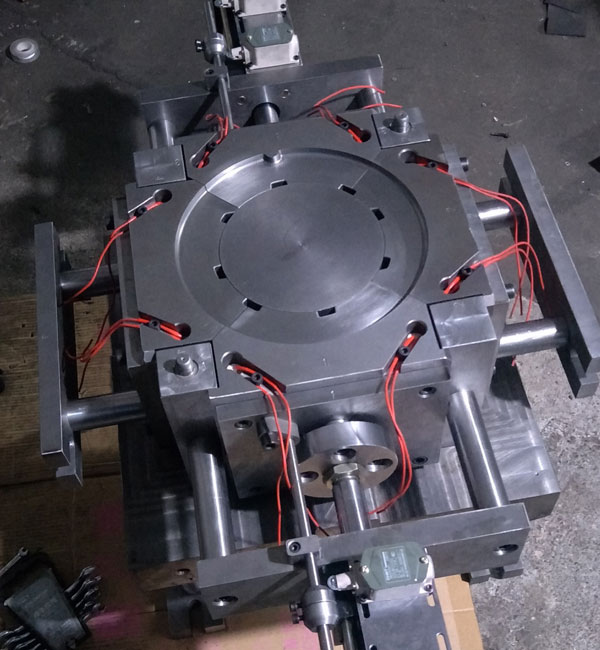
Low Pressure Casting
Low Pressure Casting means that the mold is generally placed above a sealed crucible, and compressed air is introduced into the crucible to cause a low pressure (0.06~0.15MPa) on the surface of the molten metal, so that the molten metal rises from the riser pipe to fill the mold and control Solidified casting method. This casting method has good feeding and dense structure, easy to cast large thin-walled complex castings, no risers, and a metal recovery rate of 95%. No pollution, easy to realize automation.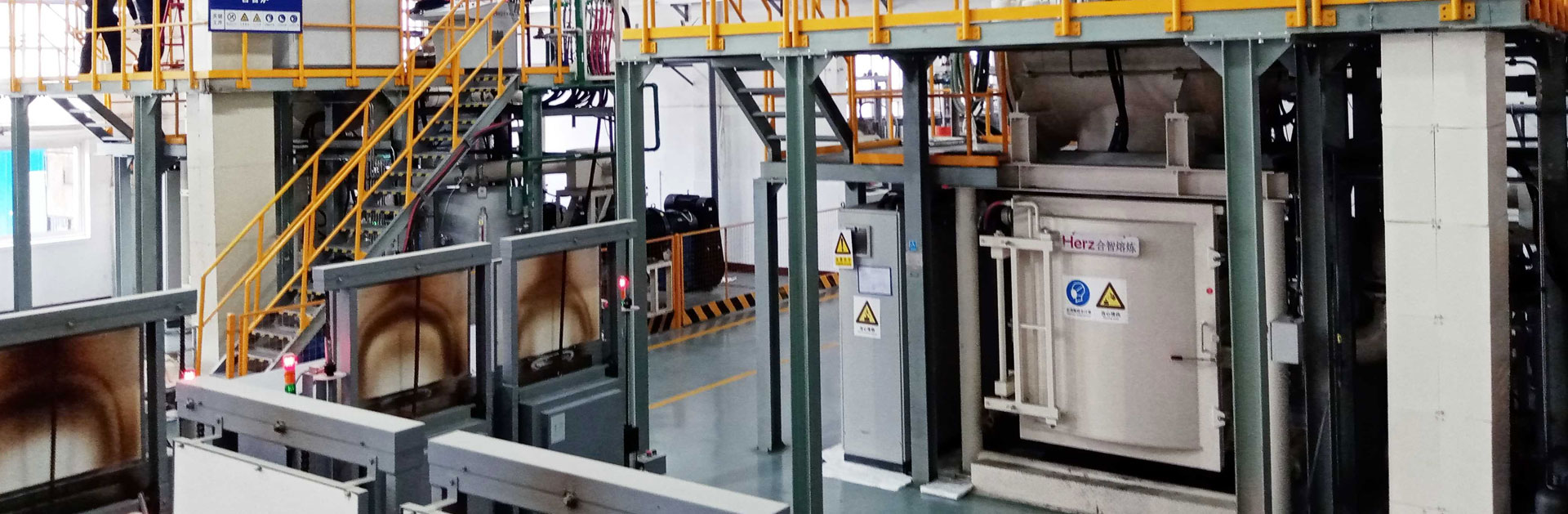