Investment Casting
What Is Investment Casting
Investment casting, also known as lost wax casting, includes processes such as pressing wax, repairing wax, assembling trees, dipping slurry, melting wax, casting molten metal, and post-treatment. Lost wax casting is to use wax to make a wax mold of the part to be cast, and then coat the wax mold with mud, which is a mud mold. After the clay mold is dried, put it in hot water to melt the internal wax mold. Take out the clay mold from the melted wax mold and fire it into a pottery mold. Once roasted. Generally, a pouring port is left when making a mud mold, and then molten metal is poured from the pouring port. After cooling, the required parts are made.
When using wax as a pattern, investment casting is also called "lost wax casting". The material is made into a pattern, and the surface of the pattern is covered with several layers of refractory material to make a mold shell, and then the pattern is melted and discharged from the mold shell to obtain a mold without parting surface. After high temperature roasting, it can be filled with sand and poured. Because patterns are widely made of waxy materials, investment casting is often referred to as "lost wax casting".
Materials Used in Lost Wax Casting – Types of Investment Castings
- Carbon Steel
- Alloy Steel
- Heat Resistant Alloy
- Stainless Steel
- Precision Alloy
- Permanent Magnet Alloy
- Bearing Alloy
- Copper Alloy
- Aluminum Alloy
- Titanium Alloy
- Nodular Cast Iron, etc.
The shape of investment castings is generally more complicated. The minimum diameter of the holes that can be cast on the castings can reach 0.5mm, and the minimum wall thickness of the castings is 0.3mm. In production, some parts that were originally composed of several parts can be combined. By changing the structure of the parts, they can be designed as integral parts and directly cast by investment casting to save processing man-hours and metal material consumption, and make the part structure more As reasonable.
The weight of investment castings is mostly zero to dozens of cattle (from a few grams to ten kilograms, generally not more than 25 kg), and it is more troublesome to produce too heavy castings by investment casting.
The investment casting process is more complicated and difficult to control, and the materials used and consumed are more expensive. Therefore, it is suitable for the production of small parts with complex shapes, high precision requirements, or other processing difficulties, such as turbine engine blades.
