Typical Casting Defects Of Multiphase Ductile Iron Grinding Balls
The multiphase ductile iron grinding ball is a project product developed by the electromechanical repair and fitting factory, and it is an upgraded product of the original low-alloy grinding ball. The mechanical and electrical repairing plant has an annual output of nearly 10,000 tons of this type of grinding balls. In actual production, due to the existence of different types of defects, the grinding balls are used under actual working conditions, and often non-wear, out-of-roundness, etc. affect the use of the grinding balls. For the unfavorable factors of quality, it is necessary to analyze all kinds of defects one by one, and formulate corresponding prevention methods to guide production practice.
Common defects and features
Poor spheroidization and spheroidization decline
Poor spheroidization means that the spheroidization treatment does not meet the spheroidization level requirements. Spheroidization decline means that the residual amount of spheroidizing elements in the grinding ball at the later stage of casting is too low to cause the spheroidization to fail. Both have the same defect characteristics.
Macroscopic characteristics: The fracture of the casting is silver-gray with black sesame spots distributed on it. The large number and large diameter indicate a serious degree. All are dark gray coarse grains, indicating no spheroidization at all.
Metallographic structure: a large number of thick flake graphite is concentratedly distributed. The more the quantity and the increase in area ratio, it indicates that the degree is serious, and the one with no spheroidization is flake graphite.
Cause: The raw molten iron contains high sulfur and the severely oxidized charge contains excessive de-spheroidizing elements; the residual magnesium and rare earth contents in the molten iron after treatment are too low. High dissolved oxygen in molten iron is an important reason for poor spheroidization.
Choose low-sulfur coke and low-sulfur metal charge, desulfurize when necessary, remove rust from scrap steel, increase the amount of rare earth elements in the spheroidizing agent when necessary, and strictly control the spheroidizing process.
2.2 Shrinkage cavity and shrinkage porosity
Features and causes: Shrinkage occurs when the temperature of the molten iron drops and shrinks once. If the atmospheric pressure sinks the solid thin layer on the surface, it will show surface depressions and local hot joint depressions. Otherwise, the gas in the molten iron will precipitate into the top shell and gather into the smooth dark shrinkage holes on the inner wall of the air holes, which sometimes communicate with the outside world to form bright cavities. Shrinkage cavity, although the inner surface is smooth, but it has been oxidized. The eutectic solidification time of nodular cast iron is longer than that of gray cast iron, and it solidifies in a porridge shape. The solidified shell is weaker. During the second expansion, the shell expands under the action of graphitization expansion force, which relaxes the internal pressure. Therefore, in the second shrinking process, the internal pressure of the last solidified hot joint is lower than atmospheric pressure, and the small molten pool separated by dendrites becomes a vacuum zone. After complete solidification, it becomes a rough hole filled with dendrites. That is, shrinkage defects. What is visible to the naked eye is called macroscopic shrinkage. It occurs in the early stage when the residual molten iron in the hot joint area begins to solidify in a large amount. It includes the primary and secondary shrinkage of the residual molten iron, so the size is slightly larger and the inner wall is full of dendrites, which is gray and dark. Loose holes or black spots like fly feet. What is visible under the microscope is called microscopic shrinkage. It is produced at the end of secondary contraction. The molten iron in the eutectic group or its group cannot be fed under negative pressure. It is formed by solidification and shrinkage, which is common in thick sections.
2.3 Subcutaneous stomata
Morphological characteristics: spherical, elliptical or pinhole-like smooth holes on the inner wall of the casting surface 2-3mm uniformly or honeycombly distributed, with a diameter of 0.5-3mm, which can be found after heat treatment and shot blasting, exposure or machining, small There are more of them.
