The Method And Application Of Sand-Coated Iron Mold Casting
What Is Sand-Coated Iron Mold Casting
Iron mold sand-coated casting is a casting process in which a thin layer of sand is covered on the inner cavity of a metal mold (called an iron mold) to form a mold. Because the sand coating layer is relatively thin (4~8mm), it is economically reasonable to use more expensive high-quality modeling materials. As a result, the quality of the castings is greatly improved and the waste is significantly reduced; due to the rigidity of the iron sand-coated casting mold Very good, thereby significantly improving the dimensional accuracy and compactness of the casting.
Germany, the former Soviet Union and other countries began to use iron sand-coated casting in casting production around the 1960s, mainly for the production of ductile iron crankshafts, brake hubs, brake discs, cylinder liners, bomb shells, tank tracks and motor bases, etc. Kind of castings. China's application research on iron mold sand-coated casting started in the early 1970s. By 1979, Zhejiang Mechanical and Electrical Design Institute and Yongkang Tractor Factory cooperated to use this process for the first time in the mass casting production of S195 crankshaft blanks. At the same time, the performance evaluation of the ductile iron crankshaft produced by this process was completed, in terms of fatigue strength (comparison of fatigue limit stress σ-1), fracture strength (comparison of threshold value ΔKth and comparison of fracture toughness K1C) and service life (Comparison of endurance test of 10000h bench), etc., compared with sand casting crankshaft, it is better than sand casting. In the following 10 years, the process has been continuously improved in application. By the early 1990s, seven companies had applied the process, especially the iron sand-coated casting process for single-cylinder crankshafts and four-cylinder crankshafts. A great success. The representative enterprises during this period are Yongkang Tractor Factory, Shangyu Power Machinery Factory, Wangdu Crankshaft and Connecting Rod Factory, Wanbei Crankshaft Factory, Jinhua Internal Combustion Engine Parts Factory, Changzhou Diesel Engine Factory, etc. In 1991, the State Planning Commission approved iron mold sand-coated casting as a key new technology promotion project of the country’s "Eighth Five-Year Plan", and made Zhejiang Mechanical and Electrical Design Institute as the technical support unit of the project. This is a significant improvement in my country’s iron mold sand-coated casting technology. Development has played a huge role in promoting. After our institute undertook the promotion project, in the following 5 to 6 years, a series of problems of iron-coated sand casting for mass production were basically solved.
Mainly:
- ①Designed and finalized the sand-coated molding machine, which solved the long-standing problem of refitting and substituting core shooters;
- ②The standard iron-type sand-coated casting production line was finalized and standardized, and the original relatively simple iron-type sand-coated casting production line was improved and applied in enterprises such as Shanghai Nodular Iron Plant;
- ③The application of sand-coated iron casting is expanded to some castings with more difficult casting processes, such as six-cylinder crankshafts and three-cylinder crankshafts;
- ④ Introducing coated sand into the production of iron-coated sand casting, greatly improving the quality of sand-coated molding;
- ⑤The design of the iron mold sand-coated casting process has been further standardized, and the design level has also been greatly improved. The computer simulation software of the iron mold sand-coated casting process and the computer-aided design software of the iron mold sand-coated casting process have been developed.
At present, nearly one hundred enterprises across the country have applied iron sand-coated casting process to produce more than 30 kinds of castings such as ductile iron crankshafts, camshafts, balance shafts, pressure-resistant valve bodies, cylinder liners, and wear-resistant gear discs. The annual output is estimated to be castings. Around 10×104t. Typical companies include Shanghai Automobile Foundry General Ductile Iron Factory, Shenyang No. 1 Crankshaft Factory, Guangxi Baikuang Group, Yixing Machinery General Factory, Shandong Jiuyang Group, Zhejiang Shuguang Crankshaft Factory, Benxi Tianyuan Crankshaft Factory, Baoding Film Machinery Factory , Shanxi Lucheng Crankshaft Factory, Hebei Xinji Crankshaft Factory, etc. However, these companies have different ways of introducing the process: some have entrusted our institute to design or build, and some have imitated and developed it by themselves. Therefore, their mastery of the iron mold sand-coated casting process is very different. Taking only the iron mold sand-coated casting waste rate as an example, many companies that have a better grasp can stabilize it at about 3%, and have achieved very good economic benefits. However, there are also a few companies whose iron mold sand-coated casting waste rate is as high as about 20%, which greatly offsets the economic benefits of this process. The reason is that these companies have not fully grasped the design and production essentials of the process, and the production management is neglected.
