Drilling
What is Cnc Drilling Process & Drilling Machining & - Drilling Services
Any kind of machine cannot be made without holes. To connect the parts, various screw holes, pin holes or rivet holes of different sizes are required; in order to fix the transmission parts, various mounting holes are required; the machine parts themselves also have many various holes (such as oil holes, Process hole, weight reduction hole, etc.). The operation of machining a hole to make the hole meet the requirements is called hole machining.
The inner hole surface is one of the important surfaces that make up the mechanical parts. In mechanical parts, parts with holes generally account for 50% to 80% of the total number of parts. The types of holes are also diverse, including cylindrical holes, conical holes, threaded holes, and shaped holes.
Common cylindrical holes are different from general holes and deep holes, and deep holes are difficult to machine.
Minghe’s drilling machining services were originally added to compliment and support our forming capabilities. Today, customers utilize our industry leading drilling services even when forming is not needed. For 35 years, we have been evolving our drilling services to provide customers with the right solutions to their specific application. Minghe engineers will review the product specifications, material call outs and volume requirements to select the most cost effective solution for your drilling project.
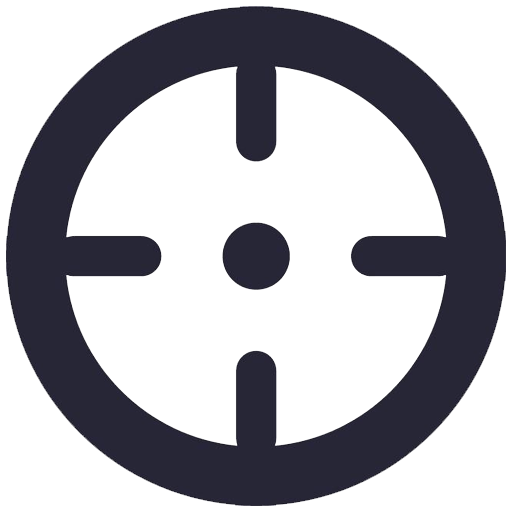
Technical Requirements For Hole Drilling
In the process of hole processing, it is necessary to avoid problems such as excessively large hole diameter expansion, poor surface roughness of the workpiece, and excessive wear of the drill bit, so as to prevent affecting the quality of the drilling and increasing the processing cost. The following technical requirements should be ensured as far as possible:
- – Dimensional accuracy: the accuracy of the diameter and depth of the hole;
- – Shape accuracy: hole roundness, cylindricity and axis straightness;
- – Position accuracy: the coaxiality between the hole and the axis of the hole or the axis of the outer circle; the parallelism and perpendicularity between the hole and the hole or the hole and other surfaces, etc.
At the same time, the following 5 elements should also be considered:
- – The structure of hole depth and tolerance surface roughness hole;
- – The structural characteristics of the workpiece, including the stability of the clamping overhang and the rotatability;
- – The power speed, coolant system and stability of the machine tool;
- – Processing batch;
- – Processing cost;
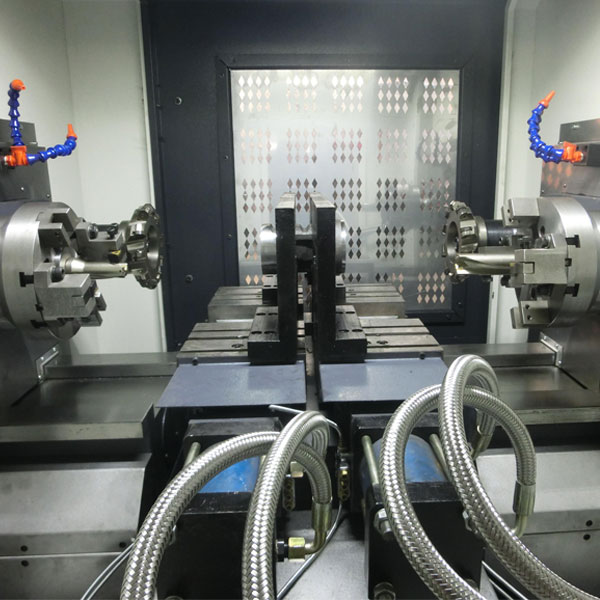
Different Types of Drilling Machining – Cnc Drilling Services Available at Minghe
Various holes of mold parts, such as screw holes, screw holes, pin holes, mandrel holes, round core fixing holes, etc., need to be drilled and reamed to meet the requirements of hole diameter, hole pitch accuracy and roughness.
The commonly used processing methods are shown in the table.
Type | Content |
Single Part Drilling | Single part is drilled directly according to the marking position |
Pilot Drill | Drill a hole in one part first, and use this as a guide to drill holes in other parts. One part can be used for direct drilling in the opposite direction when drilling; it can also lead out the drill hole to make the opposite direction drilling. |
Combination Drilling | In order to ensure the hole distance of the parts, the two parts can be clamped with parallel chucks or combined with screws to form a whole, and the holes can be drilled at the same time according to the marking. |
Reaming Machining
There are often some pin holes, ejector holes, core fixing holes, etc. in the mold that need to be processed after scribing or during assembly. The processing accuracy is generally IT6 to IT8, and the roughness is not less than Ra3.2μm.
General Principles Of Reaming
Type | Content | |
Workpiece diameter | <10 | Drilled and reamed by fitter |
10~20 | Processing by drilling, countersinking, reaming, etc. | |
>20 | Pre-controlled by the fitter drill, then milling and boring machine processing | |
Need to quench the hole | When reaming, the amount of grinding should be 0.02~0.03. The holes should be protected during heat treatment and will be ground again when assembled | |
Combination reaming of different materials | When reaming parts of different materials, reaming should be made from harder materials | |
Hardening hardware reaming | Through the hole reaming of the hardening hardware, first check whether the hole is deformed, reaming with a standard cemented carbide reamer, or reaming with an old reamer, and then use a cast iron grinding rod to grind to the required size | |
Reamed hole | When the hole is not reamed, the depth of the reaming hole should be deepened, leaving the length of the cutting part of the reamer to ensure the effective diameter of the hole; it can also be reamed with a standard reamer, and then reaming the hole with an old reamer that has ground the cutting part. Unhinged bottom | |
Machine hinge | After the workpiece is clamped once, drilling, countersinking, and reaming are carried out continuously to ensure the perpendicularity and parallelism of the hole |
Deep Hole Machining
The cooling channel holes, heater holes and part of the ejector pin holes in the plastic mold need to be deep-hole processed. Generally, the accuracy of the cooling water hole is not high, but it is necessary to prevent deflection; in order to ensure the heat transfer efficiency, the heater hole has certain requirements for the hole diameter and roughness, the hole diameter is 0.1~0.3mm larger than the heating rod, and the roughness is Ra12.5~6.3 μm; while the ejector hole requires a higher level, the general accuracy is IT8 and there are requirements for verticality and roughness.
Hole processing
Many holes in the mold are required to ensure the hole distance, hole edge distance, parallelism of the axis of each hole, perpendicularity to the end face, and coaxiality of the holes after the two parts are assembled. This type of hole system is generally processed first, and then the holes are processed by scribing.
Choose The Best Drilling Process
After browsing a list of Surface Treatment services, select a process based on essential considerations, like production time, cost-effectiveness, part tolerance, durability and applications. High-tolerance CNC milling, turning parts are not recommended to apply secondary metal surface finish, because the treatment may change the sizes of the finished part through removing or adding a small amount of materials.
Contact us or Email sales@hmminghe.com to see how our people, equipment and tooling can bring the best quality for the best price for your drilling project.