Reasons for formation: The surface tension of the magnesium-containing iron liquid is large, and it is easy to form an oxide film, which hinders the discharge of the precipitated gas and the invading gas, and is formed by staying under the skin. The temperature of the forming film increases with the increase of the amount of residual magnesium, which intensifies its hindering effect. Thin-walled (7-20mm) parts cool quickly and form the film early, which is easy to form this defect. The gas source is mainly the magnesium vapor precipitated from the molten iron during the cooling process, and the molten iron rolls up during the filling process. Magnesium in the molten iron reacts with the moisture of the molding sand. Magnesium acts as a catalyst to promote the reaction between carbon and the moisture of the molding sand. Magnesium makes the iron with increased activity react with the moisture. The reaction of water, magnesium and carbides to produce acetylene decomposition may produce hydrogen. In addition, wet and rusty furnace charge, wet ferrosilicon and intermediate alloys, and cupola high-temperature blast can bring in hydrogen. A small amount of Al (0.02%-0.03%) can significantly increase subcutaneous pores. Medium manganese ductile iron contains more nitrogen. The sand core resin binder contains more nitrogen, and the above-mentioned factors can promote the formation of this defect. The paste-like solidification characteristic of ductile iron causes the gas passage to be blocked earlier and also promotes its formation.
2.4 Stress deformation and cracks
Formation reasons and morphological characteristics: during the cooling process of the casting, the algebraic sum of the shrinkage stress, thermal stress and phase transformation stress, that is, the casting stress exceeds the fracture resistance of the section metal, and then cracks are formed. Under high temperature (1150-1000℃), thermal cracks are formed, showing dark brown uneven fractures. Cold cracks appear in the elastic range below 600°C, with light brown smooth and straight fractures. Plastic deformation can occur when the casting stress exceeds the yield limit above 600°C. When the composition of nodular cast iron is normal, it is not easy to crack.
Influencing factors: Factors that increase the tendency of white mouth, such as low carbon and silicon content, increased carbide forming elements, insufficient incubation, and excessive cooling, can all increase casting stress and cold cracking tendency. Phosphorus increases the tendency of cold cracking, and P>0.25 can also cause hot cracking. The wall thickness of castings varies greatly, the shape is complex, and deformation and cracks are easy to occur.
2.5 Slag inclusion
Morphological characteristics: Distributed on the upper surface of the casting position, under the core and at the dead corner of the casting. Dark black and matt inclusions of different depths appear on the broken surface, intermittently distributed. Metallographic observation can show strip-shaped and block-shaped inclusions, and adjacent graphite can be in the shape of flakes or spheres. During magnetic particle inspection, the magnetic marks are distributed in strips, and the stripes are thick and dense, indicating serious slag inclusion. Electron probe analysis shows that the slag contains Mg, Si, O, S, C, A1, etc., and is composed of magnesium silicate, oxygen-sulfur compounds, magnesium spinel, etc.
Formation process: Mg and RE react with O and S in molten iron to form slag during spheroidization. When the temperature of the molten iron is low, the effect of the thin slag agent is not good, the slag floating is insufficient or the slag is not cleaned and remains in the molten iron, this is a primary slag. When the molten iron is transported, poured, poured, and filled and rolled, the oxide film is broken and is drawn into the mold, floating in the mold, adsorbing sulfide and gathering on the upper surface or dead corners, which is the secondary slag. Generally, secondary slag is the mainstay.
3. Preventive measures
3.1 Causes of spheroidization decline and preventive measures
The sulfide and oxide slag formed after the spheroidization treatment of high-sulfur and low-temperature oxidation of the molten iron are not fully floated, the slag is not adequately removed, and the molten iron is not covered well. The oxygen in the air passes through the slag layer or directly enters the molten iron. Effective oxidation of spheroidizing elements and increasing active oxygen are important reasons for the decline of spheroidization. The sulphur in the slag can also re-enter the molten iron to consume the spheroidizing elements in it. During the transportation, stirring, and dumping of the molten iron, magnesium accumulates, floats, and is oxidized, thus reducing the effective residual spheroidizing elements and causing spheroidization to decline. In addition, the gestational decline also reduces the number of graphite spheres and leads to deterioration of graphite morphology. The above factors that cause poor spheroidization also accelerate the decline of spheroidization.