The main solutions for the design and actual production of the iron mold sand-coated casting process:
- ①The thickness of the iron wall and the thickness of the sand coating layer and the combination of the two can meet the different requirements for solidification and cooling of castings with different wall thicknesses and different materials;
- ②Convenient and economical sand coating molding method to meet the requirements of different castings for surface quality and dimensional accuracy;
- ③Process parameters. Such as determination of gating system, sand shooting system, exhaust system, etc.;
- ④ The realization of mass production. For example, the design and shape of production line and sand-coated host and auxiliary equipment;
- ⑤The formulation of process regulations, such as the regulations of pouring, cooling and unpacking, as well as the adjustment of casting composition.
Heat Exchange Characteristics Of Iron-Type Sand-Coated Casting
After the liquid metal is poured into the iron sand-coated casting mold, "casting-sand coating-iron mold" is an unstable heat exchange system. In order to simplify the problem, it is assumed that the casting is semi-limited; and it is assumed that the temperature field of each component in the system is distributed in a straight line. Figure 1 shows a part of the system. Obviously, the same specific heat flow q passes through each component in the system:
Two heat transfer criteria respectively representing the heat exchange intensity between the casting and the sand-coated layer, and the iron mold and the sand-coated layer. k1 is the ratio of the thermal resistance of the casting to the thermal resistance of the sand coating; k2 is the ratio of the thermal resistance of the iron type to the thermal resistance of the sand coating. Considering the combination of k1 and k2, with the change of the thickness of the sand coating, there are the following three different heat transfer situations between "casting-sand coating-iron mold" that may actually occur:
- ① When k≤1 and k2≤1, the sand coating layer is within the normal thickness, and the cooling rate of the casting increases as the thickness of the sand coating layer decreases.
- ②When the thickness of the sand-coated layer exceeds a certain thickness, the iron mold has no effect on the cooling of the casting. At this time, it is equivalent to ordinary sand casting or resin sand casting. Since the thermal conductivity of the sand-coated layer is much smaller than that of the iron type, the casting cools slowly.
- ③When k≧1 and k2≧1, the thickness of the sand coating is too thin, which is equivalent to metal mold casting.
The above heat exchange characteristics have been confirmed by experiments. When the thickness of the sand coating layer of the crankshaft (CTЦ-14) iron-type sand-coated casting gradually changes from 4 to 32 mm, the amount of cementite in the crankshaft structure is continuously reduced, and the amount of pearlite and The amount of ferrite continues to increase. When the thickness of the sand-coated layer is less than 4mm, the cooling strength of the casting is similar to that of the metal type (thick paint); when the sand-coated layer is greater than 32mm, the cooling strength is equivalent to that of ordinary resin sand casting.
When iron sand-coated casting is used in the production of various castings, it is through experiments or empirical analogy to determine the thickness of the sand-coated layer and the thickness of the iron to control the solidification rate of the casting. For example, in the design of 490Q ductile iron crankshaft iron mold sand-coated casting process, the thickness of the sand coating layer is 5-8mm, and the wall thickness of the iron mold is 20-30mm, which produces high-quality as-cast ductile iron without risers. The main reason is :
- ① The sand-coated layer effectively regulates the cooling rate of the casting, on the one hand, it makes the casting less likely to appear white, and on the other hand, the cooling rate is greater than that of sand casting. As shown in Figure 2, when the molten iron is poured into the sand-coated iron mold, the temperature of the casting drops to about 930°C after 8 minutes, and it takes 24 minutes for the sand mold to drop to the same temperature, and the cooling rate is increased by about 3 times. As a result, The mechanical properties of castings are significantly improved.
- ②The iron mold has no concession, but the thin sand coating can appropriately reduce the shrinkage resistance of the mold; and the rigidity of the iron mold effectively utilizes the graphitization expansion of the ductile iron during the solidification process to achieve No riser casting; due to the thin sand coating, the cavity is not easy to deform, and the precision of the casting is greatly improved than that of the sand mold.
Two heat transfer criteria respectively representing the heat exchange intensity between the casting and the sand-coated layer, and the iron mold and the sand-coated layer. k1 is the ratio of the thermal resistance of the casting to the thermal resistance of the sand coating; k2 is the ratio of the thermal resistance of the iron type to the thermal resistance of the sand coating. Considering the combination of k1 and k2, with the change of the thickness of the sand coating, there are the following three different heat transfer situations between "casting-sand coating-iron mold" that may actually occur:
- ① When k≤1 and k2≤1, the sand coating layer is within the normal thickness, and the cooling rate of the casting increases as the thickness of the sand coating layer decreases.
- ②When the thickness of the sand-coated layer exceeds a certain thickness, the iron mold has no effect on the cooling of the casting. At this time, it is equivalent to ordinary sand casting or resin sand casting. Since the thermal conductivity of the sand-coated layer is much smaller than that of the iron type, the casting cools slowly.
- ③When k≧1 and k2≧1, the thickness of the sand coating is too thin, which is equivalent to metal mold casting.
