How to improve the service life of the intermediate frequency furnace?
Improving the service life of the induction furnace body is the goal pursued by every foundry worker, and it will also be of great significance to the enterprise. The main factors affecting the service life of electric furnace crucibles are lining refractory materials, furnace technology and use technology, which will be introduced separately below.
Furnace lining refractories
The quality of the lining refractory material and its performance play a fundamental role in the service life of the furnace.
- Refractory materials for furnace construction must have a high degree of refractoriness, resist high temperature heat load, and do not soften or melt. At the same time, it must have high volume stability, resist high temperature heat load, and have no volume shrinkage and only uniform expansion.
- The composition of refractory materials. Impurities in refractory materials can form compounds with low melting points at high temperatures, thereby reducing the refractoriness of refractory materials. Therefore, the quartz content in the furnace lining sand must be guaranteed, and the impurity composition must be strictly controlled. The composition of the furnace lining sand is controlled as follows: ω (SiO2) ≥ 98.0%; ω (Al2O3) ≤ 0.5%; ω (Fe2O3) ≤ 0.5%; ω (TiO2) ≤ 0.05%; ω (H2O) ≤ 0.5%.
- Granularity ratio of refractory materials. The reasonable particle size ratio of refractory materials can easily form a high-density refractory layer during the furnace building process, and defects are not easy to appear during the use process. The following is a set of reasonable ratios: 3.35mm~5mm, 0.85mm~1.70mm, 0.1mm~0.85mm, and the proportions below 0.1mm are 17%, 33%, 20%, and 30% respectively.
Oven process
The oven is a process to obtain the sintered layer. The quality of the sintered layer directly affects the service life of the furnace. The oven is an important link. After the oven cavity is built, the oven should be dried immediately; before the oven, check whether the electrical equipment and cooling water system are normal; the oven must be carried out in strict accordance with the oven process. The oven process is a key factor in the oven process. The specific points: ① The heating rate must be controlled, especially in the early stage of the oven. If the heating rate is too fast and the moisture in the furnace lining is discharged too quickly, cracks are likely to form, which will make the life of the furnace Greatly shortened. ②When the furnace lining is heated to 573℃, the quartz will expand too fast during the phase transition process, which will easily cause cracks or even peeling. Therefore, when the furnace is heated at 400℃ to 600℃, the heating speed should be slowed down, and at 870℃, it should be kept for 1h~2h. , So that it can slowly and completely phase change. ③The final stage of the oven is sintering and heat preservation. The sintering temperature depends on the specific refractory material. Generally, it is hoped that a sintered layer with a thickness of 30% of the lining thickness can be obtained. Therefore, the sintering temperature is generally 50-100 ℃ higher than the tapping temperature.
Furnace technology
The various processes of the furnace use process are also very important to the service life of the furnace, and various improper operations may reduce the service life of the furnace. Therefore, the following points should be paid attention to during use.
- Since the sintering layer of the new furnace is thin, the use process of the new furnace is very important. The first furnace of the new furnace should be charged and melted after 50% of the water is discharged. This can avoid defects such as rapid cooling of the furnace lining after all the water is discharged, and cracks; the new furnace should be continuously smelted as much as possible to avoid intermittent smelting caused by sudden cold and hot The cracks should generally be melted continuously for 1 week.
- Try to avoid high temperature smelting during the smelting process. In the high temperature state, the furnace lining will react with the molten iron in the crucible, as shown in the following formula: SiO2+2C→Si+2CO. The higher the temperature, the higher the C and the lower the Si, the corrosion loss of the furnace lining will increase, especially when the furnace is new. For obvious reasons, try to avoid high temperature while ensuring the water outlet temperature when melting.
- Avoid overheating of the furnace lining. Because the heating rate of the intermediate frequency furnace is quite fast, when the smelter is not paying attention, the charge will appear "bridging" and the furnace lining will appear local high temperature or even exceed the refractoriness of the furnace lining, which may cause the furnace lining to melt and corrode.
- During use, when the furnace needs to be shut down for a long time due to failures and other reasons, the molten iron in the furnace should be emptied to avoid the lining of the furnace lining from being damaged by the cracking of the furnace lining when the molten iron is condensed.
- Try to use clean charge during use, especially when the furnace is new.
- When the furnace is stopped for cooling, in order to avoid sudden cooling of the furnace lining, an empty furnace should be cooled. At the same time, in order to avoid cracks caused by the excessive temperature difference between the upper and lower sides of the furnace lining during the cooling process, the furnace cover should be covered to make the furnace lining uniform up and down during cooling. Ensure the service life of the furnace.
