The Advantages Of Six Major Mold Manufacturing Countries In The World
The development of the automobile manufacturing industry has stimulated the market demand of the mold industry, and has gradually developed from the low-end to the high-end market. At present, China, the United States, Japan, Germany, South Korea, and Italy are the six major mold manufacturing countries whose mold output value occupies an absolute position in the world. China's mold output value is the highest in the world. So, what are the differences in production and operation between Chinese molds and the world's major mold manufacturing countries and regions?
With the development of China’s automobile industry, China’s independent brands have also made considerable progress. At the 14th Beijing International Automobile Exhibition held a few days ago, independent brand car manufacturers launched many new models, both in terms of styling and The quality has been greatly improved. Compared with the models of more than ten years ago, it can be said that there is a world of difference. New energy vehicles are blooming. China's self-owned brand vehicles have passed the threshold of entrepreneurship and have begun to enter the high-end market. The car marches on. The development of mid-to-high-end automobiles and the ascendant of new energy automobiles are the first to bear the brunt of the march that marks the true rise of Chinese automobiles. Molds are required to be updated and higher in terms of technology and quality. It is a big challenge and also a good opportunity to promote the transformation and upgrading of the mold factory, and it must go to a higher level in terms of technology and quality, and shift from manufacturing low-end molds to manufacturing high-end molds to meet the needs of the market. demand.
The development of new models puts forward higher and updated requirements for mold technology. In addition to the gradual popularization of progressive molds, multi-station molds, and automatic line molds, there are more and more high-strength plate molds, sharp edge manufacturing technology, aluminum plate molding technology, and carbon fiber molding. Technology, thermoforming technology, etc., have all been mentioned on the agenda of the mold factory.
Regarding carbon fiber forming technology, this is a completely different concept from steel forming. At present, it cannot be used in large quantities due to cost and efficiency. With the improvement of material research and development and technology, this material and technology will definitely be more widely used. When it comes to automobiles, many difficult problems in the stamping process can be easily solved by that time.
Similarly, 3D printing technology will definitely shine in mold manufacturing. In the near future, we can print inserts, print mold bases, print coatings, and stack different materials together. In the past few years abroad, 3D printing technology has been used to print the insert model. Due to the high printing accuracy, the processing volume of the insert is small, and the screw holes are directly cast, leaving a small amount of processing for the pin holes, which is actually equivalent to traditional precision casting . The development of 3D printing technology will solve many problems such as mold heat treatment and outer plate mold coating, and will promote a greater improvement in our mold manufacturing technology.
The lightweight of automobiles will have a great impact on OEMs and mold factories. At the Beijing Auto Show, Great Wall Corolla launched a pure electric coupe named "Qiantu", which uses a carbon fiber structure body, and is investing in building a factory in Suzhou. It is worth noting that this factory is not a traditional four craft factory, but a factory they call the new four craftsmanship. The chairman of the company, Lu Qun, put forward in a conversation: “We believe that new energy vehicles will bring about a comprehensive change in the structure of the automotive industry, especially because the changes in the product cost structure make cars have completely different requirements for lightweight. This has led to new requirements for lightweight materials, processes, and tooling equipment for automobiles. For example, compared with traditional steel plate materials, a large number of lightweight materials such as aluminum-magnesium alloys, plastics, and carbon fibers have begun to be used more and more. To electric vehicles. In this regard, we must view these changes from the perspective of future development, and we must arrange the entire production process closely around new materials and new processes. In fact, of course we are doing four major processes, But it is not the traditional four major processes. The traditional four major processes are steel plate stamping, welding, painting and final assembly, and what we are doing now is composite materials, carbon fiber, aluminum alloy parts and welding, as well as new material coating Final assembly."
The tall workshop and the automated stamping line are gone; sparks are splashing, and the welding lines of hundreds of robots are gone, so electrophoresis is not needed for painting; the engine, fuel tank, and gearbox are gone on the final assembly line, replaced by batteries and motors. The process flow is simplified. The new four major processes have completely affected the traditional four major processes. Of course, these new four major processes cannot completely replace the traditional four major processes. However, due to the need for lightweight vehicles, this process route is probably the only way to go. . Moreover, the wide application of carbon fiber is also an inevitable trend in the future development of the automobile industry. Faced with this trend, where does the mold factory go? Only by following this trend and developing new mold technology can it meet the current and future needs of the OEM.
The Ministry of Industry and Information Technology and the Ministry of Finance recently jointly decided to conduct public bidding for 2016 industrial strong foundation projects, including metal powder additive manufacturing processes and lightweight materials precision molding processes.
