Smelt Clean Steel At Low Cost
With the increasingly demanding demand for steel performance, the market demand of clean steel is increasing, which has a direct impact on the material, design structure, production process and management innovation of refractory materials closely related to the development of steel smelting technology.
The smelting steel in WISCO steel plant tends to be diversified and serial, the proportion of clean steel and variety steel has increased greatly, and the smelting process is developing towards automation and intelligence. Refractory workers react quickly and develop a large number of new technologies to meet the needs of new smelting technologies, such as new high efficiency converter gas supply brick technology, RH refining furnace lining non chromium technology, ladle lining material no carbonization technology, ladle long-life energy saving and heat preservation technology.
Application of new refractory Technology
Application of new type high efficiency converter gas supply brick technology. One of the core technologies of top bottom combined blowing converter is the bottom blowing gas supply element. The development of the technology of the gas supply element and the development of the re blowing process complement each other. The service effect and life of the gas supply element is one of the most important factors affecting the smelting effect. Therefore, with the development of the complex blowing process, the development of gas supply elements has attracted much attention.
In order to realize the low cost smelting of clean steel, the converter blowing process, especially the bottom blowing air supply element, has been put forward with higher performance requirements. This mainly includes: the bottom blowing strength is increased to 0.12nm3/ (min · T) or more; In smelting process, the air supply element is in the bare state, and mushroom head cannot be used to protect the air supply element; The life of the air supply element is in sync with that of the converter, that is, the air supply element cannot be shut down during the whole smelting process of converter.
However, under this smelting process, the traditional porous plug gas supply element of fine metal has some disadvantages, which affects the flow of converter steelmaking. The main embodiment is: the air supply element leaks under high-strength blowing; The air flow of the air supply element is unstable and the blockage occurs; The gas supply components and the supporting brick around them are damaged rapidly; The matching of gas supply element and the surrounding furnace bottom brick has problems, which is prone to triangle joint, which increases the risk of steel leakage in converter.
In recent years, WISCO steel corporation has cooperated with WISCO refractory company to innovate the converter gas supply components, and developed a new type of gas supply brick with high strength, stable gas supply and high overall life. The main contents are as follows: first, the performance of the magnesium carbon refractory, capillary and surrounding brick for the bottom blowing air supply element of converter is upgraded; Secondly, the innovation of the manufacturing technology of gas supply elements, for example, the design of capillary arrangement is changed from traditional mode to honeycomb like capillary arrangement mode, and the capillary pore diameter is further optimized according to the flow pressure ratio (q/p), and the technology research of capillary forming deformation prevention is carried out; Third, the research on near end forming technology; Fourth, the research on welding technology.
Application of chromium free technology for RH refining furnace lining. With the rapid development of automobile, household appliances and canned food industry and the establishment of hydropower, wind power and nuclear power units in various regions, the market demand for cold rolled sheet steel and high-grade silicon steel is increasing. RH refining furnace, as a necessary refining device for smelting high-grade steel, has developed rapidly in recent years. Because the refractory materials bear severe tests such as the hot, cold, strong impact, high vacuum conditions and the strong chemical action of various basicity slag and alloy, people have not stopped to study the service life of refractory, and magnesium chromium brick is a better choice to meet the service life. At present, the RH refining furnace of WISCO steel works mostly uses low silicon magnesium chromium brick, which makes the life of RH extended from 110 times of traditional magnesia chrome brick to more than 150 times.
However, cr6+ will be produced due to the oxidation atmosphere or strong alkaline conditions in the production and use of magnesium chromium brick, which will cause harm to human and environment. With the increasing requirements of environmental protection, chromium free has become an important development direction of RH refining furnace. In addition, the magnesia chrome brick usually needs to go through the mixing, molding, high temperature calcination, drilling, salt immersion, grinding, assembly, and overall regrinding. The manufacturing process is complex and the cost is very high. People have been committed to finding a kind of material instead of magnesium chromium brick, and successively tested magnesium aluminum brick, magnesium zirconium brick, magnesia carbon brick, etc.
At present, WISCO is testing chromium free brick, although it starts late, but it has good effect and its technology is in advanced level.
