The Causes Of Damage To Die Casting Molds
The Causes of damage to die casting production molds: In die casting production, the most common forms of mold damage are cracks and cracks. Stress is the main cause of mold damage. Thermal, mechanical, chemical, and operational shocks are all sources of stress, including mechanical stress and thermal stress. Stress occurs in:
In the mold processing and manufacturing process
- The quality of blank forging. Some molds have cracks after only a few hundred pieces are produced, and the cracks develop very quickly. It is possible that only the external dimensions are guaranteed during forging, and the loose defects such as dendrites, inclusion carbides, shrinkage cavities, and bubbles in the steel are extended and elongated along the processing method to form a streamline. This streamline affects the future The final quenching deformation, cracking, embrittlement during use, and failure tendency have a great influence.
- Cutting stress generated during final processing such as turning, milling, planing, etc., this stress can be eliminated by intermediate annealing.
- Grinding stress is generated during grinding of hardened steel, friction heat is generated during grinding, softened layer and decarburized layer are generated, thermal fatigue strength is reduced, and hot cracks and early cracks are easily caused. After precision grinding, h13 steel can be heated to 510-570°C, with a thickness of 25mm for one hour for stress relief annealing.
- EDM produces stress. A bright white layer enriched with electrode elements and dielectric elements is formed on the surface of the mold, which is hard and brittle. This layer itself will have cracks and stress. High frequency should be used in EDM to minimize the white layer, polishing method must be used to remove, and tempering treatment, tempering is carried out at the third tempering temperature.
Improper heat treatment during mold processing will result in mold cracking and premature scrapping, especially if only quenching and tempering is used without quenching, and then surface nitriding process, surface cracks and cracks will appear after several thousand die castings. . The stress produced during quenching of steel is the result of the superposition of the thermal stress during the cooling process and the structural stress during the phase transformation. The quenching stress is the cause of deformation and cracking, and the solid must be tempered to eliminate the stress.
In the process of die-casting production
The mold temperature mold should be preheated to a certain temperature before production, otherwise, chilling will occur when the high temperature molten metal is filled, which will increase the temperature gradient of the inner and outer layers of the mold, form thermal stress, and cause the mold surface to crack or even crack. In the production process, the mold temperature continues to rise. When the mold temperature is overheated, it is easy to produce mold sticking, and the failure of moving parts causes damage to the mold surface. A cooling temperature control system should be installed to keep the mold working temperature within a certain range.
Please keep the source and address of this article for reprinting: The Causes Of Damage To Die Casting Molds
Minghe Die Casting Company are dedicated to manufacture and provide quality and high performance Casting Parts(metal die casting parts range mainly include Thin-Wall Die Casting,Hot Chamber Die Casting,Cold Chamber Die Casting),Round Service(Die Casting Service,Cnc Machining,Mold Making,Surface Treatment).Any custom Aluminum die casting, magnesium or Zamak/zinc die casting and other castings requirements are welcome to contact us.
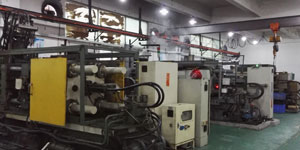
Under the control of ISO9001 and TS 16949,All processes are carried out through hundreds of advanced die casting machines, 5-axis machines, and other facilities, ranging from blasters to Ultra Sonic washing machines.Minghe not only has advanced equipment but also have professional team of experienced engineers,operators and inspectors to make the customer’s design come true.
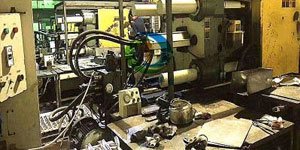
Contract manufacturer of die castings. Capabilities include cold chamber aluminum die casting parts from 0.15 lbs. to 6 lbs., quick change set up, and machining. Value-added services include polishing, vibrating, deburring, shot blasting, painting, plating, coating, assembly, and tooling. Materials worked with include alloys such as 360, 380, 383, and 413.
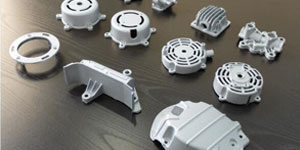
Zinc die casting design assistance/concurrent engineering services. Custom manufacturer of precision zinc die castings. Miniature castings, high pressure die castings, multi-slide mold castings, conventional mold castings, unit die and independent die castings and cavity sealed castings can be manufactured. Castings can be manufactured in lengths and widths up to 24 in. in +/-0.0005 in. tolerance.
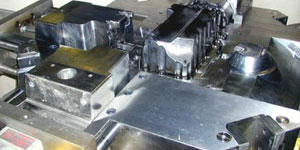
ISO 9001: 2015 certified manufacturer of die cast magnesium, Capabilities include high-pressure magnesium die casting up to 200 ton hot chamber & 3000 ton cold chamber, tooling design, polishing, molding, machining, powder & liquid painting, full QA with CMM capabilities, assembly, packaging & delivery.
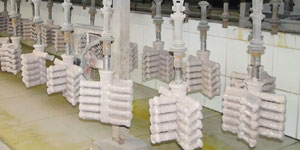
ITAF16949 certified. Additional Casting Service Include investment casting,sand casting,Gravity Casting, Lost Foam Casting,Centrifugal Casting,Vacuum Casting,Permanent Mold Casting,.Capabilities include EDI, engineering assistance, solid modeling and secondary processing.
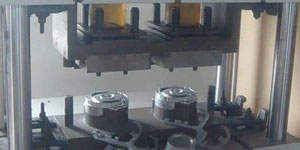
Casting Industries Parts Case Studies for: Cars, Bikes, Aircraft, Musical instruments, Watercraft, Optical devices, Sensors, Models, Electronic devices, Enclosures, Clocks, Machinery, Engines, Furniture, Jewelry, Jigs, Telecom, Lighting, Medical devices, Photographic devices, Robots, Sculptures, Sound equipment, Sporting equipment, Tooling, Toys and more.
What Can we help you do next?
∇ Go To Homepage For Die Casting China
→Casting Parts-Find out what we have done.
→Ralated Tips About Die Casting Services
By Minghe Die Casting Manufacturer |Categories: Helpful Articles |Material Tags: Aluminum Casting, Zinc Casting, Magnesium Casting, Titanium Casting, Stainless Steel Casting, Brass Casting,Bronze Casting,Casting Video,Company History,Aluminum Die Casting |Comments Off