In the past ten years, China's mold manufacturing technology has made a qualitative leap. The mold industry has grown rapidly from small to large, and has become a major mold manufacturing country in the world. We can call this stage the first take-off of China's molds. With the development of China's automobile industry, independent brands are marching to mid-to-high end, new energy vehicles are emerging, and the market has put forward new demands for us, requiring us to move from low-end molds to high-end molds, from a big mold country to a mold powerhouse, and realize China The second take-off of the mold. How to achieve the transformation from low to high, from large to strong, and how to achieve the second leap of Chinese molds, is a question worthy of consideration for every Chinese mold factory and every Chinese molder.
At present, China, the United States, Japan, Germany, South Korea, and Italy are the six major mold manufacturing countries whose mold output value occupies an absolute position in the world. China's mold output value is the highest in the world.
Let’s make a comparison between Chinese molds and major mold manufacturing countries and regions in the world: Mold manufacturing in developed countries such as the United States, Japan, and Germany has the following characteristics in terms of production and operation:
- (1) The staff is streamlined. Most of the mold companies in Europe, America and Japan are not large in scale, and the number of employees exceeds 100. The number of mold companies is generally 20-50. The configuration of all kinds of personnel in the enterprise is very streamlined, with one specialization and multiple abilities, and one person with multiple jobs. There are no idlers in the enterprise.
- (2) Adopt professionalization and accurate product positioning. Most mold factories determine their product positioning and market positioning around the needs of various molds in industries such as automobiles and electronics. In order to survive and develop in the market competition, each mold manufacturer has its own superior technology and products, and all adopt professional production methods. Most mold companies in Europe, America and Japan have a group of long-term cooperation mold users, and there are also a group of mold production cooperative manufacturers around large mold companies.
- (3)Advanced management information system to realize integrated management. European and American mold companies, especially the larger mold companies, have basically realized computer management. From production planning, process formulation, to quality inspection, inventory, statistics, etc., computers are commonly used, and various departments within the company can share information through a computer network.
- (4) Advanced process management and high degree of standardization. Unlike domestic mold factories that mostly adopt fitter-based or fitter-based production organization models, mold manufacturers in Europe and the United States rely on advanced process equipment and process routes to ensure parts accuracy and production progress. The advanced technology and advanced management of European and American mold companies have made the large, precise, and complex molds they produce play an extremely important role in promoting the development of industries such as automobiles, electronics, communications, and home appliances, and they have also brought good quality to mold companies. Economic benefits.
U.S. mold industry
There are about 7,000 mold companies in the United States, and 60% of them have less than 15 employees. 15-50 people account for 30%. Due to the rapid development of industrialization, the US mold industry has long become a mature high-tech industry and is at the forefront of the world. The specialization of molds in the United States is very clear. Each mold factory has its own superior products, and basically specializes in all the way. Take the American Synergis mold factory that we have worked with as an example, they specialize in chassis subframe molds. Progressive molds and multi-station molds. We used to manufacture three sub-frames of a vehicle model, one for the Americas, one for Europe, and one for Asia. We are responsible for processing, assembling, and delivering to the initial acceptance level, and the American mold factory is responsible for the final commissioning. This kind of cooperation is beneficial to both parties, and we have also learned a lot in the design and manufacture of large multi-station molds.
The manufacturing cycle of the side moulds processed by the Ford Motor Mould Factory in the United States is only 8 weeks. This is a miracle to us, but they did it. The process and design of the mold in the early stage are not in the mold factory. In the R&D department, the mold factory is only responsible for the manufacturing process starting from the foam model. Since the preliminary work is done well, there are few changes in the process, which saves a lot of time for mold manufacturing. The mold factory processes the foam molds and sends them to casting. The castings come back and start CNC machining. Because of the automatic conversion of multiple worktables, there is no shutdown for 24 hours, and the processing efficiency is very high. Moreover, due to the careful consideration of preliminary work such as springback and deformation, coupled with actuarial technology, the processed mold is directly debugged on the press, and the first part pass rate can reach 85-90%, which shows that the United States is specialized High processing technology.
According to statistics, the per capita output value of molds in the United States in 2014 was approximately RMB 1.27 million.
Japanese mold industry
According to industrial statistics from the Ministry of International Trade and Industry of Japan, there are about 10,000 mold manufacturing factories in Japan, of which more than 20 employees account for more than 91%. That is, the Japanese mold industry is dominated by small and medium-sized enterprises, mainly relying on specialized division of labor to complete high-quality mold design, Processing. Due to the good specialized division of labor in Japan, the overall manufacturing level of small and medium-sized mold companies is relatively high, which enables Japanese molds to occupy a higher share of the world mold market.
