The Process Application And Research of Resin Sand Casting Method
With the upgrading of the product quality of my country's machinery industry and the increase in the demand for castings in the world, more and more companies (or enterprises) in China choose to switch from clay sand dry casting process to self-hardening resin. Sand casting process. Compared with the clay sand dry casting process, the self-hardening resin sand casting process has the following advantages: good casting surface quality, high dimensional accuracy, low rejection rate, wide application range, low technical requirements for workers, and greatly reduces workers’ burden. Labor intensity and improve the working environment.
But its disadvantage is that the casting cost is relatively high. In order to reduce the casting cost, all casting production units are exploring ways to reduce the casting cost.
A company established a new self-hardening resin sand production line with an annual output of 3,000 tons of iron castings in 2002. After more than four years of continuous exploration, we believe that to reduce the cost of resin sand casting, we can reduce the cost of resin sand casting from several aspects such as equipment, raw materials, production technology, etc. consider.
Choose the right self-hardening resin sand production equipment
Choosing appropriate self-setting resin sand production equipment is a prerequisite for reducing resin sand casting costs. When selecting resin sand production equipment, not only should the actual situation of the enterprise be considered, the equipment at the appropriate price should be selected, and the operating cost of the equipment should be considered. Consider the following:
- Pay attention to the selection of dust removal equipment. When selecting production equipment, most companies tend to pay more attention to the quality of sand mixing equipment and recycling equipment, while ignoring the quality of dust removal equipment. In fact, the quality of the dust removal equipment directly affects the quality and cost of the reclaimed sand. If the dust removal effect of the dust removal equipment is not good, it will not only affect the working environment and pollute the air, but more importantly, affect the fine powder content of the reclaimed sand. The result is an increase in production costs due to the increase in the amount of resin added during sand mixing.
- The reliability of the equipment and its maintenance costs should be considered. The processing methods, assembly level and equipment configuration level of the equipment manufacturer determine the reliability of the equipment produced by it. If the reliability of the equipment is poor, the probability of equipment failure is high. Replacement The number of equipment parts increases and the utilization rate of equipment decreases. This not only increases the workload of maintenance workers and increases equipment maintenance costs, but also reduces production efficiency and increases production costs.
- Consider the energy consumption of the equipment. On the premise of meeting the technological requirements, try to reduce the installed capacity, avoid the phenomenon of large horse-drawn carts, make full use of inherent resources, reduce unnecessary energy waste, and achieve full equipment utilization and maximum energy utilization To increase corporate and social benefits.
Develop a correct and reasonable production process
The formulation of a correct and reasonable production process is the key to reducing the cost of resin sand casting. Whether the formulation of the production process is reasonable or not directly affects the yield, casting quality and casting cost of castings. When formulating the production process, the following items should be determined:
1. Determine the LOI value of suitable reclaimed sand
LOI value, i.e. ignition loss, is an important index to measure the release rate of reclaimed sand, and it is also an index closely related to the amount of gas evolution of molding sand and the occurrence of pore defects in castings. Cast iron parts are generally produced with furan resin sand. Practice has proved that LOI value control About 3% can fully meet the production requirements, and some companies require the LOI value to be controlled below 2.5%. To achieve this goal, it is necessary to increase equipment, or increase the number of sand regeneration, or add more new sand. This is undoubtedly Will increase equipment investment and regeneration costs and raw material costs. During the production process, our company gradually relaxed the LOI value control index from about 3% to about 4%. Due to proper technology and management, the quality index of castings was not affected by the change of LOI value.
2. Determine the appropriate casting process parameters
- Determining the appropriate final strength Generally, after resin sand is mixed, the highest strength, the final strength, can be reached after about 24 hours of self-hardening. Due to the different production conditions and production scales of various enterprises, the time interval from modeling to pouring does not necessarily exceed 24 hours, so the final strength should be determined by the enterprise. For small-scale enterprises that implement a furnace system for a few days, the 24-hour final strength standard can be used; for those that do not exceed the 24-hour mold curing time, the final strength standard is the strength achieved before pouring. At the same time, there are two tendencies to overcome in production: on the one hand, blindly increase the strength to ensure the quality, which increases the cost of casting and cause waste; on the other hand, the strength is reduced to ensure the cost, resulting in unstable quality and fluctuation range. Large, so that the quality of castings is greatly affected by raw materials and operators. Each enterprise should determine the appropriate final strength according to its own situation, so as to save the resin and curing agent to the greatest extent and reduce the casting cost while ensuring the quality of the casting.
