The Advantages And Disadvantages Of Aluminum Casting Process
Due to the different elements of each group of aluminum alloys, the physical and chemical properties of the alloys are different. The crystallization process is also different. Therefore, it must be aimed at the characteristics of aluminum alloy. Reasonable choice of casting method. In order to prevent or reduce the occurrence of casting defects within the permitted range, so as to optimize the casting.
Aluminum Alloy Casting Process Performance
Aluminum alloy casting process performance. It is usually understood as a combination of those properties that are most prominent in the process of filling characteristics, crystallization and cooling, such as fluidity, shrinkage, air tightness, casting stress, and air absorption. These characteristics of aluminum alloy depend on the composition of the alloy. But it is also related to the casting factors, the complexity of the alloy heating temperature mold, the pouring riser system, and the gate shape.
(1) Liquidity
Fluidity refers to the ability of alloy liquid filling characteristics. The fluidity determines whether the alloy can cast complex castings. There are many factors that affect liquidity. The main factors are the composition, temperature, and solid particles of metal oxides, metal compounds and other pollutants in the alloy liquid, but the external objective factors are the pouring temperature and the flow pressure (commonly known as the condensed injection head).
(2) Contractility
Shrinkage is one of the main characteristics of cast aluminum alloys. The alloy is divided into three stages from liquid pouring to solidification until it reaches room temperature. They are liquid shrinkage, solidification shrinkage and solid state shrinkage. The shrinkage of the alloy has a decisive influence on the quality of the casting. It affects the size of the shrinkage cavity of the casting, the formation of stress cracks and the change of the size. The shrinkage of the rapid constant berkelium is divided into body shrinkage and linear shrinkage. In actual production, linear shrinkage is generally used to improve the shrinkage of gold alloys. Aluminum alloy shrinkage size. Usually expressed as a percentage, called shrinkage.
① body contraction
Body contraction includes liquid contraction and solidification contraction.
Casting alloy liquid from pouring to solidification. At the end of the solidification, there will be macroscopic or microscopic shrinkage in the Vietnamese side. This kind of macroscopic shrinkage caused by shrinkage is visible to the naked eye and is divided into concentrated shrinkage and partial shrinkage. The pore diameter of the concentrated shrinkage cavity is large and concentrated. And they are distributed in the top part of the casting or the thick hot spots on the surface. The dispersive shrinkage cavities are scattered and fine. Most of them are distributed in the casting axis and hot joints. The microscopic craters are difficult to see with the naked eye. Most of the microscopic shrinkage cavities are distributed under the grain boundaries or between the dendrites of the dendrites.
Shrinkage and porosity are one of the main defects of castings. The reason is that the liquid contraction is greater than the national contraction. During production, it is found that the casting aluminum alloy solidification range is smaller. The more crystals form Leizhong shrinkage cavities. Check the coagulation range. The more crystals form dispersive shrinkage cavities. therefore. In the design, the casting seam aluminum alloy must conform to the principle of sequential solidification. The body shrinkage of printed castings during liquid hand solidification should be supplemented by alloy liquid. Shrinkage cavities and looseness are concentrated in the outer riser of the casting. For aluminum alloy castings that are prone to be scattered and loose. The number of 100-port installations is more than that of centralized shrinkage holes. And set up a cold iron at the place where the crystals are generated to increase the local cooling rate. Make it solidify at the same time or quickly.
②Line shrinkage
The size of the line shrinkage will directly affect the quality of the casting. The system shrinks and invites big. The tendency of aluminum castings to produce cracks and stresses is also greater: the size and shape of the castings become larger after cooling.
For different cast aluminum alloys, there are different shrinkage rates of the joints, and the same alloy is printed. The casting is different. The shrinkage rate is also different. On the same casting. The shrinkage rate of its length, width and height is also different. It should be determined according to the specific situation.
(3) Hot cracking
The occurrence of hot cracks in aluminum castings is mainly due to the shrinkage stress of the castings exceeding the bonding force between the metal grains. Most of them occur along the grain boundaries. It can be seen from the crack fracture that the metal at the cracks is often oxidized and loses its metallic luster. The cracks extend along the grain boundary, with a zigzag shape, a wide surface and a narrow inside, and some penetrate the entire end surface of the casting.
