The Measures To Improve The Life Of Aluminum-Magnesium Alloy Die Casting Mold
As an important processing equipment, aluminum-magnesium alloy die-casting molds have a direct impact on the product quality and economic benefits of the company. The mold material and heat treatment technology are the main factors affecting the life of aluminum-magnesium alloy die-casting molds. This article analyzes the main failure modes of aluminum-magnesium alloy die-casting molds, briefly introduces typical mold steels and common heat treatment methods, and points out that a reasonable selection of mold materials and heat treatment processes can significantly improve mold thermal stability, hardenability, wear resistance, and thermal stability. Properties such as fatigue and thermal conductivity, thereby increasing the service life of the mold.
The Failure Mode Of Aluminum-Magnesium Alloy Die Casting Mold
The aluminum-magnesium alloy die-casting mold is a forming mold used to die-cast aluminum-magnesium alloy castings on a die-casting machine. The surface temperature of the cavity can reach about 600 ℃ during work, and the molten aluminum-magnesium alloy liquid is easy to adhere to steel materials. Frequent application of anti-stick coatings to the mold cavity causes severe fluctuations in the surface temperature of the cavity. The main failure modes are mold sticking, erosion, thermal fatigue and wear. When the mold cavity structure is complex and there is stress concentration, the mold will also break and fail under the combined action of thermal load and mechanical load.
1.1 Sticky Mold
When the aluminum-magnesium alloy parts and the mold surface are moving, due to the uneven surface, the local stress of some contact points exceeds the yield strength of the material to bond, and the bonded joints are sheared and fractured and pulled apart, making the surface material of the mold Transfer to the workpiece or fall off.
1.2 Erosion
When the mold surface is in contact with the aluminum-magnesium alloy liquid for relative movement, the bubble formed at the contact between the liquid and the mold ruptures and produces instantaneous impact and high temperature, causing the mold surface to form tiny pits and pits. The aluminum-magnesium alloy liquid and small solid particles fall at a high speed and repeatedly impact the surface of the mold, causing local material loss and forming pits and pits on the metal surface. Under repeated action, fatigue cracks will develop on the surface of the die, and even local fractures will occur.
1.3 Thermal Fatigue
The surface of the mold is repeatedly subjected to heating and cooling to cause fatigue and form cracks. The main reason for the cracking of aluminum-magnesium alloy die-casting mold is the difference between the pouring temperature and the preheating temperature of the mold. The greater the temperature difference, the faster the cooling rate, the easier the thermal fatigue cracks will occur. Secondly, the thermal cycle speed, the heat treatment process of the mold and the Surface treatment is also closely related.
1.4 Wear
Because the friction between the mold surface and the processed high-temperature aluminum-magnesium alloy parts cannot be lubricated, and the high-temperature workpieces are oxidized, the surface of the mold cavity is tempered and softened, and the low hardness increases the wear. The severe wear prevents the mold from processing qualified products. Retirement is invalid.
1.5 Break
The phenomenon that the aluminum-magnesium alloy die-casting mold has large cracks or partial separation during work and loses its normal service ability is called fracture failure. Mold fracture is usually manifested as local fragments or the entire mold is broken into several parts.
Selection Of Aluminum Magnesium Alloy Die Casting Die Steel
The type of mold material, chemical composition, metallographic structure, hardness, toughness, hypoploid structure and other comprehensive factors are important reasons for the failure of aluminum-magnesium alloy die-casting molds. Poor working conditions require aluminum-magnesium alloy die-casting molds to have high The performance of anti-tempering stability and resistance to cold and heat fatigue, has good resistance to high temperature, high pressure and high speed liquid aluminum-magnesium alloy erosion ability and high strength and toughness.
2.1 3Cr2W8V (H21) steel
Containing more tungsten, chromium, and vanadium elements, it has high hardenability, tempering stability, and thermal strength. It is suitable for die-casting molds with high bearing capacity, high thermal strength and high tempering stability.
2.2 4Cr5MoSiV1 (H13) steel
It has high toughness and resistance to cold and heat fatigue, and it is not easy to produce thermal fatigue cracks. Even if thermal fatigue cracks appear, they are thin and short, and are not easy to expand. There is no need to preheat before use, and it can be cooled by tap water. The thermal strength.
2.3 4Cr5Mo2MnSiV1 (Y10) steel
Molybdenum with a mass fraction of about 2% is added, supplemented by elements such as vanadium and mud to improve thermal stability, and appropriate amounts of silicon and manganese are added to increase the strength of the matrix, with good thermal fatigue performance and resistance to molten metal corrosion.
2.4 4Cr5MoSiV (H11) Steel
It belongs to the tungsten hot work die steel. It has good toughness under medium temperature conditions, good thermal strength, thermal fatigue performance and certain wear resistance. It is air quenched and heat treated under lower austenitizing temperature conditions. The deformation is small, the tendency to produce oxide scale during air quenching is small, and it can resist the erosion effect of molten aluminum.
