How Does Silicon Carbide Improve The Quality Of Castings?
1.Introduction
The chemical composition of molten iron is the same, and the smelting process is different, and the properties of cast iron obtained vary greatly. The foundry adopts methods such as molten iron overheating, inoculation treatment, changing the charge ratio, adding trace or alloying elements, etc., to improve the metallurgical quality and casting performance of cast iron, and at the same time greatly improve the mechanical properties and processing performance. Induction electric furnace smelting of molten iron can effectively control the temperature of molten iron, accurately adjust the chemical composition, reduce element burning loss, and have low sulfur and phosphorus content. It is very beneficial for the production of ductile iron, vermicular graphite cast iron and high-strength gray cast iron. However, the nucleation rate of molten iron smelted in the induction electric furnace is reduced, and the white mouth tends to be large, and it is easy to produce supercooled graphite. Although the strength and hardness have increased, the metallurgical quality of cast iron is not high.
In the 1980s, Chinese engineers who went abroad to study and study saw that black broken glass-like objects were added to the electric furnace of foreign foundries when they were smelted. After inquiries, they learned that it was silicon carbide. Domestic Japanese-funded foundry companies have also used silicon carbide as an additive in large quantities for a long time. In cupola or electric furnace smelting molten iron, the advantages of adding pretreatment agent SiC are many. Silicon carbide is divided into abrasive grade and metallurgical grade. The former is high in purity and expensive, while the latter is low in price.
The silicon carbide added into the furnace is converted into carbon and silicon of cast iron. One is to increase the carbon equivalent; the other is to strengthen the reduction of molten iron and greatly reduce the adverse effects of rusty charge. The addition of silicon carbide can prevent the precipitation of carbides, increase the amount of ferrite, make the cast iron structure dense, significantly improve the processing performance and make the cutting surface smooth. Increase the number of graphite balls per unit area of nodular cast iron and increase the spheroidization rate. It also has a good effect on reducing non-metallic inclusions and slag, eliminating shrinkage porosity, and eliminating subcutaneous pores.
2. The Role Of Pretreatment
2.1 The principle of nucleation In Fe-C eutectic system, gray cast iron is the leading phase of eutectic due to the high melting point of graphite during the eutectic solidification stage, and austenite is precipitated by graphite. The two-phase graphite + austenite co-grown and co-grown grains formed with each graphite core as the center are called eutectic clusters. The submicroscopic graphite aggregates, unmelted graphite particles, some high melting point sulfides, oxides, carbides, nitride particles, etc. existing in the cast iron melt may become heterogeneous graphite nuclei. There is no essential difference between the nucleation of nodular cast iron and the nucleation of gray cast iron, except that magnesium oxides and sulfides are added to the core material.
The precipitation of graphite in molten iron must undergo two processes: nucleation and growth. There are two ways of graphite nucleation: homogeneous nucleation and heterogeneous nucleation. Homogeneous nucleation is also called spontaneous nucleation. There are a large number of undulating carbon atoms in the molten iron that exceed the critical crystal nucleus size, and the carbon atom groups arranged in an orderly manner in the short range may become homogeneous crystal nuclei. Experiments show that the degree of supercooling of homogeneous crystal nuclei is very large, and the heterogeneous crystal nucleus must be mainly used as a nucleating agent for graphite in molten iron. There are a large number of foreign particles in the molten cast iron, and there are 5 million oxidized material points in every 1cm3 of molten iron. Only those particles that have a certain relationship with the lattice parameters and phases of graphite can become graphite nucleation substrates. The characteristic parameter of the lattice matching relationship is called the plane mismatch degree. Of course, only when the mismatch of the lattice plane is small can the carbon atoms easily match the graphite nucleus. If the nucleation material is carbon atoms, then their mismatch degree is zero, and such nucleation conditions are the best.
The internal energy of silicon carbide decomposed into carbon and silicon in molten iron is greater than the carbon and silicon contained in the molten iron itself. The Si contained in the molten iron itself is dissolved in austenite, and the carbon in the molten iron of ductile cast iron is partly in the iron. Graphite spheres are formed in the liquid, some of which have not yet been precipitated in austenite. Therefore, the addition of silicon carbide has a good deoxidation effect.
