Pressure Vessel Heat Treatment Process Regulation
1 Scope
This standard specifies the post-weld heat treatment process for carbon steel and low-alloy steel welded components.
This standard is applicable to carbon steel and low-alloy steel products of boilers and pressure vessels. The post-weld heat treatment is implemented for the main purpose of improving joint performance and reducing welding residual stress. The post-weld heat treatment of other products can also be implemented by reference.
2. Reference standards
The provisions contained in the following standards constitute the provisions of this standard through quotation in this standard. At the time of publication of the standard, the editions shown were valid. All standards will be revised, and all parties using this standard should explore the possibility of using the latest version of the following standards.
GB9452-2003 Method for measuring effective heating zone of heat treatment furnace
3. Requirements
3.1 Personnel and responsibilities
3.1.1 The heat treatment operator shall be trained, qualified and obtain the job certificate before performing the post-weld heat treatment operation.
3.1.2 The post-weld heat treatment process is compiled by the heat treatment technician and reviewed by the heat treatment engineer.
3.1.3 The heat treatment workers should strictly follow the post-weld heat treatment process and fill in the original operation records carefully.
3.1.4 The heat treatment engineer is responsible for reviewing the original operation records of post-weld heat treatment (including the time-temperature automatic recording curve), verifying whether it meets the requirements of the post-welding heat treatment process, and signing and sealing after confirmation.
3.2 Equipment
3.2.1 Various post-weld heat treatments and devices should meet the following requirements:
- a) It can meet the requirements of post-weld heat treatment process;
- b) During the post-weld heat treatment process, there is no harmful effect on the heated parts;
- c) It can ensure that the heated part of the heated part is evenly heated;
- d) Able to accurately measure and control temperature;
- e) After the heated part is heat treated after welding, its deformation can meet the design and use requirements.
3.2.2 The post-weld heat treatment equipment can be one of the following:
- a) Electric heating furnace;
- b) Hood gas stove;
- c) Infrared high temperature ceramic electric heater;
- d) Other heating devices that can meet the requirements of post-weld heat treatment process
3.3 Post-weld heat treatment method
3.3.1 Heat treatment in furnace
- a) The post-weld heat treatment should preferably adopt the method of heating in the furnace, and the heat treatment furnace should meet the relevant regulations of GB9452. In the case where the corresponding relationship value between the furnace temperature and the heated part is accumulated, the furnace temperature is generally allowed to calculate the temperature of the heated part during heat treatment in the furnace. However, for special or important welding products, the temperature measurement should be placed in the heated part. The thermocouple on the heating element shall prevail.
- b) The heated parts should be neatly placed in the effective heating zone of the furnace, and the heat in the furnace should be even and circulated. In the heat treatment in the flame furnace, the flame should be avoided to spray directly on the workpiece.
- c) In order to prevent the occurrence of restraint stress and deformation, the support of the heated part should be arranged reasonably, and necessary supports and other tools should be added to the large-scale thin-walled parts and those with large differences in structure and geometric dimensions to increase rigidity and balance stability.
3.3.2 Sectional heat treatment
The post-weld heat treatment is allowed to be carried out in sections in the furnace. When the heated part is heat-treated in sections, its repeated heating length shall not be less than 1500mm. Appropriate insulation measures should be taken for the outer part of the furnace to be heated so that the temperature gradient will not affect the structure and performance of the material.
3.3.3 Heat treatment outside the overall furnace
When performing overall heat treatment outside the furnace, on the basis of meeting 3.2.1, you should also pay attention to:
- a) Consider the adverse effects of climate change, power outages and other factors on heat treatment and emergency measures;
- b) Necessary measures should be taken to ensure the uniformity and stability of the temperature of the heated part, and avoid restraint stress and deformation of the heated part, supporting structure, base, etc. due to thermal expansion and contraction
3.3.4 Local heat treatment
Type B, C, D welded joints, type A welded joints where the spherical head is connected to the cylinder, and defective welded joints, local heat treatment methods are allowed. During local heat treatment, the heating width on each side of the weld shall not be less than 2 times the thickness of the steel δs (δs is the thickness of the steel at the welded joint); the heating width shall not be less than 6 times the thickness δs of the steel when the pipe is welded to the shell. Heat preservation measures should be taken for the parts close to the heating zone so that the temperature gradient will not affect the structure and performance of the material.
