Permanent Mold Casting
What is Permanent Mold Casting
Permanent Mold Casting is a metal casting process that uses reusable molds (so-called "permanent molds", generally made of metal). Using gravity to fill the mold is the most common method, called gravity casting, but there are also processes that use air pressure or vacuum. There is also a variation of gravity casting, called the bitumen casting method, which is used to produce hollow castings. Commonly used casting metals include aluminum, magnesium and copper alloys. Other materials such as tin, zinc and lead alloys, as well as steel and iron will also be cast using graphite molds.
Permanent Mold Casting is also called Metal Type Casting. It is a casting method in which liquid metal is poured into metal molds to obtain castings. The mold is made of metal and can be used repeatedly (hundreds to thousands of times). The castings that can be produced by metal mold casting have certain restrictions in terms of weight and shape. For example, ferrous metals can only be castings with simple shapes; the weight of the castings cannot be too large; the wall thickness is also limited, and the wall thickness of the smaller castings Unable to cast
In various applications that require mass production or replication projects, a permanent mold casting process is required. In this process, the mold is preheated. This step removes the moisture that may exist in the mold, and prevents the molten metal from cooling too quickly. The preheating of the permanent mold can also prevent damage to the mold due to thermal expansion when the molten metal is introduced into the mold. The most common method is to use gravity to simply pour liquid metal into a heated mold. This method is the lowest cost method of permanent mold casting because it requires less equipment, but it is not suitable for situations where liquid metal may not reach all areas of the mold. In the case of permanent molds with details that must be filled with molten metal, A vacuum or pressure may be required to assist the introduction of metal. In the case of pressure-assisted permanent molds, low pressure is used to force molten metal into the mold for casting. For vacuum-assisted permanent mold casting, air is drawn from the mold to form a low-pressure vacuum, drawing the metal into the mold. In both cases, pressurization will make the molten metal fill small spaces and small details, otherwise it may ruin the casting. Another change in the metal mold casting process is the mud casting method. In this method, molten metal is poured into a mold and hardens around the outer edge of the shell. Once the cast metal starts to harden, the liquid metal in the center will be poured out, leaving a hollow casting suitable for decoration and decorative products.
Minghe is an experienced Permanent Mold Casting services supplier, manufacturer, exporter in China, has been specialized in offering best OEM Permanent Mold Casting services for superior quality low cost metal parts or components with the operation of an impressive range of state-of-the-art casting machines, such as gears, splines, rims, gearboxes, pipe fittings, fuel injection system housings, and vehicle engine pistons etc. Our advanced casting device routinely works with a wide variety of materials, ranging from copper, brass, stainless steel, carbon steel, aluminum, and titanium. We can always choose a suitable metal casting process to reach your requirements. Our custom permanent mold casting services ensure that our customers receive the highest quality casting parts. Send your inquiry or drawing fast to get an online casting quote.
The Advantages And Disadvantages Of Permanent Mold Casting
Comparison of Permanent Mold Casting and Sand Casting: There are many advantages in technology and economy.
- - Metal castings have higher mechanical properties than sand castings. For the same alloy, its tensile strength can be increased by about 25% on average, its yield strength can be increased by about 20% on average, and its corrosion resistance and hardness have also been significantly improved;
- - The precision and surface finish of castings are higher than that of sand castings, and the quality and size are stable;
- - The process yield of castings is high, and the consumption of liquid metal is reduced, generally saving 15-30%;
- - No sand or less sand is used, generally 80-100% of modeling materials can be saved;
In addition, Permanent Mold Casting has high production efficiency; reduces the causes of casting defects; the process is simple, and it is easy to realize mechanization and automation. Although Permanent Mold Casting has many advantages, it also has disadvantages. Such as:
- - The cost of manufacturing metal molds is high;
- - The metal type is not air-permeable and has no retreat, which is easy to cause defects such as insufficient pouring, cracking or white mouth of the cast iron;
- - In Permanent Mold Casting, the working temperature of the mold, the pouring temperature and speed of the alloy, the time the casting stays in the mold, and the coating used are very sensitive to the quality of the casting and need to be strictly controlled.
Therefore, when deciding to adopt Permanent Mold Casting, the following factors must be considered comprehensively: the shape and weight of the casting must be appropriate; there must be sufficient batches; the deadline for completing the production task is permitted.
The Molding Characteristics Of Permanent Mold Casting
Metal molds and sand molds have significant differences in performance. For example, sand molds have air permeability, while metal molds do not; sand molds have poor thermal conductivity, metal molds have good thermal conductivity, sand molds have retreat, but metal molds do not. These characteristics of the metal mold determine that it has its own rules in the forming process of the casting.
The influence of the change of the gas state in the cavity on the molding of the casting: When the metal is filled, the gas in the cavity must be quickly discharged, but the metal has no gas permeability. As long as the process is neglected, the quality of the casting will be adversely affected. .
The characteristics of the heat exchange during the solidification of the casting: once the molten metal enters the cavity, it transfers heat to the metal wall. Liquid metal loses heat through the mold wall, solidifies and shrinks, while the mold wall gains heat, increases the temperature and expands at the same time. As a result, a "gap" is formed between the casting and the mold wall. Before the "casting-gap-metal mold" system reaches the same temperature, the casting can be regarded as cooling in the "gap", while the metal mold wall is heated through the "gap".