Different aluminum alloy castings have different tendency to crack. This is because the greater the difference between the temperature at which a complete crystalline framework is formed during the solidification of the cast aluminum alloy and the solidification temperature, the greater the shrinkage of the alloy and the greater the tendency for hot cracking , Even the same type of alloy has different hot cracking tendency due to the resistance of the mold, the structure of the casting, the pouring process and other factors. Measures such as regressive casting molds or improved casting aluminum alloy casting systems are often used in production to avoid cracks in aluminum castings. The hot crack ring method is usually used to detect hot cracks in aluminum castings.
(4) Air tightness
The air-tightness of cast aluminum alloy refers to the degree of non-leakage of cavity-type aluminum castings under the action of high-pressure gas or liquid. The air-tightness actually characterizes the degree of compactness and purity of the internal structure of the casting.
The air-tightness of cast aluminum alloy is related to the properties of the alloy. The smaller the solidification range of the alloy, the smaller the tendency to produce porosity. At the same time, the smaller the precipitation pores, the higher the air-tightness of the alloy. The airtightness of the same cast aluminum alloy is also related to the casting process. For example, lowering the casting temperature of the cast aluminum alloy, placing cold iron to accelerate the cooling rate, and solidifying and crystallization under pressure, etc., can all make the airtightness of aluminum castings. improve. The impregnation method can also be used to plug the leakage gap to improve the air tightness of the casting.
(5) Casting stress
Casting stress includes three kinds of stress, phase transformation stress and shrinkage stress. The causes of various stresses are not the same.
The airtightness of cast aluminum alloy is related to the properties of the alloy. The smaller the alloy solidification range. The tendency to produce sulphur pine is also smaller. At the same time, it produces small stomata. Otherwise, the air tightness of the alloy will be high. The airtightness of the same cast aluminum alloy is also related to the casting inspection process. Such as lowering the casting temperature of cast aluminum alloy, placing cold iron to accelerate the cooling rate, and solidifying and crystallization under pressure, etc., can improve the air tightness of aluminum castings. The gas tightness of the casting can also be improved by plugging the gap of high leakage through the treatment method.
- Thermal stress. The thermal stress is due to the uneven section thickness at the intersection of the different geometric shapes of the casting. Cooling is not a few reasons. The formation of compressive stress in the thin part leads to residual stress in the casting.
- Intersecting stress. The phase transformation stress is due to the phase transformation of some cast aluminum alloys during the cooling process after solidification. The size of the zone at the end of the courtyard changes. The main member is aluminum. The wall thickness of the casting is uneven. It is caused by the intersection of different parts at different times.
- Shrinkage stress. When aluminum casting shrinks, it is hindered by the mold and core, resulting in tensile stress. This kind of stress is temporary, and aluminum castings will disappear automatically when they are out of the box. However, improper unpacking time often causes hot cracks, especially for metal cast aluminum alloys that are prone to hot cracks under such stress. The residual stress in the cast aluminum alloy reduces the mechanical properties of the alloy and affects the machining accuracy of the casting. Residual stress in aluminum castings can be eliminated by annealing. The alloy has good thermal conductivity and no phase change during the cooling process. As long as the casting structure is designed reasonably, the residual stress of the aluminum casting is generally small.
(6) Inhalation
Aluminum alloy is easy to absorb gas, which is the main characteristic of cast aluminum alloy. The hydrogen produced by the reaction between the components of liquid aluminum and aluminum alloys and the moisture contained in the furnace charge, organic matter combustion products, and molds is absorbed by the aluminum liquid.
The higher the temperature of the aluminum alloy melt, the more hydrogen is absorbed. At 700°C, the solubility of hydrogen in 100g of aluminum is 0.5 to 0.9. When the temperature rises to 850°C, the solubility of hydrogen increases by 2 to 3 times. When alkali metal impurities are contained, the solubility of hydrogen in molten aluminum is significantly increased.
In addition to the inhalation of cast aluminum alloy during smelting, it also produces inhalation when pouring into the mold. The liquid metal entering the mold decreases with the temperature, the solubility of the gas decreases, and excess gas is precipitated, and there is a part of the gas that cannot escape. It is left in the casting to form pores, which are usually called "pinholes". The gas sometimes combines with the shrinkage cavity, and the gas precipitated in the molten aluminum stays in the shrinkage cavity. If the pressure generated by the heating of the bubbles is large, the surface of the pores is smooth and there is a bright layer around the holes; if the pressure generated by the bubbles is small, the inner surface of the pores is wrinkled, which looks like "fly feet", and there are shrinkage holes on closer inspection. Characteristics.
