Automobile Panel Moulds and the Development of China Solid Casting
1. The development of China's automobile industry will inevitably drive the development of China's automobile mold manufacturing industry
Since the reform and opening up, China's auto market has maintained a momentum of sustained rapid growth. Today, my country has ranked first in the world in auto production and sales for four consecutive years. Relevant data shows: China's automobile production exceeded 18 million for three consecutive years. In 2012, China's automobile production and sales exceeded 19 million. According to authoritative survey data, the average growth rate of automobiles in developed countries is expected to be 1%, while that in China will reach 36%. , Surpassing the world's economic power-the United States, to become the world's largest auto market, shocking the world.
With the further expansion of cars entering the family, the growth rate of different grades of cars in China has become more rapid. Chinese consumers have become more and more mature, rational and critical. They hope to buy cars with more novel styles and better performance. During the development process, more than 90% of the workload was carried out around the transformation of the automobile profile. The development of a new type of car requires the design and development of about 1,500 sets of molds, of which about 1,000 sets of stamping molds are used, and a large part of the body cover is formed by the automobile cover mold. Therefore, the production of automobile panel molds has a crucial relationship with the speed of new car development and market prospects. The vigorous development of China's automobile industry has greatly promoted the vitality and prosperity of China's automobile mold manufacturing industry, and created huge business opportunities for China's automobile mold industry.
China's automobile panel molds developed from a blank point in the 1950s and 1960s to 2011, my country has dozens of key backbone enterprises. We have developed from only repairing molds instead of manufacturing auto molds, and now our country can not only manufacture molds for inner panels of automobile panels, but also manufacture exterior panel molds for mid-range passenger cars, and can also contract some internationally renowned The cover molds of brand cars can independently develop and produce 20 equivalent vehicle molds a year, which has played an irreplaceable supporting role for the development of China's automobile industry. With the continuous development of China's automobile industry, the domestic automobile mold market will be more prosperous. In the past few years, when people mentioned the automobile mold manufacturing industry, they might think of FAW Mold, Tianqi Mold and Dongfeng Mold, but now this situation has been broken, and more and more private mold companies in China have emerged at the historic moment, such as Shanghai Yisen , Ningbo Shuanglin, Hebei Xingda, Hebei Xinglin and other private mold manufacturing companies have begun to step into the forefront of the automotive mold manufacturing industry, stepping into the advanced ranks of the mold manufacturing industry, their use of funds is more free, the pace of investment in the market is faster, and the mechanism is flexible. At present, these private enterprises are no longer just a little joke in the past. Instead, they attach great importance to the brand building of the enterprise, the information investment of the enterprise, and the development of the international market. The rapidly rising Chinese automobile mold manufacturing industry will be more prosperous with the further development of the automobile industry.
2. The development of China's mold manufacturing industry has promoted the progress of China's solid casting industry
The solid resin sand casting process in my country is a casting process developed in the past ten years. With the development of China’s automobile industry and the prosperity of the automobile mold market, the production of automobile mold castings is an excellent casting process-the solid casting industry is different The extraordinary speed has risen rapidly on the land of China.
The reason why the solid casting process is favored by the automotive panel mold industry is that the automotive panel mold castings have various shapes, complex structures and high quality requirements, and they belong to a single-piece production mode. As shown in Fig. 1 and Fig. 2, the large and complex automobile cover mold base castings adopt the traditional sand casting process, which not only has a long production cycle, high model cost, and accuracy is difficult to guarantee, but adopts a solid casting process and uses EPS to make the model. , The molding is convenient, the adaptability is extremely strong, and the modeling is convenient. It eliminates the need for cumbersome processes such as core making, drying, core hanging and chucking, and greatly shortens the production cycle. It has the incomparable advantages of the traditional sand casting process. The castings produced have no drape seams and have a smooth surface. It can be seen that the solid casting process is an excellent process for producing automobile cover mold castings. In addition, automobile cover molds are important process equipment for the upgrading of all automobiles, and more than 90% of the weight of automobile cover molds is castings.
