Feeding Wire Method Ductile Iron Treatment Process
Through actual production, the punching method and the feeding method are used to produce ductile iron, and the characteristics of the two processes are analyzed. Through the comparison, the comprehensive performance of the castings produced by the feeding method is more stable than that of the punching method; and the feeding process is spheroidized. To share some of the experiences in it.
1. Overview
As we all know, the axle is an important load-bearing part of the vehicle, and it is directly related to the safety of the vehicle. The axle housing is one of the key components of the axle. The performance of the axle housing material directly determines the load-carrying capacity of the vehicle. At present, the axle housings in the heavy truck industry are generally divided into two categories: stamped and welded axle housings and cast axle housings, and cast axle housings can be divided into cast steel axle housings and cast iron axle housings.
The cast axle housing has always occupied the main position of the heavy truck axle housing due to its high load-bearing weight and low production cost. Due to the harsh working environment of the axle housing and long-term work under dynamic load, this requires high requirements for the material properties of the axle housing. While ensuring the strength, it also needs to obtain higher plasticity and toughness to adapt to the axle housing. Work characteristics.
We know that for nodular cast iron, the spheroidizing process is a key link in the production of nodular cast iron, and the quality of the spheroidizing treatment directly affects the quality of the nodular cast iron. At the beginning, the spheroidizing process we used was the spheroidizing process of rush-in method. Although this method is simple and easy to operate, it has many shortcomings, such as: low alloy yield; large smoke and poor working environment; reaction The amount of slag produced at the time is large; the treatment effect is easily affected by external factors, which leads to fluctuations in the quality of castings and often unqualified spheroidization. These quality fluctuations will affect the performance of the axle housing and even affect the safety of the vehicle.
The wire feeding method spheroidizing treatment process was applied to the production of cast iron. It started in the 1980s abroad. Although the domestic production of nodular cast iron started to apply this technology late, the technology has been popularized and used quickly in the country, and it is useful for improving the production of nodular graphite. The stability effect of cast iron quality is obvious.
2. Feeding wire spheroidizing process
The basic principle of the thread feeding spheroidizing process is to wrap a certain composition of powdered spheroidizing agent and inoculant through the steel skin, and send it into the spheroidizing treatment package at a certain speed through the equipment, so that the spheroidizing at the bottom of the package will detonate. To achieve the purpose of spheroidization inoculation treatment.
At present, the wire-feeding spheroidizing process we adopt is: adjust the chemical composition to the process requirements, heat up to 1510-1520℃ and let stand still, the tapping temperature is 1480~1500℃, the iron output is 2t, and the spheroidizing treatment temperature is 1420~1450℃. The pouring temperature is 1370~1380℃. The inoculation rate with the flow is 0.1%.
The length of the spheroidizing line is 39-46m, adjusted according to the sulfur content of the original molten iron. The higher the sulfur content, the longer the spheroidizing line needs to be added, and vice versa. The length of the inoculation line is 32m.
3. The spheroidizing process of feeding wire improves the quality of castings
After more than a year of production, the quality of our axle housings has been significantly improved compared to before. Especially the stability of composition, metallography and mechanical properties has been greatly improved.
Comparison of metallographic structure Select the same position of the casting to polish and observe the metallographic structure. The metallographic picture taken is shown in Figure 2. Compared with the punching method, the graphite balls of the casting produced by the feeding method are more and thinner, and the roundness is better.
4. Advantages of feeding thread spheroidization process
According to our actual production comparison, the thread-feeding spheroidizing process has many advantages over the spheroidizing process of the punching method.
- Improvement of the on-site production environment. When the spheroidizing agent reacts with the molten iron, a large amount of smoke and strong light are generated, which makes the on-site working environment worse; when the wire feeding method is used for spheroidization, the processing station There is a cover to cover the spheroidization bag, and the cover is connected to the dust removal system of the processing station, so that the smoke is processed by the dust removal system instead of being directly released in the workshop.
- The amount of alloy added is reduced, and the production cost is reduced. After calculation, the processing of 1t of molten iron feeding method can save about 78 yuan in raw material cost than the impulse method. According to the annual production capacity of 10,000 tons of ductile iron axle housing of our factory, the annual saving is The cost is 780,000 yuan and the benefits are considerable.
- Realize job automation and reduce the labor intensity of workers. When the spheroidization process is carried out, the workers’ preliminary preparations are cumbersome, including weighing the spheroidizing agent and inoculant, adding the spheroidizing agent and inoculant to the bag, and Tamping and covering operations are required; the adding amount of the spheroidizing and inoculating lines of the thread feeding method is automatically added through the control cabinet, which reduces a lot of work.