The sulfur and oxygen content of the original molten iron should be reduced as much as possible, and the temperature should be appropriately controlled. Slag thinner can be added to fully float the slag and fully remove the slag. After removing the slag, add grass ash, cryolite powder, graphite powder or other covering agents to isolate the air. Adding a cover or using a sealed pouring ladle, and using nitrogen or argon protection can effectively prevent the spheroidization from declining. Pouring should be speeded up, and the time of unloading, transportation and staying should be minimized. The use of yttrium-based heavy rare earth magnesium spheroidizing agent can extend the decay time by 1.5-2 times, and the decay time of light rare earth magnesium spheroidizing agent is slightly longer than that of magnesium spheroidizing agent. If necessary, the addition amount of spheroidizing agent can also be appropriately increased. The graphite morphology deteriorated due to the incubation decline, which can be improved after supplementation.
3.2 Influencing factors and preventive measures for shrinkage and porosity
Low carbon equivalent increases the tendency of shrinkage cavities and porosity. The phosphorus eutectic weakens the strength of the solidified shell, and the ternary phosphorus eutectic reduces the graphitization expansion, so the high phosphorus content significantly increases the shrinkage tendency. Molybdenum increases the stability of carbides, especially under high phosphorus conditions, it is easy to form carbide-phosphorus eutectic composites, and it also increases the tendency of shrinkage and shrinkage. Too high residual magnesium increases the tendency of shrinkage porosity and shrinkage cavities, a moderate amount of residual rare earth can reduce shrinkage porosity, and too high an increase the tendency of both. Therefore, the carbon equivalent of the molten iron should be increased, the phosphorus content should be reduced, the residual amount of rare earth magnesium should be reduced as much as possible under the guaranteed spheroidization conditions, and the molybdenum should be used rationally. Improve the rigidity of the mold, such as high-pressure molding, wax sand mold, and metal mold sand coating can reduce shrinkage and shrinkage, while increasing the carbon equivalent of molten iron, appropriately reducing the pouring temperature, and using a thin and wide inner runner to make it expand in the second time. Before solidification and sealing, graphitization expansion is used to compensate for liquid iron shrinkage and solidification shrinkage, which can eliminate shrinkage and porosity.
3.3 Preventive measures for subcutaneous pores: The pouring temperature shall not be lower than 1300°C. When the residual magnesium content is high, the pouring temperature should be increased accordingly; the residual magnesium content should be reduced as much as possible under the guaranteed spheroidization condition, and rare earths should be used appropriately; the open multi-runner pouring system is adopted to make the molten iron flow smoothly into the cavity and avoid the cavity Turn inward to control the moisture content of the molding sand ≤ 4.5% one s. 5%, mixed with coal powder 8%-15% can be burned into CO, inhibit the reaction of water vapor and magnesium to form H2 (spraying spindle oil on the surface of the mold can also play the same role); the surface of the mold is removed from cryolite powder and reacts with water vapor at high temperatures The formation of HF gas protects the molten iron from reaction and controls the low aluminum content of the molten iron. Strictly control the drying of the furnace charge and reduce the rust, the cupola dehumidification and air supply, reduce the gas in the molten iron, and use the resin sand with less or no nitrogen, etc.
3.4 Measures to prevent stress, deformation and cracks: appropriately increase carbon equivalent, reduce phosphorus content, strengthen inoculation, and necessary casting process measures.
3.5 Influencing factors of slag inclusion and preventive measures: The important reason for the formation of slag inclusion is the high sulfur content of the original molten iron and serious oxidation. The fundamental preventive measures are to reduce the sulfur and oxygen content of the original molten iron and increase the temperature. The main reason for the formation of secondary slag is that the amount of residual magnesium is too high, which increases the temperature of oxide film formation. The main measure is to minimize the residual magnesium content (small and medium-sized parts not exceeding 0.055%) under the conditions of ensuring spheroidization. Adding a proper amount of rare earth can reduce the film forming temperature; add 0.16% cryolite during the spheroidization treatment, and then sprinkle 0.3% on the surface after treatment , Used to dilute slag and generate A1F3 gas and MgF2 film to reduce secondary oxidation. This method is mainly used to prevent slag inclusion in large parts, and the pouring temperature should not be lower than 1300 ℃, making the pouring temperature higher than the film forming temperature, which can prevent secondary slag formation. The gating system should be designed so that the filling is stable, and the slag discharge riser is set at the location prone to sand inclusion. The installation of a filter can prevent the primary slag from entering the cavity.