In 1988, I went to a Japanese mold factory and a solid casting plant to study. The mold factory only processed the main parts of large parts, and the rest were divided into the following small factories for processing. There was a special design company for the design, and there was a shortage of steel plates. A phone call was quick. It is processed and sent to the designated location. Lack of screws or nails is also a phone call to the designated location quickly, and the division of labor and supporting systems are very complete.
However, due to the rise of molds in China and South Korea, the price advantage has caused a great impact on Japan, and it has become the main competitor of Japanese small and medium mold companies in the mold market with low and medium technology content. It is precisely because of this that Japanese mold companies have to devote themselves to the production of high-end molds and technology upgrades to avoid price competition. That is to use small but precise, small and specialized technology accumulation as the source of competitiveness, to promote the continuous innovation of small and medium-sized mold companies to create a sustainable development environment. Many mold manufacturers in Japan are actively expanding equipment investment. In terms of processing, a large number of unattended processing units are used, or online control is carried out through a computer. The technical development of molds mainly develops in terms of high precision, high speed, long life, complexity, large size, integration and high performance.
According to statistics, the per capita output value of Japanese molds in 2014 was about 1.2 million yuan.
German mold industry
Germany is one of the earliest countries engaged in mold production in Europe. Its mold manufacturing technology and mold quality have been affirmed by users all over the world. It enjoys a high reputation in the world and is one of the most important high-end mold suppliers in the world. After years of practice and exploration, German mold manufacturers have reached a consensus: the entire industry must coordinate, work together, technological innovation, learn from each other's strengths, make progress together, and give full play to the overall advantages in order to achieve success in the industry. In addition, in order to meet the needs of today's rapid development of new products, not only large companies have established new development centers in Germany, but many small and medium-sized enterprises have also done so, actively doing research and development work for customers. Germany has always been very active in research and has become an important foundation for its unbeaten in the international market. In the fierce competition, the German mold industry has maintained a strong position in the international market for many years, and the export rate has been stable at about 33%. According to the German Machinery Factory Manufacturing Association (VDMA), the number of mold manufacturers is about 5,000, but the country's mold industry structure is still dominated by small and medium-sized enterprises: 80% of the employees are less than 20, 19% of the employees are 20-100, and 100 More than 1% of people.
According to statistics, the per capita output value of German molds in 2014 was about 2 million yuan.
Mold industry in Taiwan, China
Taiwan's mold industry is basically a small and medium-sized enterprise, with fine professional division of labor, close production coordination, and relatively stable customers. Each company only produces a certain type of molds, and each has its own competitive products, which is conducive to technological excellence, so that it can survive and develop in fierce competition. The standard mold parts required by the mold factory are all purchased, and some parts processing industries are co-produced by other cooperative factories.
The production of belt parts by mold companies is relatively common. Taiwan's mold industry focuses on the integration of molds and products, and molds and products complement each other and promote each other. Conducive to the development of mold companies.
Develop molds closely following the needs of main products and focus on opening up overseas markets. Taiwan's mold industry is developing rapidly. Among them, the development and manufacture of molds following the needs of the main products is also an important factor. In recent years, the rapid development of the electronics industry and the automobile industry has driven the development of Taiwan's molds. At present, 76% of Taiwan's mold production value comes from electronic products and automobiles.
I once inspected a CNC machine tool factory in Taiwan. The main engine factory is only responsible for assembly and some finishing (partial scraping). The bed is welded by steel plates, and a special factory is responsible for cutting the material, and then send it to the welding plant, after welding, to the annealing plant, after annealing, to the processing plant, and after processing, it is sent to the main engine factory for assembly. Except for the large-scale OEMs, the other factories are very small, and each factory is only responsible for one process. This shows that Taiwan's manufacturing industry has a fine division of labor and close coordination.
China Mould Industry
My country's mold industry started late. Since the mid-1980s, my country's mold industry has undergone great changes, especially in the past ten years, the changes can be said to be earth-shaking, and now it has become the world's largest mold production country. In most areas, Chinese molds have already occupied a considerable share. However, high-end molds still have to be imported in large quantities from abroad. From the perspective of the mold industry as a whole, the overall level of my country's molds is still dominated by medium and low-end molds.
From the perspective of the development history of Chinese mold factories, after the founding of the People’s Republic of my country, there were no professional mold factories in our country. With the establishment of automobile factories in the 1950s and 1960s, tool factories attached to the main engine factories were gradually established, basically referring to the Soviet model. With the development of the automobile industry, the large and comprehensive tool factories established have gradually turned into mold factories.