Metal mold hinders the impact of shrinkage on castings: metal molds or metal cores have no retreat during the solidification process of the castings and hinder the shrinkage of the castings. This is another feature of it
Different Types Production Scenario Of Permanent Mold Casting
Minghe always adheres to the customer's requirements and the company's service standards. In any link of mold design, mold assembly, mold debugging, mold trial production, casting process, etc., there are dedicated engineers to keep you on the phone;
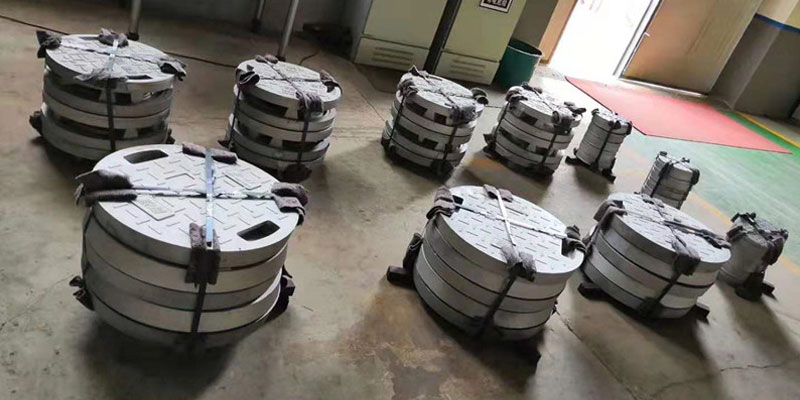
Permanent Mold Casting Process (1)▶ |
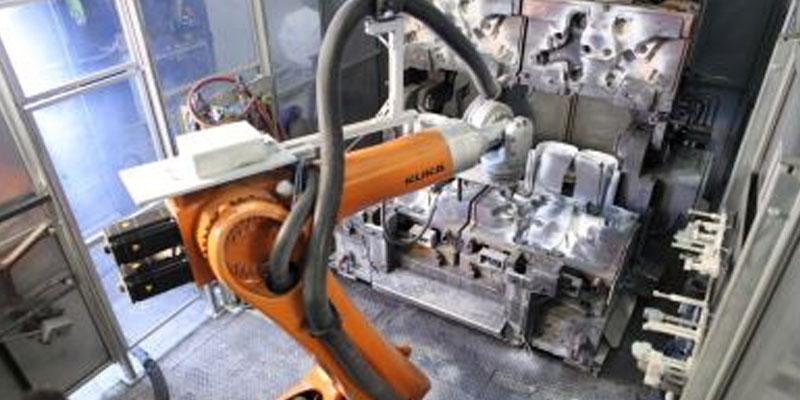
Permanent Mold Casting Process (2)▶ |
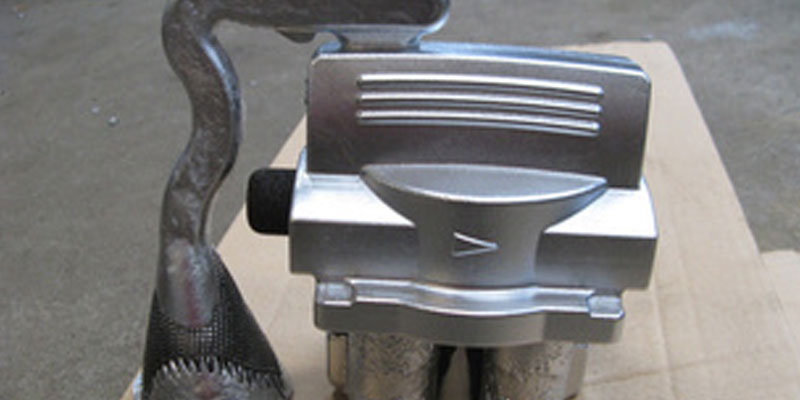