The above heat exchange characteristics have been confirmed by experiments. When the thickness of the sand coating layer of the crankshaft (CTЦ-14) iron-type sand-coated casting gradually changes from 4 to 32 mm, the amount of cementite in the crankshaft structure is continuously reduced, and the amount of pearlite and The amount of ferrite continues to increase. When the thickness of the sand-coated layer is less than 4mm, the cooling strength of the casting is similar to that of the metal type (thick paint); when the sand-coated layer is greater than 32mm, the cooling strength is equivalent to that of ordinary resin sand casting.
When iron sand-coated casting is used in the production of various castings, it is through experiments or empirical analogy to determine the thickness of the sand-coated layer and the thickness of the iron to control the solidification rate of the casting. For example, in the design of 490Q ductile iron crankshaft iron mold sand-coated casting process, the thickness of the sand coating layer is 5-8mm, and the wall thickness of the iron mold is 20-30mm, which produces high-quality as-cast ductile iron without risers. The main reason is :
- ① The sand-coated layer effectively regulates the cooling rate of the casting, on the one hand, it makes the casting less likely to appear white, and on the other hand, the cooling rate is greater than that of sand casting. As shown in Figure 2, when the molten iron is poured into the sand-coated iron mold, the temperature of the casting drops to about 930°C after 8 minutes, and it takes 24 minutes for the sand mold to drop to the same temperature, and the cooling rate is increased by about 3 times. As a result, The mechanical properties of castings are significantly improved.
- ②The iron mold has no concession, but the thin sand coating can appropriately reduce the shrinkage resistance of the mold; and the rigidity of the iron mold effectively utilizes the graphitization expansion of the ductile iron during the solidification process to achieve No riser casting; due to the thin sand coating, the cavity is not easy to deform, and the precision of the casting is greatly improved than that of the sand mold.
Cooling Rate Of Iron Sand-Coated Castings
The factors affecting the cooling rate of iron sand-coated castings include casting wall thickness, casting material, pouring temperature, sand coating thickness, sand coating material, iron mold thickness, iron mold material, and mold temperature. Here, only the influence of casting wall thickness (bc), sand coating thickness (bm) and iron thickness (bi) are discussed.
The Influence Of bc, bm And bi On Casting Cooling
Different casting wall thicknesses (10mm, 20mm, 40mm, 80mm, respectively), different sand coating thicknesses (4mm and 32mm, respectively) and different iron type wall thicknesses (32mm and 8mm, respectively) made under the following experimental conditions The influence of the cooling rate of iron-type sand-coated castings: the chemical composition of the casting is 3.52%C, 2.46%Si, 0.80%Mn, 0.18%P, 0.031%S, and the chemical composition of the sand-coated layer is: 90% quartz sand, 8% clay, Coal powder 2%, moisture 3%
- ①The casting wall thickness, sand coating thickness and iron wall thickness affect the cooling rate of the casting. Therefore, in actual production, suitable iron mold thickness and sand coating thickness should be selected according to different casting wall thicknesses to obtain the required cooling rate.
- ② Castings of different thicknesses can be obtained by selecting the appropriate sand coating thickness and iron wall thickness to obtain the same cooling rate. For example, in Figure 3, zone I means the thickness is 10mm and 20mm, zone II means 20mm and 40mm, and zone III means 40mm. And the overlap between the cooling range of 80mm castings.
- ③Although bm and bi can be changed to obtain the same cooling rate for castings of different thicknesses, not all thicknesses of castings can obtain the same cooling rate. Under the experimental conditions, castings with a thickness of 10mm and a thickness of 40mm cannot be obtained The exact same cooling rate (there is no overlap between the curves).
Selection Of Sand Coating Thickness (bm) And Iron Wall Thickness (bi)
Bm and bi are generally determined based on experience or experiment. Here is a chart method, which is suitable for casting thickness (bc) from 10 to 80mm and unpacking temperature of 600℃. The ordinate is the cooling time. The abscissa of the curve on the right is marked with the thickness of the sand coating, which can be determined from the time required for the known casting to cool to 600°C and the thickness of various castings, and in the required casting wall thickness (10, 20 , 40, 80mm) is known, then it is very convenient to determine the thickness of the sand coating and the thickness of the iron mold. Find the corresponding bc (for example, bc=20mm) from the horizontal axis of the left half of the curve and draw a horizontal line.
If the two lines intersect within the range of the cross-hatched curve, it indicates that this casting is suitable for iron sand coating Casting. Extend this horizontal line to the right, and it will extend into the area of bc=20mm, and draw a vertical line down in this area to get the required sand coating thickness. However, this vertical line should be drawn to the right as much as possible in order to obtain the smallest thickness of the sand coating and the thickness of the iron mold. If the thickness of the sand-coating layer that needs to be determined is not within this range, you can find it from the adjacent curve range in a similar way.
