Basic Knowledge Of Aluminum Alloy Die Casting Tooling
1. The Basic Definition Of Aluminum Alloy Die Casting Tooling
Mold making refers to the processing of forming and blank making tools. In addition, it also includes cutting die and die cutting tooling. In general, tooling consists of upper module and lower module. The steel plate is placed between the upper and lower dies, and the material is formed under the action of the press. When the press is opened, the workpiece determined by the tooling shape will be obtained or the corresponding waste will be removed. Parts as small as electronic connectors and as large as automobile dashboard can be molded with tooling.
Progressive die is a set of tooling that can automatically move the workpiece from one station to another, and get the molding part in the last station.
Tooling process includes: cutting die, blanking die, compound die, extrusion die, four slide die, progressive die, stamping die, die cutting tooling, etc.
2. Tooling Type
- (1) Metal stamping tooling: continuous die, single die, compound die, drawing die
- (2) Plastic molding mold: injection mold, extrusion mold, suction mold
- (3) Die casting tooling: zinc alloy die casting tooling, aluminum alloy die casting tooling
- (4) Forging tooling
- (5) Powder metallurgy tooling
- (6) Rubber tooling
3. Tooling Process
- Cutting: front die material, back die material, insert material, row position material and inclined jacking material;
- Open frame: front mold frame and back mold frame;
- Opening: front mold cavity opening, back mold cavity opening, parting line opening;
- Copper male: front die copper male, rear mold copper male, parting line angle clearance copper male;
- Wire cutting: insert parting line, copper male, oblique top pillow position;
- Computer gongs: fine gongs parting line, fine gongs after mold core;
- EDM: front mold thick, copper male, male mold line angle cleaning, back mold bone position, pillow position;
- Drilling, pinhole, thimble; tooling top pinhole waterway hole processing line position, row position pole;
- Oblique top, compound thimble, with thimble.
4 Others
- (1) Chui, code mould pit, garbage nail (limit nail);
- (2) Flying model;
- (3) Nozzle, support head, spring and water transportation;
- (4) The position of saving mould, polishing, front mould and back mould bone position;
- (5) Fine water structure, pull rod screw hook, spring
- (6) Heat treatment, quenching and nitriding of important parts;
5.Tooling Software
UGNX, Pro / NC, CATIA, master cam, SURFCAM, topsolid cam, space-e, camworks, worknc, tebis, hyperMILL, PowerMILL, gibbscam, featurecam, etc.
6. Basic Features
- (1) A pair of tooling is generally composed of a female die, a punch and a die base, and some of them may be multi piece assembly modules. Therefore, the combination of upper and lower dies, the combination of inserts and cavities, and the assembly of modules all require high machining accuracy. The dimensional accuracy of precision tooling is often up to μ m level.
- (2) The shape surface of some products, such as automobile covering parts, aircraft parts, toys and household appliances, is composed of a variety of curved surfaces, so the tooling cavity surface is very complex. Some surfaces have to be treated mathematically.
- (3) The production of small tooling in batch is not mass production. In many cases, only one delivery is produced.
- (4) There are many kinds of working procedures in the process of tooling, such as milling, boring, drilling, reaming and tapping.
- (5) The use of repeated production tooling has a long life. When a pair of tooling is used beyond its service life, it is necessary to replace it with a new one, so the production of tooling is often repetitive.
- (6) Sometimes there are neither drawings nor data in the production of profiling, and profiling processing should be carried out according to the actual object. This requires high precision and no deformation.
- (7) Tooling materials are excellent and have high hardness. The main materials of tooling are made of high-quality alloy steel, especially those with high life, which are often made of ledeburite steel such as Crl2 and CrWMn. This kind of steel has strict requirements from blank forging, processing to heat treatment. Therefore, the preparation of processing technology can not be ignored, heat treatment deformation is also a serious problem in processing.
According to the above characteristics, the selection of machine tools should meet the processing requirements as far as possible. For example, the function of CNC system should be strong, the precision of machine tool should be high, the rigidity should be good, the thermal stability should be good, and the profiling function should be provided.
