The Material Classification Of Commonly Used Die-Cast Aluminum Alloy
The density of aluminum is only about 1/3 of that of iron, copper, zinc and other alloys. It is currently one of the die-casting alloy materials that meet the requirements of lightweight. In addition, aluminum has higher specific strength and specific rigidity, and has good plastic rheological properties. , The advantages of narrow crystallization temperature range, low linear shrinkage rate, easy forming and cutting, high mechanical properties and corrosion resistance, based on the above advantages, aluminum alloy has become one of the high-strength and toughness die-casting alloy materials. Aluminum alloy die castings have excellent weight reduction effects in the automotive, aerospace and other industries. Since the 1980s, the rapid development of the automotive industry has driven the development of related industries. The development of the automotive industry mainly centers on intelligence, lightweight, and modular化 and so on.
The influence of alloy composition on the properties of aluminum alloy The composition and content of die-cast aluminum alloy have a significant impact on the mechanical properties of the casting. For the performance requirements of different castings, different die-casting processes and corresponding aluminum alloy compositions should be selected. At present, die-cast aluminum alloys are widely used in the industrial field. Al-Si binary alloys, Al-Mg binary alloys, Al-Si-Mg alloys, Al-Si-Cu alloys, etc. are commonly used in China, the United States, and Japan. The aluminum alloy model and composition are shown in Table 1. Generally, the main alloying elements added to the traditional die-cast aluminum alloy are Si, Fe, Cu, etc., among which the addition of Si element can enhance
The fluidity of aluminum alloy, the addition of Fe element is conducive to the demolding of die castings, the addition of Cu element can enhance the strength of castings, and the addition of various alloying elements makes aluminum alloys have different properties and advantages and disadvantages.
Alloy Composition | China | United States | Japan | Element Composition |
AI-Si | YL102 | A413 | ADC2 | AISi12(Fe) |
- | C443 | - | AISi9 | |
AI-Mg | YL302 | 518 | ADC5 | AIMg8 |
AI-Si-Cu | YL113 | A383 | ADC12 | AISillCu3 |
YL117 | B390 | ADC14 | AISil7Cu5Mg | |
AI-Si-Mg | YL101 | A360 | ADC3 | AISil10Mg(Fe) |
ADC6 | AIMg5Si |
Al-Si Series Alloy
The addition of Si element to the die-cast aluminum alloy will reduce the crystallization temperature range, the eutectic content will increase, and due to the large latent heat of crystallization of the Si element, the fluidity of the alloy will increase. In addition, the volume shrinkage rate of Si element is approximately zero, and the linear expansion coefficient is much smaller than that of Al. As the content of Si element increases, the shrinkage rate of the formed alloy decreases, reducing the tendency of pore shrinkage and hot cracking, and inhibiting high temperature brittleness. Due to the addition of Si element to die-cast aluminum alloy, it has good casting performance, thermal conductivity, corrosion resistance and other advantages, so that Al-Si series alloys are widely used in the field of casting. Although the traditional Al-Si binary alloy series has good strength, its plasticity is poor, and it is difficult to meet the requirements for higher performance aluminum alloys in the rapid development of the automotive industry.
The main defect of Al-Si series alloys is that during the casting process, it is easy to cause defects such as non-conforming casting size and pores. The microstructure grains of traditional cast aluminum alloys are dendrites, which affect the mechanical properties of the alloy. The industry divides Al-Si alloys into three categories: hypoeutectic Al-Si alloys, eutectic Al-Si alloys, and hypereutectic Al-Si alloys, as shown in Figure 1. The higher Si content in the alloy promotes the formation of hard and rough primary Si particles and improves the wear resistance of hypereutectic Al-Si alloys. At the same time, the presence of primary Si particles is also detrimental to the mechanical properties of the alloy. Impact, such as reducing cutting performance.
Al-Mg Series Alloy
Al-Mg alloys have excellent plasticity and corrosion resistance. The surface quality of the formed castings is high. It is mainly used in automobile corrosion-resistant parts and die castings with high surface quality requirements. Mg element is added to die-cast aluminum alloy. Since the radius of Mg atoms is 13% larger than that of Al atoms, after solution treatment, Mg dissolves in the alpha phase of Al, causing greater distortion and improving the strength of the aluminum alloy. A spinel film with strong corrosion resistance can be formed on the surface of the Al-Mg alloy liquid, which can improve the corrosion resistance of the alloy, and the tendency of the alloy to form a mucous film is low, and the surface quality of the casting is high. However, Al-Mg alloys may produce hard and brittle phases of Mg 2 Si and Al 3 Mg 2, which reduce the elongation of the alloy and increase the tendency of hot cracking. It is easy to oxidize or form slag during smelting, resulting in poor casting performance.