The higher the argon content in the cast aluminum alloy liquid, the more pinholes produced in the casting. Pinholes in aluminum castings not only reduce the air tightness and corrosion resistance of the castings, but also reduce the mechanical properties of the alloy. To obtain aluminum castings with no or less pores, the key lies in the melting conditions. If a covering agent is added for protection during smelting, the amount of gas inhalation of the alloy is greatly reduced. Refining the molten aluminum can effectively control the hydrogen content in the molten aluminum. The casting method that uses sand, clay and other auxiliary materials to make a mold is called sand casting. The materials of sand molds are collectively referred to as molding materials. The sand molds for non-ferrous metal applications are made of sand, clay or other binders and water.
The forming process of aluminum castings is a process of interaction between metal and mold. After the aluminum alloy liquid is injected into the mold, the heat is transferred to the mold, and the sand mold is subjected to the thermal, mechanical, and chemical effects of the liquid metal. Therefore, in order to obtain high-quality castings, in addition to strictly mastering the smelting process, it is also necessary to correctly design the mold (core) sand ratio, modeling and pouring processes.
3. Metal Mold Casting
1. Introduction and technological process
Metal mold casting is also called hard mold casting or permanent mold casting. It is a method of pouring the melted aluminum alloy into a metal mold to obtain castings. Most of the aluminum alloy metal mold casting uses metal cores, but also sand cores or shell cores. Method, compared with pressure casting, aluminum alloy metal mold has a long service life.
2. Casting advantages
(1) Advantages
The metal mold has a faster cooling rate and a denser structure of the casting, which can be strengthened by heat treatment, and its mechanical properties are about 15% higher than that of sand casting. Metal mold casting, the quality of castings is stable, the surface roughness is better than sand casting, and the rate of waste crystal is low. The working conditions are good, the productivity is high, and the workers are easy to master.
(2) Disadvantages
The metal type has a large thermal conductivity and poor filling ability. The metal type itself has no air permeability. Corresponding measures must be taken to effectively exhaust. The metal mold has no retreat and is easy to crack and deform during solidification.
3. Common defects and prevention of metal castings
(1) Pinhole
Measures to prevent pinholes: It is strictly forbidden to use contaminated cast aluminum alloy materials, materials stained with organic compounds and severely oxidized and corroded; control the smelting process, strengthen degassing and refining; control the thickness of the metal type coating, too thick is easy to produce pinholes ; Mold temperature should not be too high, adopt chilling measures for thick wall parts of castings, such as copper inlay or watering, etc.; when using sand molds, strictly control moisture and try to use dry cores.
(2) Stoma
Measures to prevent pores: modify the unreasonable pouring and riser system to make the liquid flow stable and avoid the gas from being involved; the mold and core should be preheated, and then painted, and must be dried thoroughly before use; design the mold Adequate exhaust measures should be considered with the core.
(3) Oxidation and slag inclusion
Measures to prevent oxidation and slag inclusion: strictly control the smelting process, fast smelting, reduce oxidation, and remove slag thoroughly. A1- Mg alloy must be smelted under a covering agent; the furnace and tools should be clean, free of oxides, and should be preheated, and the coating should be dried for use after slowing down;
The designed pouring system must have stable flow, buffering and slag-skimming capabilities; the inclined pouring system is used to stabilize the liquid flow without secondary oxidation; the selected coating must have strong adhesion, and will not spall during the pouring process and enter the casting to form Slag.
(4) Thermal cracking
Measures to prevent thermal cracking: Local overheating should be avoided in the actual pouring system to reduce internal stress; the inclination of the mold and core must be above 2°, and the pouring riser can be core-pulled to open the mold once it has solidified, and sand cores can be used if necessary Replace the metal core; control the thickness of the coating to make the cooling rate of each part of the casting consistent; choose the appropriate mold temperature according to the thickness of the casting; refine the alloy structure to improve the hot cracking ability; improve the casting structure to eliminate sharp corners and wall thickness mutations, Reduce hot cracking tendency.
(5) Loose
Measures to prevent porosity: reasonable riser settings to ensure solidification and feeding capacity; appropriately lower the working temperature of the metal mold; control the thickness of the coating and reduce the thickness of the thick wall; adjust the cooling rate of each part of the metal mold to make The thick wall of the casting has a greater stimulating ability; appropriately reduce the metal pouring temperature.