Permanent Mold Casting Process (3)▶ |
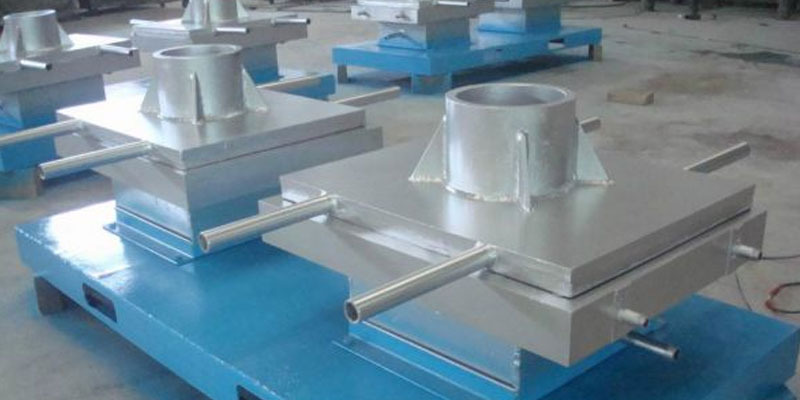
Permanent Mold Casting Process (4)▶ |
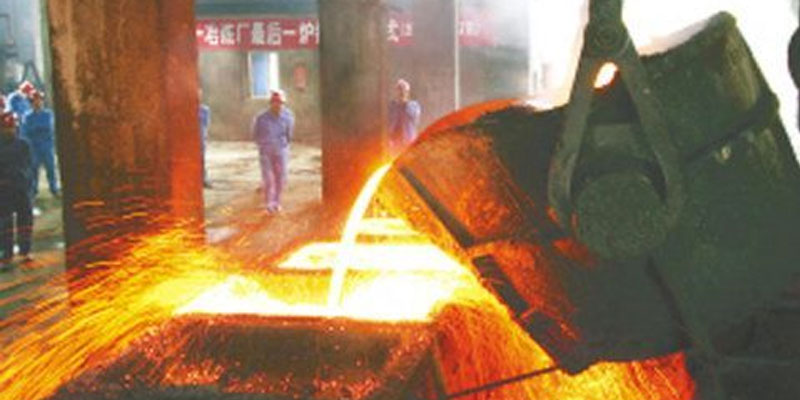
Permanent Mold Casting Process (5)▶ |
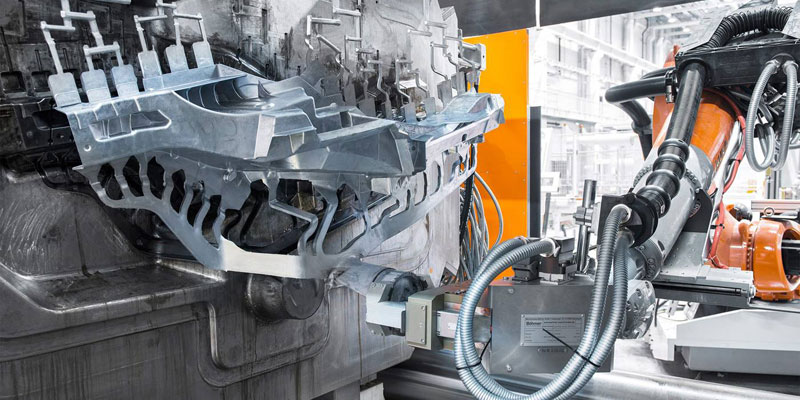
Permanent Mold Casting Process (6)▶ |
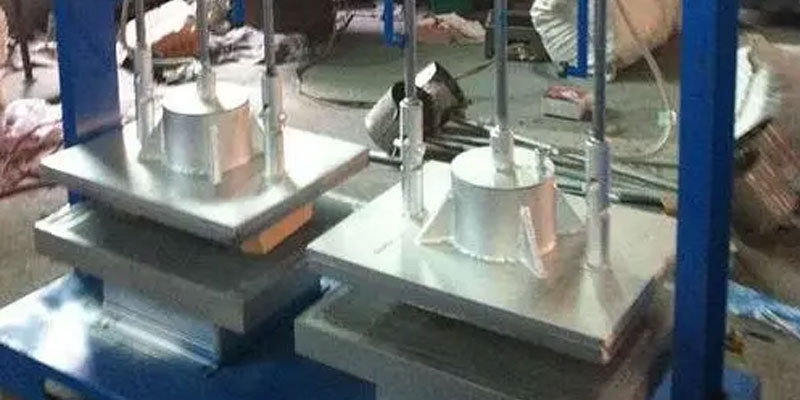
Permanent Mold Casting Process (7) ▶ |
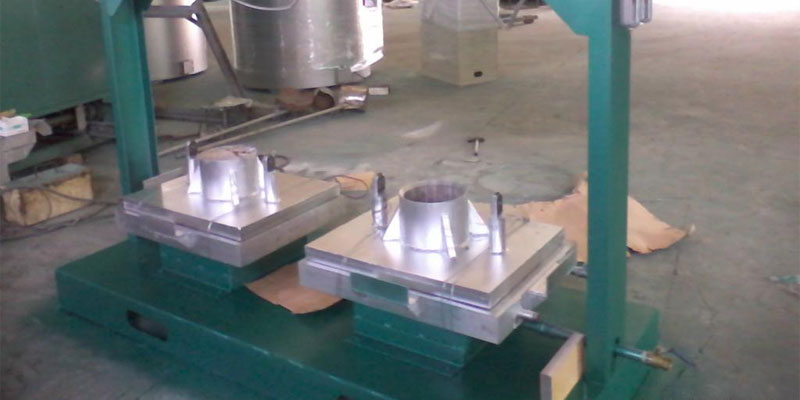
Permanent Mold Casting Process (8)▶ |
The Minghe Case Studies Of Permanent Mold Casting
Minghe Casting fabrication services are available for both design to reality and low to high volume production runs of your die casting parts,sand casting parts,investment casting parts,metal casting parts, lost foam casting parts and more.
