The Analysis Of Mn-V Alloy Steel Weldability For Brake Hub
With the development and application of a large number of ultra-deep well drilling rigs, the load of the lifting system of the drilling rig is getting heavier, and the requirements for the safety and stability of the drawworks brake system are getting higher and higher. Usually the drawworks brake system is composed of main brake and auxiliary brake. As the key force component of the main brake of the drawworks brake system of drilling rigs and workover rigs, brake hubs are under severe stress conditions and are easily damaged. Take belt-type water-cooled brakes as an example. During drilling rig operation, the surface temperature of the brake hub can reach 650°C from the end of braking. Under the action of the internal circulating water, the temperature of the brake hub drops rapidly, which alternately cycle. Under the action of alternating thermal strain, the material of the brake hub forms a tortoise crack through the accumulation of vacancies; at the same time, the hardness decreases at high temperatures, the friction pairs are easy to dissolve each other, and the oxidation rate of the material increases, thereby increasing the wear rate. The brake hub works under chilled and heated conditions, and the main failure modes are thermal fatigue surface cracking and wear.
In order to meet the requirements of ultra-deep well drilling, a lot of work has been done to deal with excessive wear and thermal fatigue cracking of the drawworks brake hub. On the one hand, through technological innovation, the wear resistance of the material is improved, and the service life of the brake hub is prolonged. For example, a layer of wear-resistant material is surfacing welded on the Q345A matrix to improve the wear resistance of the brake hub, or a cast structure is used instead, and a denser, finer and uniform structure is obtained through forging, thereby improving the wear resistance of the material. On the other hand, develop new wear-resistant materials and composite materials, such as adding rare earth to Cr-Mo steel to improve the wear resistance and thermal strength of the brake hub, and increase the service life of the brake hub. However, the production efficiency of the surfacing method is low, and it is usually only used as the size repair after the brake hub is worn; forging the brake hub requires large-scale ring rolling equipment, and the heating process is increased, which increases the production cost; Cr-Mo steel contains precious metals, which increases Material costs. Therefore, it is of great engineering significance to develop a new type of low-cost, high-wear-resistant cast brake hub material to extend the service life of the brake hub.
The Mn-V alloy used in this article is a new material independently developed by a domestic petroleum equipment company. It has good thermal strength and wear resistance, and can meet the requirements of the use of brake hubs under severe working conditions. Good economic benefits. However, through the author's investigation and oilfield statistics, it is found that the welded joints of this material are prone to cracking during long-term use, which affects the application of this material to a certain extent. This article analyzes the welding samples of the material in order to improve the welding performance of the material.
The experimental test board is made of alkaline phenolic resin sand casting. The proportion of resin sand is 1.6% resin, 0.4% curing agent, and the rest is sand. The sand is a mixture of new sand and old sand, and the ratio of new sand to old sand is 1:3. After cutting the riser, the casting is normalized at 1100℃. Normalizing heat preservation time is 6h. After normalizing, the casting blank is machined into a test plate of 530mm×180mm×25mm, with a 60°V groove, and using Φ1.2mm JQ•MG50-6 welding wire for GMAW multi-layer multi-pass welding. Preheat the sample to 150°C before welding, control the interlayer temperature not to exceed 300°C, and slowly cool after welding.
After the brake hub is welded with Mn-V steel, the joint has a certain degree of hardenability, which is easy to cause brittle cracking of the joint. After welding, the joint is treated with aging treatment, the plastic toughness of the welded joint is improved, and the comprehensive mechanical properties of the joint are improved through the strengthening of the second phase and the fine-grained strengthening. Aging at 500°C for 30 minutes, the sample obtained the best mechanical properties, with a yield strength of 560MPa and a tensile strength of 715MPa. The heat-affected zone is the weak link of the entire joint, and the tensile specimens all fracture in the heat-affected zone of the welded joint. The aging treatment of the brake hub after welding can improve the plastic toughness of the joint, and the joint will turn from brittle fracture to ductile fracture after aging. When the aging temperature exceeds 300°C and the aging time is 30 minutes, it is manifested as plastic fracture.