The application of carbonization free technology for ladle lining material. With the continuous progress of steel smelting technology and the increasingly fierce technical competition, steel-making steel has been developing to high added value and high technology content. In order to meet the technical requirements of refractory materials in smelting process of low carbon steel, ultra-low carbon steel and pure steel, since 2000, no carbonization measures have been implemented gradually in WISCO steel ladle to meet the smelting demand of clean steel. Up to now, more than 80% of the ladle in the steel making plant has achieved no carbonization. The main technological innovation in the implementation process is: the material changes from aluminum magnesium spinel to corundum; The method of masonry is changed from spiral to flat, which solves the problem of triangle gap between bricks and the steel penetration in use; A set of comprehensive technology of ladle operation, maintenance and monitoring has been formed, and the service life of ladle is extended.
Application of long life energy saving and heat preservation technology for ladle. The refractory structure used in traditional smelting ladle lining is mainly divided into two layers, namely permanent layer and working layer. Most permanent layers are made of high alumina bauxite brick or cast with bauxite castable. The resistance of these refractories to steel scour and slag erosion is relatively poor. In the process of using traditional ladle, the temperature of ladle shell is higher, which is generally over 300 ℃ or even over 350 ℃. In order to meet the temperature demand of steel pouring, the steel plant has to improve the temperature of steel output or compensate the temperature through LF furnace, which wastes a lot of energy and alloy, and increases the cost of per ton of steel; The high smelting temperature, the erosion and erosion of the ladle working layer are more serious, the working layer consumes too fast, the safety of the permanent layer is not guaranteed, the ladle operation risk increases, and the service life of the ladle is shortened; The high temperature of the ladle shell makes the steel structure of the shell deformed easily, which has certain influence on the safe operation and service life of the ladle.
Since 2013, in order to meet the requirements of new smelting technology and customer requirements, further improve the safety of ladle production, extend the life of ladle refractory and reduce the energy consumption of steel plant, WISCO refractory plant has carried out transformation and upgrading of the structural design, product performance and intelligent temperature measurement of steel clad refractory, and developed a new type of energy-saving and heat preservation and long-life steel ladle. The ladle has the following advantages in its application effect: first, the safety performance is higher.
Because of the high smelting temperature of traditional ladle, the working layer of ladle is more seriously washed and eroded. The working layer consumes too fast and the safety of permanent layer can not be guaranteed. The new ladle changed this shortcoming, developed a new design structure, which has high working strength at high temperature and excellent resistance to scour of molten steel, which makes the safety coefficient of ladle use improved. Second, the thermal insulation performance is better. The new type of ladle is applied to a steel ladle of WISCO group. Compared with traditional ladle, the temperature of new ladle shell is reduced by 70 ℃ ~100 ℃, the risk of steel leakage is effectively reduced and the energy consumption of steel plant is effectively reduced. Third, the service life is longer. The new type ladle is applied to a steel ladle of WISCO group. The average life of the new ladle is about 20% longer than that of the traditional ladle.
Management innovation of refractory
Refractory has an important influence on the quality, cost and even safety of steel plant products. The promotion and application of new technology plays an important role in the development of new smelting technology, but the innovation of refractory use management is also very important.
Global contract is a more advanced marketing mode for refractory enterprises; For steel mills, it is a more advanced management mode. It integrates design, supply, construction and maintenance, and realizes the transformation from the settlement of t-resistant materials to the settlement mode of consumption per ton of steel. The first mock exam has been running in our country for 10 years or so, and has been popularized in many steel mills, and good results have been achieved. The first mock exam is the contractual relationship, and some enterprises that lack the ability to design and improve continuously are involved in vicious competition and disrupt the market. This makes the advanced nature of this model face severe challenges.
In recent two years, a new management mode of resistant materials, total refractory management, has emerged abroad. This mode is developed on the basis of the general contract mode of durable materials. It emphasizes not only the contract relationship, but the management. Management should not only have the ability, such as design ability, continuous improvement ability, advanced technical reserve ability, etc., but also have sense of responsibility and master's consciousness, so as to release the steel factory from the trivial matters of refractory management. Its significance is not only to reduce and lock down the cost of refractory, but also to make refractory suppliers change to service providers and managers.