Minghe Casting Is ISO9001:2015 certified china advance manufacturer of standard and complex precision wax investment casting prototypes. Wax and resin models or patterns can be completed in only a few hours from CAD or math data files. Metal cast prototypes can be made in as little as 2 to 4 weeks and complete cast and machined parts can be developed in as little as 3-5 weeks. Industries served include aerospace, automotive, defense, marine, medical, nuclear, oil and gas, and tool and die.
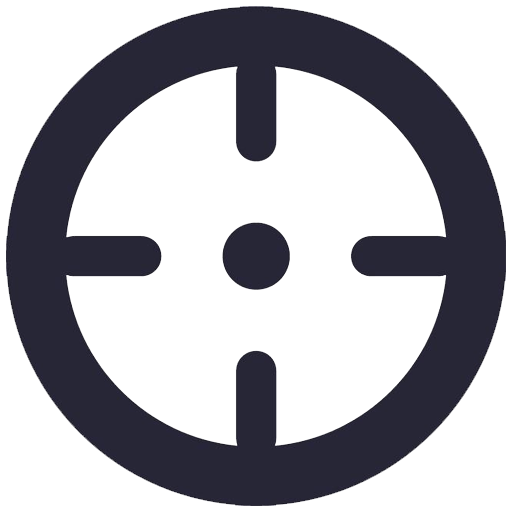
Benefits of Investment Casting Process
The functions of investment casting can be summarized as follows:
- – Can produce large parts
- – Can form complex shapes
- – High strength parts
- – High production rate
- – The dimensional accuracy of investment castings is relatively high, generally up to CT4-6 (sand casting is CT10~13, die casting is CT5~7)
- – Water glass casting, low temperture lost-wax casting process, with capacity to cast products range from 0.5kg to 100kgs. The usually used materials are carbon steel, alloy steel, and stainless steel, wear resistant material, etc.
- – The surface finish of investment castings is higher than that of general castings, generally up to Ra.1.6~3.2μm.