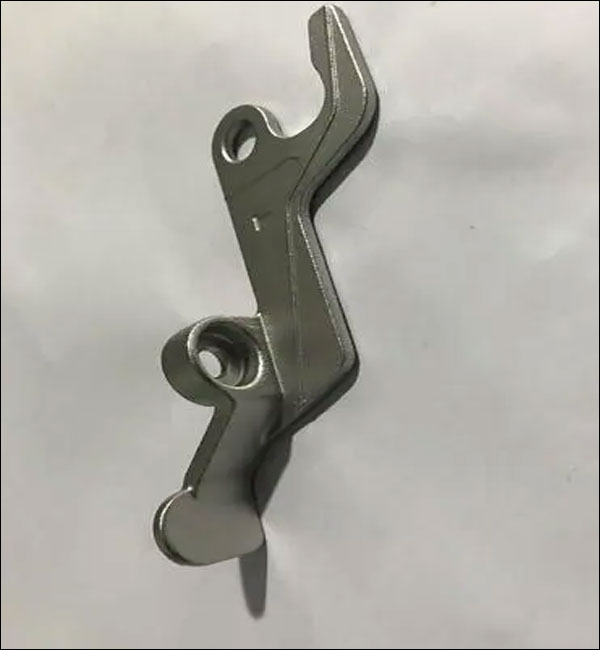
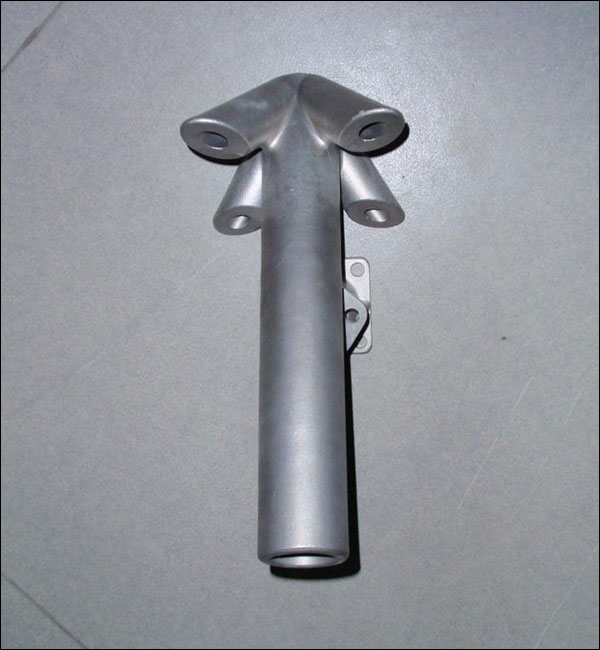
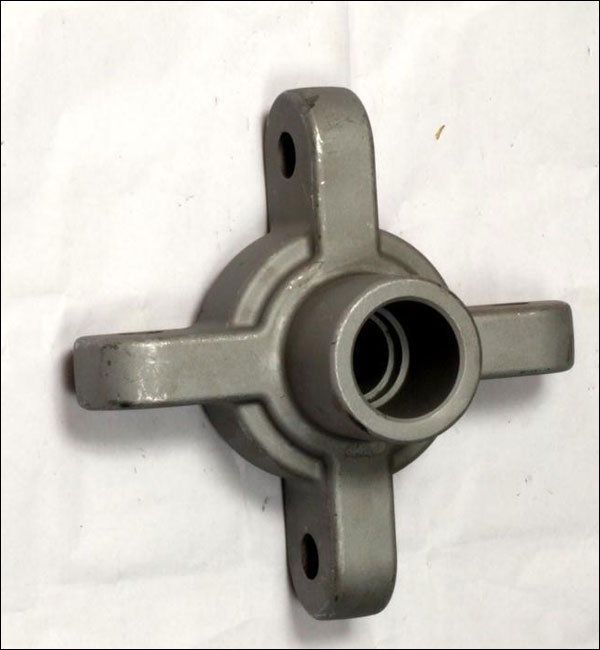
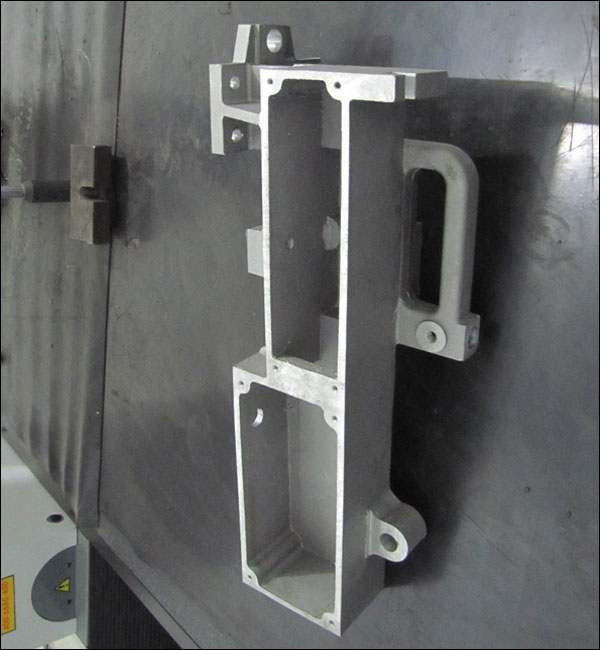
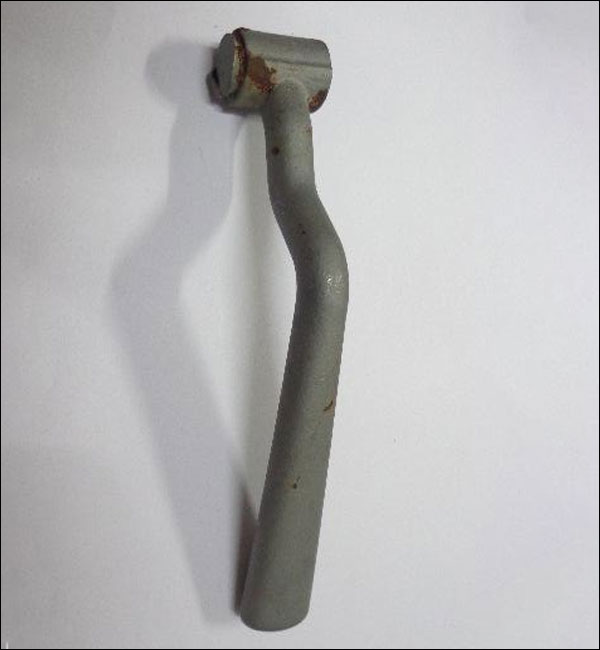
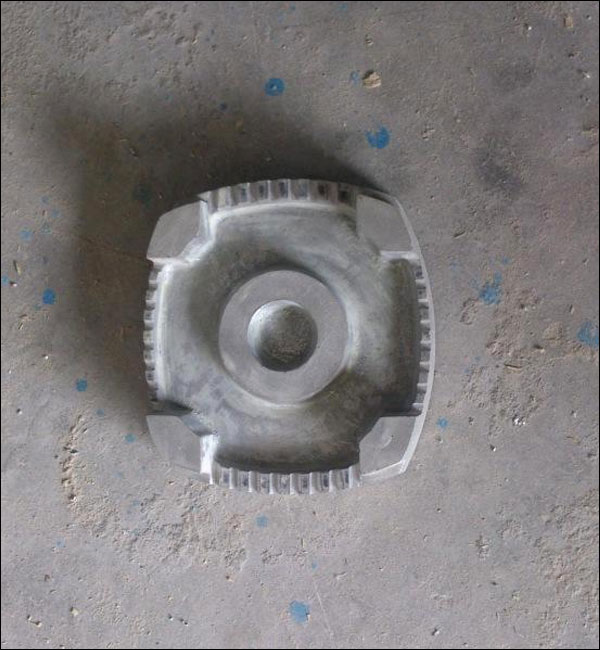
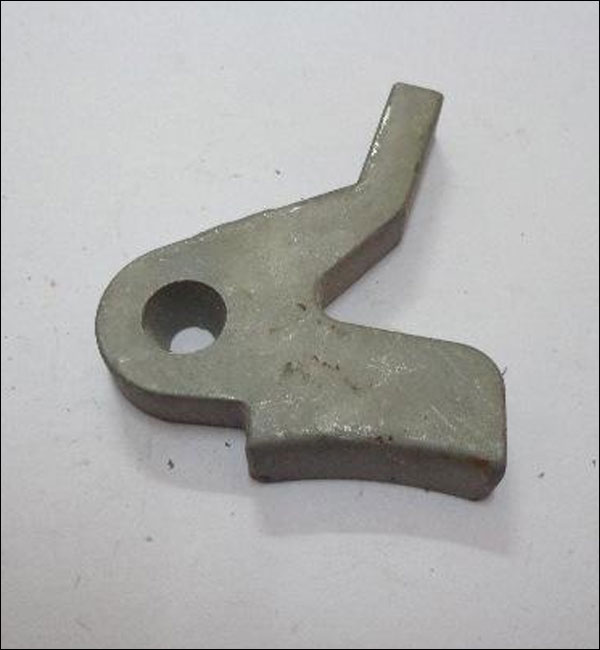
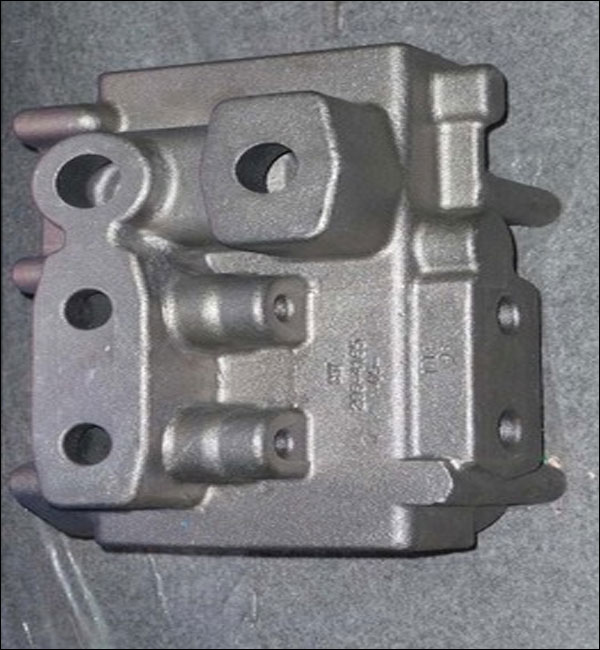
Go To View More Casting Parts Cases Studies >>>
Choose the Best Permanent Mold Casting Supplier
Currently, our permanent mold casting parts are exported to America, Canada, Australia, United Kingdom, Germany, France, Sout Africa, and many other countries all over the world. We are ISO9001-2015 registered and also certified by SGS.