Al-Si-Mg Series Alloy
Al-Si-Mg series alloys belong to a special kind of Al-Si series alloys. In Al-Si series alloys, the solubility of Si element in Al is small, and it is difficult to add more Si element to aluminum alloy. Therefore, adding Si element to aluminum alloy The intensity of the impact is small. Since it cannot be strengthened by the heat treatment process, it can be considered to add Mg element to the Al-Si series alloy. After the heat treatment process, the alloy will precipitate a dispersion strengthening phase to improve the strength of the alloy. For example, ZL114A aluminum alloy is an Al-Si-Mg alloy, a small amount of Mg can improve the tensile strength and yield strength of the alloy, has better mechanical properties, and the alloy has better filling capacity, corrosion resistance and lower The tendency of thermal cracking. Al-Si-Mg series alloy is the development target of new die-cast aluminum alloy, which can be used in car body
Parts with complex shapes and high requirements for comprehensive mechanical properties, but the subsequent processing of formed parts requires higher requirements, which will increase manufacturing costs.
1.1.4 Al-Si-Cu series alloy
The Cu element is added to the Al-Si-Cu series alloy. The solubility of Cu element in α-Al solid solution at room temperature is small, but the solubility is greater at high temperature, so that Cu element can be dissolved in the aluminum matrix in the alloy or form particles Shaped compound strengthening phases (mainly AlCu and Al 5 Cu 2 Mg 8 Si 6 phases) improve the creep resistance of the alloy and the strong hardness of the alloy. The addition of Cu element to Al-Si-Cu series alloys can increase the mechanical properties, casting properties and machinability of aluminum alloys
Yes, but the chemical potential difference between Al element and Cu element is large, which is easy to cause the corrosion resistance of the alloy to deteriorate, and the tendency to hot crack is higher. In the Al-Si-Cu die-casting alloy, the Cu content is generally controlled at 1%~ 5%. A383 alloy is an improved die-casting aluminum alloy based on the traditional A380 alloy in the United States. The Si content is closer to eutectic than A380, which improves the fluidity of the alloy. Its Cu element content is less, and there is a certain degree of hot cracking during the die-casting process. Tends to form a hot crack path.
The Role Of Other Elements In Aluminum Alloy
Fe element is an impurity element with great influence in die-casting aluminum alloy. Fe element easily reacts with Al, Si, Mg and other elements in aluminum alloy to form Al 3 Fe, Al 9 Fe 2 Si 2, Al 8 Mg 3 FeSi 6, etc. The phases are all hard and brittle phases, which are prone to cracks, and it is easy to accumulate impurity gas at the position of the phase, which reduces the mechanical properties of the alloy. The die-casting process is used to reduce the precipitation of the needle-like Fe-rich phase to a certain extent, so that it reduces the adverse effects on the matrix. In addition, the high content of Fe element will reduce the corrosion resistance and fluidity of aluminum alloy, and increase the hot cracking tendency and
Tendency to shrink holes.
The solubility of Zn element in the α-Al matrix is good, and it can form a solid solution, strengthen the mechanical properties of the alloy, improve its fluidity, and improve the mechanical processing performance of the alloy. But similar to the Cu element, due to the large difference in chemical potential between the Zn element and the Al in the alloy, the corrosion resistance of the die-cast aluminum alloy is poor, and the volume shrinkage rate of the Zn element in the alloy is as high as 4.7%, which makes the die-cast aluminum alloy have a higher The tendency to shrink.
Rare earth elements are often added to die-cast aluminum alloys. The atomic radius of rare earth elements is larger than that of Al element. The crystal structure of Al element is a face-centered cubic lattice, and the rare earth element is a close-packed hexagonal lattice. Therefore, rare earth elements are contained in aluminum alloys. The solubility is small, and it is not easy to form a solid solution. The addition of rare earth elements to aluminum alloys will be concentrated in front of the solid-liquid interface, causing excessive cooling of the composition, which can improve the mechanical properties of the aluminum alloy. Rare earth elements are more active and easy to fill when aluminum alloy is smelted.