- – The use of investment casting method can greatly save machine tool equipment and processing man-hours, and greatly save metal raw materials.
- – Investment casting can cast complex castings of various alloys, especially high-temperature alloy castings. For example, the blade of a jet engine, its streamlined profile and cooling cavity, can hardly be formed by machining technology. Production by investment casting process can not only achieve mass production, ensure the consistency of castings, but also avoid the stress concentration of residual knife marks after machining.
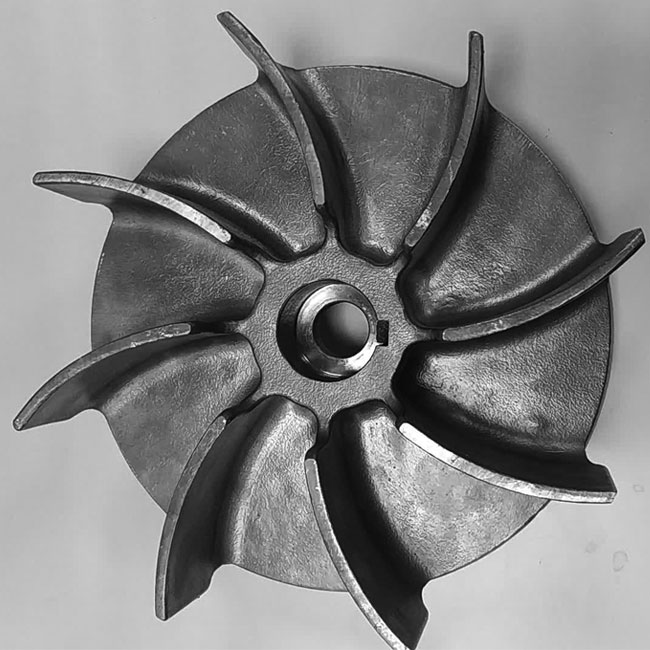
Minghe Hardware Production Process Of Investment Casting
Investment casting (lost wax casting) is the process of using wax to make the mold of the parts to be cast, and then the wax mold is coated with mud, which is called clay mold. After the clay mould is dried, heat and melt the inner wax mould. Take out the clay mold after melting the wax mold and bake it into a ceramic mold. Generally, the gate system is left when making the mud mold, then the molten metal can be poured into the mold. Cool it until the part solidifies, the required parts are made.Minghe Steps of Investment Casting Process:
