Various defects that endanger the quality of billets
Various defects that endanger the quality of billets. The defects of steel billets can be divided into two categories according to their sources: defects caused by steelmaking and ingot casting and defects caused by steel rolling. From the location of the defect, it can be divided into two types: surface defect and internal defect.
Billet defects mainly include: scarring, cracks, tearing, inclusions (see non-metallic inclusions), residual shrinkage holes (see shrinkage holes), air bags, bubbles, internal cracks, overburning, internal heat, tail holes, tooth marks, folding, Scratches, indentations, dents, angular dissatisfaction, bends (see curvature), ears, twists, bursts, shear defects, poor cleaning, peeling, joints, net cracks, splits, oversize and hemp Wait.
- Airbag. Shrinkage-like defects appear on the shear section of the boiling billet. There are tongue-shaped wave crests with a symmetrical vertical axis on the section, and granular inclusions, fire, discoloration, etc. appear at the cracks of the wave crests. Sometimes the surface bulges, tears, large shearing and spreading, etc., the surface of the finished billet appears convex, there are tongue-shaped wave crests on the section, and the serious billet has long holes.
- Internal fissure. For the cracks inside the billet, when rolling, there is a bulge phenomenon, and a symmetrical single wave peak or double wave peak is formed on the cut surface of the 255 garlg steel. There are cracks and blue fire under the wave peak, and no low melting point substance is precipitated at the wave peak.
- Internal heat. The internal temperature of the steel ingot is higher than the surface temperature, and there is bulging during rolling. The non-rolling surface of the billet is convex, it is compressed during shearing, and it is widened. A "П"-shaped wave crest appears on the shear section, and there is no low-melting substance overflow at the crest.
- Tail hole. The fish tail of the billet is not cut clean and called the tail hole, also known as the mechanical shrinkage hole, but the wave crest is not necessarily symmetrical, and the lower surface of the wave crest is smooth without overflow of inclusions.
- Tooth marks. There are longitudinal cracks on the surface of the billet, the middle of the crack is wide and deep, and it gradually closes to both ends, the surface is smooth, and there are no inclusions inside.
- Depressed. The two sides of the billet are curved and concave.
- The angle is dissatisfied. The corners of the billet are not full, or the fillet radius is too large, which is like a missing corner. Angle dissatisfaction can appear in one corner or several corners, part of the billet or the full length.
- Burst. Steel with low thermal conductivity, cracks due to excessive heating or cooling. The blasting cracks are mostly cracks and transverse cracks, and the cracks are clean and tidy. There will be noise during the cracking process, and the billet will be truncated in severe cases.
- Shearing defects. There are: flattening, the width of the end of the billet after shearing exceeds the standard requirements; cutting obliquely, the cross section of the end of the billet is not perpendicular to the longitudinal axis; the length and the length are not cut according to the fixed length; the burr, the end of the billet is missed.
- Poor cleaning. Such as: burning pits, pits caused by poor operation of flame gun ignition; incompatible aspect ratio, billet cleaning aspect ratio is less than 5:1; pattern edges and corners are too large, and the width of the gun is not enough; missed inspection, defects are not detected before cleaning, Leak clean up.
- Flip the skin. There are layers of corrugated scars around a certain section of the steel ingot, and distinct snakeskin-like scars appear on the four sides of a certain section after rolling into a steel billet.
- Contact mark. There is a horizontal closed crack around the billet, which is caused by the discontinuity of molten steel during ingot casting.
- Reticulated cracks. Due to poor steel quality, high sulfur content and low manganese content, a slightly higher heating temperature can present a burn-out pattern.
- Split. The billet head splits during rolling. Due to the residual shrinkage holes, air pockets, inclusions and low manganese-sulfur ratio of the steel in the head of the steel ingot, and the uneven temperature of the rolled piece during rolling, the speed of the upper and lower rolls is not synchronized, which causes splitting.
- The size is out of tolerance. The section of the billet is correct, but the size exceeds the prescribed standard. The cross-section of the billet is incorrect, showing a rhombus, trapezoid, flat quadrilateral, polygon, staggered convex, etc., which exceeds the standard.