- Si + O2 → SiO2
- (1) MgO +SiO2 →MgO∙SiO2
- (2) 2MgO +2SiO2→ 2MgO∙2SiO2
- (3) Enstatite composition MgO∙SiO2 and forsterite composition 2MgO∙2SiO2 have a high degree of mismatch with graphite (001), which is difficult to be used as a base for graphite nucleation. After being treated with molten iron containing Ca, Ba, Sr, Al and ferrosilicon, MgO∙SiO2 + X → XO∙SiO2 + Mg
- (4) (2MgO∙2SiO2) + 3X+ 6Al → 3 (XO∙Al2O3∙2SiO2) + 8Mg
- (5) Where X——Ca, Ba, Sr.
The reaction products XO∙SiO2 and XO∙Al2O3∙SiO can form faceted crystals on MgO∙SiO2 and 2MgO∙2SiO2 substrates. Due to the low mismatch between graphite and XO∙SiO2 and XO∙Al2O3∙SiO2, it is conducive to graphite nucleation. Good graphitization. It can improve the processing performance and improve the mechanical properties.
2.2 Pre-inoculation of non-equilibrium graphite:
Generally, the scope of heterogeneous nucleation is expanded through inoculation, and the role of heterogeneous nucleation in molten iron:
- ①Promote a large amount of precipitation of C in the eutectic solidification stage and form graphite to promote graphitization;
- ②Reduce the degree of molten iron supercooling and reduce the tendency of white mouth;
- ③Increase the number of eutectic clusters in gray cast iron or increase the number of graphite balls in ductile iron.
SiC is added during the smelting of the charge. Silicon carbide has a melting point of 2700°C and does not melt in molten iron. It only melts in molten iron according to the following reaction formula.
SiC+Fe→FeSi+C (non-equilibrium graphite)
(6) In the formula, Si in SiC is combined with Fe, and the remaining C is non-equilibrium graphite, which serves as the core of graphite precipitation. Non-equilibrium graphite makes C in the molten iron unevenly distributed, and the local C element is too high, and "carbon peaks" will appear in the micro areas. This new graphite has high activity, and its mismatch with carbon is zero, so it is easy to absorb the carbon in the molten iron, and the inoculation effect is extremely superior. It can be seen that silicon carbide is such a silicon-based nucleating agent.
Silicon carbide is added during the smelting of cast iron. For gray cast iron, the pre-incubation of non-equilibrium graphite will generate a large number of eutectic clusters and increase the growth temperature (reduce the relative undercooling), which is conducive to the formation of type A graphite; the number of crystal nuclei increases, making the flakes Graphite is fine, which improves the degree of graphitization and reduces the tendency of white mouth, thereby improving the mechanical properties. For spheroidal graphite cast iron, the increase of crystalline cores increases the number of graphite spheres and the spheroidization rate can be improved.
2.3 Elimination of E-type graphite hypereutectic gray cast iron. C-type and F-type primary graphite are formed in the liquid phase. Because the growth process is not interfered by austenite, under normal circumstances, it is easy to grow into large flakes and less branched C-type Graphite: When the thin-walled casting is cooled rapidly, the graphite will branch and grow into a star-shaped F-type graphite.
The flake graphite grown in the eutectic solidification stage produces A, B, E, D graphites of different shapes and different distributions under different chemical compositions and different undercooling conditions.
Type A graphite is formed in the eutectic cluster with low undercooling and strong nucleation ability, and is evenly distributed in cast iron. Among the fine flake pearlite, the smaller the graphite length, the higher the tensile strength, which is suitable for machine tools and various mechanical castings.
Type D graphite is point and sheet-like interdendritic graphite with non-directional distribution. D-type graphite cast iron has a high ferrite content and its mechanical properties are affected. However, D-type graphite cast iron has many austenite dendrites, graphite is short and curled, and the eutectic group is in the form of pellets. Therefore, compared with the same matrix A-type graphite cast iron, it tends to have higher strength.