Once an automobile developer has a new model design, he hopes that the new car will meet with the world as soon as possible. Among many factors, the automobile panel mold is the key node for the new car to be launched on the market. The above fully explains why in the past ten years, with the development of China's automobile industry and the prosperity of China's automobile mold industry, the solid casting industry has rapidly risen in the land of China. Before 2000, there were only a handful of small-scale solid casting factories in the country. In just 10 years after that, Tianjin Jingbo Mould Casting, Great Wall Precision Casting, Zhejiang Jinao Casting and Wuhu Ruihu Casting Co., Ltd. were built all over the country. The company has more than 10 professional real-mould foundries with an annual output of more than 10,000 tons. At present, the technology of some solid casting factories has become mature, and some companies have also innovated in certain aspects, which has made the application of solid casting technology in China made greater progress and development. To reach a higher level, some of their product quality has caught up with the level of world-renowned solid casting companies.
2.1 The development of the automobile mold manufacturing industry has promoted the progress of my country's solid casting process
In the past ten years, China's automobile molds have developed by leaps and bounds from design to manufacturing. At the same time, they have put forward higher requirements for the production of solid mold casting, the basis of the automobile mold manufacturing industry. Progress and development provide favorable opportunities. At present, the new-type car cover molds are developing in the direction of high efficiency, long life, large-scale and high-precision. The shape of the molds is becoming more and more complex. Such development has raised higher standards for the production of solid castings in terms of casting technology and casting materials. Claim. Large-scale drawing molds for cars are commonly made of gray cast iron, nodular cast iron, alloy cast iron or steel castings. The size of the mold is 5-6m, and the weight of the mold is 20-30t.
In addition, the drawing mold not only requires extremely high processing accuracy, but also some mold working surfaces need to be treated by surface quenching, ion nitriding or electroplating. The mold working surfaces are required to have extremely high finish and hardness, and castings are required. The surface must be extremely clean, and no pores, sand holes, sand, slag and carbon deposits are allowed. Therefore, extremely high requirements are placed on the casting process and materials.
As everyone knows, solid casting enterprises are different from traditional casting factories. They are technology-intensive enterprises integrating scientific research, innovation and production. Without one of the two, it is difficult to develop. In recent years, China's automobile mold manufacturing industry has achieved rapid development in terms of production equipment, design, and production technology. It can be said that it is changing with each passing day. The solid casting industry for its supporting services has followed closely and has also moved forward rapidly. The pace of progress. In the past few years, some famous mold companies hired foreign technicians to take charge of the design. They believed that high-end automobile molds and some difficult mold castings could not be cast in mainland China. Therefore, Chinese mold manufacturers had to pay a large price to transfer the above castings to Germany and Japan.
Produced in Korea, or put into production by foreign-funded enterprises in the mainland, this approach is not necessarily to promote foreigners, but we are indeed inferior to their advanced and mature experience in real casting production, and cannot be used for some difficult mold castings. To ensure a 100% success in casting (casting failure, loss of white mold, delay in construction period), this status quo has stimulated the innovation passion of our country's real casting technology workers.
After several years of hard work, at present, such as Hebei Great Wall Precision Casting, Wuhu Ruihu Casting, Zhejiang Jinao Casting, Tianjin Jingbo Mould Casting, etc., the actual casting capacity has exceeded 10,000t/year, and the quality of castings can reach export molds. The required level, whether it is high-grade high-end automobile mold castings or difficult large-scale mold castings, the above-mentioned domestic solid casting companies can achieve a successful casting at one time, and the quality of the castings is almost the same as that of some famous international casting companies. It can meet the requirements of automobile mold manufacturing enterprises and has also been praised by some foreign engineers who are in charge of mold design.
2.2 The development of the automobile mold manufacturing industry promotes the progress of solid casting materials
The improvement of China's automobile mold design level and the development of manufacturing technology have attracted the attention of the world. The material resources and labor resources in mainland China have made foreign companies yearn for. At present, a large number of foreign mold manufacturing projects are flocking to China. This is a fact that is obvious to all. The world's top numerical control processing equipment and processing technology from foreign countries have been continuously introduced into China, which has made the development of China's mold processing industry even more powerful and advancing by leaps and bounds.