7. Process flow arrangement
- (1) Bottom processing, processing quantity guarantee;
- (2) Casting blank benchmark alignment, 2D, 3D surface allowance inspection;
- (3) Rough machining of 2D and 3D profile, non installation and non working plane machining (including safety platform surface, buffer mounting surface, pressing plate plane and side datum plane);
- (4) Before semi finishing, the side datum plane should be found correctly to ensure the accuracy;
- (5) Semi finish machining 2D and 3D surfaces, finish machining all kinds of installation working surfaces (including limit block installation surface and contact surface, insert installation surface and back side, punch installation surface, waste cutter installation surface and back side, spring installation surface and contact surface, various travel limit working face, wedge installation surface and back face), semi finish all kinds of guide surfaces and guide holes, and make allowance for finishing Process datum hole and height datum, and record data;
- (6) Check and recheck the machining accuracy;
- (7) Fitter inlay process;
- (8) Before finishing, align the datum plane of process reference hole and check the insert allowance;
- (9) Finish machining profile 2D, 3D, side punch profile and hole position, finish machining process reference hole and height datum, finish machining guide surface and guide hole;
- (10) Check and recheck the machining accuracy.
8. Matters needing attention
(1) Process preparation is concise and detailed, and the processing content is expressed as numerically as possible;
(2) For the key and difficult points of processing, the craftsmanship should be particularly emphasized;
(3) It is necessary to combine processing locations, and the process is clearly expressed;
(4) When the insert needs to be processed separately, pay attention to the process requirements of the processing accuracy;
(5) After combined processing, for the insert parts that need to be processed separately, the process is equipped with the benchmark requirements for separate processing during combined processing;
(6) Springs are most easily damaged in mold processing, so mold springs with long fatigue life should be selected.
Processing problems of large aluminum alloy die-casting molds
1. Huge size and weight
When processing large molds, how to deal with its own huge size and weight is a major challenge facing processing companies. The processing of large molds often requires a lot of labor, special equipment, and multiple adjustments and clamping, and the processing accuracy is also affected by many potential factors and cannot be easily guaranteed.
2. The issue of acquisition cost
The largest cost directly related to the processing and production of various large molds is the purchase cost of the machine tool. The machine tool that can produce large molds is quite expensive, especially under the complex process arrangement, multiple machine tools are needed to complete all the processes from roughing to finishing of the mold. Such early high input costs are also the biggest obstacle for many companies to enter this market. From this, we can see that if the rough machining and finishing of large molds can be realized on a suitable machine tool, even if only one debugging and clamping is required, then many problems will be solved and the machining accuracy can be guaranteed.
Machining Center
1. Cast iron bed structure, machine tool spindle has heat dissipation function
Cast iron material has high rigidity and heat dissipation characteristics, so it is the most stable material for manufacturing machine tool structures. For any machine tool used for milling large parts, it first needs to have a very strong cast iron structure and be equipped with a spindle with heat dissipation function.
As far as the main shaft of the machine tool is concerned, it must use built-in cooling technology to cool the main shaft from the outside of the bearing to ensure that the main shaft itself will not be burnt out or lose precision due to thermal expansion during long-term machining. These factors are very important, because the processing of large molds takes a long time, and under heavy cutting conditions, this will increase the heat and stress of the mold. Therefore, the structural parts of the machine tool must have good rigidity and heat dissipation characteristics, which is the prerequisite for processing large-scale high-quality aluminum alloy die-casting molds. Therefore, it is necessary to limit the vibration of the machine tool during the machining process to the greatest extent and quickly diffuse the heat generated during the machining process. Choosing the right processing machine tools and tools can achieve a win-win situation in terms of cost and cycle time.
2. Thermal stability technology
Due to the long processing time, the influence of ambient temperature must also be considered. For example, processing a large aluminum alloy die-casting mold on an ordinary machine tool, when the ambient temperature changes by 10°C, will cause a 6°C temperature change in the machine tool column, which will cause a 0.07mm change in the parallelism of the spindle angle plate. Therefore, the design of the machine tool must take into account the effect of ambient temperature to avoid the influence of ambient temperature on the accuracy of processed parts.
3. Speed
For a large mold machining center that can move quickly, the spindle speed of the large mold processing machine tool should reach at least 20000r/min, and the metal cutting speed should meet 762~20000mm/min.