- ①The casting wall thickness, sand coating thickness and iron wall thickness affect the cooling rate of the casting. Therefore, in actual production, suitable iron mold thickness and sand coating thickness should be selected according to different casting wall thicknesses to obtain the required cooling rate.
- ② Castings of different thicknesses can be obtained by selecting the appropriate sand coating thickness and iron wall thickness to obtain the same cooling rate. For example, in Figure 3, zone I means the thickness is 10mm and 20mm, zone II means 20mm and 40mm, and zone III means 40mm. And the overlap between the cooling range of 80mm castings.
- ③Although bm and bi can be changed to obtain the same cooling rate for castings of different thicknesses, not all thicknesses of castings can obtain the same cooling rate. Under the experimental conditions, castings with a thickness of 10mm and a thickness of 40mm cannot be obtained The exact same cooling rate (there is no overlap between the curves).
Please keep the source and address of this article for reprinting: The Method And Application Of Sand-Coated Iron Mold Casting
Minghe Die Casting Company are dedicated to manufacture and provide quality and high performance Casting Parts(metal die casting parts range mainly include Thin-Wall Die Casting,Hot Chamber Die Casting,Cold Chamber Die Casting),Round Service(Die Casting Service,Cnc Machining,Mold Making,Surface Treatment).Any custom Aluminum die casting, magnesium or Zamak/zinc die casting and other castings requirements are welcome to contact us.
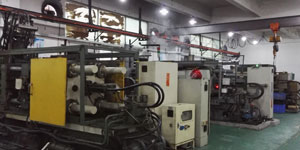
Under the control of ISO9001 and TS 16949,All processes are carried out through hundreds of advanced die casting machines, 5-axis machines, and other facilities, ranging from blasters to Ultra Sonic washing machines.Minghe not only has advanced equipment but also have professional team of experienced engineers,operators and inspectors to make the customer’s design come true.
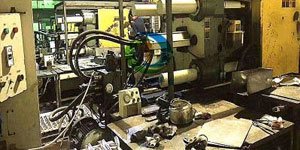
Contract manufacturer of die castings. Capabilities include cold chamber aluminum die casting parts from 0.15 lbs. to 6 lbs., quick change set up, and machining. Value-added services include polishing, vibrating, deburring, shot blasting, painting, plating, coating, assembly, and tooling. Materials worked with include alloys such as 360, 380, 383, and 413.
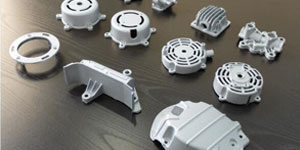
Zinc die casting design assistance/concurrent engineering services. Custom manufacturer of precision zinc die castings. Miniature castings, high pressure die castings, multi-slide mold castings, conventional mold castings, unit die and independent die castings and cavity sealed castings can be manufactured. Castings can be manufactured in lengths and widths up to 24 in. in +/-0.0005 in. tolerance.
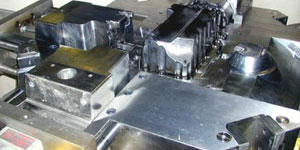
ISO 9001: 2015 certified manufacturer of die cast magnesium, Capabilities include high-pressure magnesium die casting up to 200 ton hot chamber & 3000 ton cold chamber, tooling design, polishing, molding, machining, powder & liquid painting, full QA with CMM capabilities, assembly, packaging & delivery.
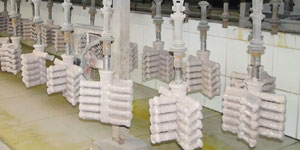
ITAF16949 certified. Additional Casting Service Include investment casting,sand casting,Gravity Casting, Lost Foam Casting,Centrifugal Casting,Vacuum Casting,Permanent Mold Casting,.Capabilities include EDI, engineering assistance, solid modeling and secondary processing.
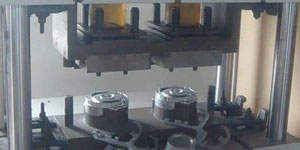
Casting Industries Parts Case Studies for: Cars, Bikes, Aircraft, Musical instruments, Watercraft, Optical devices, Sensors, Models, Electronic devices, Enclosures, Clocks, Machinery, Engines, Furniture, Jewelry, Jigs, Telecom, Lighting, Medical devices, Photographic devices, Robots, Sculptures, Sound equipment, Sporting equipment, Tooling, Toys and more.
What Can we help you do next?
∇ Go To Homepage For Die Casting China
→Casting Parts-Find out what we have done.
→Ralated Tips About Die Casting Services
By Minghe Die Casting Manufacturer |Categories: Helpful Articles |Material Tags: Aluminum Casting, Zinc Casting, Magnesium Casting, Titanium Casting, Stainless Steel Casting, Brass Casting,Bronze Casting,Casting Video,Company History,Aluminum Die Casting |Comments Off