Take the BAIC I once worked for as an example. It was called BAIC Tool Branch in the 1960s, and Beijing Jeep was established in the 1980s, called Tool Workshop. It mainly produces measuring tools, cutting tools, punching dies, forging dies, casting core boxes, die-casting molds, injection molds, rubber molds and various fixtures. In the late 1990s, it was gradually transformed into a stamping mold factory.
Since the 1990s, the rise of private mold factories, the introduction of a large number of CNC machine tools, the gradual implementation of CAD, CAE, and CAM, and the gradual implementation of CAD, CAE, CAM, the mold industry has flourished, and China has become a major mold manufacturing country, but the production methods of these factories are mostly large and comprehensive. It is small and comprehensive. Basically, it manufactures low-end molds, and there are few mid-to-high-end molds. Everyone basically competes in the low-end market.
What hinders us to be strong, specialized, and refined? One of the biggest obstacles is our large and complete or small and complete production method. Our mold production does not have a specialized division of labor, or that the specialized division of labor is insufficient.
At present, there are about 30,000 mold manufacturing factories in my country, of which state-owned enterprises account for about 5%, joint ventures account for about 10%, private enterprises account for about 85%, and there are about 1 million employees. There are about 5000 enterprises with an annual output value of more than 20 million yuan. . In 2015, the total output value of molds was about 170 billion yuan, and the output value of enterprise's own molds was about 40 billion yuan, which added up to 210 billion, and the per capita output value of molds was about 210,000 yuan. According to the statistics of 82 key enterprises in 2014 by the China Mould Association, the total output value of molds of these enterprises in 2014 was 9 billion yuan, there were 26,800 employees, and the per capita output value was about 335,000 yuan.
From the comparison of the per capita output value of molds, Japanese molds are 1.2 million yuan, American molds are 1.27 million yuan, and German molds are 2 million yuan. That is to say, the per capita output value of molds in the United States and Japan is 3-5 times that of my country, and Germany is 5- 9 times.
There are two main reasons for the low per capita output value. One is that most of the molds we produce are low-end molds with low added value; the other is that our production efficiency is low. Our equipment is not inferior to them. Why is the added value low and the efficiency low? A very important reason is that we are not "specialized". The so-called practice makes perfect, "professional" can produce technology. "Professional" can produce excellent products, and "professional" can produce efficiency. The division of labor is good, so the mold quality is high and the efficiency is high. We are big but not strong, broad but not specialized, we do everything and we are not precise, which has caused our slow technological improvement, slow quality improvement, and slow efficiency improvement. Therefore, the specialization and intensification of mold production is the only way for mold companies to upgrade technology, improve quality, and improve efficiency, and transform to large and strong, professional and sophisticated.
With the continuous improvement of mold manufacturing technology, the types of molds in the future will become more and more abundant. It is impossible for any mold company to fully master these technologies, so the mold manufacturing industry in the future is bound to be a highly specialized industry.
From the current large and complete, small and complete mold manufacturing model, gradually transform to large and strong, specialized and sophisticated, and form a specialized and intensive production model with large and small, and point-to-face. That is to say, a mold center drives multiple small mold factories and multiple process processing plants to form a large, strong, small and specialized production situation. Each center has a professional focus, such as side mold factory, door panel mold factory, beam category Mould factory etc. There are many rules for market segmentation, some will be classified according to different molding materials; some may be classified according to mold type; some will also be classified according to inner panels, outer panels, and even the various assemblies of the car body, and so on.
Specialized production of molds is an inevitable trend. With enterprises as the main body and demand as the driving force, the development of "specialized, refined, special, new" mold enterprises and mold industry clusters, only in this way can we occupy the high-end mold market, and my country can become a major mold power Transformed into a mold powerhouse. In addition to market screening and self-selection by mold factories, the mold association should also adopt various methods to guide this transformation. The fine mold evaluation of the China Mold Association can add special mold evaluations, such as the best side panels, the best fenders, the best doors, the best beams, etc., to guide the mold factory and recommend to the main engine factory. The appraisal will be more meaningful and will promote the specialized division of labor for mold production. Companies should also implement differentiated strategies based on their own conditions and specific local conditions, so that mold production will develop toward intensive, professional, high-quality, and internationalized mold production.
Participated in the Jilin Province and Changchun Mould Association meeting at the end of last year. FAW Mould proposed to establish a regional mould alliance and mould ecosystem to improve the overall level and meet the needs of high-end moulds and the international market. It has taken a good lead in the mould industry.
