The Quality Control of Die Casting Aluminum Alloy Parts
With the continuous development of the metal casting industry, various new technologies and new materials have been continuously applied, and various products have been born. These products are small in size and light in use, and most of them are produced by pressure casting. Die casting has many advantages. The products produced by it are not only of guaranteed quality, but also high in efficiency, and have a wide range of applications. Die castings using aluminum alloy materials have good application prospects, especially in auto parts frequently. Based on the advantages of die casting method, the quality of castings is therefore valued by many people. However, since the quality of castings will be affected by various factors in the die-casting production process, if the control is not in place, defective products will be produced.
Quality Control Of Raw Materials For Die-Casting Aluminum Alloy Parts
For aluminum alloy castings, in order to improve its quality, it is necessary to increase the qualified rate of production. Raw materials are fundamental, so it should be the top priority for quality control. When selecting raw materials, we must strictly control the quality, adopt sampling inspection to determine the chemical composition of the main elements of the alloy, and carry out corresponding acceptance.
Generally speaking, if there is too much iron in the alloy structure, it will greatly affect the quality of the casting, because it will cause cracks in the casting and greatly reduce the plasticity. However, if the iron content is too small, it will cause problems such as mucous film and difficult demoulding of the casting. Therefore, the iron content must be reasonably controlled. In die castings, the content of copper should also be attached great importance. Appropriately increasing the content of copper can improve the fluidity of the alloy and increase the strength and hardness of the castings. If the copper content is too high, the plasticity of the casting will decrease, the possibility of hot cracking will be higher, and it will not be conducive to subsequent processing, so the copper content should also be controlled. In die castings, the appropriate content of manganese can make the iron in the alloy into a fine crystal shape, reducing the adverse effect of iron on the alloy. It is necessary to properly control the manganese content, because if the manganese content exceeds the standard, it may cause segregation problems, so keeping it within a reasonable range can improve the plasticity of the casting. Zinc can improve the fluidity and machinability of the alloy, and the content should not be too high, otherwise it will cause cracks in the casting. Silicon can improve the shaping of aluminum alloys at high temperatures, and controlling the content of silicon can further improve the performance of the castings, otherwise it will lead to poor processing effects of the castings. In addition, raw materials such as material ends and side leathers also need to be highly valued. In particular, the materials that need to be returned to the furnace must be strictly controlled and cleaned so that they can be used for the second time without contaminating new materials. The ratio of recycled materials to new materials should not exceed one-third, otherwise the quality of die castings will be affected.
Mould Design And Manufacture
2.1 Inner gate and overflow groove
Regarding the design of the inner gate, attention should be paid to its cross-sectional size, because this can ensure that the alloy melt has a certain flow rate, flow rate and pressure. In addition to the section size, the pressure of the die-casting machine and the speed of the punch also affect these contents. From a theoretical point of view, if the cross-sectional size of the inner gate is wider and the thickness is smaller, then under the premise of higher speed, the pressure and filling speed of the alloy will be guaranteed to ensure the quality of die castings. In practical applications, since the cross section of the inner gate does not change, if only increasing the pressure and speed, it will not bring too good results. Therefore, before designing, the inner gate must be designed according to the shape of the casting. In order to further improve the design of the inner gate, the actual situation of the trial mold can be combined.
For some complicated and large-sized parts, attention should be paid to avoiding the formation of vortex when the metal solution flows and avoiding defects such as pores. Therefore, it is necessary to design an overflow groove and match it with the exhaust groove. Use it to enhance the exhaust effect.
2.2 Exhaust slot
The exhaust slot is undoubtedly the focus of the design. When performing die-casting production, the metal solution needs to flow into the cavity, and the corresponding gas will also enter, thereby hindering the normal flow of the metal solution, and the hindered metal solution cannot flow fully, which will inevitably affect its crystallization effect, leaving behind Quality defects such as porosity in castings. For the surface of the casting that needs to be processed and formed, the surface of the processed and unprocessed surface is completely different. No problem can be found when it is not processed. Once processed, there will be many pores on the surface, which means that the casting is defective. Pay attention to the design of the exhaust groove to reduce the internal pores and improve the quality and qualification rate of castings.
2.2.1 Design the exhaust groove according to the shape of the casting
When the new mold is in use, due to the limited running-in of internal components, it may cause poor exhaust due to the shrinking of the scheduling gap in the high temperature state, which affects the quality of the product. Therefore, it is necessary to design the exhaust groove according to the shape of the casting, and pay attention to the reasonable setting of the exhaust gap. Try to set up as many exhaust grooves as possible, do not leave the gap too large, otherwise it will cause the phenomenon of alloy solution spraying around during the mold work. The reasonable thickness of the exhaust groove gap should not exceed 0.20 mm.
2.2.2 Utilize the parting surface and core of the mold
In order to remove the gas as soon as possible, so that it will not affect the normal crystallization of the metal solution, it is necessary to be good at using the parting surface of the mold, the core and other matching parts of the matching gap to remove the gas. Different types of exhaust grooves are designed on the parting surface to ensure that the gap between the core and the part is in a larger state.
2.3 Cavity and mold material
When designing the cavity, it is necessary to consider the melting point of the aluminum alloy material. In the case of high temperature, it will affect the fluidity of the metal, and it will also cause corrosion and damage to the cavity, and it is not easy to demold. Therefore, when designing, you must pay attention to increasing the mold angle, transition fillet radius and cavity Surface roughness value.