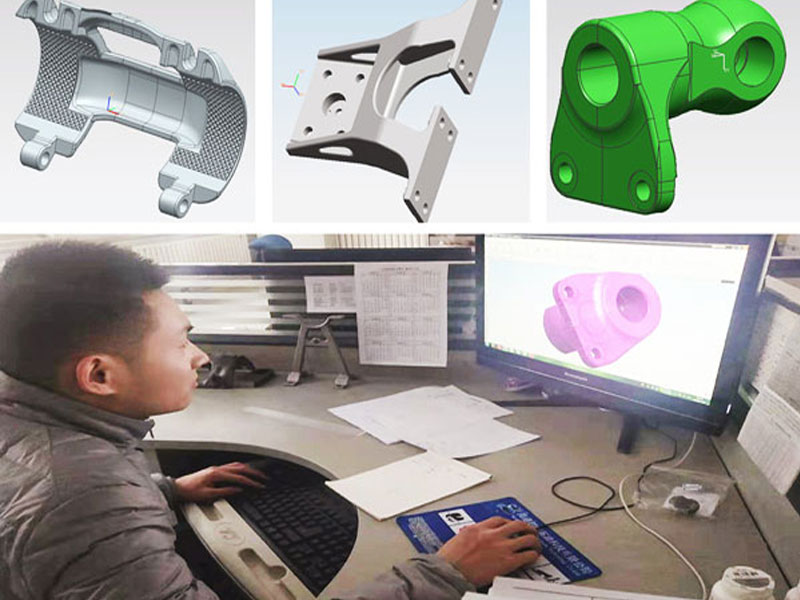
Mold Development And Design ▶ |
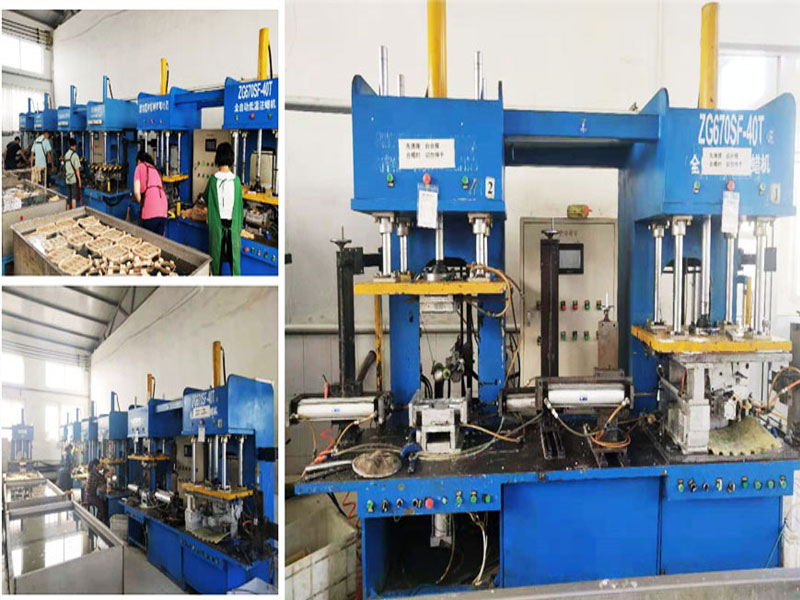
Lost Wax Workshop ▶ |
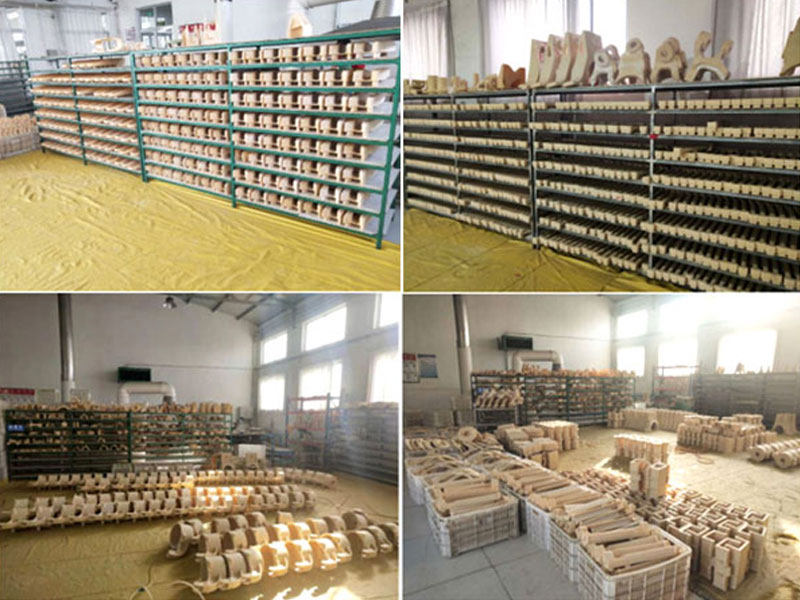
Lost Wax Inspection ▶ |
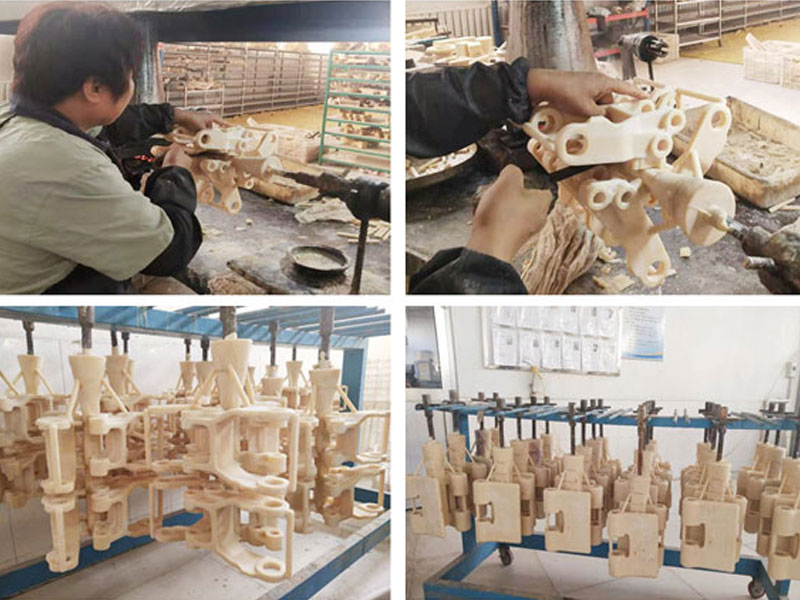
Wax Group Tree▶ |
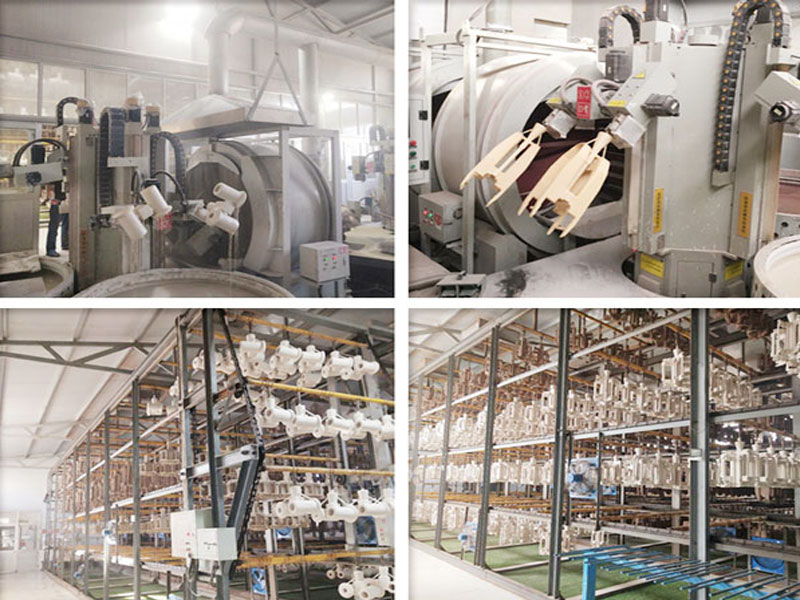
Silica Sol Shell ▶ |
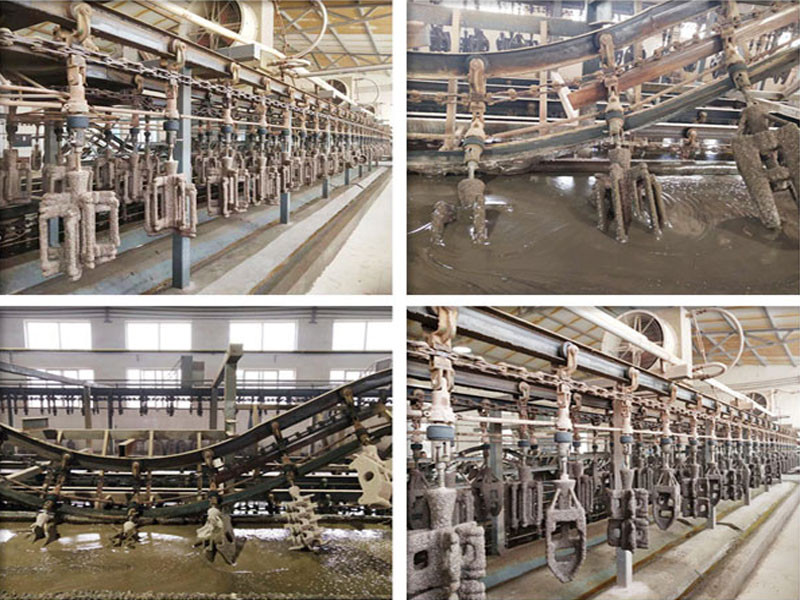
Water Glass Reinforcement▶ |
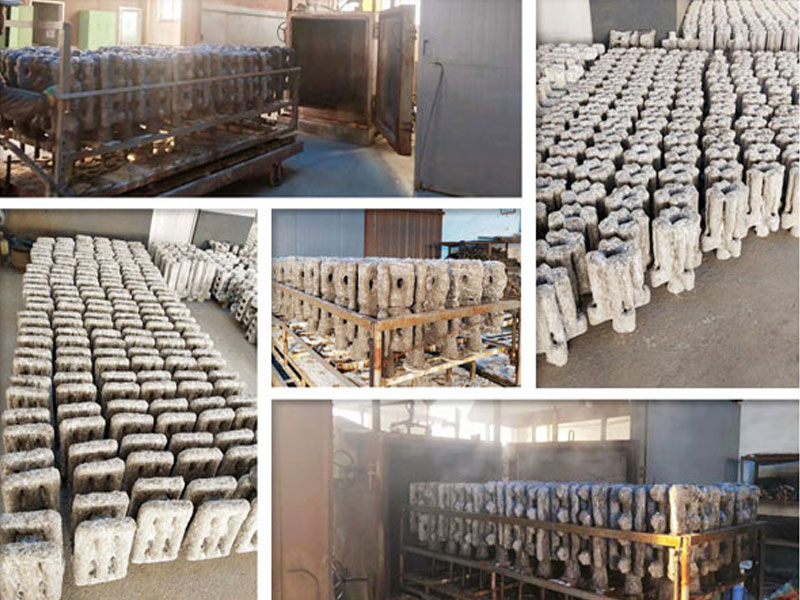
Steam Dewaxing ▶ |
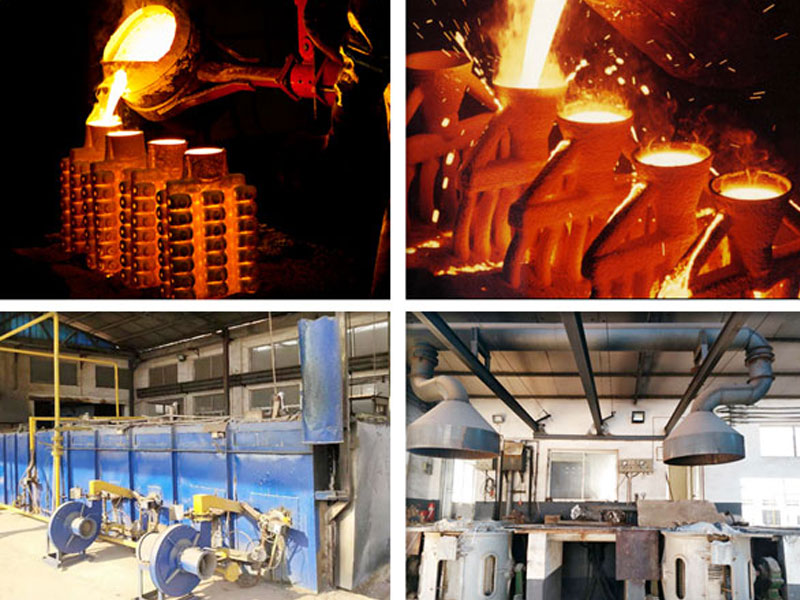
Roasting-Pouring▶ |
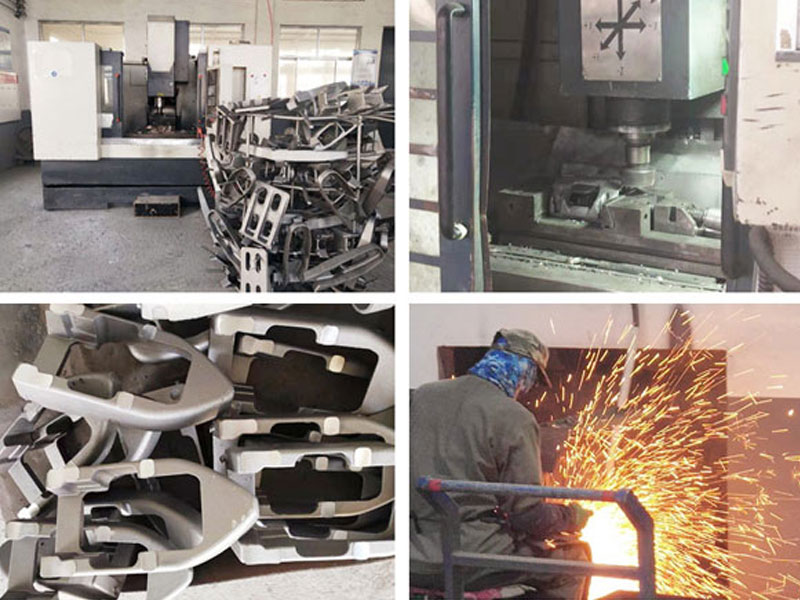
Remove Gate Sanding ▶ |
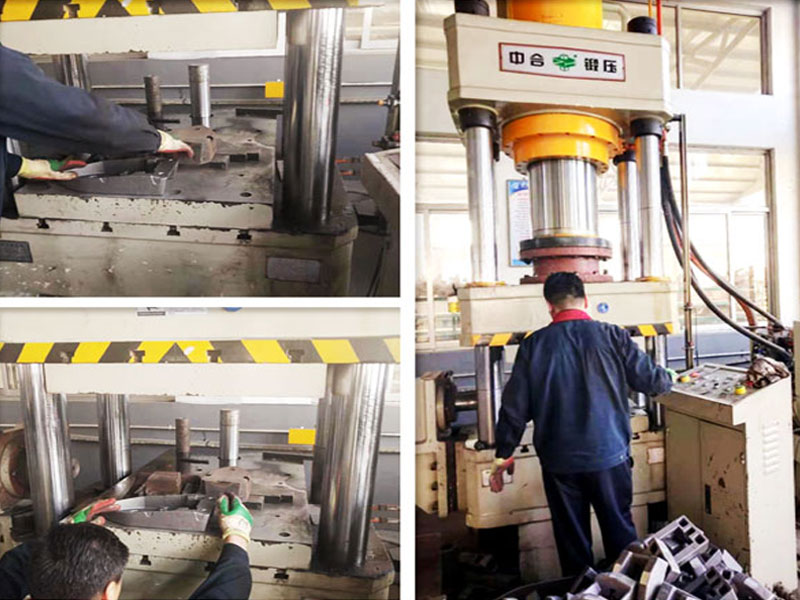
Blank Positive▶ |
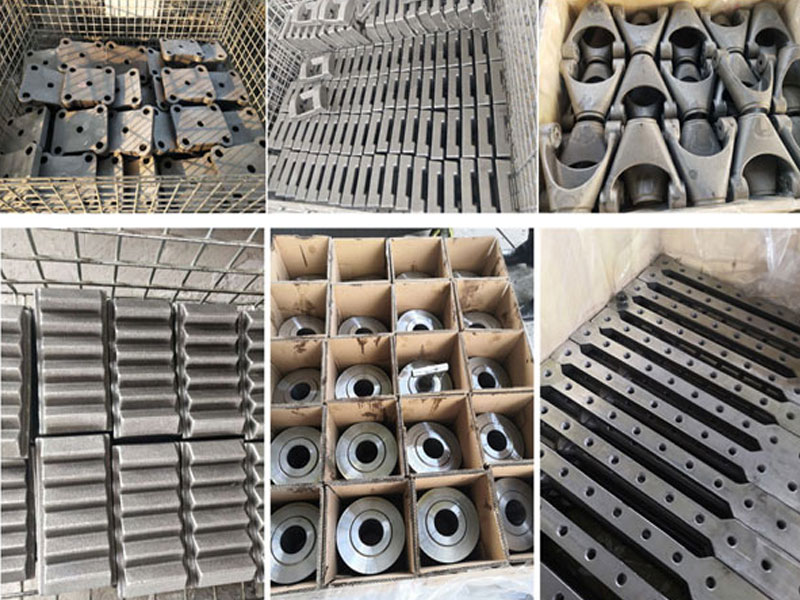
Complete Precision Castings▶ |
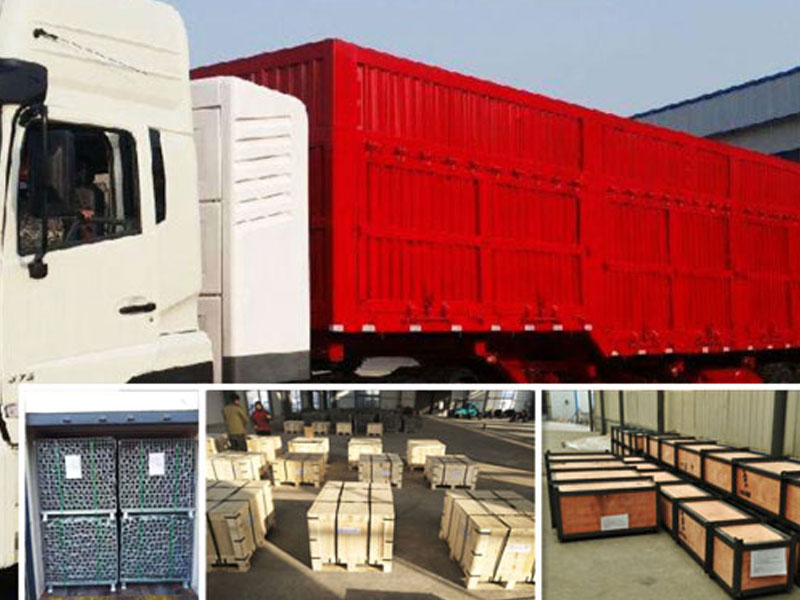
Pack And Ship▶ |
The Minghe Case Studies Of Investment Casting
Minghe Casting fabrication services are available for both design to reality and low to high volume production runs of your die casting parts,sand casting parts,investment casting parts,metal casting parts, lost foam casting parts and more.
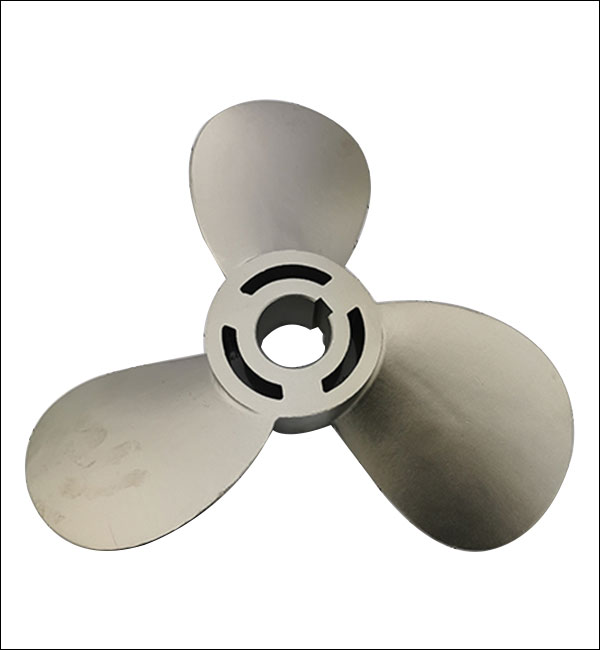
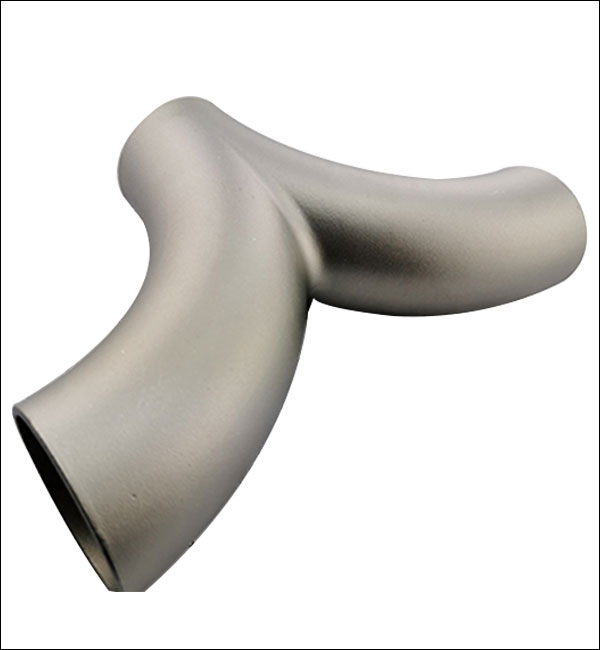
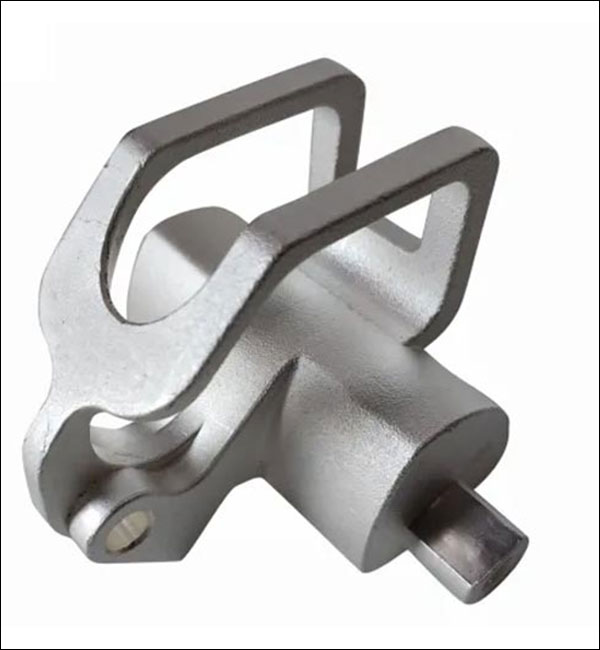
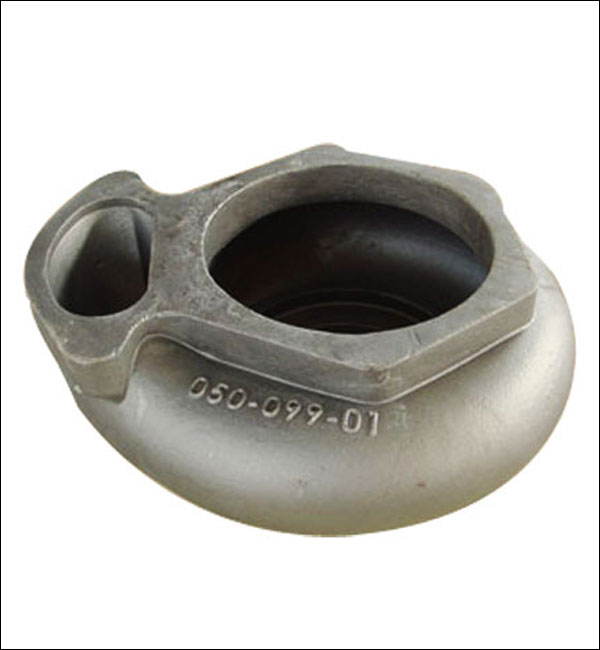
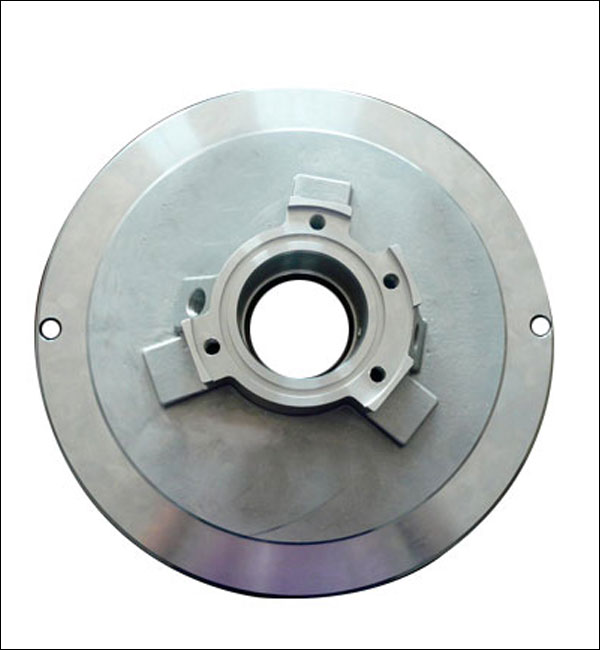
