Comprehensive Diagnosis And Control Of Automobile Aluminum Die Castings Quality
The comprehensive diagnosis and control of the quality of automotive aluminum alloy die castings are analyzed and researched, and the following drawbacks and defects are found. For automobile aluminum alloy die-casting parts, the automobile cylinder has a relatively large link, especially the head cover position of the cylinder block takes up a large space and the structure is more complicated. Some parts of the processed links and cylinder surface must not have holes and holes, which seriously affects the quality of die castings. Secondly, due to externally purchased components and materials, operating malpractice, etc., it also brings quality impacts to automotive die-casting parts. In order to improve the quality of automotive die-casting parts, it is necessary to increase the degree of attention to the above-mentioned drawbacks, and improve the process design links and hole drawbacks.
1 Comprehensive diagnosis and control of the quality of automotive aluminum alloy die castings
1.1 Description of diagnosis defects
For automobile aluminum alloy die-casting parts as a whole, the links of the automobile cylinder part are relatively large, especially the position of the head cover of the cylinder body occupies a large space and the structure is relatively complicated. Some parts of the processed links and cylinder surface cannot be caused by the existence of holes and holes. For those cylinder surfaces that allow holes and holes to exist, the distribution of holes and holes is more diffuse, and there are strict specifications and requirements for the size. For the cylinder head link, the camshaft position is accompanied by flaw detection. After processing, the size of the hole must meet the monitoring requirements and meet the minimum monitoring standards. For this type of component, it brings great difficulty to the design and production work, and seriously affects the design efficiency and production efficiency. The technology and process of castings cannot fully take into account the different links and positions of the entire castings, and it is less compatible with production links and process design links. Some larvae walls are accompanied by smooth features, and the depth of the larvae walls is large, accompanied by air-pollution problems. Secondly, there are also some disadvantages such as pores linking air cavities and shrinkage cavities.
1.2 Process comprehensive diagnosis and analysis and image simulation analysis
Externally purchased components and materials, operating malpractices, process design mitigation, and the practical applicability of mechanical devices, etc., all have a great impact on the safety of automobile castings, leading to quality changes, and severe cases will lead to casting scraps. The above-mentioned factors all have the characteristics of variability, and thus have a greater impact on the quality of castings. Any change in any link will bring fluctuations in the quality of castings. It is not easy to find the main reasons for the changes in casting quality brought about by externally purchased components and materials, operational malpractices, process design mitigation, and the practical applicability of mechanical devices. Faced with this situation, it is necessary to increase continuous tracking and investigation of casting design and process links. First of all, we must observe and analyze the production dates of different castings, establish a rationalized timing arrangement, establish the quality of the castings as the guiding goal, and monitor and continue to observe the following mitigation. Including the comprehensive monitoring and tracking of casting raw materials, auxiliary materials, smelting links, casting design and process production parameters, casting quality monitoring and other links [21. For image simulation analysis, the main defects of castings are reflected in the gear chamber. The main influencing factors of this defect are the influence of gas changes and shrinkage, which brings great defects to the holes. For castings, the gas produced is mainly obtained from the inside of the melt and the gas obtained from the release agent. Unexpected gas from the casting process. The gas produced in the solution is closely related to the type and properties of the casting material, and is closely related to the smelting technology of the casting.
2 Optimization and improvement measures
2.1 Image simulation management and improvement
For castings, the gas produced is mainly obtained from the inside of the melt and the gas obtained from the release agent. Unexpected gas from the casting process. The gas generated in the solution is closely related to the type and properties of the casting material, and is closely related to the smelting technology of the casting [41. The gas generated by the release agent is closely related to the selection of the casting process design link and the casting's pressing link model. For this shortcoming in the development of castings, the use of adjustments to casting smelting technology and the adjustment of spraying technology can be used to improve and optimize. There is a close relationship between the gas disadvantages brought by the castings in the pressing process and the operation form of the liquid metal. The drawbacks of the expansion and contraction of the casting are closely related to the temperature and solidification of the casting. After clarifying the design plan of the casting, you can expand the design and configuration of the runner, set the exhaust line and overflow equipment, set the temperature of the casting mold, and set the coefficient of the press. When designing and configuring the coefficients and parameters of the compression parts, the flow form of the liquid metal in the casting body should be considered, the solidification of the liquid should be considered, the shrinkage cavity value should be minimized, and the limit should be minimized. Furthermore, image simulation can be used for analysis in this link. The method of image simulation is the main method to analyze the law of castings and understand its filling shape at present, and provide scientific basis for the reason of the defects of castings. Change the timing model and present it in a triangular form, and then give the simulation system of its technology and process, and distinguish the format of the STL file. After the identification, use Msgmasoft software to start the division of the network. Give it a hundred thousand network nodes with castings and pouring systems. After in-depth research and analysis of Msg-masoft software, and its practical application, it is found that the use of Msgmasoft software has practical applicability, which can reform and innovate casting process molds, and lay a theoretical foundation for the design of casting molds and processes. .
2.2 Increase the management of dissolved gases
When the timing gear is in the smelting operation, the charge out of the gear chamber includes 50% of the aluminum deposit and 39% of the furnace. Because the moisture and some other substances will continue to increase during the re-furnace operation, which will increase the gas content, and then the material should be treated and managed in time to reduce the melt element content and add and remove it before the material is put into the furnace. For gas and liquid, the monitoring and observation of gas content has been increased. At the same time, the process should be changed and optimized, the injection technology should be improved, and the injection line should be adjusted to ensure efficient degassing operations and improve degassing efficiency. Ensure that the gas content of one hundred grams of aluminum material is around 0.2ml.