2.5 3Cr3Mo3VNb (HM3) Steel
A new type of high-strength and toughness hot forging die steel, which adds trace element Nb under the condition of low carbon content to improve tempering resistance and thermal strength, has obvious tempering secondary hardening effect, and can effectively overcome the mold Early failure due to thermal wear, thermal fatigue, thermal cracking, etc.
2.6 4Cr3Mo3SiV (H10) Steel
It has higher hardness, heat resistance and wear resistance at working temperature of 500 ~ 600 ℃, and has very good hardenability and high toughness, tempering resistance and thermal stability are higher than H13 steel, impact toughness The hardness and fracture toughness are higher than that of 3Cr2W8V steel. When the tempering temperature exceeds 260℃, the hardness of the steel is higher than that of H13 steel. The use of high-strength and tough mold materials is a very important measure to improve the performance of aluminum-magnesium alloy die-casting molds and extend the service life of the mold. For example, a certain mold is directly processed by 3Cr2W8V steel. Dimensions φ180x85mm, hardness requirement 42~46HRC, can only be die-cast 249 in production and use,
900 pieces. Later, it was made of 4Cr3Mo3SiV, and the service life was increased to 1000.000 pieces.
Selection Of Heat Treatment Process For Aluminum-Magnesium Alloy Die-casting Mold
The heat treatment of the aluminum-magnesium alloy die-casting mold is to change the structure of the mold steel, so that the mold can obtain the required structure and performance, and can extend the service life of the mold. The heat treatment process specification should be determined according to the mold material, mold shape, size, and complexity.
3.1 Pre-heat Treatment
The pre-heat treatment of the die-casting mold can adopt three processes: continuous annealing, isothermal annealing and quenching and tempering heat treatment. The purpose is to obtain a uniform structure and dispersed carbide before the final heat treatment to improve the strength and toughness of the steel. The continuous annealing process is relatively simple, and a better granular pearlite structure can also be obtained. For die-casting molds with complex shapes and high requirements, isothermal annealing can be used to obtain a more ideal granular pearlite structure.
3.2 Quenching And Preheating
Die-casting mold steel is mostly high-alloy steel with poor thermal conductivity. Preheating measures are often taken during quenching and heating. The number of preheating and temperature depend on the composition of the die steel and the requirements for mold deformation. For molds with low quenching temperature, simple shape, and low deformation requirements, a preheating (800℃~850℃) should be carried out during quenching heating without cracking. For molds with higher temperature quenching, complex shapes and high deformation requirements, secondary preheating (600 to 650°C, 800 to 850°C) is necessary. The purpose is to reduce the stress generated during the heating process and at the same time make the overall structure of the mold uniform .
3.3 Quenching Heating
The quenching heating temperature of the die-casting mold can be implemented according to the quenching heating specification of each steel grade. For example, the quenching temperature of 3Cr2W8V steel is 1050~1150℃, and the quenching temperature of H13 steel is 1020~1100℃. In order to ensure full dissolution of carbides, obtain uniform austenite, and obtain good high-temperature performance, the quenching and heating holding time of die-casting molds should be appropriately extended. Generally, the heating holding coefficient in the salt bath furnace is 0.8 ~ 1.0min/mm.
3.4 Quenching And Cooling
The oil quenching rate is fast and good performance can be obtained, but the tendency of deformation and cracking is great. Generally, oil cooling is used for die-casting molds with simple shapes and low deformation requirements; for die-casting molds with complex shapes and high deformation requirements, hierarchical quenching should be used to prevent mold deformation and cracking. Quench cooling should be as slow as possible to reduce quenching deformation, heating and quenching in a vacuum resistance furnace, cooling can be adopted gas quenching. Heating and quenching in a salt bath, and grading quenching can be adopted when cooling. When the mold is quenched and cooled, it should be tempered immediately after it is soaked and cooled to 150~200℃, and it is not allowed to cool to room temperature.
3.5 Tempering
The hardness of the die-casting mold is achieved by tempering, and the hardness of the die-casting mold cavity directly affects the hot and cold fatigue life of the mold. Different materials, different quenching temperature, and tempering temperature are also different. For example, the hardness of 3Cr2W8V steel aluminum-magnesium alloy die-casting mold is generally 42 ~ 48HRC, and its tempering temperature is generally selected between 560 ~ 620 ℃, but if high temperature quenching is used, the tempering temperature is as high as 670 ℃. The hardness after quenching at 1150°C and tempering at 650°C is 45HRC; while the hardness after quenching at 1050°C and tempering at 650°C is 35HRC.
3.6 Surface Strengthening Treatment
After the die-casting mold is quenched and tempered, the surface hardness is not very high. In order to obtain high hardness and wear resistance on the surface of the die-casting mold, while the core part still maintains sufficient strength and toughness, and to improve the anti-sticking performance of the aluminum-magnesium alloy die-casting mold, surface nitriding can be performed on the die-casting mold. Or nitrocarburizing treatment. The use of toughening treatment and surface strengthening treatment process is an important way to improve the performance and life of the mold. For example, the nitrocarburizing heat treatment medium of H13 die-casting mold is ammonia gas + ethanol, and the process is 580℃ x4.5h. After quenching at 1030°C and tempering at 600°C and 580 gas nitrocarburizing heat treatment, the surface hardness of the mold is above 900HV, the matrix hardness is 46~48HRC, and the wear resistance, fatigue resistance and corrosion resistance of the mold are greatly improved. .