The defects produced by the alloy phase reduce the surface tension between the two phases and form an active layer on the surface of the alloy grains to prevent the growth of the grains. For impurities such as Fe in the alloy, rare earth elements can react with them to purify the aluminum liquid and improve the Fe-rich impurity phase.
Please keep the source and address of this article for reprinting: The Material Classification Of Commonly Used Die-Cast Aluminum Alloy
Minghe Die Casting Company are dedicated to manufacture and provide quality and high performance Casting Parts(metal die casting parts range mainly include Thin-Wall Die Casting,Hot Chamber Die Casting,Cold Chamber Die Casting),Round Service(Die Casting Service,Cnc Machining,Mold Making,Surface Treatment).Any custom Aluminum die casting, magnesium or Zamak/zinc die casting and other castings requirements are welcome to contact us.
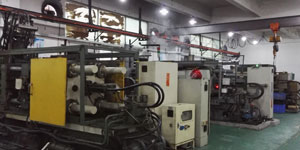
Under the control of ISO9001 and TS 16949,All processes are carried out through hundreds of advanced die casting machines, 5-axis machines, and other facilities, ranging from blasters to Ultra Sonic washing machines.Minghe not only has advanced equipment but also have professional team of experienced engineers,operators and inspectors to make the customer’s design come true.
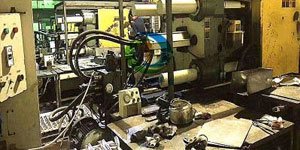
Contract manufacturer of die castings. Capabilities include cold chamber aluminum die casting parts from 0.15 lbs. to 6 lbs., quick change set up, and machining. Value-added services include polishing, vibrating, deburring, shot blasting, painting, plating, coating, assembly, and tooling. Materials worked with include alloys such as 360, 380, 383, and 413.
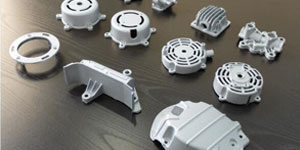
Zinc die casting design assistance/concurrent engineering services. Custom manufacturer of precision zinc die castings. Miniature castings, high pressure die castings, multi-slide mold castings, conventional mold castings, unit die and independent die castings and cavity sealed castings can be manufactured. Castings can be manufactured in lengths and widths up to 24 in. in +/-0.0005 in. tolerance.
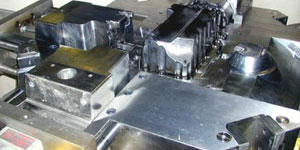
ISO 9001: 2015 certified manufacturer of die cast magnesium, Capabilities include high-pressure magnesium die casting up to 200 ton hot chamber & 3000 ton cold chamber, tooling design, polishing, molding, machining, powder & liquid painting, full QA with CMM capabilities, assembly, packaging & delivery.
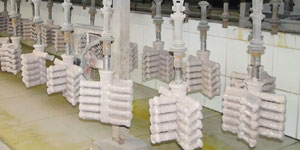
ITAF16949 certified. Additional Casting Service Include investment casting,sand casting,Gravity Casting, Lost Foam Casting,Centrifugal Casting,Vacuum Casting,Permanent Mold Casting,.Capabilities include EDI, engineering assistance, solid modeling and secondary processing.
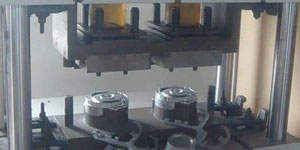
Casting Industries Parts Case Studies for: Cars, Bikes, Aircraft, Musical instruments, Watercraft, Optical devices, Sensors, Models, Electronic devices, Enclosures, Clocks, Machinery, Engines, Furniture, Jewelry, Jigs, Telecom, Lighting, Medical devices, Photographic devices, Robots, Sculptures, Sound equipment, Sporting equipment, Tooling, Toys and more.
What Can we help you do next?
∇ Go To Homepage For Die Casting China
→Casting Parts-Find out what we have done.
→Ralated Tips About Die Casting Services
By Minghe Die Casting Manufacturer |Categories: Helpful Articles |Material Tags: Aluminum Casting, Zinc Casting, Magnesium Casting, Titanium Casting, Stainless Steel Casting, Brass Casting,Bronze Casting,Casting Video,Company History,Aluminum Die Casting |Comments Off