Low-Pressure Casting Process-Three-Point Targeted Measures To Prevent Waste
In low pressure casting, the mold is placed on a closed holding furnace, and the cavity is communicated with the metal in the furnace through a riser pipe. When working, add pressurized air to the furnace, and the molten metal will flow into the cavity from the riser pipe.
After the molten metal has solidified, the compressed air in the furnace is released, and the unsolidified metal flows back into the furnace from the riser pipe. The aluminum wheels and blades in the torque converter core have four major advantages: first, the casting structure is dense and the mechanical properties are good; second, the process production rate is high.
At present, the die casting process production rate of our company's foundry is in Above 93%, the production rate of gravity casting for the same product is 70% to 80%; third, the production efficiency is high, the production efficiency of the same product die casting process is three times that of gravity casting; fourth, the surface is smooth, which can reduce processing margin.
Low pressure casting production process
- Mold inspection The paint should be cleaned before the mold is used. The paint has failed or the surface is uneven after a production cycle, and the paint needs to be polished with a grinding wheel. Then clean the aluminum scraps of the ejector rod and clean the vent plug.
- Bake the mold The best working temperature of the mold is (360±10) ℃, so the mold should be baked to the working temperature before working.
- Coating: When the mold is heated to 300℃, spray the coating. The coating must be even and there should be no sagging. Coatings mainly play the following roles: first, prevent aluminum alloy from corroding the cavity and increase the life of the mold; second, prevent aluminum alloy from sticking to the cavity or parting surface, so that production can be carried out continuously and quickly; third , The coating makes the cavity have a layer of thermal insulation protection organization, so that the molten metal can easily flow into the cavity smoothly, reduce the flow resistance of the molten aluminum, and increase the filling performance of the molten metal.
- The core is loaded.
- Setting process parameters The process parameters of low-pressure casting are mainly the temperature of the molten aluminum, the pressurization rate of the equipment and the pressure setting. These three factors will affect the quality of castings, causing defects such as sand sticking, insufficient pouring, and choking. Therefore, parameter setting is very important for castings.
- Pouring.
Common defects and treatment methods of castings
- Fire choking Figure 3 shows the fire choking defect on the large end face of aluminum wheel castings.The cause of the choking fire: low mold temperature; poor exhaust; too fast filling rate.Solution: increase the mold temperature to 350℃ or above; strengthen the exhaust, mainly by increasing the vent plug, and spraying the paint with good permeability; increasing the filling time, so that all the cavity gas can be exhausted.
- Sticky sand Figure 4 shows the sticky sand defect of the blade casting.The reasons for sticky sand: pouring temperature is too high; sand core strength is insufficient; holding pressure is too high.Solution: The molten aluminum pouring temperature is not higher than 670℃; reduce the baking time of the sand core and maintain the strength of the sand core; set a reasonable holding pressure.
- The main reasons for insufficient pouring: low temperature of molten aluminum and poor fluidity; unreasonable filling parameters, low flow rate during filling; poor exhaust of the mold and high internal pressure, which hinder filling.
- Shrinkage porosity refers to the shrinkage porosity caused by the blade and aluminum wheel respectively.Shrinkage porosity is mainly around the hot joints of the aluminum wheel, gathering or dispersing fine cavities, causing the organization to not be dense. Prevention method: pay attention to the mold temperature field, create sequential solidification conditions; increase the crystallization pressure.
Conclusion
Compared with traditional gravity casting, low pressure casting can greatly increase the production rate of castings, and the work efficiency is high. Because it is crystallized under pressure, the structure of the casting is dense, and the tensile strength can reach more than 200MPa. However, low-pressure casting has higher requirements for equipment, molds and processes, and a little carelessness will cause batches of waste. After our long-term summary, the main reasons that affect the quality of low pressure can be attributed to three points: one is temperature (mold temperature and molten aluminum temperature); the second is exhaust; the third is filling parameters. By taking targeted measures to the above three points, the rejection rate of castings can be continuously reduced.