- Determine the appropriate sand-iron ratio. Since the self-hardening resin sand has high strength, mold release after curing, and smooth parting surface, its sand consumption is smaller than that of clay sand, but its sand-to-iron ratio also has certain requirements. If the casting sand-to-iron ratio is too high, both resin and curing agent will be wasted during the production process, and large waste sand blocks will be produced, which will increase the burden on the reclaimer, reduce the release rate, increase the LOI value, and increase the possibility of porosity in the casting. Large; if the sand-to-iron ratio is too low, it is easy to run out of fire during pouring, and the casting is easy to deform. According to our experience, the sand to iron ratio should be chosen to be 2.2~3:1.
- Determining the appropriate molding process The yield rate of castings directly affects the casting cost. The appropriate molding process can not only ensure the quality of the castings, but also reduce the casting cost. Reducing the casting reject rate is the most obvious and direct measure to reduce the casting cost. one. When determining the molding process, try to make a special sand box with more pores on the wall of the box. The model is made as a real sample, and the template is modeled. The pouring system uses ceramic tubes and the inner gate adopts multiple and dispersed, and the paint is evenly applied and not missed. Set up air outlet to ensure smooth core exhaust
The correct selection of raw materials is the basis for reducing the cost of resin sand casting.
The choice of raw materials has a greater impact on the cost of casting, which has been recognized by the vast majority of peers, because the quality of raw materials affects the addition and consumption of various materials on the one hand, and on the other hand affects the casting cost. Quality Index.
- The choice of raw sand. Raw sand is divided into ordinary sand, water-washed sand, scrubbing sand, etc. Since the mud content in scrubbing sand is already very small, it can greatly reduce the waste of resin. It should be selected first, followed by water-washed sand. But never use untreated raw sand. The price of scrubbing sand itself is not high, generally 50 yuan/t to 70 yuan/t, but the freight is relatively high. For example, if our company buys scrubbing sand from a sand factory in Dalin for 65 yuan/t, but it is shipped to the company, the total cost It is 280 yuan/t. When choosing molding sand, one must follow the principle of nearby selection, so that on the one hand, it can reduce expensive freight, and on the other hand, it can guarantee the supply without affecting production. Second, try to choose raw sand with low angle coefficient. At the same time, due to the different technical level and equipment level of each scrubbing sand production enterprise, the quality of the scrubbing sand produced is also different. Therefore, if conditions permit, when determining the use of sand, the scrubbing sand production enterprise should be inspected and inspected. Technical status, equipment status and sand source status, etc., and discover the other party’s sand quality control results. In short, in the process of selecting raw sand, it is best to pass tests and comparisons, refer to other aspects of the problem, and under the premise of ensuring production and quality, minimize the production cost.
- The choice of resin The price of resin is more expensive, generally around 10,000 yuan/t, so it has a greater impact on the casting cost. At the same time, due to the uneven production equipment of the manufacturer, the quality of the resin produced is also quite different. If a poor quality resin is selected, it will affect the quality of the molding sand, increase casting waste, and increase the amount of resin added. The direct result will increase the casting cost. Therefore, the choice of raw materials cannot be based on the manufacturer. The technical data provided is determined, and the manufacturer’s production equipment, production process and quality control methods should be understood, and the various indicators of the resin should be inspected as much as possible, or the relevant reputable inspection department should be invited to conduct the inspection, or Use the experience of similar manufacturers for reference, or choose products from well-known large companies with good reputation. Since the beginning of production, our company has been using the resin produced by Jinan Shengquan Group. Due to its good resin quality and stable performance, although its price is higher than that of some enterprises, its addition amount is less and the production process is stable. The actual production cost is also not high.
- Selection of other raw materials Other raw materials include curing agents, coatings, adhesives, mold release agents, sealing mud sticks, etc. The impact of these raw materials on the quality of castings is not the main one, but the impact on casting costs cannot be ignored, such as The difference in the amount of curing agent added not only affects the production cost due to the production efficiency of the modeling process, but also affects the material cost. Therefore, the selection principle of other raw materials is not only to consider their quality issues, but also to consider their matching with the main materials, such as procurement and transportation convenience. In short, as long as the equipment selection is reasonable, the performance is reliable, the operation is normal, the raw material selection is matched, the quality is stable, the supply is timely, the production process parameters are set reasonably, the tooling and equipment are guaranteed, the self-hardening resin sand casting can control and reduce the casting cost, and bring it to the enterprise Development and efficiency.
