China independent research and development of AKR composite desulfurization process
The AKR composite desulfurization process, independently developed by Anshan Iron and Steel, which combines the injection desulfurization process and the KR desulfurization process, has achieved remarkable results after preliminary industrial applications. The desulfurization powder per ton of iron—passivated metal magnesium powder and passivated lime powder have been reduced by nearly 30%. Provide strong technical support to further reduce smelting costs.
Desulfurization pretreatment of molten iron is an important means for the modern steel industry to optimize technological processes and improve smelting quality. At present, there are two mainstream desulfurization methods, namely injection method and KR desulfurization method. The equipment of the injection method is complicated. Compared with the KR process, the one-time investment is large. At the same time, because the injection process adopts the magnesium powder and calcium powder process, the desulfurization flux cost of the injection process is much higher than that of the KR process. The KR stirring desulfurization method has obvious advantages, because of the good kinetic conditions, low unit consumption of desulfurizer, and ideal desulfurization effect and cost, but the investment in new construction is relatively high. Due to historical reasons, except for the third branch D and E converters for KR desulfurization, the other converters are all injection desulfurization.
In the process of challenging the extreme cost and reducing costs and increasing efficiency, the plant has set its sights on reducing the cost of molten iron injection desulfurization powder. The more advanced KR desulfurization system that has been launched saves time and effort, and can also achieve the goal of reducing the cost of powder injection, but the investment and time costs of new equipment are very high. Under this premise, the steelmaking plant decided to combine the existing process conditions, creatively transform the current injection process, and integrate the KR desulfurization process principle into the existing powder injection desulfurization process to achieve low-cost transformation and high-efficiency cost reduction. the goal.
The first branch of Anshan Iron and Steel Co., Ltd. Steelmaking Plant, which undertakes specific research and development tasks, acted immediately. On the one hand, based on the existing injection process equipment and fully borrowed from the KR desulfurization process principle, the plant’s injection desulfurization equipment was transformed and a new type of rotary was developed. The paddleless T-type spray gun improves the equipment dynamics conditions, expands the stirring range and the reaction interface, and enhances the stirring desulfurization effect. On the other hand, the process equipment parameters are explored and determined. After more than two months of orthogonal experiments, the final confirmation of each Optimal interval of item process parameters.
After more than two months, the data of 270 cans of molten iron shows that the AKR composite desulfurization process, which integrates the KR desulfurization process principle, not only has a higher desulfurization efficiency, but also meets the process requirements for the desulfurization effect. It also saves on the use of desulfurization powder. The two powders, passivated metal magnesium powder and passivated lime powder per ton of iron, were reduced by 25.3% and 28.9%, respectively, reaching the expected target. This composite desulfurization process is also named "AKR desulfurization process", which means the KR stirring desulfurization process independently developed by Anshan Iron and Steel.
Please keep the source and address of this article for reprinting: China independent research and development of AKR composite desulfurization process
Minghe Die Casting Company are dedicated to manufacture and provide quality and high performance Casting Parts(metal die casting parts range mainly include Thin-Wall Die Casting,Hot Chamber Die Casting,Cold Chamber Die Casting),Round Service(Die Casting Service,Cnc Machining,Mold Making,Surface Treatment).Any custom Aluminum die casting, magnesium or Zamak/zinc die casting and other castings requirements are welcome to contact us.
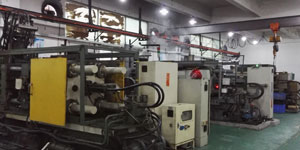
Under the control of ISO9001 and TS 16949,All processes are carried out through hundreds of advanced die casting machines, 5-axis machines, and other facilities, ranging from blasters to Ultra Sonic washing machines.Minghe not only has advanced equipment but also have professional team of experienced engineers,operators and inspectors to make the customer’s design come true.
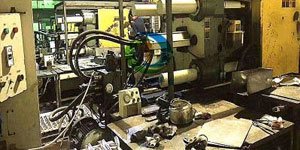
Contract manufacturer of die castings. Capabilities include cold chamber aluminum die casting parts from 0.15 lbs. to 6 lbs., quick change set up, and machining. Value-added services include polishing, vibrating, deburring, shot blasting, painting, plating, coating, assembly, and tooling. Materials worked with include alloys such as 360, 380, 383, and 413.
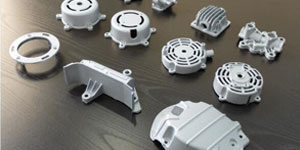
Zinc die casting design assistance/concurrent engineering services. Custom manufacturer of precision zinc die castings. Miniature castings, high pressure die castings, multi-slide mold castings, conventional mold castings, unit die and independent die castings and cavity sealed castings can be manufactured. Castings can be manufactured in lengths and widths up to 24 in. in +/-0.0005 in. tolerance.
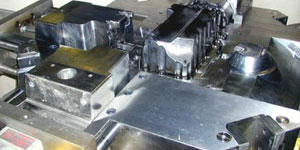
ISO 9001: 2015 certified manufacturer of die cast magnesium, Capabilities include high-pressure magnesium die casting up to 200 ton hot chamber & 3000 ton cold chamber, tooling design, polishing, molding, machining, powder & liquid painting, full QA with CMM capabilities, assembly, packaging & delivery.
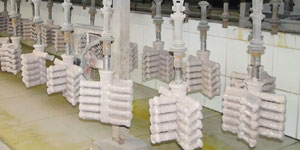
ITAF16949 certified. Additional Casting Service Include investment casting,sand casting,Gravity Casting, Lost Foam Casting,Centrifugal Casting,Vacuum Casting,Permanent Mold Casting,.Capabilities include EDI, engineering assistance, solid modeling and secondary processing.
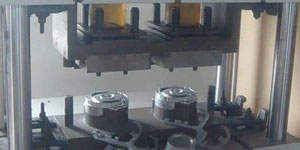
Casting Industries Parts Case Studies for: Cars, Bikes, Aircraft, Musical instruments, Watercraft, Optical devices, Sensors, Models, Electronic devices, Enclosures, Clocks, Machinery, Engines, Furniture, Jewelry, Jigs, Telecom, Lighting, Medical devices, Photographic devices, Robots, Sculptures, Sound equipment, Sporting equipment, Tooling, Toys and more.
What Can we help you do next?
∇ Go To Homepage For Die Casting China
→Casting Parts-Find out what we have done.
→Ralated Tips About Die Casting Services
By Minghe Die Casting Manufacturer |Categories: Helpful Articles |Material Tags: Aluminum Casting, Zinc Casting, Magnesium Casting, Titanium Casting, Stainless Steel Casting, Brass Casting,Bronze Casting,Casting Video,Company History,Aluminum Die Casting |Comments Off