The Heat Treatment Process Of Cast Iron
In addition to the proper selection of excellent ingredients in the production of cast iron to obtain a predetermined structure, heat treatment is also an important way to further adjust and improve the matrix structure to improve the performance of cast iron. The heat treatment of cast iron and the hot embedding of steel have similarities and differences. Heat treatment of cast iron generally cannot improve the morphology and distribution of graphite in the original structure.
For gray cast iron, the stress concentration effect caused by flake graphite is the dominant element in the performance of cast iron. Therefore, the strengthening effect of heat treatment on gray cast iron is far less significant than that of steel and ductile iron. Therefore, the heat treatment process of Youkou cast iron is mainly annealing and normalizing. For ductile iron, since the graphite is spherical, the splitting effect on the matrix is greatly reduced, and the matrix structure can be fully exerted by heat treatment, which can significantly improve the spherical mechanical properties.
Therefore, ductile iron is like steel, and its heat treatment processes include annealing, normalizing, quenching and tempering, multi-temperature quenching, induction heating quenching and surface chemical heat treatment.
Heat treatment process of cast iron
1. Stress relief annealing
Due to the uneven wall thickness of the casting, effect forces and structural stress will be generated during heating, cooling and phase change. In addition, large parts are prone to residual stresses after machining, and all these internal stresses must be eliminated. The usual heating temperature for stress relief annealing is 500~550℃, the holding time is 2~8h, and then furnace cooling (gray iron) or air cooling (ductile iron). Using this process can eliminate 90-95% of the internal stress of the casting, but the structure of the cast iron does not change. If the temperature exceeds 550℃ or the holding time is too long, it will cause graphitization and reduce the strength and hardness of the casting.
2. Eliminate the high temperature graphitization annealing of the white mouth of the casting
When the casting is cooled, the surface layer and thin section often have white mouths. The white mouth structure is hard and brittle, has poor processing performance and is easy to peel off. Therefore, the method of annealing (or normalizing) must be used to eliminate the white mouth structure. The annealing process is: heating to 550-950°C for 2 to 5 hours, then furnace cooling to 500-550°C and then air cooling. During the high temperature holding period, the high cementite and eutectic cementite decompose into graphite and A, and the secondary cementite and eutectoid cementite also decompose during the subsequent cooling process, and the graphitization process occurs. Due to the decomposition of cementite, the hardness decreases, thereby improving the machinability.
3. Normalizing of ductile iron
The purpose of normalizing ductile iron is to obtain the pearlite matrix structure, and to refine the crystal grains and uniform structure to improve the mechanical properties of the castings. Sometimes normalizing is also the preparation for the surface quenching of ductile iron. Normalizing is divided into high temperature normalizing and low temperature normalizing. The high-temperature normalizing temperature generally does not exceed 950-980℃, and the low-temperature normalizing is generally heated to a common bending temperature range of 820-860℃. After normalizing, four people are required to deal with it to eliminate the internal stress generated during normalizing.
4. Quenching and tempering of ductile iron
In order to improve the mechanical properties of ductile iron, generally castings are heated to 30-50°C above Afc1 (Afc1 represents the final temperature of A formation during heating), and then quenched into oil after heat preservation to obtain a martensitic structure. In order to appropriately reduce the residual stress after quenching, tempering should generally be carried out after quenching. The low-temperature tempering structure is tempered martensite with residual bainite and nodular graphite. This structure has good wear resistance and is used for parts that require high wear resistance and high strength. The tempering temperature of the medium temperature is 350-500℃. The structure after tempering is tempered troostite plus spherical graphite, which is suitable for thick parts that require good wear resistance, stability and elasticity. High temperature The tempering temperature is 500-60D ℃, the structure after tempering is tempered Soxhlet made of spheroidal graphite, which has a good combination of toughness and strength, so it is widely used in production.
5. Multi-temperature quenching of ductile iron
Ductile iron can obtain high strength after austempering, while having good plasticity and toughness. The selection of the heating temperature for multi-temperature quenching mainly considers that the original structure is completely A-formed, without residual F, and at the same time, avoiding the growth of A crystal grains. The heating temperature is generally 30-50°C above Afc1, and the isothermal treatment temperature is 0-350°C to ensure that the lower bainite structure with comprehensive mechanical properties is obtained. Rare earth magnesium aluminum ductile iron after isothermal quenching σb=1200~1400MPa, αk=3~3.6J/cm2, HRC=47~51. But it should be noted that a tempering process should be added after austempering.