Related Pages: Aluminum Casting
Related Articles:
- Metal Oxide Film Influence On The Quality Of Aluminum Alloy Castings
- The Application Of Aluminum Alloy Casting In Automobile
Please keep the source and address of this article for reprinting:The Advantages And Disadvantages Of Aluminum Casting Process
Minghe Die Casting Company are dedicated to manufacture and provide quality and high performance Casting Parts(metal die casting parts range mainly include Thin-Wall Die Casting,Hot Chamber Die Casting,Cold Chamber Die Casting),Round Service(Die Casting Service,Cnc Machining,Mold Making,Surface Treatment).Any custom Aluminum die casting, magnesium or Zamak/zinc die casting and other castings requirements are welcome to contact us.
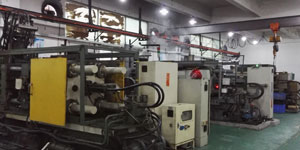
Under the control of ISO9001 and TS 16949,All processes are carried out through hundreds of advanced die casting machines, 5-axis machines, and other facilities, ranging from blasters to Ultra Sonic washing machines.Minghe not only has advanced equipment but also have professional team of experienced engineers,operators and inspectors to make the customer’s design come true.
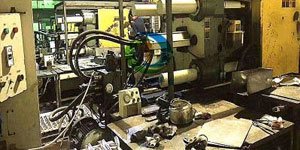
Contract manufacturer of die castings. Capabilities include cold chamber aluminum die casting parts from 0.15 lbs. to 6 lbs., quick change set up, and machining. Value-added services include polishing, vibrating, deburring, shot blasting, painting, plating, coating, assembly, and tooling. Materials worked with include alloys such as 360, 380, 383, and 413.
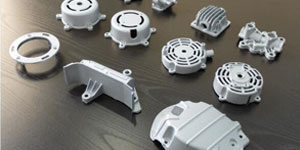
Zinc die casting design assistance/concurrent engineering services. Custom manufacturer of precision zinc die castings. Miniature castings, high pressure die castings, multi-slide mold castings, conventional mold castings, unit die and independent die castings and cavity sealed castings can be manufactured. Castings can be manufactured in lengths and widths up to 24 in. in +/-0.0005 in. tolerance.
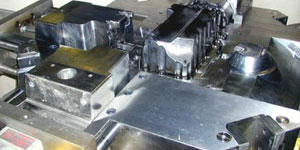
ISO 9001: 2015 certified manufacturer of die cast magnesium, Capabilities include high-pressure magnesium die casting up to 200 ton hot chamber & 3000 ton cold chamber, tooling design, polishing, molding, machining, powder & liquid painting, full QA with CMM capabilities, assembly, packaging & delivery.
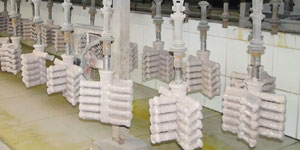
ITAF16949 certified. Additional Casting Service Include investment casting,sand casting,Gravity Casting, Lost Foam Casting,Centrifugal Casting,Vacuum Casting,Permanent Mold Casting,.Capabilities include EDI, engineering assistance, solid modeling and secondary processing.
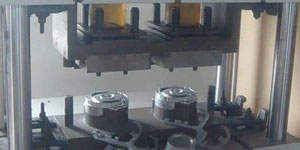
Casting Industries Parts Case Studies for: Cars, Bikes, Aircraft, Musical instruments, Watercraft, Optical devices, Sensors, Models, Electronic devices, Enclosures, Clocks, Machinery, Engines, Furniture, Jewelry, Jigs, Telecom, Lighting, Medical devices, Photographic devices, Robots, Sculptures, Sound equipment, Sporting equipment, Tooling, Toys and more.
What Can we help you do next?
∇ Go To Homepage For Die Casting China
→Casting Parts-Find out what we have done.
→Ralated Tips About Die Casting Services
By Minghe Die Casting Manufacturer |Categories: Helpful Articles |Material Tags: Aluminum Casting, Zinc Casting, Magnesium Casting, Titanium Casting, Stainless Steel Casting, Brass Casting,Bronze Casting,Casting Video,Company History,Aluminum Die Casting |Comments Off