Refractory enterprises and steel plants have common value orientation and realize seamless connection. Refractory enterprises can reduce the waste of refractory and reduce the consumption of refractory under the premise of ensuring the safe operation of steel plant through technological progress and management innovation. This objective reduces the pollution of refractory to the molten steel, is conducive to the production of clean steel, thus achieving a win-win goal.
Please keep the source and address of this article for reprinting:Smelt Clean Steel At Low Cost
Minghe Die Casting Company are dedicated to manufacture and provide quality and high performance Casting Parts(metal die casting parts range mainly include Thin-Wall Die Casting,Hot Chamber Die Casting,Cold Chamber Die Casting),Round Service(Die Casting Service,Cnc Machining,Mold Making,Surface Treatment).Any custom Aluminum die casting, magnesium or Zamak/zinc die casting and other castings requirements are welcome to contact us.
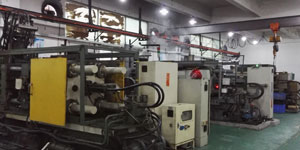
Under the control of ISO9001 and TS 16949,All processes are carried out through hundreds of advanced die casting machines, 5-axis machines, and other facilities, ranging from blasters to Ultra Sonic washing machines.Minghe not only has advanced equipment but also have professional team of experienced engineers,operators and inspectors to make the customer’s design come true.
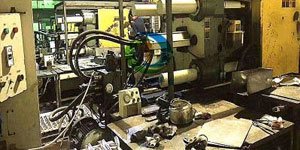
Contract manufacturer of die castings. Capabilities include cold chamber aluminum die casting parts from 0.15 lbs. to 6 lbs., quick change set up, and machining. Value-added services include polishing, vibrating, deburring, shot blasting, painting, plating, coating, assembly, and tooling. Materials worked with include alloys such as 360, 380, 383, and 413.
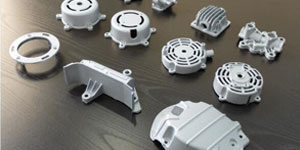
Zinc die casting design assistance/concurrent engineering services. Custom manufacturer of precision zinc die castings. Miniature castings, high pressure die castings, multi-slide mold castings, conventional mold castings, unit die and independent die castings and cavity sealed castings can be manufactured. Castings can be manufactured in lengths and widths up to 24 in. in +/-0.0005 in. tolerance.
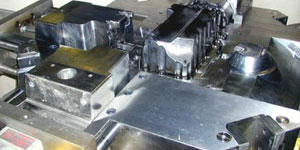
ISO 9001: 2015 certified manufacturer of die cast magnesium, Capabilities include high-pressure magnesium die casting up to 200 ton hot chamber & 3000 ton cold chamber, tooling design, polishing, molding, machining, powder & liquid painting, full QA with CMM capabilities, assembly, packaging & delivery.
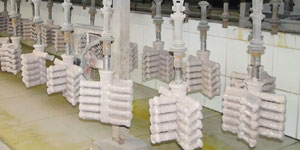
ITAF16949 certified. Additional Casting Service Include investment casting,sand casting,Gravity Casting, Lost Foam Casting,Centrifugal Casting,Vacuum Casting,Permanent Mold Casting,.Capabilities include EDI, engineering assistance, solid modeling and secondary processing.
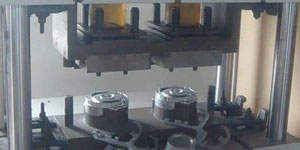
Casting Industries Parts Case Studies for: Cars, Bikes, Aircraft, Musical instruments, Watercraft, Optical devices, Sensors, Models, Electronic devices, Enclosures, Clocks, Machinery, Engines, Furniture, Jewelry, Jigs, Telecom, Lighting, Medical devices, Photographic devices, Robots, Sculptures, Sound equipment, Sporting equipment, Tooling, Toys and more.
What Can we help you do next?
∇ Go To Homepage For Die Casting China
→Casting Parts-Find out what we have done.
→Ralated Tips About Die Casting Services
By Minghe Die Casting Manufacturer |Categories: Helpful Articles |Material Tags: Aluminum Casting, Zinc Casting, Magnesium Casting, Titanium Casting, Stainless Steel Casting, Brass Casting,Bronze Casting,Casting Video,Company History,Aluminum Die Casting |Comments Off