Conclusion
In the production of aluminum-magnesium alloy die-casting molds, it is necessary to analyze and study the causes of failure according to the working conditions of the mold, correctly select the mold material, and formulate a reasonable heat treatment process to ensure the mold surface hardness, wear resistance, core strength and toughness, and prevent metal liquid corrosion and mold sticking. , Effectively reduce the rejection rate and significantly increase the service life of the mold. Production practice has proved that preheating the aluminum-magnesium alloy die-casting mold to an effective and economical temperature can reduce the temperature difference between the mold and the workpiece, reduce the generation of mold cracks, extend the service life of the mold, and increase productivity. Of course, during the use of aluminum-magnesium alloy die-casting molds, correct use, reasonable management, and careful maintenance are also effective measures to reduce the early fracture failure of the mold and increase the service life of the mold.
Related Pages:mold manufacturing
Please keep the source and address of this article for reprinting: The Measures To Improve The Life Of Aluminum-Magnesium Alloy Die Casting Mold
Minghe Die Casting Company are dedicated to manufacture and provide quality and high performance Casting Parts(metal die casting parts range mainly include Thin-Wall Die Casting,Hot Chamber Die Casting,Cold Chamber Die Casting),Round Service(Die Casting Service,Cnc Machining,Mold Making,Surface Treatment).Any custom Aluminum die casting, magnesium or Zamak/zinc die casting and other castings requirements are welcome to contact us.
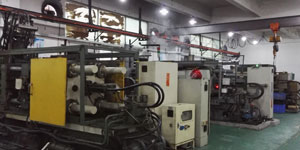
Under the control of ISO9001 and TS 16949,All processes are carried out through hundreds of advanced die casting machines, 5-axis machines, and other facilities, ranging from blasters to Ultra Sonic washing machines.Minghe not only has advanced equipment but also have professional team of experienced engineers,operators and inspectors to make the customer’s design come true.
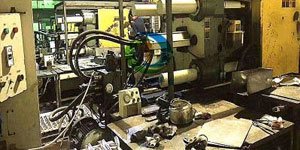
Contract manufacturer of die castings. Capabilities include cold chamber aluminum die casting parts from 0.15 lbs. to 6 lbs., quick change set up, and machining. Value-added services include polishing, vibrating, deburring, shot blasting, painting, plating, coating, assembly, and tooling. Materials worked with include alloys such as 360, 380, 383, and 413.
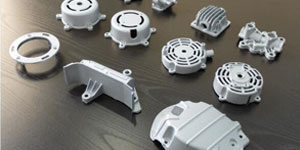
Zinc die casting design assistance/concurrent engineering services. Custom manufacturer of precision zinc die castings. Miniature castings, high pressure die castings, multi-slide mold castings, conventional mold castings, unit die and independent die castings and cavity sealed castings can be manufactured. Castings can be manufactured in lengths and widths up to 24 in. in +/-0.0005 in. tolerance.
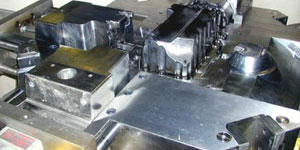
ISO 9001: 2015 certified manufacturer of die cast magnesium, Capabilities include high-pressure magnesium die casting up to 200 ton hot chamber & 3000 ton cold chamber, tooling design, polishing, molding, machining, powder & liquid painting, full QA with CMM capabilities, assembly, packaging & delivery.
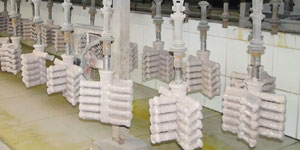
ITAF16949 certified. Additional Casting Service Include investment casting,sand casting,Gravity Casting, Lost Foam Casting,Centrifugal Casting,Vacuum Casting,Permanent Mold Casting,.Capabilities include EDI, engineering assistance, solid modeling and secondary processing.
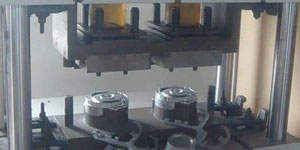
Casting Industries Parts Case Studies for: Cars, Bikes, Aircraft, Musical instruments, Watercraft, Optical devices, Sensors, Models, Electronic devices, Enclosures, Clocks, Machinery, Engines, Furniture, Jewelry, Jigs, Telecom, Lighting, Medical devices, Photographic devices, Robots, Sculptures, Sound equipment, Sporting equipment, Tooling, Toys and more.
What Can we help you do next?
∇ Go To Homepage For Die Casting China
→Casting Parts-Find out what we have done.
→Ralated Tips About Die Casting Services
By Minghe Die Casting Manufacturer |Categories: Helpful Articles |Material Tags: Aluminum Casting, Zinc Casting, Magnesium Casting, Titanium Casting, Stainless Steel Casting, Brass Casting,Bronze Casting,Casting Video,Company History,Aluminum Die Casting |Comments Off