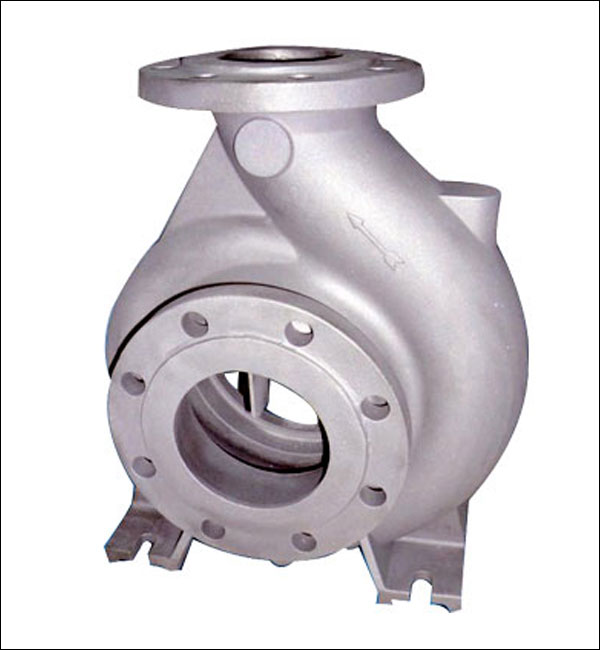
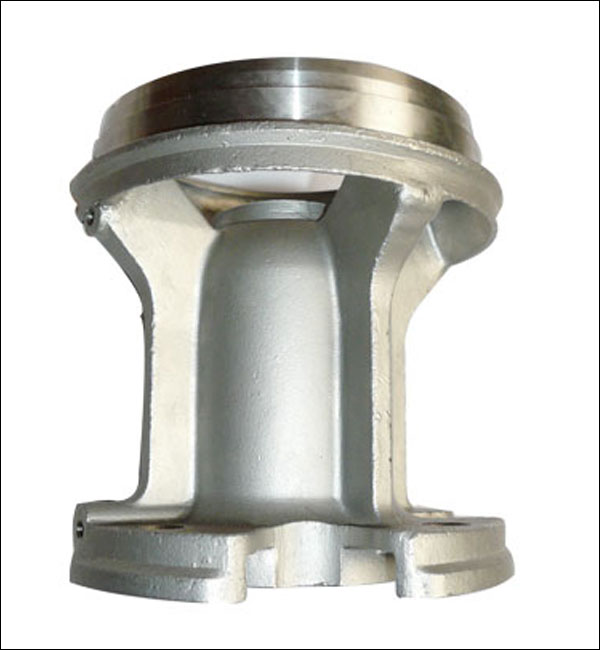
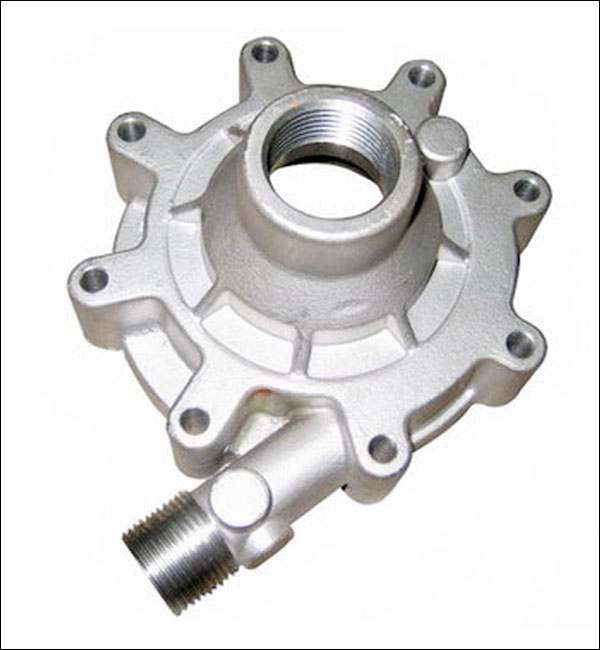
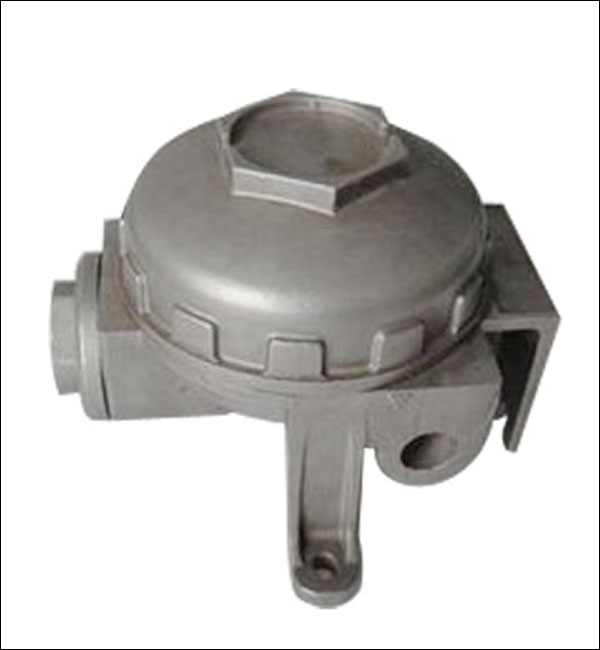
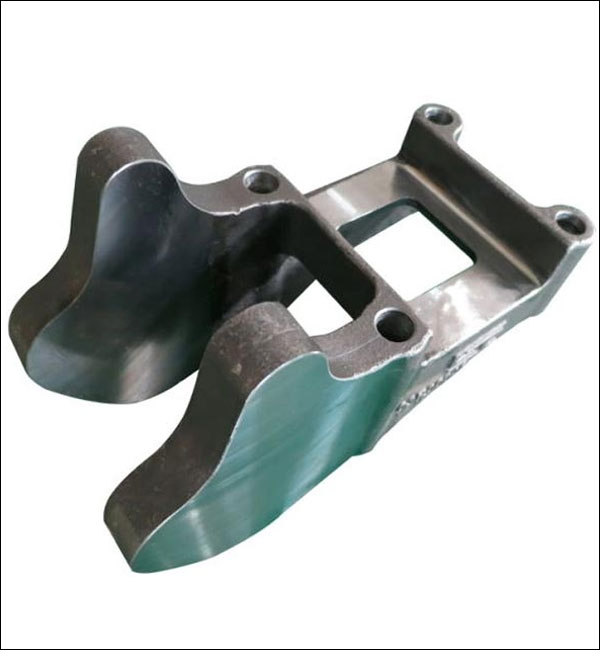
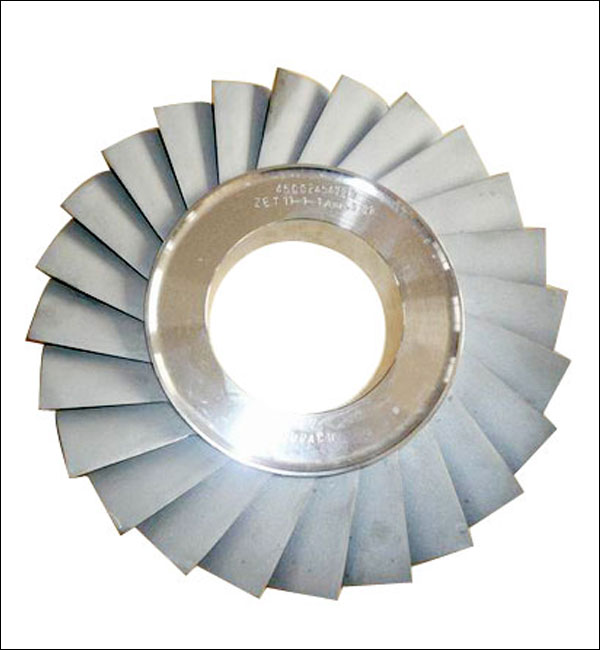
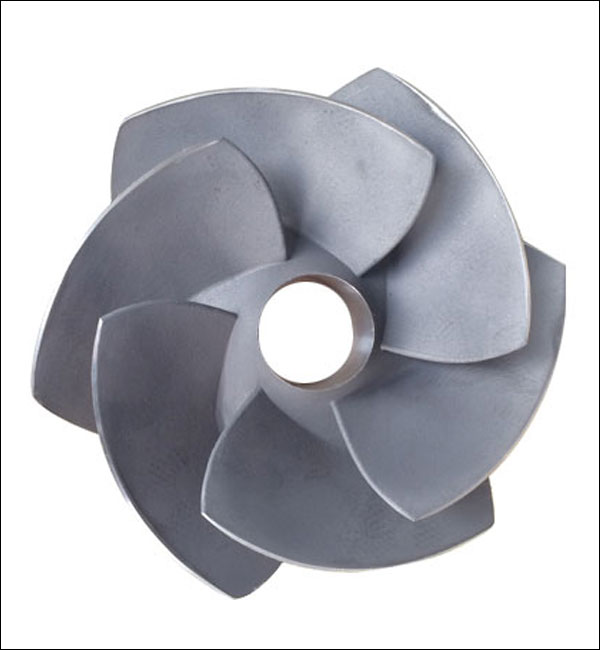
Go To View More Casting Parts Cases Studies >>>
Choose the Best Investment Casting Supplier
Currently, our investment casting parts are exported to America, Canada, Australia, United Kingdom, Germany, France, Sout Africa, and many other countries all over the world. We are ISO9001-2015 registered and also certified by SGS.
Our custom investment casting fabrication service provides durable and affordable castings that meet your specifications for automotive, medical, aerospace, electronics, food, construction, security, marine, and more industries. Fast to send your inquiry or submit your drawings to get a free quote in the shortest time.Contact us or Email sales@hmminghe.com to see how our people, equipment and tooling can bring the best quality for the best price for your investment casting project.
We Provide Casting Services Include:
Minghe Casting services working with sand casting、metal casting 、investment casting lost foam casting, and more.