For example, Tianjin Automobile Mould Processing Center, China FAW Mould Manufacturing Company, Shanghai Yisen Mould Company, Shanghai Hongxu Mould Company, Hebei Xingda Mould, Wuhu Ruihu Mould, etc. have all become well-known enterprises in the manufacture of body moulds. In the foreign-related mold business, most of their requirements for automotive mold castings are implemented in accordance with foreign standards. Therefore, many new issues have been raised for solid casting, such as high-speed machining technology and "one pass" technology (One Pass Machining) in recent years. (High-speed cutting is more than 10 times the conventional cutting speed; the "one-time" technology is a one-time clamping of the workpiece to complete the rough and fine machining of the profile). The development and application of the above-mentioned high-end technologies put forward higher requirements for castings, requiring that the internal structure and hardness of the castings must be uniform, and there must be no pores, shrinkage holes, sand holes, slag holes and other defects inside the castings.
In addition, the service life of the mold mainly depends on the mold material, manufacturing and assembly accuracy, and the wear resistance of the mold surface. In recent years, the life of the mold in my country has generally been low. The main reason is that the performance of the mold material in my country is relatively large compared with the developed countries. The gap, there is still a lot of room for improvement. In order to catch up with the world's advanced automobile mold level, the country has given great support and support in policy and economy. The vast number of scientific and technological workers have made unremitting efforts to explore.
The real mold casting workers have cooperated and worked together to develop and develop in the past few years. Many new materials for foreign-related mold projects have been released, such as: GGG70L, D6510, EN-JS2070, GM241, GM246, GM190, 50CD4, GP4M, 1.2769s, 1.2333, 1.2370 and a large number of new grades of cast iron or cast steel used in the mold industry Class materials, and put them on the market in batches. Tianjin Jingbo Mould Casting Co., Ltd. pays attention to strengthening technical strength, innovation and enterprising. It attaches great importance to the research and development of new materials and new products. It does not hesitate to invest and walks in the forefront of new materials and new products.
In 2010, the company was rated as the first national A pioneering enterprise in the foundry industry, in 2011, it was rated as a key backbone enterprise in the national foundry industry by the China Foundry Association, and was rated as a small and medium-sized technology-based enterprise by the Tianjin Science and Technology Commission. The developing Chinese solid mold casting industry continues to research and develop new materials and new products, which has enriched the theory of Chinese solid mold casting, trained a group of young Chinese solid mold casting workers, and has also made some Chinese solid mold casting researchers. It has created obvious economic benefits for the enterprise, and at the same time has made due contributions to the society.
3. The progress of China's solid mold casting provides a broad space for Chinese auto mold designers
The solid resin sand casting process in our country is a casting process developed in the past ten years. It is made of foamed plastic board (EPS) by CNC processing to make the structure and shape exactly the same as the casting. After the surface is painted and dried, Buried in the resin sand mold, after the sand mold is hardened, the molten metal is poured, the EPS pattern is heated and gasified, and the molten metal is replaced by a casting method of solidification and molding. Its main characteristics are: the shape is exactly the same as the shape of the casting, without parting surface, parting surface, draft angle, etc. The digitization of the 3D design and processing of the mold is the basis for integration, and the 3D foam model forming technology in the real casting production process enables the programming and numerical control processing in the white mold production process to be seamlessly connected with the mold manufacturing, which can fully reflect the mold in time The engineer's design ideas and technical requirements make it possible to manufacture automobile molds in a refined manner. At the same time, the solid casting process can timely and accurately meet the production requirements of complex molds such as automobile mold drawing dies. The efficiency of manufacturing and development of automobile molds has been improved, and the desire of automobile developers to shorten the development cycle of the entire vehicle becomes possible.