Our custom permanent mold casting fabrication service provides durable and affordable castings that meet your specifications for automotive, medical, aerospace, electronics, food, construction, security, marine, and more industries. Fast to send your inquiry or submit your drawings to get a free quote in the shortest time.Contact us or Email sales@hmminghe.com to see how our people, equipment and tooling can bring the best quality for the best price for your permanent mold casting project.
We Provide Casting Services Include:
Minghe Casting services working with sand casting、metal casting 、investment casting lost foam casting, and more.
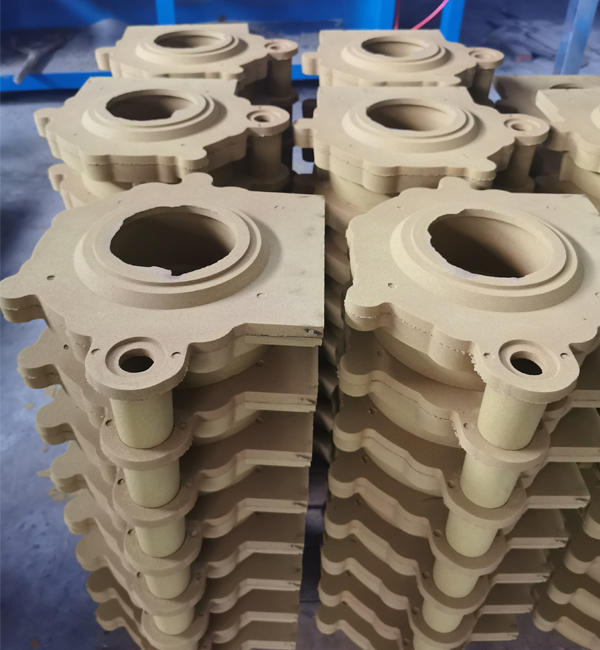
Sand Casting
Sand Casting is a traditional casting process that uses sand as the main modeling material to make molds. Gravity casting is generally used for sand molds, and low-pressure casting, centrifugal casting and other processes can also be used when there are special requirements. Sand casting has a wide range of adaptability, small pieces, large pieces, simple pieces, complex pieces, single pieces, and large quantities can be used.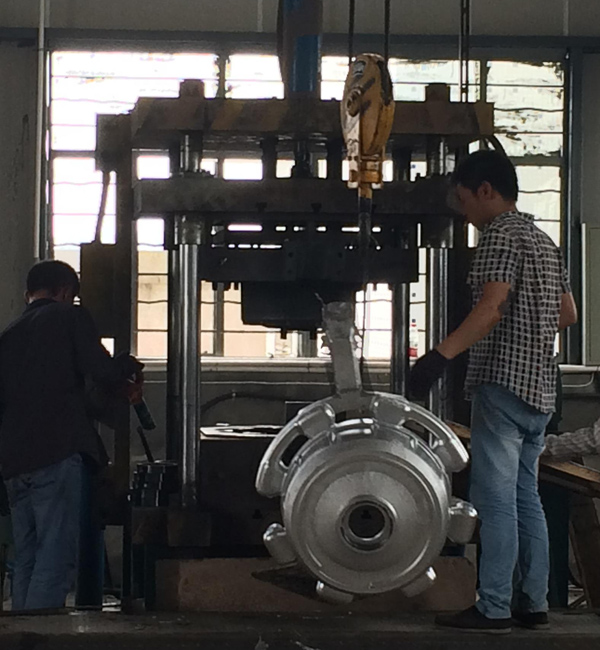
Permanent Mold Casting
Permanent Mold Casting have a long life and high production efficiency, not only have good dimensional accuracy and smooth surface, but also have higher strength than sand castings and are less likely to be damaged when the same molten metal is poured. Therefore, in the mass production of medium and small non-ferrous metal castings, as long as the melting point of the casting material is not too high, metal casting is generally preferred.