6. Surface hardening
In order to improve the surface hardness, wear resistance and fatigue strength of some castings, surface quenching can be used. Both gray cast iron and ductile iron castings can be surface hardened. Generally, high (medium) frequency induction heating surface hardening and electric contact surface hardening are used.
7. Chemical heat treatment
For castings that require surface wear resistance, oxidation resistance, and corrosion resistance, chemical heat treatment processes similar to steel can be used, such as gas "target="_blank">gas soft chlorination, chlorination, boronizing, sulfurizing and other treatments.
Please keep the source and address of this article for reprinting:The Heat Treatment Process Of Cast Iron
Minghe Die Casting Company are dedicated to manufacture and provide quality and high performance Casting Parts(metal die casting parts range mainly include Thin-Wall Die Casting,Hot Chamber Die Casting,Cold Chamber Die Casting),Round Service(Die Casting Service,Cnc Machining,Mold Making,Surface Treatment).Any custom Aluminum die casting, magnesium or Zamak/zinc die casting and other castings requirements are welcome to contact us.
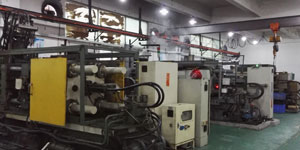
Under the control of ISO9001 and TS 16949,All processes are carried out through hundreds of advanced die casting machines, 5-axis machines, and other facilities, ranging from blasters to Ultra Sonic washing machines.Minghe not only has advanced equipment but also have professional team of experienced engineers,operators and inspectors to make the customer’s design come true.
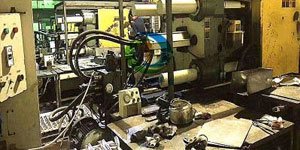
Contract manufacturer of die castings. Capabilities include cold chamber aluminum die casting parts from 0.15 lbs. to 6 lbs., quick change set up, and machining. Value-added services include polishing, vibrating, deburring, shot blasting, painting, plating, coating, assembly, and tooling. Materials worked with include alloys such as 360, 380, 383, and 413.
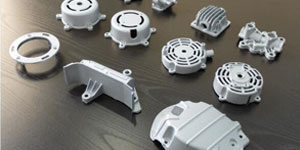
Zinc die casting design assistance/concurrent engineering services. Custom manufacturer of precision zinc die castings. Miniature castings, high pressure die castings, multi-slide mold castings, conventional mold castings, unit die and independent die castings and cavity sealed castings can be manufactured. Castings can be manufactured in lengths and widths up to 24 in. in +/-0.0005 in. tolerance.
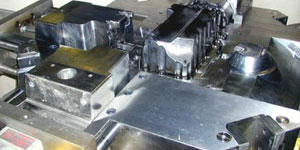
ISO 9001: 2015 certified manufacturer of die cast magnesium, Capabilities include high-pressure magnesium die casting up to 200 ton hot chamber & 3000 ton cold chamber, tooling design, polishing, molding, machining, powder & liquid painting, full QA with CMM capabilities, assembly, packaging & delivery.
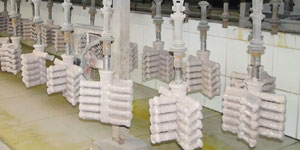
ITAF16949 certified. Additional Casting Service Include investment casting,sand casting,Gravity Casting, Lost Foam Casting,Centrifugal Casting,Vacuum Casting,Permanent Mold Casting,.Capabilities include EDI, engineering assistance, solid modeling and secondary processing.
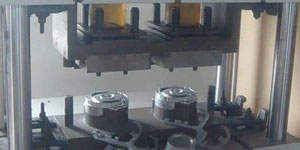
Casting Industries Parts Case Studies for: Cars, Bikes, Aircraft, Musical instruments, Watercraft, Optical devices, Sensors, Models, Electronic devices, Enclosures, Clocks, Machinery, Engines, Furniture, Jewelry, Jigs, Telecom, Lighting, Medical devices, Photographic devices, Robots, Sculptures, Sound equipment, Sporting equipment, Tooling, Toys and more.
What Can we help you do next?
∇ Go To Homepage For Die Casting China
→Casting Parts-Find out what we have done.
→Ralated Tips About Die Casting Services
By Minghe Die Casting Manufacturer |Categories: Helpful Articles |Material Tags: Aluminum Casting, Zinc Casting, Magnesium Casting, Titanium Casting, Stainless Steel Casting, Brass Casting,Bronze Casting,Casting Video,Company History,Aluminum Die Casting |Comments Off