Please keep the source and address of this article for reprinting: The Analysis Of Mn-V Alloy Steel Weldability For Brake Hub
Minghe Die Casting Company are dedicated to manufacture and provide quality and high performance Casting Parts(metal die casting parts range mainly include Thin-Wall Die Casting,Hot Chamber Die Casting,Cold Chamber Die Casting),Round Service(Die Casting Service,Cnc Machining,Mold Making,Surface Treatment).Any custom Aluminum die casting, magnesium or Zamak/zinc die casting and other castings requirements are welcome to contact us.
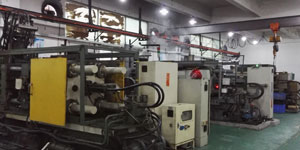
Under the control of ISO9001 and TS 16949,All processes are carried out through hundreds of advanced die casting machines, 5-axis machines, and other facilities, ranging from blasters to Ultra Sonic washing machines.Minghe not only has advanced equipment but also have professional team of experienced engineers,operators and inspectors to make the customer’s design come true.
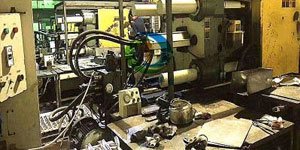
Contract manufacturer of die castings. Capabilities include cold chamber aluminum die casting parts from 0.15 lbs. to 6 lbs., quick change set up, and machining. Value-added services include polishing, vibrating, deburring, shot blasting, painting, plating, coating, assembly, and tooling. Materials worked with include alloys such as 360, 380, 383, and 413.
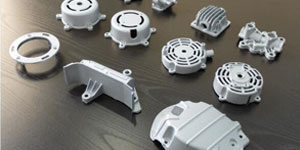
Zinc die casting design assistance/concurrent engineering services. Custom manufacturer of precision zinc die castings. Miniature castings, high pressure die castings, multi-slide mold castings, conventional mold castings, unit die and independent die castings and cavity sealed castings can be manufactured. Castings can be manufactured in lengths and widths up to 24 in. in +/-0.0005 in. tolerance.
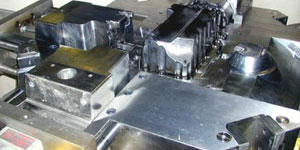
ISO 9001: 2015 certified manufacturer of die cast magnesium, Capabilities include high-pressure magnesium die casting up to 200 ton hot chamber & 3000 ton cold chamber, tooling design, polishing, molding, machining, powder & liquid painting, full QA with CMM capabilities, assembly, packaging & delivery.
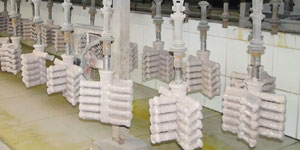
ITAF16949 certified. Additional Casting Service Include investment casting,sand casting,Gravity Casting, Lost Foam Casting,Centrifugal Casting,Vacuum Casting,Permanent Mold Casting,.Capabilities include EDI, engineering assistance, solid modeling and secondary processing.
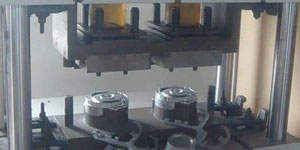
Casting Industries Parts Case Studies for: Cars, Bikes, Aircraft, Musical instruments, Watercraft, Optical devices, Sensors, Models, Electronic devices, Enclosures, Clocks, Machinery, Engines, Furniture, Jewelry, Jigs, Telecom, Lighting, Medical devices, Photographic devices, Robots, Sculptures, Sound equipment, Sporting equipment, Tooling, Toys and more.
What Can we help you do next?
∇ Go To Homepage For Die Casting China
→Casting Parts-Find out what we have done.
→Ralated Tips About Die Casting Services
By Minghe Die Casting Manufacturer |Categories: Helpful Articles |Material Tags: Aluminum Casting, Zinc Casting, Magnesium Casting, Titanium Casting, Stainless Steel Casting, Brass Casting,Bronze Casting,Casting Video,Company History,Aluminum Die Casting |Comments Off