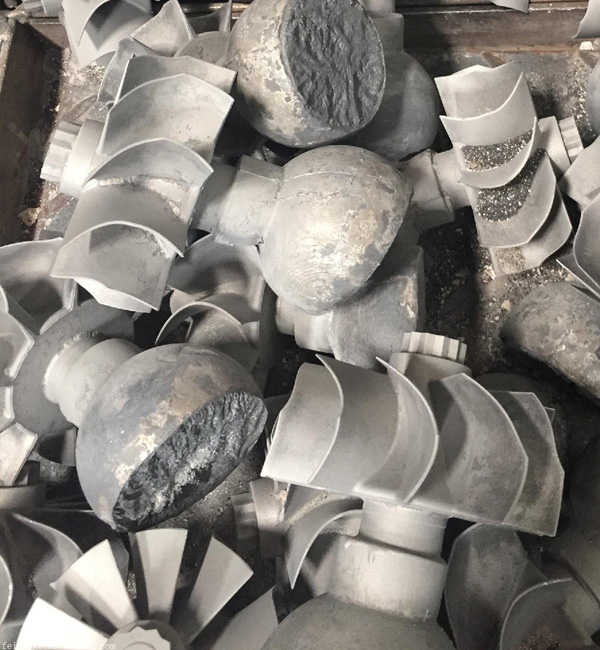
Investment Casting
The biggest advantage of investment casting is that because investment castings have high dimensional accuracy and surface finish, they can reduce machining work, but leave a little machining allowance on the parts with higher requirements. It can be seen that the use of investment casting method can save a lot of machine tool equipment and processing man-hours, and greatly save metal raw materials.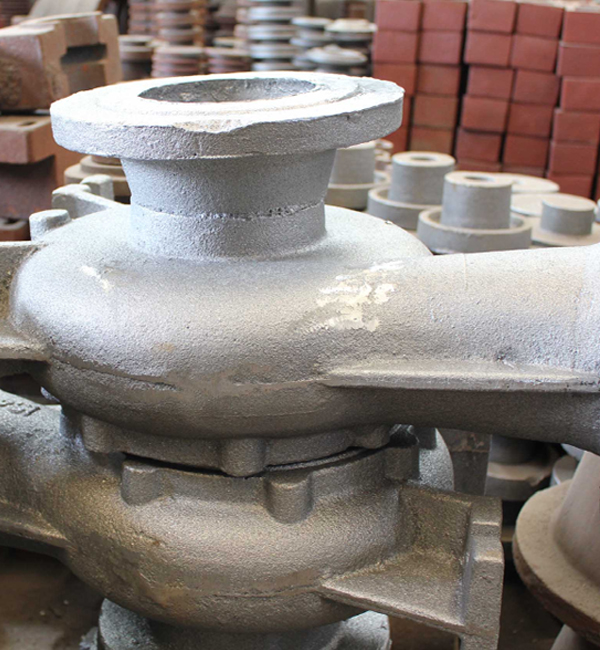
Lost Foam Casting
Lost foam casting is to combine paraffin wax or foam models similar to the casting size and shape into model clusters. After brushing and drying refractory coatings, they are buried in dry quartz sand for vibration modeling, and poured under negative pressure to gasify the model. , The liquid metal occupies the position of the model and forms a new casting method after solidification and cooling.
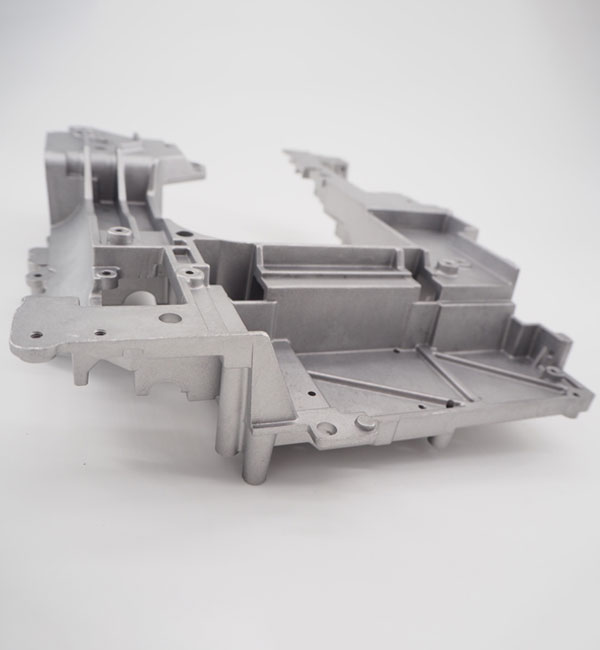
Die Casting
Die casting is a metal casting process, which is characterized by applying high pressure to the molten metal using the cavity of the mold. Molds are usually made of higher-strength alloys, and this process is somewhat similar to injection molding. Most die castings are iron-free, such as zinc, copper, aluminum, magnesium, lead, tin, and lead-tin alloys and their alloys. Minghe has been China's top die casting service since 1995.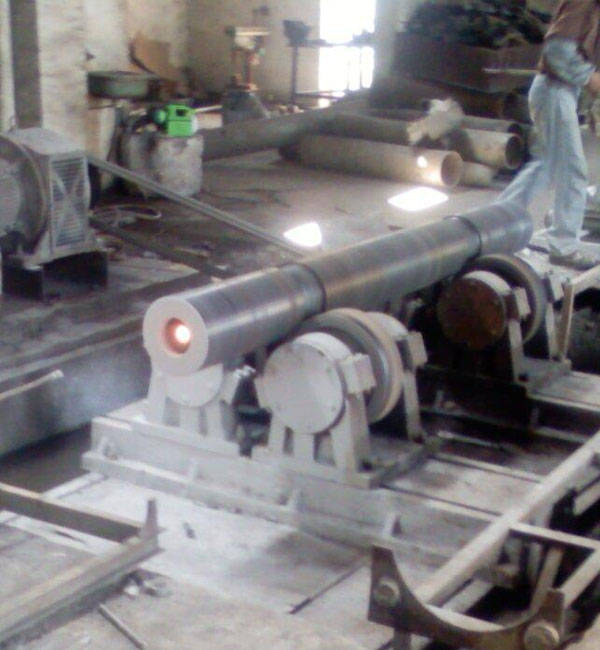
Centrifugal Casting
Centrifugal Casting is a technique and method of injecting liquid metal into a high-speed rotating mold, so that the liquid metal is centrifugal motion to fill the mold and form a casting. Due to the centrifugal movement, the liquid metal can fill the mold well in the radial direction and form the free surface of the casting; it affects the crystallization process of the metal, thereby improving the mechanical and physical properties of the casting.