Please keep the source and address of this article for reprinting:The Process Application And Research of Resin Sand Casting Method
Minghe Die Casting Company are dedicated to manufacture and provide quality and high performance Casting Parts(metal die casting parts range mainly include Thin-Wall Die Casting,Hot Chamber Die Casting,Cold Chamber Die Casting),Round Service(Die Casting Service,Cnc Machining,Mold Making,Surface Treatment).Any custom Aluminum die casting, magnesium or Zamak/zinc die casting and other castings requirements are welcome to contact us.
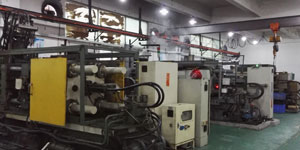
Under the control of ISO9001 and TS 16949,All processes are carried out through hundreds of advanced die casting machines, 5-axis machines, and other facilities, ranging from blasters to Ultra Sonic washing machines.Minghe not only has advanced equipment but also have professional team of experienced engineers,operators and inspectors to make the customer’s design come true.
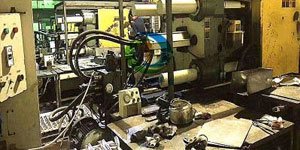
Contract manufacturer of die castings. Capabilities include cold chamber aluminum die casting parts from 0.15 lbs. to 6 lbs., quick change set up, and machining. Value-added services include polishing, vibrating, deburring, shot blasting, painting, plating, coating, assembly, and tooling. Materials worked with include alloys such as 360, 380, 383, and 413.
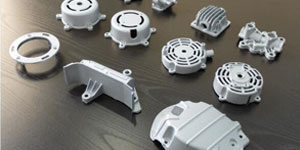
Zinc die casting design assistance/concurrent engineering services. Custom manufacturer of precision zinc die castings. Miniature castings, high pressure die castings, multi-slide mold castings, conventional mold castings, unit die and independent die castings and cavity sealed castings can be manufactured. Castings can be manufactured in lengths and widths up to 24 in. in +/-0.0005 in. tolerance.
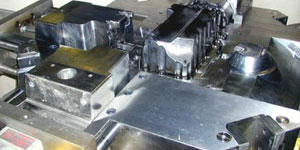
ISO 9001: 2015 certified manufacturer of die cast magnesium, Capabilities include high-pressure magnesium die casting up to 200 ton hot chamber & 3000 ton cold chamber, tooling design, polishing, molding, machining, powder & liquid painting, full QA with CMM capabilities, assembly, packaging & delivery.
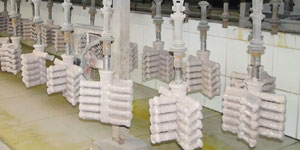
ITAF16949 certified. Additional Casting Service Include investment casting,sand casting,Gravity Casting, Lost Foam Casting,Centrifugal Casting,Vacuum Casting,Permanent Mold Casting,.Capabilities include EDI, engineering assistance, solid modeling and secondary processing.
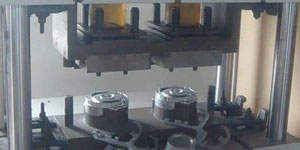
Casting Industries Parts Case Studies for: Cars, Bikes, Aircraft, Musical instruments, Watercraft, Optical devices, Sensors, Models, Electronic devices, Enclosures, Clocks, Machinery, Engines, Furniture, Jewelry, Jigs, Telecom, Lighting, Medical devices, Photographic devices, Robots, Sculptures, Sound equipment, Sporting equipment, Tooling, Toys and more.
What Can we help you do next?
∇ Go To Homepage For Die Casting China
→Casting Parts-Find out what we have done.
→Ralated Tips About Die Casting Services
By Minghe Die Casting Manufacturer |Categories: Helpful Articles |Material Tags: Aluminum Casting, Zinc Casting, Magnesium Casting, Titanium Casting, Stainless Steel Casting, Brass Casting,Bronze Casting,Casting Video,Company History,Aluminum Die Casting |Comments Off