Type E graphite is a kind of flake graphite that is shorter than Type A graphite. Like D-type graphite, it is located between dendrites and is collectively referred to as dendritic graphite. E ink is easy to be produced in cast iron with low carbon equivalent (large degree of hypoeutectic) and rich austenite dendrites. At this time, the eutectic clusters and dendrites cross-growth. Because the number of interdendritic eutectic iron liquid is small, the precipitated eutectic graphite only distributes along the direction of the dendrites, which has obvious directionality. The degree of undercooling forming E-type graphite is greater than that of A-type graphite and less than that of D-type graphite, and its thickness and length are between A and D-type graphite. Type E graphite does not belong to supercooled graphite, and is often accompanied by type D graphite. The directional distribution of E-type graphite among dendrites makes it easy for cast iron to be brittle and break in a band along the graphite arrangement direction under a small external force. Therefore, E-type graphite appears, and the corners of small castings can be broken by hand, and the strength of the castings is greatly reduced. As the carbon content increases, the cooling rate necessary to form fine interdendritic graphite increases, and the possibility of producing interdendritic graphite decreases. The high degree of overheating of the melt and long-term heat preservation will increase the degree of undercooling, thereby increasing the growth rate of the dendrites, making the dendrites longer and having more obvious directionality. When SiC is used to pre-incubate the molten iron, the undercooling of the primary austenite is reduced at the same time, and short austenite dendrites are observed at this time. Eliminates the structural basis of E-type graphite.
2.4 Improve The Quality Of Cast Iron
For spheroidal graphite cast iron, in the case of the same amount of spheroidizing agent, pretreatment with silicon carbide, the final yield of magnesium is higher. For molten iron pretreated with silicon carbide, if the amount of residual magnesium in the casting is kept approximately the same, the amount of spheroidizing agent added can be reduced by 10%, and the white mouth tendency of nodular cast iron is alleviated.
Silicon carbide in the smelting furnace, in addition to the carbon and silicon in the molten iron shown in the formula (1), the deoxidation reaction of formulas (2) and (3) is also carried out. If the added SiC is close to the furnace wall, the generated SiO2 will deposit on the furnace wall and increase the thickness of the furnace wall. Under the high temperature of smelting, SiO2 will undergo the decarburization reaction of formula (4) and the slagging reaction of formula (5) and (6).
- (7) 3SiC + 2Fe2O3 = 3SiO2 +4Fe +3C
- (8) C + FeO → Fe + CO ↑
- (9) (SiO2) + 2C = [Si] + 2CO (gaseous state)
- (10) SiO2 + FeO → FeO·SiO2 (slag)
- (11) Al2O3 + SiO2 → Al2O3·SiO2 (slag)
The deoxidizing effect of silicon carbide makes the deoxidized product have a series of metallurgical reactions in the molten iron, reducing the harmful effects of oxides in the corroded charge, and effectively purifying the molten iron.
2.5 How To Use Silicon Carbide
The purity of metallurgical grade silicon carbide is between 88% and 90%, and the impurities must be deducted first when calculating the carbon and silicon increase. According to the molecular formula of silicon carbide, it is easy to get: Carbon increase: C= C/(C + Si) = 12 / (12 + 28) = 30% (12) Silicon increase: Si = Si/(C + Si) = 28 / (12 + 28) = 70% (13) The amount of silicon carbide added is usually 0.8%-1.0% of the amount of molten iron. The method of adding silicon carbide is: smelting molten iron in an electric furnace. When the crucible melts 1/3 of the charge, add it to the middle of the crucible, try not to touch the furnace wall, and then continue to add the charge for smelting. In cupola smelting molten iron, silicon carbide with a particle size of 1-5mm can be mixed with an appropriate amount of cement or other adhesives, and water is added to form a mass. After being dried in the hot sun, it can be used in the furnace according to the batch ratio.
3.Concluding Remarks
In the past 20 years, whether it is a truck, a business or a family car, reducing the weight of the vehicle has always been the development trend of automobile research and development. In the market slump of the financial crisis, China Northern Corporation bucked the trend and exported heavy-duty trucks to North America, precisely based on the light weight of heavy-duty trucks. The application of thin-walled gray cast iron, ductile iron and vermicular graphite cast iron, thick-walled ductile iron and Aubrey ductile iron, puts forward higher requirements on the metallurgical quality of cast iron.
The inoculation pretreatment of silicon carbide has a good effect on improving the metallurgical quality of cast iron. Foundry expert Li Chuanshi wrote an article that after the pretreatment agent is added to the molten iron, two effects can be observed: one is to increase the carbon equivalent; the other is to change the metallurgical conditions of the molten iron, which enhances the reducibility.
In 1978, B.C. Godsell of the United Kingdom published its research results on the pretreatment of ductile iron. Since then, the experimental research on the pretreatment process has been uninterrupted, and the process is now relatively mature. For gray cast iron, silicon carbide inoculation pretreatment can reduce the degree of undercooling and reduce the tendency of white mouth; increase the graphite core, promote the formation of A-type graphite, reduce or prevent the production of B-type, E-type and D-type graphite, and increase the number of eutectic clusters. Fine flake graphite; for spheroidal graphite cast iron, the pretreatment of silicon carbide inoculation promotes the increase of the number of graphite balls in the cast iron, the spheroidization rate, and the roundness of the graphite balls.