- The quality of spheroidization is stable and the spheroidization effect is better. According to statistics, since the use of thread-feeding spheroidization process in 2013, the spheroidization pass rate is over 99.5%, while the pass rate of the spheroidization process is only 95. %.
5. How to correctly choose the process parameters of feeding thread spheroidization
In actual production, how to correctly select the parameters of the wire feeding process requires a certain number of tests to verify. We have undergone many process adjustments from the beginning of the organization of the test to the formal mass production. The following will share our experience with colleagues.
To correctly select the process parameters of feeding thread spheroidization, you need to pay attention to the following aspects:
- (1) The choice of cored wire Some foreign experience does not recommend the use of high Mg cored wire. The Mg content is too high, the spheroidization reaction is intense, the Mg burns a lot, and the amount of slag is large. Generally, it is recommended to select Mg content of about 30%, and use Ba-containing inoculation thread, which can effectively prevent inoculation decline. The main parameters of the cored wire used by our company are: the thickness of the outer steel sheath is 0.4mm, and the diameter of the core wire is 13mm. Before use, check that the appearance of the cored wire should be round and free of cracks, powder leakage, etc.In actual production, it is necessary to adjust according to the treatment temperature and the height of the molten iron. Generally, the higher the treatment temperature, the higher the height of the molten iron, and the faster the wire feeding speed. In addition. Some materials have also introduced a convenient and feasible method of measuring the optimal wire feeding speed: first measure the height of the molten iron in the processing bag, and then manually feed the wire machine so that the core wire just touches the liquid surface, then clear the counter , The manual wire feeding machine performs wire feeding. When you hear the "boom" response sound, check the feeding length immediately. If this length is basically equal to the height of the molten iron, the speed should be appropriate. After verification, we selected the feeding speed of 30m/min.
- Selection of thread feeding amount The appropriate thread feeding amount is to feed the least cored thread under the premise of ensuring the spheroidization effect. The amount of wire feeding should be determined according to the processing volume of the molten iron, the processing temperature, and the sulfur content of the molten iron. According to our original molten iron sulfur content and product process requirements, combined with experimental verification, under the condition of ensuring the residual magnesium content, the length of the spheroidizing line is 39-46m, and the length of the inoculation line is 32m.
- The choice of processing temperature The processing temperature should be reduced as much as possible under the premise of ensuring the pouring temperature. The lower the processing temperature, the higher the absorption rate of magnesium and the less the consumption of cored wire. According to actual production testing, the time from the beginning of the spheroidizing treatment to the beginning of pouring is 4 to 5 minutes, during which the temperature drop is 40 to 50°C, and the spheroidizing reaction time is 80 to 90 seconds. Since the spheroidizing process needs to be turned over, we set the processing temperature at 1410~1450℃, the upper limit is taken when the room temperature is lower than 5℃, and the lower limit when the room temperature is higher than 25℃.
- Selection of residual magnesium content in molten iron after treatment. The residual magnesium content should be set aside for a certain amount of magnesium content according to the characteristics of the casting itself. At first, we controlled the residual magnesium content to 0.03% to 0.06%, but after actual production verification, it is more appropriate to control the residual magnesium content to 0.05% to 0.06%, because we found that when the residual magnesium is less than 0.04%, its graphite The roundness of the ball is slightly worse. When it is higher than 0.07%, cementite is prone to appear, and the shrinkage tendency of the molten iron becomes larger.
- Solving the problem of wire jamming during use The wire jam phenomenon will occur during the conveying process of the cored wire, which will cause the entire pack of molten iron to be scrapped. To this end, we have taken the following measures: one is to install a steel ring above the cored wire reel, as shown in Figure 5, which can reduce the bending of the core wire and make it smoothly enter the guide mechanism; the second is to connect the two coils When welding, after welding, polish away the larger bumps to prevent the wire from jamming during the conveying process; thirdly, avoid the bends of diameter less than 1m in the conveying pipeline or route of the cored wire to prevent the cored wire from being transported Powder leakage or jamming occurred during the process
6 Conclusion
- Feeding wire method spheroidizing process has low alloy addition amount, high Mg absorption rate, and can effectively reduce smoke and strong light pollution in the workshop, creating good economic and environmental benefits for foundry enterprises.