Please keep the source and address of this article for reprinting: Low-Pressure Casting Process-Three-Point Targeted Measures To Prevent Waste
Minghe Die Casting Company are dedicated to manufacture and provide quality and high performance Casting Parts(metal die casting parts range mainly include Thin-Wall Die Casting,Hot Chamber Die Casting,Cold Chamber Die Casting),Round Service(Die Casting Service,Cnc Machining,Mold Making,Surface Treatment).Any custom Aluminum die casting, magnesium or Zamak/zinc die casting and other castings requirements are welcome to contact us.
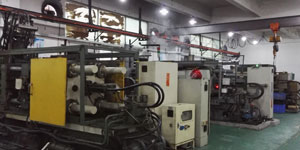
Under the control of ISO9001 and TS 16949,All processes are carried out through hundreds of advanced die casting machines, 5-axis machines, and other facilities, ranging from blasters to Ultra Sonic washing machines.Minghe not only has advanced equipment but also have professional team of experienced engineers,operators and inspectors to make the customer’s design come true.
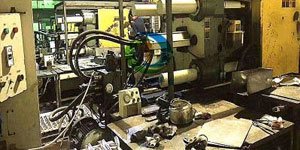
Contract manufacturer of die castings. Capabilities include cold chamber aluminum die casting parts from 0.15 lbs. to 6 lbs., quick change set up, and machining. Value-added services include polishing, vibrating, deburring, shot blasting, painting, plating, coating, assembly, and tooling. Materials worked with include alloys such as 360, 380, 383, and 413.
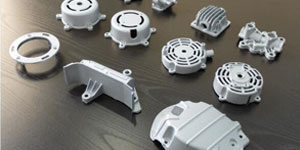
Zinc die casting design assistance/concurrent engineering services. Custom manufacturer of precision zinc die castings. Miniature castings, high pressure die castings, multi-slide mold castings, conventional mold castings, unit die and independent die castings and cavity sealed castings can be manufactured. Castings can be manufactured in lengths and widths up to 24 in. in +/-0.0005 in. tolerance.
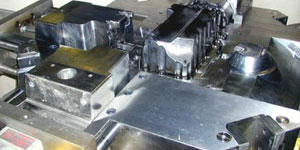
ISO 9001: 2015 certified manufacturer of die cast magnesium, Capabilities include high-pressure magnesium die casting up to 200 ton hot chamber & 3000 ton cold chamber, tooling design, polishing, molding, machining, powder & liquid painting, full QA with CMM capabilities, assembly, packaging & delivery.
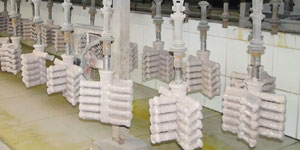
ITAF16949 certified. Additional Casting Service Include investment casting,sand casting,Gravity Casting, Lost Foam Casting,Centrifugal Casting,Vacuum Casting,Permanent Mold Casting,.Capabilities include EDI, engineering assistance, solid modeling and secondary processing.
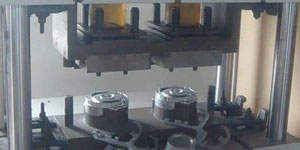
Casting Industries Parts Case Studies for: Cars, Bikes, Aircraft, Musical instruments, Watercraft, Optical devices, Sensors, Models, Electronic devices, Enclosures, Clocks, Machinery, Engines, Furniture, Jewelry, Jigs, Telecom, Lighting, Medical devices, Photographic devices, Robots, Sculptures, Sound equipment, Sporting equipment, Tooling, Toys and more.
What Can we help you do next?
∇ Go To Homepage For Die Casting China
→Casting Parts-Find out what we have done.
→Ralated Tips About Die Casting Services
By Minghe Die Casting Manufacturer |Categories: Helpful Articles |Material Tags: Aluminum Casting, Zinc Casting, Magnesium Casting, Titanium Casting, Stainless Steel Casting, Brass Casting,Bronze Casting,Casting Video,Company History,Aluminum Die Casting |Comments Off