3.4 Process parameters of post-weld heat treatment
3.4.1 The temperature of the heated part when entering or exiting the furnace shall not exceed 400°C, but for heated parts with large thickness differences, complex structures, high dimensional stability requirements, and low residual stress values, they may enter the furnace or The temperature in the furnace when it is out of the furnace should generally not exceed 300°C.
3.4.2 After the weldment is heated to 400°C, the heating rate of the heating zone shall not exceed (5000/δs)°C/h, and shall not exceed 200°C/h, and the minimum may be 50°C/h.
3.4.3 When heating up, the temperature difference within any 5000mm length in the heating zone shall not be greater than 120°C.
3.4.4 During heat preservation, the difference between the highest and lowest temperature in the heating zone should not exceed 65°C.
3.4.5 During the heating and holding period, the atmosphere of the heating zone should be controlled to prevent excessive oxidation of the surface of the weldment.
3.4.6 When the furnace temperature is higher than 400℃, the cooling rate of the heating zone shall not exceed (6500/δs)℃/h, and it shall not exceed 260℃/h, and the minimum can be 50℃/h.
3.4.7 The weldment shall continue to be cooled in still air after being discharged according to the discharge temperature of 3.4.1.
3.4.8 Recommended holding temperature and holding time of post-weld heat treatment for commonly used steel grades
Steel grade Thickness of post-weld heat treatment δs, mm Post-weld heat treatment temperature ℃ Post-weld heat treatment holding time
No preheating before welding, preheating 100℃ before welding
Q235-A.F, Q235-A,10, 20, 20R, 25 >32 >38 600~640
1) When the thickness
- When δs≤50mm,
- It is (δs/25)h, but the shortest time is not less than 1/4h.
2) When the thickness
- When δs>50mm,
- Is [2+1/4×(δs-50)/25]h
- 09MnD —— —— 580~620
- 16Mn, 16MnR
- 16MnD, 16MnDR >30 >34 600~640
- 12CrMo —— Any thickness 640~680 1) When the thickness δs≤125mm, it is (δs/25)h, but the shortest time is not less than 1/4h.
3) When the thickness δs>125mm, it is [5+0.25×(δs-125)÷25]h
- 15CrMo, 15CrMoR —— any thickness 640~680
- 1Cr5Mo —— any thickness 720~760
Note:
1. For welded joints with different steel thicknesses, the thickness δs shall be the thinner one.
2. For welded joints of dissimilar steels, the one with strict heat treatment shall be determined.
3. For the post-weld heat treatment of quenched and tempered steel, the holding temperature should generally be lower than the tempering temperature of the steel. However, there is no restriction on post-weld heat treatment where the holding temperature is higher than the tempering temperature and the performance of the steel can still meet the requirements of the product.
4. Heat treatment thickness δs refers to:
- a) The thickness of the thinner part when the shell and the head are connected;
- b) The thickness of the shell welded with flanges, tube sheets or other similar structures;
- c) The thickness of the shell or head welded to the nozzle;
- d) The thickness of the weld at the joint when the non-pressure part is welded to the pressure part;
- e) Depth of repair weld.
5. The holding time can be cumulatively added.
3.5 Requirements of post-weld heat treatment for test plates
For vessels with heat treatment requirements, the test plate shall be subjected to post-weld heat treatment together with the vessel.
3.6 Requirements for the storage period of post-weld heat treatment records
The post-weld heat treatment time and temperature curve record retention period shall not be less than 7 years.