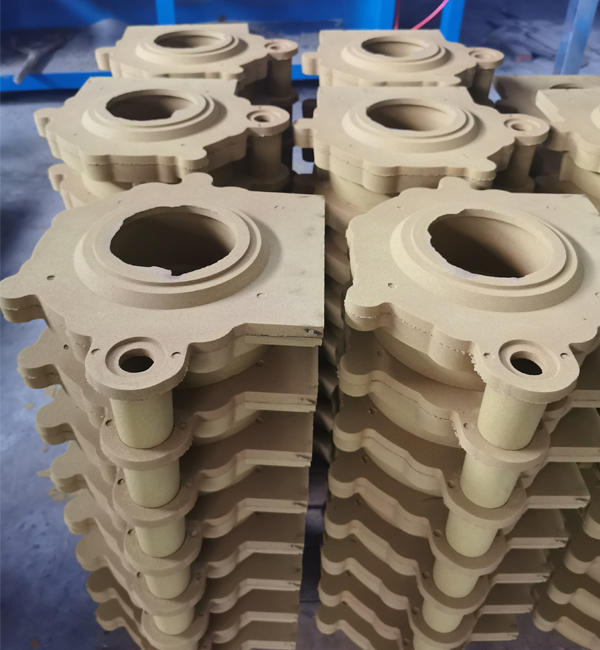
Sand Casting
Sand Casting is a traditional casting process that uses sand as the main modeling material to make molds. Gravity casting is generally used for sand molds, and low-pressure casting, centrifugal casting and other processes can also be used when there are special requirements. Sand casting has a wide range of adaptability, small pieces, large pieces, simple pieces, complex pieces, single pieces, and large quantities can be used.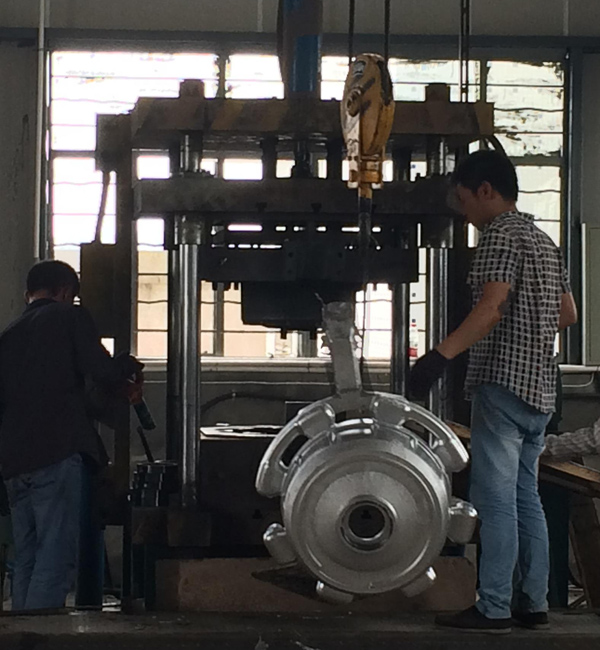
Permanent Mold Casting
Permanent Mold Casting have a long life and high production efficiency, not only have good dimensional accuracy and smooth surface, but also have higher strength than sand castings and are less likely to be damaged when the same molten metal is poured. Therefore, in the mass production of medium and small non-ferrous metal castings, as long as the melting point of the casting material is not too high, metal casting is generally preferred.
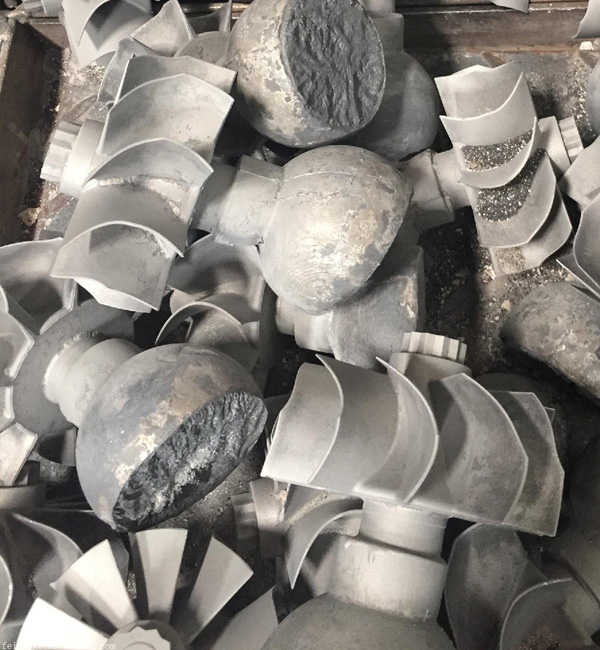
Investment Casting
The biggest advantage of investment casting is that because investment castings have high dimensional accuracy and surface finish, they can reduce machining work, but leave a little machining allowance on the parts with higher requirements. It can be seen that the use of investment casting method can save a lot of machine tool equipment and processing man-hours, and greatly save metal raw materials.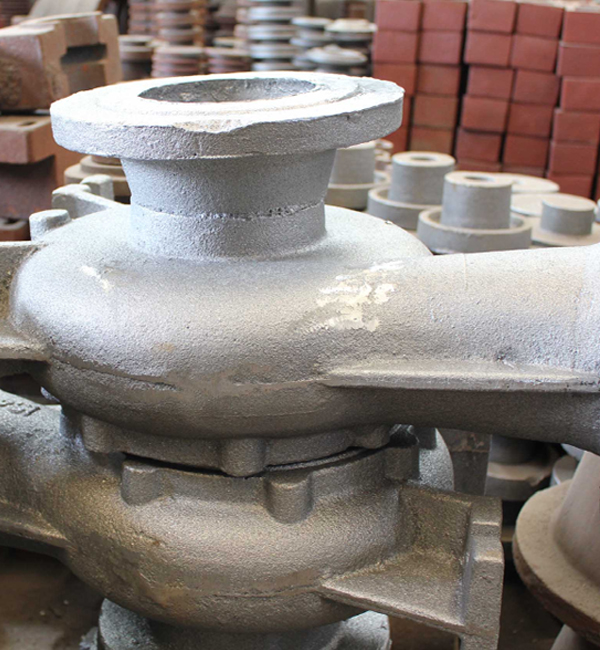
Lost Foam Casting
Lost foam casting is to combine paraffin wax or foam models similar to the casting size and shape into model clusters. After brushing and drying refractory coatings, they are buried in dry quartz sand for vibration modeling, and poured under negative pressure to gasify the model. , The liquid metal occupies the position of the model and forms a new casting method after solidification and cooling.