The real casting pattern is directly produced by the digital model application automatic CNC machining center. The shape and size of the pattern are basically close to real castings, which minimizes unnecessary machining allowances and creates favorable conditions for saving high high-speed cutting processing costs. Reduce the high cost of vehicle development, so that automotive mold designers can more broaden their thinking.
At present, the market not only requires the car body to be beautiful and generous, but also requires the improvement of the rigidity and strength of the vehicle as well as the higher impact resistance of the vehicle. At present, IF series steel plates with tensile strengths of about 500MP are generally used for automobile bodies. In the future, they will be replaced by high-strength steel plates, and low-alloy alloy steels will be replaced by dual-phase steels and ultra-high-strength steels. Relevant persons in the automobile design unit pointed out that the current rapid grasp of the stamping technology of high-strength steel plates is an important issue that needs to be solved urgently in my country's automobile mold industry. To solve the technical problem of stamping high-strength steel plate, the first problem is to improve the strength and hardness of the mold material. People in the industry know that the quality and performance of mold materials are important factors affecting mold quality, life and cost. The use of high-strength alloy ductile iron materials for medium and large stamping dies in foreign countries is a development trend that deserves attention. Alloy ductile iron has Strong toughness, high wear resistance and workability. However, in the production process of such castings in China, they are often confused by slag inclusions and carbon defects. At one time, this type of casting business seemed to have become the patent of some foreign-funded enterprises, and many Chinese solid casting manufacturers were afraid to accept it.
Due to the cost of casting production, some Chinese mold manufacturers have to switch to other materials. After repeated research and experimentation, the castings of this material were successfully developed in China Dongfeng Casting and Forging Factory and Tianjin Jingbo Casting Company, and then some of the above-mentioned solid casting enterprises in China have also successfully trial-produced such as: GGG70L (as shown in the figure). 3); D6510; EN-JS2070 and other high-difficulty alloy ductile iron drawing die castings. Wuhu Ruihu Casting Co., Ltd. has not only made remarkable achievements in the development of alloy ductile iron products, but also made a lot of innovations in the real-mould casting process, and carried out in solving difficult problems such as slag inclusion and carbon defects in large ductile iron parts. A useful attempt, and achieved good results. The solid casting can not only successfully cast high-strength alloy ductile iron drawing die castings, but also ensure that the surface of the castings is smooth and free of slag and carbon defects. It provides low-cost and high-quality services for mold manufacturing companies and for my country's automotive mold designers. The selection of mold materials provides a broad leeway.
At this stage, another important problem that plagues the automotive mold industry in my country is the low mold accuracy, although there are many factors that affect the accuracy of the mold. Automobile molds are becoming more and more large-scale, which leads to the problem of reduced mold accuracy due to mold deformation, which has risen to a higher level. Some mold manufacturers inspect molds when manufacturing is completed, and all mold indicators meet the requirements. , But it was stored for a period of time. When the mold was delivered for re-inspection, it was found that the mold was deformed and the mold accuracy index was out of tolerance. Such entanglement accidents caused by mold deformation occur from time to time. The author believes that the problem of mold deformation should be searched from many aspects, from the analysis and search of various factors such as mold structure, mold casting, heat treatment process and cold working process. As a supplier of mold castings, the material of the casting and its casting stress must first be considered. The cooling method and holding time during casting, the aging treatment of castings, and even some material phase change stress issues have an impact on deformation. Therefore, casting quality and accuracy retention are undoubtedly important influencing factors. The solidification process of molten metal from liquid to solid is accompanied by liquid shrinkage, solid state shrinkage and graphitization expansion, especially the filling process of molten iron and the temperature in the cavity during the casting of large mold castings. Factors such as field distribution are all factors that cause the deformation of castings and cannot be ignored. Often, solid casting factories are limited to whether the part can be cast into a piece, and lack the casting process analysis for each casting, and lack clever use of various technological measures to prevent castings. Experience of excessive stress, deformation, and cracking. Wuhu Ruihu Casting Company is conducting experiments and explorations in cleverly using casting experience and technology to effectively solve the problem of dimensional instability caused by casting deformation. It is expected to provide a useful reference for how to maintain the accuracy of the mold in automobile mold manufacturing.