Please keep the source and address of this article for reprinting: Pressure Vessel Heat Treatment Process Regulation
Minghe Die Casting Company are dedicated to manufacture and provide quality and high performance Casting Parts(metal die casting parts range mainly include Thin-Wall Die Casting,Hot Chamber Die Casting,Cold Chamber Die Casting),Round Service(Die Casting Service,Cnc Machining,Mold Making,Surface Treatment).Any custom Aluminum die casting, magnesium or Zamak/zinc die casting and other castings requirements are welcome to contact us.
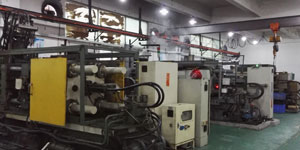
Under the control of ISO9001 and TS 16949,All processes are carried out through hundreds of advanced die casting machines, 5-axis machines, and other facilities, ranging from blasters to Ultra Sonic washing machines.Minghe not only has advanced equipment but also have professional team of experienced engineers,operators and inspectors to make the customer’s design come true.
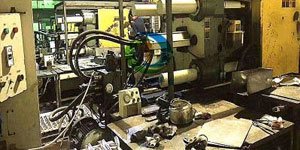
Contract manufacturer of die castings. Capabilities include cold chamber aluminum die casting parts from 0.15 lbs. to 6 lbs., quick change set up, and machining. Value-added services include polishing, vibrating, deburring, shot blasting, painting, plating, coating, assembly, and tooling. Materials worked with include alloys such as 360, 380, 383, and 413.
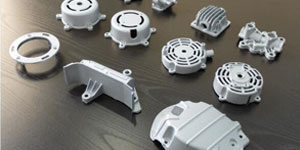
Zinc die casting design assistance/concurrent engineering services. Custom manufacturer of precision zinc die castings. Miniature castings, high pressure die castings, multi-slide mold castings, conventional mold castings, unit die and independent die castings and cavity sealed castings can be manufactured. Castings can be manufactured in lengths and widths up to 24 in. in +/-0.0005 in. tolerance.
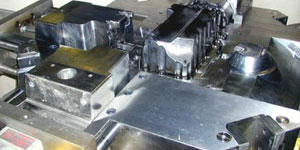
ISO 9001: 2015 certified manufacturer of die cast magnesium, Capabilities include high-pressure magnesium die casting up to 200 ton hot chamber & 3000 ton cold chamber, tooling design, polishing, molding, machining, powder & liquid painting, full QA with CMM capabilities, assembly, packaging & delivery.
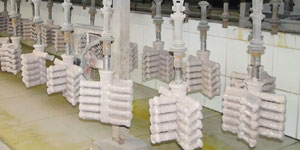
ITAF16949 certified. Additional Casting Service Include investment casting,sand casting,Gravity Casting, Lost Foam Casting,Centrifugal Casting,Vacuum Casting,Permanent Mold Casting,.Capabilities include EDI, engineering assistance, solid modeling and secondary processing.
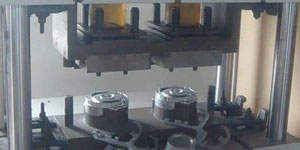
Casting Industries Parts Case Studies for: Cars, Bikes, Aircraft, Musical instruments, Watercraft, Optical devices, Sensors, Models, Electronic devices, Enclosures, Clocks, Machinery, Engines, Furniture, Jewelry, Jigs, Telecom, Lighting, Medical devices, Photographic devices, Robots, Sculptures, Sound equipment, Sporting equipment, Tooling, Toys and more.
What Can we help you do next?
∇ Go To Homepage For Die Casting China
→Casting Parts-Find out what we have done.
→Ralated Tips About Die Casting Services
By Minghe Die Casting Manufacturer |Categories: Helpful Articles |Material Tags: Aluminum Casting, Zinc Casting, Magnesium Casting, Titanium Casting, Stainless Steel Casting, Brass Casting,Bronze Casting,Casting Video,Company History,Aluminum Die Casting |Comments Off