4. Precision
Precision control always runs through all stages of mold processing. If you need to implement rough machining and finishing of large molds on a machining center, you must strictly control the positioning accuracy and repeat positioning accuracy of the machine tool. The machining center dedicated for large molds generally has a positioning accuracy of ±1.5μm, and a repeat positioning accuracy of ±1μm. At the same time, its pitch accuracy should be kept within 5μm.
5. Feedback resolution
For high-precision surface processing, the feedback resolution of the machine tool itself is very important for detecting the accuracy of the processed parts. With the standard 1μm feedback resolution, the results usually obtained are not very satisfactory. If the resolution can reach 0.05μm, then its finishing result is almost without any flaws. Moreover, through the control of machine tool resolution, scale feedback and small pitch ball screws, the processing quality of the part surface can be further improved.
6. Spindle
The spindle used on the large mold machining center must meet the requirements of rough machining, semi-finishing and high-quality finishing, and as a reference standard, the surface machining quality that can be achieved should be controlled at the level of 2μm. Usually, it is very important for the finishing of the mold closing surface and parting line part, but under the traditional technology, many mold manufacturers have to use manual polishing to make up for the lack of tool machining accuracy. Because large-scale processing machine tools are expensive to build, it is obviously impractical to purchase a multifunctional machine tool for this process.
In addition, a reasonable spindle design must be able to maximize the service life of the tool so that it can continue to work with low vibration and low temperature rise during the processing cycle. For example, when processing automobile dashboard molds on a large mold machining center, if a 16mmCBN insert is used for finishing tools, the processing speed can reach 8m/min, the service life exceeds 30h, and the quality of the processed surface can be controlled within 0.336~3.2μm. It can be seen that, considering the increase in tool costs when processing large molds, the use of specially designed large mold processing machine tools can not only extend the service life of the tools, but also save a lot of tool costs for processing each mold.
7. Movable multi-axis machining head
Due to the limitation of mold size and weight, it usually takes a long time to clamp the workpiece. Therefore, the use of a 3-axis machining center not only reduces the number of debugging and clamping times of the workpiece, but also does not affect the machining accuracy of the machine tool, thereby greatly improving the production capacity of the workshop for processing large molds.
The movable multi-axis machining head can be used to process large molds with particularly complex structures. The machining head designed according to the variable geometry allows 3-axis simultaneous machining. Only one clamping of the workpiece can be used to mill and process deep cavities. Molds and cooling holes, as well as cutting many other parts with complex geometries. For example, when the spindle is inclined at an optimal angle, the proximity of the processing head to the milling processing point can be increased, so that the multi-axis processing head can be used to complete the processing of the oblique hole.
In addition, since the multi-axis machining head processes the surface of the workpiece, the radius edge of the tool is used instead of the tip of the tool, so the surface roughness can be improved.
8. Chip management
A large amount of chips will be generated during metal cutting. If it cannot be eliminated in time, it will inevitably lead to secondary cutting and cause the temperature rise of machine tool structural parts or workpiece surfaces. There are usually 18 chip holes under the worktable of a large mold machining center, no matter where the worktable is moved, the chips can be reliably removed. There are 4 built-in hinged chip conveyor belts on the machine tool, which send the chips to the front of the machine tool at a high speed.
9. High pressure coolant
When processing large molds, high-pressure coolant plays a very important role. For example, when using the 2+3 axis machining method to drill inclined holes, a coolant with a pressure of 1000psi (1psi=6890Pa) is required to effectively remove the chips and achieve higher precision cutting. If there is no such high-pressure coolant, additional machine tools need to be added when processing inclined holes, a secondary installation is required, which reduces processing accuracy and increases cycle costs. According to the above analysis, it can be seen that the simple processing of large molds requires the machine tool to have more and better functions. The new MCC2516VG 3-axis horizontal machining center developed by Makino, the spindle speed can reach 15000r/min, and adopts the "shaft core cooling" method and the "bearing internal pressure lubrication" function to ensure that the spindle and its attached bearings can be cooled in time and effectively .