- Since vertical cracks are unavoidable when the furnace is cold, when the cold furnace is started, the furnace should be baked at a low temperature before melting, so that the cracks can be closed first, and the cracks can be prevented from infiltrating into the cracks when the molten iron is melted and the cracks are further expanded.
- Pay attention to the furnace conditions during the use of the furnace. Observing the furnace conditions is a kind of protection for the furnace. The furnace bottom is measured every 3 days, and the furnace wall must be observed for each furnace every day, thus ensuring the safety of the furnace lining.
- Maintenance and maintenance of electric furnace equipment, such as frequent purging of the coil, cleaning the debris on the coil to prevent coil breakdown, thus avoiding the furnace disassembly caused by equipment failure, and effectively improving the service life of the crucible.
Please keep the source and address of this article for reprinting:How to improve the service life of the intermediate frequency furnace?
Minghe Die Casting Company are dedicated to manufacture and provide quality and high performance Casting Parts(metal die casting parts range mainly include Thin-Wall Die Casting,Hot Chamber Die Casting,Cold Chamber Die Casting),Round Service(Die Casting Service,Cnc Machining,Mold Making,Surface Treatment).Any custom Aluminum die casting, magnesium or Zamak/zinc die casting and other castings requirements are welcome to contact us.
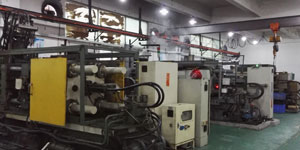
Under the control of ISO9001 and TS 16949,All processes are carried out through hundreds of advanced die casting machines, 5-axis machines, and other facilities, ranging from blasters to Ultra Sonic washing machines.Minghe not only has advanced equipment but also have professional team of experienced engineers,operators and inspectors to make the customer’s design come true.
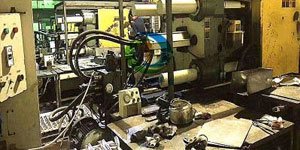
Contract manufacturer of die castings. Capabilities include cold chamber aluminum die casting parts from 0.15 lbs. to 6 lbs., quick change set up, and machining. Value-added services include polishing, vibrating, deburring, shot blasting, painting, plating, coating, assembly, and tooling. Materials worked with include alloys such as 360, 380, 383, and 413.
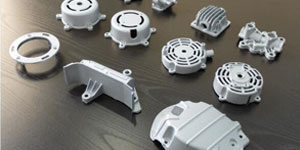
Zinc die casting design assistance/concurrent engineering services. Custom manufacturer of precision zinc die castings. Miniature castings, high pressure die castings, multi-slide mold castings, conventional mold castings, unit die and independent die castings and cavity sealed castings can be manufactured. Castings can be manufactured in lengths and widths up to 24 in. in +/-0.0005 in. tolerance.
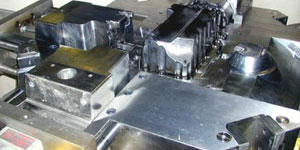
ISO 9001: 2015 certified manufacturer of die cast magnesium, Capabilities include high-pressure magnesium die casting up to 200 ton hot chamber & 3000 ton cold chamber, tooling design, polishing, molding, machining, powder & liquid painting, full QA with CMM capabilities, assembly, packaging & delivery.
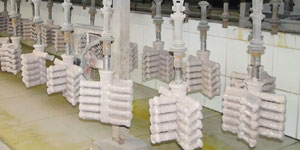
ITAF16949 certified. Additional Casting Service Include investment casting,sand casting,Gravity Casting, Lost Foam Casting,Centrifugal Casting,Vacuum Casting,Permanent Mold Casting,.Capabilities include EDI, engineering assistance, solid modeling and secondary processing.
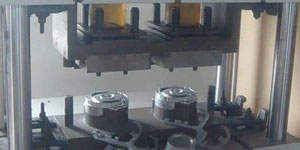
Casting Industries Parts Case Studies for: Cars, Bikes, Aircraft, Musical instruments, Watercraft, Optical devices, Sensors, Models, Electronic devices, Enclosures, Clocks, Machinery, Engines, Furniture, Jewelry, Jigs, Telecom, Lighting, Medical devices, Photographic devices, Robots, Sculptures, Sound equipment, Sporting equipment, Tooling, Toys and more.
What Can we help you do next?
∇ Go To Homepage For Die Casting China
→Casting Parts-Find out what we have done.
→Ralated Tips About Die Casting Services
By Minghe Die Casting Manufacturer |Categories: Helpful Articles |Material Tags: Aluminum Casting, Zinc Casting, Magnesium Casting, Titanium Casting, Stainless Steel Casting, Brass Casting,Bronze Casting,Casting Video,Company History,Aluminum Die Casting |Comments Off