- The thread feeding method spheroidization process can effectively reduce the spheroidization failure rate, improve the quality of nodular cast iron, improve its comprehensive mechanical properties, and enhance the market competitiveness of the enterprise.
- Each foundry should select the appropriate process parameters for wire spheroidization according to its own production conditions and product process requirements, combined with the production experience of the peers.
Feed line spheroidizing process can significantly improve the stability of the quality of nodular cast iron, reduce production costs, improve the production environment, and reduce the labor intensity of workers. This is the recent development trend of the spheroidizing process.
Please keep the source and address of this article for reprinting: Feeding Wire Method Ductile Iron Treatment Process
Minghe Die Casting Company are dedicated to manufacture and provide quality and high performance Casting Parts(metal die casting parts range mainly include Thin-Wall Die Casting,Hot Chamber Die Casting,Cold Chamber Die Casting),Round Service(Die Casting Service,Cnc Machining,Mold Making,Surface Treatment).Any custom Aluminum die casting, magnesium or Zamak/zinc die casting and other castings requirements are welcome to contact us.
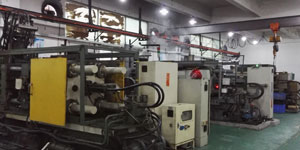
Under the control of ISO9001 and TS 16949,All processes are carried out through hundreds of advanced die casting machines, 5-axis machines, and other facilities, ranging from blasters to Ultra Sonic washing machines.Minghe not only has advanced equipment but also have professional team of experienced engineers,operators and inspectors to make the customer’s design come true.
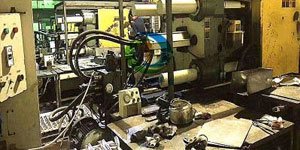
Contract manufacturer of die castings. Capabilities include cold chamber aluminum die casting parts from 0.15 lbs. to 6 lbs., quick change set up, and machining. Value-added services include polishing, vibrating, deburring, shot blasting, painting, plating, coating, assembly, and tooling. Materials worked with include alloys such as 360, 380, 383, and 413.
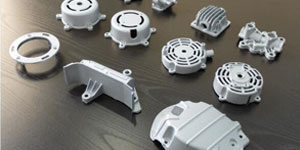
Zinc die casting design assistance/concurrent engineering services. Custom manufacturer of precision zinc die castings. Miniature castings, high pressure die castings, multi-slide mold castings, conventional mold castings, unit die and independent die castings and cavity sealed castings can be manufactured. Castings can be manufactured in lengths and widths up to 24 in. in +/-0.0005 in. tolerance.
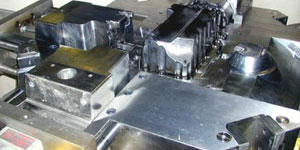
ISO 9001: 2015 certified manufacturer of die cast magnesium, Capabilities include high-pressure magnesium die casting up to 200 ton hot chamber & 3000 ton cold chamber, tooling design, polishing, molding, machining, powder & liquid painting, full QA with CMM capabilities, assembly, packaging & delivery.
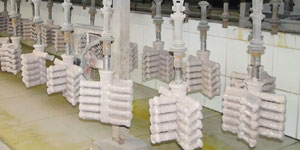
ITAF16949 certified. Additional Casting Service Include investment casting,sand casting,Gravity Casting, Lost Foam Casting,Centrifugal Casting,Vacuum Casting,Permanent Mold Casting,.Capabilities include EDI, engineering assistance, solid modeling and secondary processing.
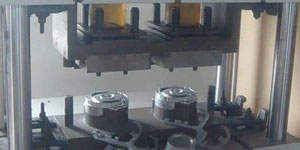
Casting Industries Parts Case Studies for: Cars, Bikes, Aircraft, Musical instruments, Watercraft, Optical devices, Sensors, Models, Electronic devices, Enclosures, Clocks, Machinery, Engines, Furniture, Jewelry, Jigs, Telecom, Lighting, Medical devices, Photographic devices, Robots, Sculptures, Sound equipment, Sporting equipment, Tooling, Toys and more.
What Can we help you do next?
∇ Go To Homepage For Die Casting China
→Casting Parts-Find out what we have done.
→Ralated Tips About Die Casting Services
By Minghe Die Casting Manufacturer |Categories: Helpful Articles |Material Tags: Aluminum Casting, Zinc Casting, Magnesium Casting, Titanium Casting, Stainless Steel Casting, Brass Casting,Bronze Casting,Casting Video,Company History,Aluminum Die Casting |Comments Off