In addition, the main shaft can not only move along the horizontal X axis, the vertical Y axis and the front and rear Z axis directions, but can also rotate with the A axis and the C axis. With two indexing functions, it can not only reduce the workload of adjustment, but also cut complex workpieces, such as bumpers, instrument panels, and automobile headlight lenses.
Please keep the source and address of this article for reprinting:Basic Knowledge Of Aluminum Alloy Die Casting Tooling
Minghe Die Casting Company are dedicated to manufacture and provide quality and high performance Casting Parts(metal die casting parts range mainly include Thin-Wall Die Casting,Hot Chamber Die Casting,Cold Chamber Die Casting),Round Service(Die Casting Service,Cnc Machining,Mold Making,Surface Treatment).Any custom Aluminum die casting, magnesium or Zamak/zinc die casting and other castings requirements are welcome to contact us.
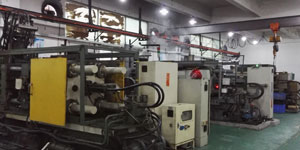
Under the control of ISO9001 and TS 16949,All processes are carried out through hundreds of advanced die casting machines, 5-axis machines, and other facilities, ranging from blasters to Ultra Sonic washing machines.Minghe not only has advanced equipment but also have professional team of experienced engineers,operators and inspectors to make the customer’s design come true.
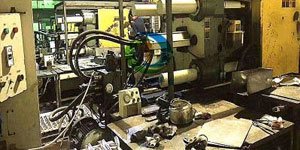
Contract manufacturer of die castings. Capabilities include cold chamber aluminum die casting parts from 0.15 lbs. to 6 lbs., quick change set up, and machining. Value-added services include polishing, vibrating, deburring, shot blasting, painting, plating, coating, assembly, and tooling. Materials worked with include alloys such as 360, 380, 383, and 413.
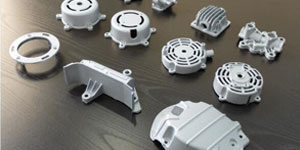
Zinc die casting design assistance/concurrent engineering services. Custom manufacturer of precision zinc die castings. Miniature castings, high pressure die castings, multi-slide mold castings, conventional mold castings, unit die and independent die castings and cavity sealed castings can be manufactured. Castings can be manufactured in lengths and widths up to 24 in. in +/-0.0005 in. tolerance.
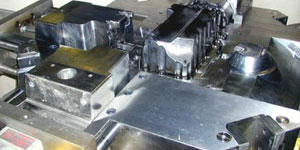
ISO 9001: 2015 certified manufacturer of die cast magnesium, Capabilities include high-pressure magnesium die casting up to 200 ton hot chamber & 3000 ton cold chamber, tooling design, polishing, molding, machining, powder & liquid painting, full QA with CMM capabilities, assembly, packaging & delivery.
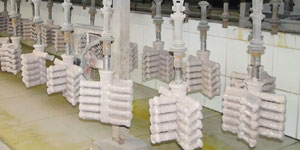
ITAF16949 certified. Additional Casting Service Include investment casting,sand casting,Gravity Casting, Lost Foam Casting,Centrifugal Casting,Vacuum Casting,Permanent Mold Casting,.Capabilities include EDI, engineering assistance, solid modeling and secondary processing.
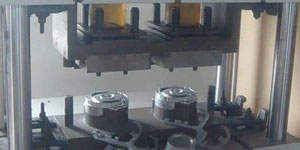
Casting Industries Parts Case Studies for: Cars, Bikes, Aircraft, Musical instruments, Watercraft, Optical devices, Sensors, Models, Electronic devices, Enclosures, Clocks, Machinery, Engines, Furniture, Jewelry, Jigs, Telecom, Lighting, Medical devices, Photographic devices, Robots, Sculptures, Sound equipment, Sporting equipment, Tooling, Toys and more.
What Can we help you do next?
∇ Go To Homepage For Die Casting China
→Casting Parts-Find out what we have done.
→Ralated Tips About Die Casting Services
By Minghe Die Casting Manufacturer |Categories: Helpful Articles |Material Tags: Aluminum Casting, Zinc Casting, Magnesium Casting, Titanium Casting, Stainless Steel Casting, Brass Casting,Bronze Casting,Casting Video,Company History,Aluminum Die Casting |Comments Off