MINGHE HARDWARE Mould is a factory that mainly produces high-strength board molds. When visiting the factory in September last year, the leaders of the factory proposed to build MINGHE Mould into a professional high-strength board mold factory and no longer participate in the competition of other types of molds. .
These phenomena show that the trend of specialized production and intensive production has emerged in the Chinese mold industry. Let us add to the flames and promote the continuous development of this trend. A single flower does not mean spring, but spring is only a thousand reds. May the garden of Chinese molds be beautiful with big flowers, fragrant flowers and lush green leaves. The road to specialized production of Chinese molds is a long one. As long as we keep going, we will see the dawn of a powerful mold country. This is the dream of our generations of molders!
Please keep the source and address of this article for reprinting: The Advantages Of Six Major Mold Manufacturing Countries In The World
Minghe Die Casting Company are dedicated to manufacture and provide quality and high performance Casting Parts(metal die casting parts range mainly include Thin-Wall Die Casting,Hot Chamber Die Casting,Cold Chamber Die Casting),Round Service(Die Casting Service,Cnc Machining,Mold Making,Surface Treatment).Any custom Aluminum die casting, magnesium or Zamak/zinc die casting and other castings requirements are welcome to contact us.
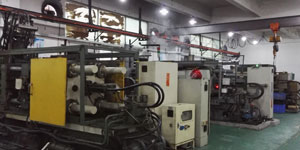
Under the control of ISO9001 and TS 16949,All processes are carried out through hundreds of advanced die casting machines, 5-axis machines, and other facilities, ranging from blasters to Ultra Sonic washing machines.Minghe not only has advanced equipment but also have professional team of experienced engineers,operators and inspectors to make the customer’s design come true.
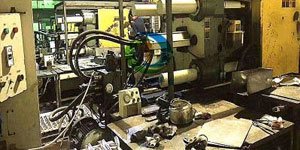
Contract manufacturer of die castings. Capabilities include cold chamber aluminum die casting parts from 0.15 lbs. to 6 lbs., quick change set up, and machining. Value-added services include polishing, vibrating, deburring, shot blasting, painting, plating, coating, assembly, and tooling. Materials worked with include alloys such as 360, 380, 383, and 413.
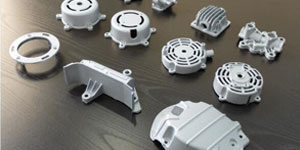
Zinc die casting design assistance/concurrent engineering services. Custom manufacturer of precision zinc die castings. Miniature castings, high pressure die castings, multi-slide mold castings, conventional mold castings, unit die and independent die castings and cavity sealed castings can be manufactured. Castings can be manufactured in lengths and widths up to 24 in. in +/-0.0005 in. tolerance.
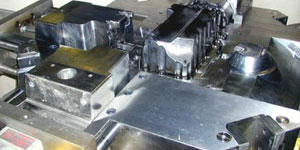
ISO 9001: 2015 certified manufacturer of die cast magnesium, Capabilities include high-pressure magnesium die casting up to 200 ton hot chamber & 3000 ton cold chamber, tooling design, polishing, molding, machining, powder & liquid painting, full QA with CMM capabilities, assembly, packaging & delivery.
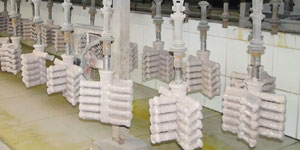
ITAF16949 certified. Additional Casting Service Include investment casting,sand casting,Gravity Casting, Lost Foam Casting,Centrifugal Casting,Vacuum Casting,Permanent Mold Casting,.Capabilities include EDI, engineering assistance, solid modeling and secondary processing.
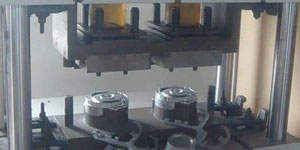
Casting Industries Parts Case Studies for: Cars, Bikes, Aircraft, Musical instruments, Watercraft, Optical devices, Sensors, Models, Electronic devices, Enclosures, Clocks, Machinery, Engines, Furniture, Jewelry, Jigs, Telecom, Lighting, Medical devices, Photographic devices, Robots, Sculptures, Sound equipment, Sporting equipment, Tooling, Toys and more.
What Can we help you do next?
∇ Go To Homepage For Die Casting China
→Casting Parts-Find out what we have done.
→Ralated Tips About Die Casting Services
By Minghe Die Casting Manufacturer |Categories: Helpful Articles |Material Tags: Aluminum Casting, Zinc Casting, Magnesium Casting, Titanium Casting, Stainless Steel Casting, Brass Casting,Bronze Casting,Casting Video,Company History,Aluminum Die Casting |Comments Off