Please keep the source and address of this article for reprinting: Automobile Panel Moulds and the Development of China Solid Casting
Minghe Die Casting Company are dedicated to manufacture and provide quality and high performance Casting Parts(metal die casting parts range mainly include Thin-Wall Die Casting,Hot Chamber Die Casting,Cold Chamber Die Casting),Round Service(Die Casting Service,Cnc Machining,Mold Making,Surface Treatment).Any custom Aluminum die casting, magnesium or Zamak/zinc die casting and other castings requirements are welcome to contact us.
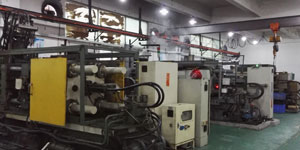
Under the control of ISO9001 and TS 16949,All processes are carried out through hundreds of advanced die casting machines, 5-axis machines, and other facilities, ranging from blasters to Ultra Sonic washing machines.Minghe not only has advanced equipment but also have professional team of experienced engineers,operators and inspectors to make the customer’s design come true.
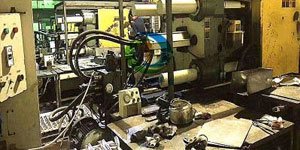
Contract manufacturer of die castings. Capabilities include cold chamber aluminum die casting parts from 0.15 lbs. to 6 lbs., quick change set up, and machining. Value-added services include polishing, vibrating, deburring, shot blasting, painting, plating, coating, assembly, and tooling. Materials worked with include alloys such as 360, 380, 383, and 413.
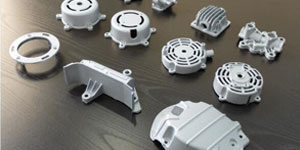
Zinc die casting design assistance/concurrent engineering services. Custom manufacturer of precision zinc die castings. Miniature castings, high pressure die castings, multi-slide mold castings, conventional mold castings, unit die and independent die castings and cavity sealed castings can be manufactured. Castings can be manufactured in lengths and widths up to 24 in. in +/-0.0005 in. tolerance.
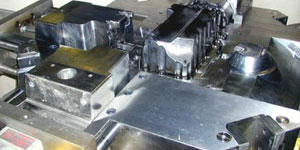
ISO 9001: 2015 certified manufacturer of die cast magnesium, Capabilities include high-pressure magnesium die casting up to 200 ton hot chamber & 3000 ton cold chamber, tooling design, polishing, molding, machining, powder & liquid painting, full QA with CMM capabilities, assembly, packaging & delivery.
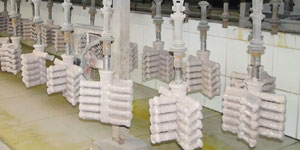
ITAF16949 certified. Additional Casting Service Include investment casting,sand casting,Gravity Casting, Lost Foam Casting,Centrifugal Casting,Vacuum Casting,Permanent Mold Casting,.Capabilities include EDI, engineering assistance, solid modeling and secondary processing.
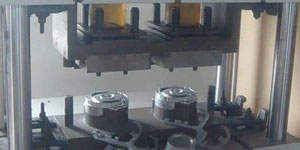
Casting Industries Parts Case Studies for: Cars, Bikes, Aircraft, Musical instruments, Watercraft, Optical devices, Sensors, Models, Electronic devices, Enclosures, Clocks, Machinery, Engines, Furniture, Jewelry, Jigs, Telecom, Lighting, Medical devices, Photographic devices, Robots, Sculptures, Sound equipment, Sporting equipment, Tooling, Toys and more.
What Can we help you do next?
∇ Go To Homepage For Die Casting China
→Casting Parts-Find out what we have done.
→Ralated Tips About Die Casting Services
By Minghe Die Casting Manufacturer |Categories: Helpful Articles |Material Tags: Aluminum Casting, Zinc Casting, Magnesium Casting, Titanium Casting, Stainless Steel Casting, Brass Casting,Bronze Casting,Casting Video,Company History,Aluminum Die Casting |Comments Off