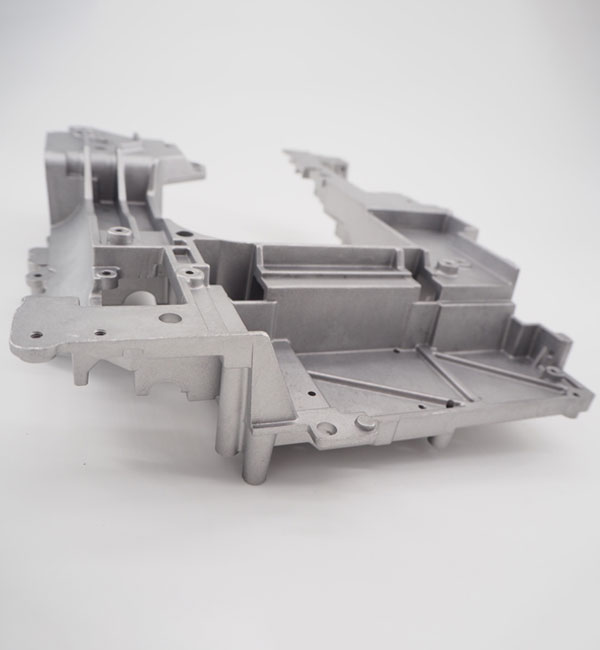
Die Casting
Die casting is a metal casting process, which is characterized by applying high pressure to the molten metal using the cavity of the mold. Molds are usually made of higher-strength alloys, and this process is somewhat similar to injection molding. Most die castings are iron-free, such as zinc, copper, aluminum, magnesium, lead, tin, and lead-tin alloys and their alloys. Minghe has been China's top die casting service since 1995.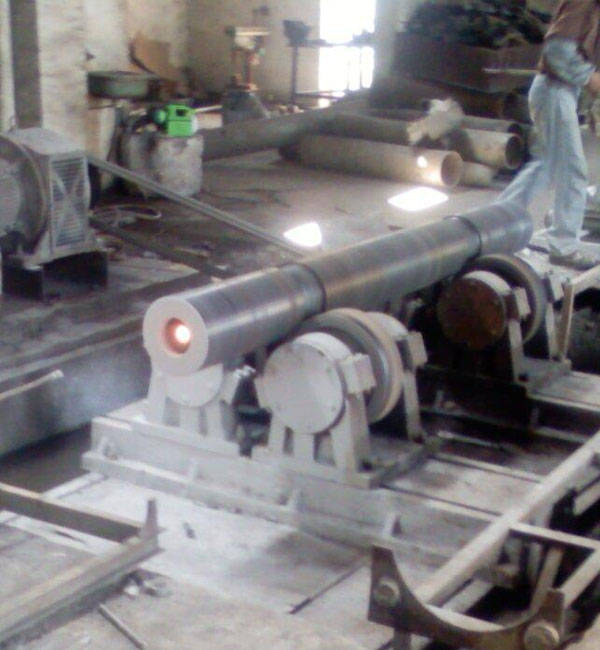
Centrifugal Casting
Centrifugal Casting is a technique and method of injecting liquid metal into a high-speed rotating mold, so that the liquid metal is centrifugal motion to fill the mold and form a casting. Due to the centrifugal movement, the liquid metal can fill the mold well in the radial direction and form the free surface of the casting; it affects the crystallization process of the metal, thereby improving the mechanical and physical properties of the casting.
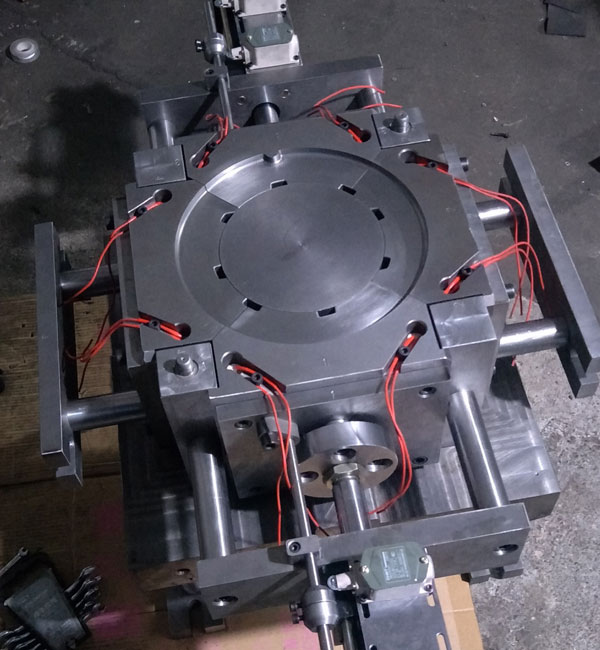
Low Pressure Casting
Low Pressure Casting means that the mold is generally placed above a sealed crucible, and compressed air is introduced into the crucible to cause a low pressure (0.06~0.15MPa) on the surface of the molten metal, so that the molten metal rises from the riser pipe to fill the mold and control Solidified casting method. This casting method has good feeding and dense structure, easy to cast large thin-walled complex castings, no risers, and a metal recovery rate of 95%. No pollution, easy to realize automation.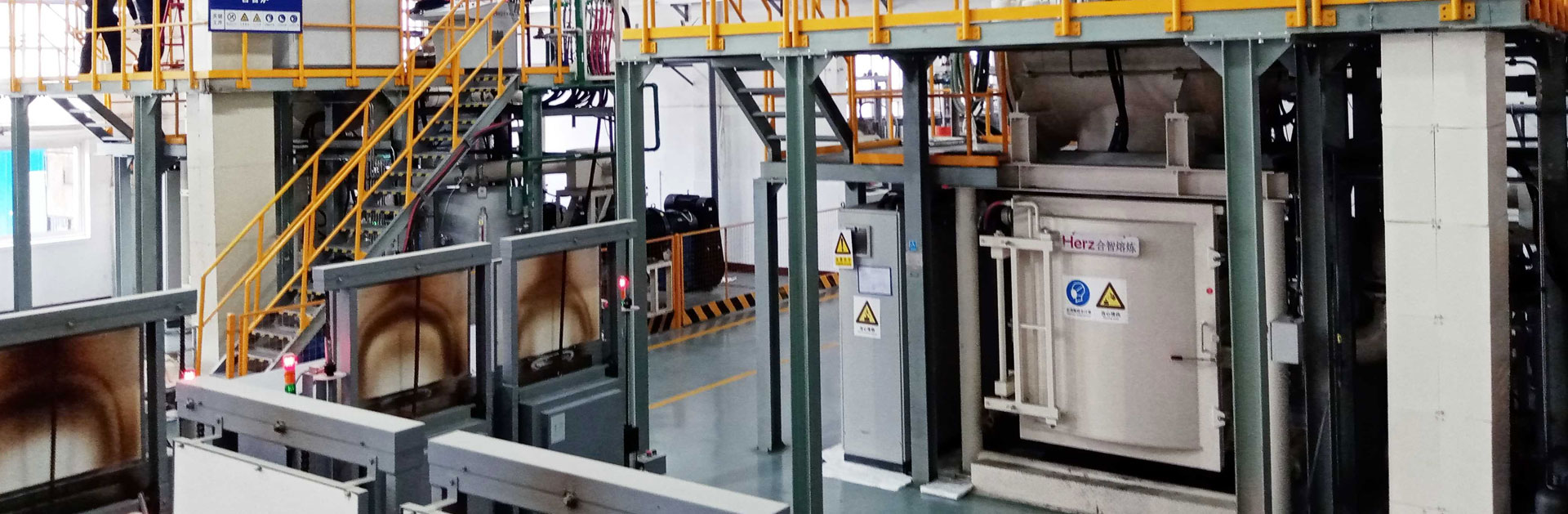