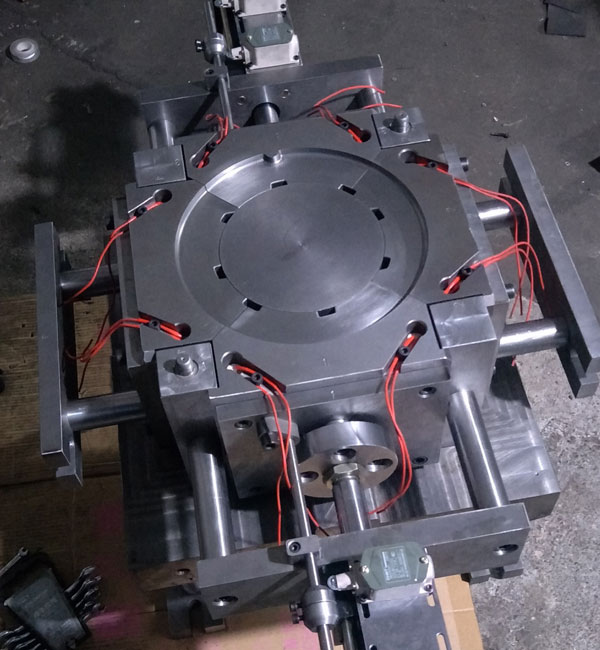
Low Pressure Casting
Low Pressure Casting means that the mold is generally placed above a sealed crucible, and compressed air is introduced into the crucible to cause a low pressure (0.06~0.15MPa) on the surface of the molten metal, so that the molten metal rises from the riser pipe to fill the mold and control Solidified casting method. This casting method has good feeding and dense structure, easy to cast large thin-walled complex castings, no risers, and a metal recovery rate of 95%. No pollution, easy to realize automation.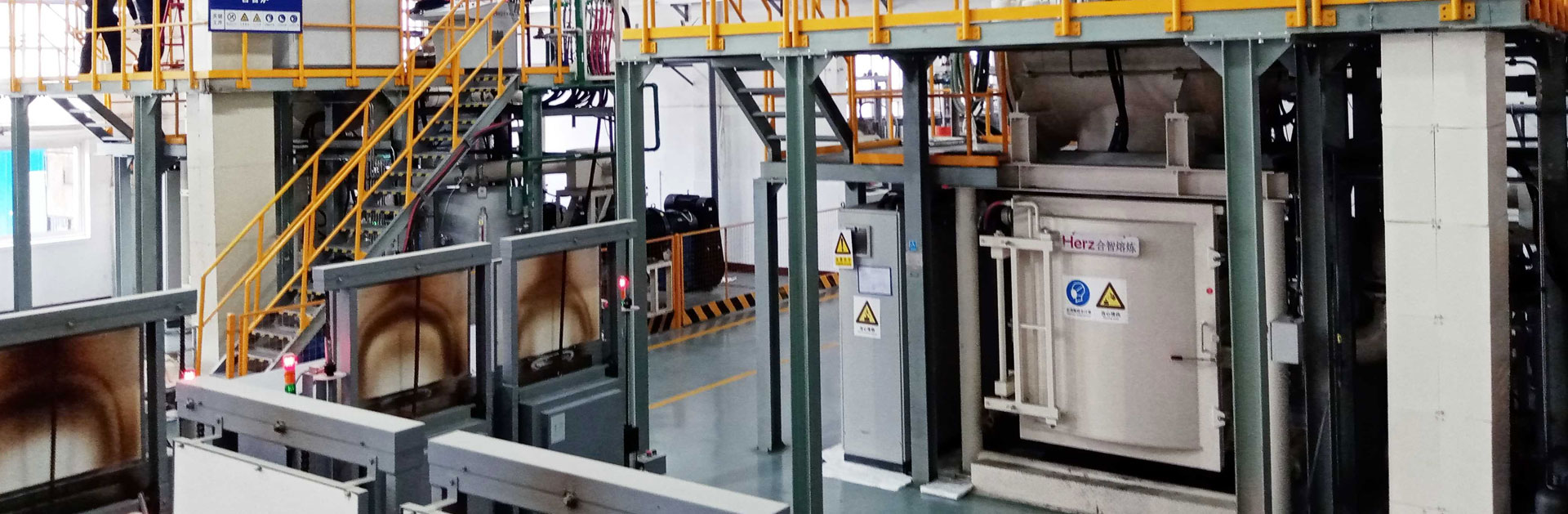
Vacuum Casting
Vacuum Casting is a casting process in which metal is smelted, poured and crystallized in a vacuum chamber. Vacuum casting can minimize the gas content in the metal and prevent metal oxidation. This method can produce very demanding special alloy steel castings and extremely easily oxidized titanium alloy castings. Minghe Casting has a vacuum casting sub-factory, which is enough to solve all the problems related to vacuum casting