The use of silicon carbide can strengthen the deoxidation and reduction effect of iron oxide, make the cast iron structure compact and increase the smoothness of the cutting surface. The use of silicon carbide can extend the life of the furnace wall without increasing the aluminum and sulfur content of the molten iron.
Please keep the source and address of this article for reprinting:How Does Silicon Carbide Improve The Quality Of Castings?
Minghe Die Casting Company are dedicated to manufacture and provide quality and high performance Casting Parts(metal die casting parts range mainly include Thin-Wall Die Casting,Hot Chamber Die Casting,Cold Chamber Die Casting),Round Service(Die Casting Service,Cnc Machining,Mold Making,Surface Treatment).Any custom Aluminum die casting, magnesium or Zamak/zinc die casting and other castings requirements are welcome to contact us.
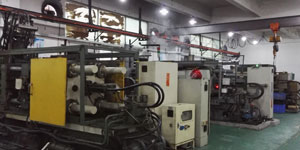
Under the control of ISO9001 and TS 16949,All processes are carried out through hundreds of advanced die casting machines, 5-axis machines, and other facilities, ranging from blasters to Ultra Sonic washing machines.Minghe not only has advanced equipment but also have professional team of experienced engineers,operators and inspectors to make the customer’s design come true.
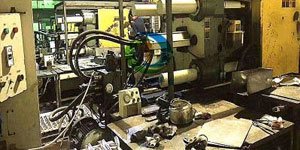
Contract manufacturer of die castings. Capabilities include cold chamber aluminum die casting parts from 0.15 lbs. to 6 lbs., quick change set up, and machining. Value-added services include polishing, vibrating, deburring, shot blasting, painting, plating, coating, assembly, and tooling. Materials worked with include alloys such as 360, 380, 383, and 413.
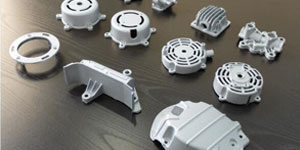
Zinc die casting design assistance/concurrent engineering services. Custom manufacturer of precision zinc die castings. Miniature castings, high pressure die castings, multi-slide mold castings, conventional mold castings, unit die and independent die castings and cavity sealed castings can be manufactured. Castings can be manufactured in lengths and widths up to 24 in. in +/-0.0005 in. tolerance.
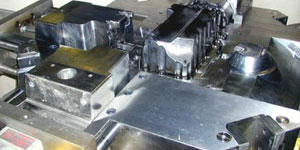
ISO 9001: 2015 certified manufacturer of die cast magnesium, Capabilities include high-pressure magnesium die casting up to 200 ton hot chamber & 3000 ton cold chamber, tooling design, polishing, molding, machining, powder & liquid painting, full QA with CMM capabilities, assembly, packaging & delivery.
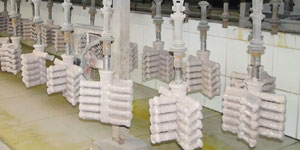
ITAF16949 certified. Additional Casting Service Include investment casting,sand casting,Gravity Casting, Lost Foam Casting,Centrifugal Casting,Vacuum Casting,Permanent Mold Casting,.Capabilities include EDI, engineering assistance, solid modeling and secondary processing.
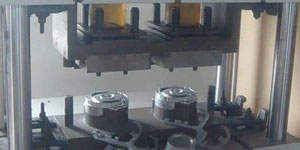
Casting Industries Parts Case Studies for: Cars, Bikes, Aircraft, Musical instruments, Watercraft, Optical devices, Sensors, Models, Electronic devices, Enclosures, Clocks, Machinery, Engines, Furniture, Jewelry, Jigs, Telecom, Lighting, Medical devices, Photographic devices, Robots, Sculptures, Sound equipment, Sporting equipment, Tooling, Toys and more.
What Can we help you do next?
∇ Go To Homepage For Die Casting China
→Casting Parts-Find out what we have done.
→Ralated Tips About Die Casting Services
By Minghe Die Casting Manufacturer |Categories: Helpful Articles |Material Tags: Aluminum Casting, Zinc Casting, Magnesium Casting, Titanium Casting, Stainless Steel Casting, Brass Casting,Bronze Casting,Casting Video,Company History,Aluminum Die Casting |Comments Off