Please keep the source and address of this article for reprinting:Typical Casting Defects Of Multiphase Ductile Iron Grinding Balls
Minghe Die Casting Company are dedicated to manufacture and provide quality and high performance Casting Parts(metal die casting parts range mainly include Thin-Wall Die Casting,Hot Chamber Die Casting,Cold Chamber Die Casting),Round Service(Die Casting Service,Cnc Machining,Mold Making,Surface Treatment).Any custom Aluminum die casting, magnesium or Zamak/zinc die casting and other castings requirements are welcome to contact us.
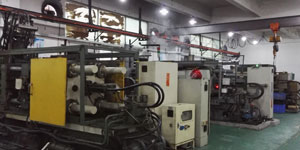
Under the control of ISO9001 and TS 16949,All processes are carried out through hundreds of advanced die casting machines, 5-axis machines, and other facilities, ranging from blasters to Ultra Sonic washing machines.Minghe not only has advanced equipment but also have professional team of experienced engineers,operators and inspectors to make the customer’s design come true.
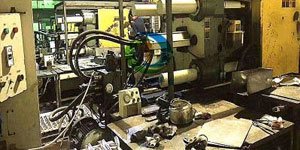
Contract manufacturer of die castings. Capabilities include cold chamber aluminum die casting parts from 0.15 lbs. to 6 lbs., quick change set up, and machining. Value-added services include polishing, vibrating, deburring, shot blasting, painting, plating, coating, assembly, and tooling. Materials worked with include alloys such as 360, 380, 383, and 413.
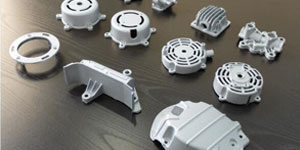
Zinc die casting design assistance/concurrent engineering services. Custom manufacturer of precision zinc die castings. Miniature castings, high pressure die castings, multi-slide mold castings, conventional mold castings, unit die and independent die castings and cavity sealed castings can be manufactured. Castings can be manufactured in lengths and widths up to 24 in. in +/-0.0005 in. tolerance.
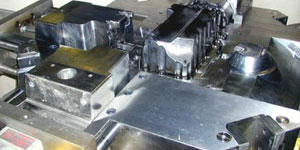
ISO 9001: 2015 certified manufacturer of die cast magnesium, Capabilities include high-pressure magnesium die casting up to 200 ton hot chamber & 3000 ton cold chamber, tooling design, polishing, molding, machining, powder & liquid painting, full QA with CMM capabilities, assembly, packaging & delivery.
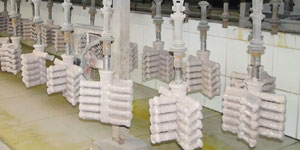
ITAF16949 certified. Additional Casting Service Include investment casting,sand casting,Gravity Casting, Lost Foam Casting,Centrifugal Casting,Vacuum Casting,Permanent Mold Casting,.Capabilities include EDI, engineering assistance, solid modeling and secondary processing.
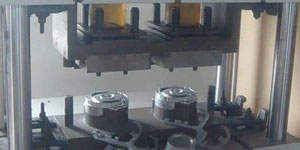
Casting Industries Parts Case Studies for: Cars, Bikes, Aircraft, Musical instruments, Watercraft, Optical devices, Sensors, Models, Electronic devices, Enclosures, Clocks, Machinery, Engines, Furniture, Jewelry, Jigs, Telecom, Lighting, Medical devices, Photographic devices, Robots, Sculptures, Sound equipment, Sporting equipment, Tooling, Toys and more.
What Can we help you do next?
∇ Go To Homepage For Die Casting China
→Casting Parts-Find out what we have done.
→Ralated Tips About Die Casting Services
By Minghe Die Casting Manufacturer |Categories: Helpful Articles |Material Tags: Aluminum Casting, Zinc Casting, Magnesium Casting, Titanium Casting, Stainless Steel Casting, Brass Casting,Bronze Casting,Casting Video,Company History,Aluminum Die Casting |Comments Off