2_3 Increase the rationality of process parameters and optimize casting conditions
Regarding the rationality of the process parameters, first of all, according to the monitoring results, the process parameters and quality relationships that can affect the castings should be analyzed and studied, and the quality of the castings can be increased without changing the casting conditions. In order to ensure the rationality of the process parameters, the injection process can be used to increase the compactness of the castings, the pressure of the filling gas in the process, etc., to increase the rationality of the casting process. Secondly, it is necessary to increase the degree of attention to the casting conditions, ensure the rational operation of the process, increase the degree of attention to the holes, adjust the size of the runner, and add an exhaust pipe in the liquid junction. In the actual production and design activities of castings, it is necessary to increase the observation of casting holes to see if there are defects and drawbacks, and to observe their size and spread range. This observation of castings is mainly to monitor the actual applicability of the castings to see if they need to be scrapped and updated. Intercept the defective links of castings and reprocess the defective parts to ensure that they meet the requirements of standard castings and increase their practical applicability. For the finished castings, pay attention to the observation of the hole wall to see if the hole wall is rough. For the rougher hole wall, it mainly shows the nature of tree branches. When using a microscope for observation and analysis, the bottom can be found The continuity is better, accompanied by the shrinking and loosening of the larvae.
3 concluding remarks
To manage the quality defects of automotive aluminum alloy die castings, we must first increase the management of the dissolved gas, change and optimize the process, increase the rationality of the process parameters, optimize the casting conditions, monitor and observe the castings to see if they need to be Scrap and update. Reprocess the defective parts to ensure that they meet the requirements of standard castings. For image simulation and analysis of the main defects of timing properties of castings, you can use the adjustment of the casting smelting technology and the adjustment of the spraying technology.
Please keep the source and address of this article for reprinting:Comprehensive Diagnosis And Control Of Automobile Aluminum Die Castings Quality
Minghe Die Casting Company are dedicated to manufacture and provide quality and high performance Casting Parts(metal die casting parts range mainly include Thin-Wall Die Casting,Hot Chamber Die Casting,Cold Chamber Die Casting),Round Service(Die Casting Service,Cnc Machining,Mold Making,Surface Treatment).Any custom Aluminum die casting, magnesium or Zamak/zinc die casting and other castings requirements are welcome to contact us.
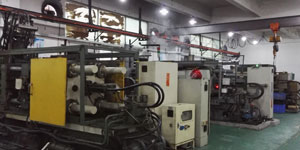
Under the control of ISO9001 and TS 16949,All processes are carried out through hundreds of advanced die casting machines, 5-axis machines, and other facilities, ranging from blasters to Ultra Sonic washing machines.Minghe not only has advanced equipment but also have professional team of experienced engineers,operators and inspectors to make the customer’s design come true.
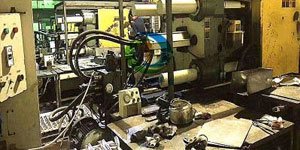
Contract manufacturer of die castings. Capabilities include cold chamber aluminum die casting parts from 0.15 lbs. to 6 lbs., quick change set up, and machining. Value-added services include polishing, vibrating, deburring, shot blasting, painting, plating, coating, assembly, and tooling. Materials worked with include alloys such as 360, 380, 383, and 413.
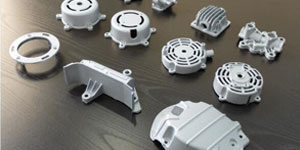
Zinc die casting design assistance/concurrent engineering services. Custom manufacturer of precision zinc die castings. Miniature castings, high pressure die castings, multi-slide mold castings, conventional mold castings, unit die and independent die castings and cavity sealed castings can be manufactured. Castings can be manufactured in lengths and widths up to 24 in. in +/-0.0005 in. tolerance.
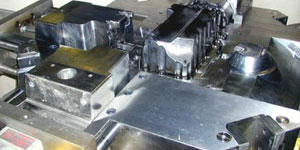
ISO 9001: 2015 certified manufacturer of die cast magnesium, Capabilities include high-pressure magnesium die casting up to 200 ton hot chamber & 3000 ton cold chamber, tooling design, polishing, molding, machining, powder & liquid painting, full QA with CMM capabilities, assembly, packaging & delivery.
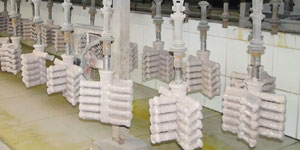
ITAF16949 certified. Additional Casting Service Include investment casting,sand casting,Gravity Casting, Lost Foam Casting,Centrifugal Casting,Vacuum Casting,Permanent Mold Casting,.Capabilities include EDI, engineering assistance, solid modeling and secondary processing.
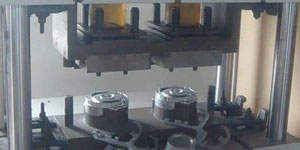
Casting Industries Parts Case Studies for: Cars, Bikes, Aircraft, Musical instruments, Watercraft, Optical devices, Sensors, Models, Electronic devices, Enclosures, Clocks, Machinery, Engines, Furniture, Jewelry, Jigs, Telecom, Lighting, Medical devices, Photographic devices, Robots, Sculptures, Sound equipment, Sporting equipment, Tooling, Toys and more.
What Can we help you do next?
∇ Go To Homepage For Die Casting China
→Casting Parts-Find out what we have done.
→Ralated Tips About Die Casting Services
By Minghe Die Casting Manufacturer |Categories: Helpful Articles |Material Tags: Aluminum Casting, Zinc Casting, Magnesium Casting, Titanium Casting, Stainless Steel Casting, Brass Casting,Bronze Casting,Casting Video,Company History,Aluminum Die Casting |Comments Off