Please keep the source and address of this article for reprinting: Various defects that endanger the quality of billets
Minghe Die Casting Company are dedicated to manufacture and provide quality and high performance Casting Parts(metal die casting parts range mainly include Thin-Wall Die Casting,Hot Chamber Die Casting,Cold Chamber Die Casting),Round Service(Die Casting Service,Cnc Machining,Mold Making,Surface Treatment).Any custom Aluminum die casting, magnesium or Zamak/zinc die casting and other castings requirements are welcome to contact us.
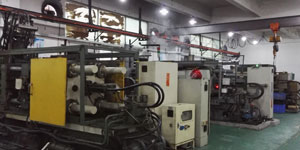
Under the control of ISO9001 and TS 16949,All processes are carried out through hundreds of advanced die casting machines, 5-axis machines, and other facilities, ranging from blasters to Ultra Sonic washing machines.Minghe not only has advanced equipment but also have professional team of experienced engineers,operators and inspectors to make the customer’s design come true.
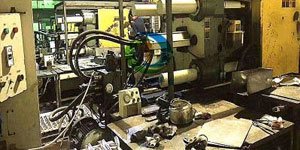
Contract manufacturer of die castings. Capabilities include cold chamber aluminum die casting parts from 0.15 lbs. to 6 lbs., quick change set up, and machining. Value-added services include polishing, vibrating, deburring, shot blasting, painting, plating, coating, assembly, and tooling. Materials worked with include alloys such as 360, 380, 383, and 413.
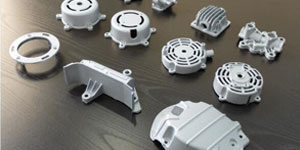
Zinc die casting design assistance/concurrent engineering services. Custom manufacturer of precision zinc die castings. Miniature castings, high pressure die castings, multi-slide mold castings, conventional mold castings, unit die and independent die castings and cavity sealed castings can be manufactured. Castings can be manufactured in lengths and widths up to 24 in. in +/-0.0005 in. tolerance.
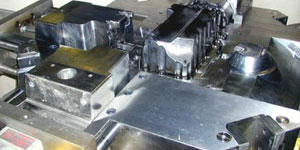
ISO 9001: 2015 certified manufacturer of die cast magnesium, Capabilities include high-pressure magnesium die casting up to 200 ton hot chamber & 3000 ton cold chamber, tooling design, polishing, molding, machining, powder & liquid painting, full QA with CMM capabilities, assembly, packaging & delivery.
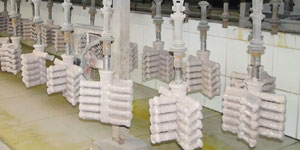
ITAF16949 certified. Additional Casting Service Include investment casting,sand casting,Gravity Casting, Lost Foam Casting,Centrifugal Casting,Vacuum Casting,Permanent Mold Casting,.Capabilities include EDI, engineering assistance, solid modeling and secondary processing.
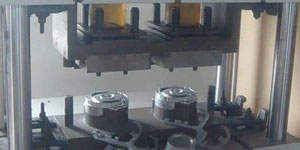
Casting Industries Parts Case Studies for: Cars, Bikes, Aircraft, Musical instruments, Watercraft, Optical devices, Sensors, Models, Electronic devices, Enclosures, Clocks, Machinery, Engines, Furniture, Jewelry, Jigs, Telecom, Lighting, Medical devices, Photographic devices, Robots, Sculptures, Sound equipment, Sporting equipment, Tooling, Toys and more.
What Can we help you do next?
∇ Go To Homepage For Die Casting China
→Casting Parts-Find out what we have done.
→Ralated Tips About Die Casting Services
By Minghe Die Casting Manufacturer |Categories: Helpful Articles |Material Tags: Aluminum Casting, Zinc Casting, Magnesium Casting, Titanium Casting, Stainless Steel Casting, Brass Casting,Bronze Casting,Casting Video,Company History,Aluminum Die Casting |Comments Off