When choosing the mold material, choose the corresponding material according to the requirements of different parts, and be equipped with the appropriate heat treatment process. For example, the materials for the cavity and core should preferably be materials with better thermal stability. When making the mold, pay attention to the heat treatment and finishing of the mold.
Heat treatment should take into account the cavity and core parts. In order to prevent quality defects such as cracks in the product, conservative processing methods can generally be used. However, this will shorten the service life of the mold, because the new mold may have cracks on its surface after not working for a long time. The maintenance cost of the mold. Therefore, if the process is improved, the service life of the mold can be increased.
The Control Of Mold Temperature
When die-casting production is carried out in the cold mold, the castings may have many defects, which will affect the quality of the castings. Therefore, the mold temperature must be controlled. Adjust the temperature to a certain level before proceeding to die-casting production, which can greatly reduce the defects of castings. However, the temperature must not be adjusted too high, which will lead to difficult demolding, serious thermal cracks, and affect the surface quality of the casting and the service life of the mold.
The temperature formed by the mold cavity has a great relationship with its own heat dissipation performance. At the same time, the shape of the casting is also related to the cavity temperature. When measuring the temperature of the cavity, choose a place where the heat dissipation part is common, so that a more accurate temperature can be measured.
Conclusion
In summary, in order to improve the quality of aluminum alloy castings, it is necessary to pay attention to the application of die-casting process and do a reasonable quality control, so as to reduce quality defects and increase the qualification rate of castings. Under the existing equipment conditions, how to improve the quality of die castings is still a problem that requires us to think carefully.
Please keep the source and address of this article for reprinting:The Quality Control of Die Casting Aluminum Alloy Parts
Minghe Die Casting Company are dedicated to manufacture and provide quality and high performance Casting Parts(metal die casting parts range mainly include Thin-Wall Die Casting,Hot Chamber Die Casting,Cold Chamber Die Casting),Round Service(Die Casting Service,Cnc Machining,Mold Making,Surface Treatment).Any custom Aluminum die casting, magnesium or Zamak/zinc die casting and other castings requirements are welcome to contact us.
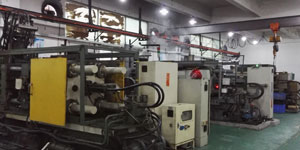
Under the control of ISO9001 and TS 16949,All processes are carried out through hundreds of advanced die casting machines, 5-axis machines, and other facilities, ranging from blasters to Ultra Sonic washing machines.Minghe not only has advanced equipment but also have professional team of experienced engineers,operators and inspectors to make the customer’s design come true.
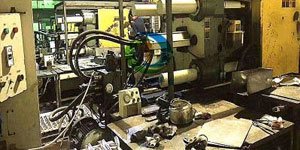
Contract manufacturer of die castings. Capabilities include cold chamber aluminum die casting parts from 0.15 lbs. to 6 lbs., quick change set up, and machining. Value-added services include polishing, vibrating, deburring, shot blasting, painting, plating, coating, assembly, and tooling. Materials worked with include alloys such as 360, 380, 383, and 413.
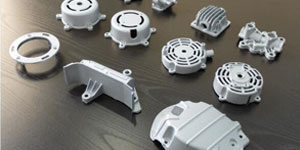
Zinc die casting design assistance/concurrent engineering services. Custom manufacturer of precision zinc die castings. Miniature castings, high pressure die castings, multi-slide mold castings, conventional mold castings, unit die and independent die castings and cavity sealed castings can be manufactured. Castings can be manufactured in lengths and widths up to 24 in. in +/-0.0005 in. tolerance.
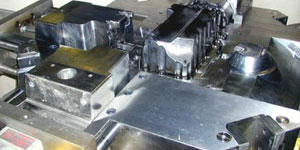
ISO 9001: 2015 certified manufacturer of die cast magnesium, Capabilities include high-pressure magnesium die casting up to 200 ton hot chamber & 3000 ton cold chamber, tooling design, polishing, molding, machining, powder & liquid painting, full QA with CMM capabilities, assembly, packaging & delivery.
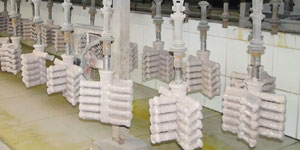
ITAF16949 certified. Additional Casting Service Include investment casting,sand casting,Gravity Casting, Lost Foam Casting,Centrifugal Casting,Vacuum Casting,Permanent Mold Casting,.Capabilities include EDI, engineering assistance, solid modeling and secondary processing.
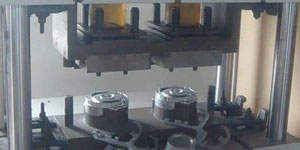
Casting Industries Parts Case Studies for: Cars, Bikes, Aircraft, Musical instruments, Watercraft, Optical devices, Sensors, Models, Electronic devices, Enclosures, Clocks, Machinery, Engines, Furniture, Jewelry, Jigs, Telecom, Lighting, Medical devices, Photographic devices, Robots, Sculptures, Sound equipment, Sporting equipment, Tooling, Toys and more.
What Can we help you do next?
∇ Go To Homepage For Die Casting China
→Casting Parts-Find out what we have done.
→Ralated Tips About Die Casting Services
By Minghe Die Casting Manufacturer |Categories: Helpful Articles |Material Tags: Aluminum Casting, Zinc Casting, Magnesium Casting, Titanium Casting, Stainless Steel Casting, Brass Casting,Bronze Casting,Casting Video,Company History,Aluminum Die Casting |Comments Off