The Degradation Mechanism Of Forging Mold
Die forging is currently the most advanced forging technology, mainly used for mass production of key components of molds. The biggest disadvantage is the poor durability of the forming tools. According to the editor of diecastingcompany.com, the cost of tools is 8-15% of the total cost of products. In fact, if you consider the time required to replace worn tools and the loss caused by accidental failure, the cost may be as high as 30% to 50%. Moreover, the wear of the tool will cause a significant deterioration in the quality of the forging. The most common defects caused by tool wear are cavity filling errors, that is, folding, burrs, deformation, scratches, delamination and micro and macro cracks.
These defects will ultimately affect the performance of forged products. Due to the strong competition in the market, manufacturers of die forging products continue to reduce their costs while improving the quality of forgings. Even so, they are still very interested in the problem of poor tool durability.
The durability of a tool is usually defined in several ways. In terms of production, the durability of a tool is expressed by the number of forgings, that is, the number of products of the expected quality that can be obtained with this tool. According to this definition, the average durability of tools may vary between 2,000 and 20,000 pieces. In terms of tools, durability is related to degradation, so it is defined as the ability to withstand degradation phenomena. This article mainly uses the second definition. It should be said that forging tools are affected by a variety of degrading factors during use, and the interaction of these factors makes the analysis of the problem more difficult. In the literature on this subject, one can find various explanations of degradation phenomena.
According to the statistics of many scholars, the major reason for the withdrawal of forging molds from service is due to changes in wear dimensions. Mold scrap due to wear accounts for about 70%, plastic deformation accounts for about 25%, and fatigue cracking and other reasons account for only about 5%. Many phenomena often occur at the same time, and their interaction depends on the design of the mold, the conditions of their forging and manufacturing, the heat treatment of the mold material, and the shape of the preform and the insert.
Working conditions of forging dies: In the process of hot die forging, tools are mainly subjected to degradation from three aspects: intensive thermal shock, periodic changes of mechanical load, and high temperature and high pressure. In order to reduce the yield stress of steel products during hot forging, the deformed metal is heated to 10,000-2,000 degrees Celsius. At the moment of material deformation, the temperature of the tool surface may reach 800 degrees Celsius, followed by intensive cooling, and therefore the tool will be exposed to a large temperature gradient. On the cross-section of the mold, the mold surface temperature and near-surface temperature can differ by several hundred degrees Celsius. The temperature of hot die forging is lower than that of hot forging, that is to say, the temperature of steel deformation reaches about 900 degrees Celsius. This means that the load generated by the cyclic heating and cooling of the tool surface is not as large as that of hot forging. Nevertheless, the life of the tools used in the semi-hot forging process is still quite short. This is mainly due to the combined effect of the cyclic temperature and the larger mechanical load. The mechanical load mainly comes from cooling and harder materials.
Degeneration mechanism of forging tools
The service life of forging tools mainly depends on their design, preparation, heat treatment of tool materials, their forging conditions, the shape of preforms and core blocks, etc. We can find a lot of information about degradation in the literature on this subject. These mechanisms are divided into different categories. Research results show that the following wear mechanisms mainly occur on the surface of forging tools: abrasive wear, thermomechanical fatigue, plastic deformation, fatigue cracking, adhesive wear and oxidation. The shape of the working indentation of the tool determines the contact time, pressure, friction path and temperature changes, which determine the rate of occurrence of the special degradation mechanism.
In the flat area, the contact time between the tool and the thermal material is the longest, and it is also the place where the maximum pressure occurs. Thermomechanical fatigue is the main degradation mechanism.
The inner radius of the rounding is affected by the cyclic tensile load, which is caused by the increase of the external load, which mainly occurs when the deformation tends to be concentrated during the forging process. As a result, fatigue microcracks develop into large cracks during the service of the tool and appear in these places. The outer radius of the mold dent and the place where the mold imprint enters the flash bridge due to the weakening of the material under high temperature conditions, the lower the yield point of the material, which leads to plastic deformation. The dense flow of deformed materials causes abrasive wear in these areas, which is further aggravated by the hard oxides, which are formed on the surface of the forging material of the tool during the high-temperature oxidation process.
Adhesive wear of the degradation mechanism of forging dies
Adhesive wear occurs in the plastic deformation area of the surface layer, especially where the surface is irregular. It usually occurs under high pressure and relatively low speed conditions, mainly due to similar material interactions or materials showing chemical affinity (typical forging processing conditions). Under higher pressure conditions, the material molding slips along the surface of the tool, removing the oxide coating, leaving the fresh surface of the tool exposed. This mainly occurs in the irregular area of the surface projection (the peak part of the rough surface).
When the materials in these places are placed close to each other, so that the interatomic forces begin to work, local metal bonds are formed. Then, as the surfaces shifted further to each other, the metal bond was destroyed. Plastic deformation of the surface layer is formed in this process. The breaking of the metal bond leads to the peeling of the metal particles, which tend to stick to the surface.
Abrasive wear of the degradation mechanism of forging dies
Material loss is usually attributed to abrasive wear. The size of the peeled particles mainly depends on the forging coefficient and the properties of the tool surface layer. An example of adhesive wear is the second stage operation of the forging of the CV universal joint housing, as shown in the figure. The temperature at which the material deforms in this process is about 900°C, that is, it is usually much lower than the traditional hot forging process, which tends to be this type of wear. Adhesive wear will stick itself to the material itself or to the tool, where the cross-sectional area is reduced.
Abrasive wear is the result of material loss and is mainly achieved by the separation of material from the surface. Abrasive wear will occur when there are loose or fixed abrasive particles, or when there are irregular portions of protrusions on the interaction surface. For the forging tool, its hardness is much higher than that of the deformed material. In this case, if abrasive particles appear in the contact part between the forging tool and the deformed material, abrasive wear will occur. Abrasive wear will be exacerbated by the appearance of hard oxide particles, which are formed on the surface of small particles separated from the forging part and the mold and the mold surface under high temperature conditions. Due to this mechanism, grooves are created along the direction in which the deformation of the material changes.
Their shape and depth mainly depend on the forging conditions. The protruding part is particularly susceptible to wear and will be quickly removed from the surface of the tool during its further service, which leads to material loss and changes in material geometry. Particularly easy to form abrasive wear, and also particularly sensitive to abrasive wear is the place where the longest slip occurs during the deformation of the material. The most common is the outer radius of the mold cavity, where the mold enters the flash bridge.
Please keep the source and address of this article for reprinting: The Degradation Mechanism Of Forging Mold
Minghe Die Casting Company are dedicated to manufacture and provide quality and high performance Casting Parts(metal die casting parts range mainly include Thin-Wall Die Casting,Hot Chamber Die Casting,Cold Chamber Die Casting),Round Service(Die Casting Service,Cnc Machining,Mold Making,Surface Treatment).Any custom Aluminum die casting, magnesium or Zamak/zinc die casting and other castings requirements are welcome to contact us.
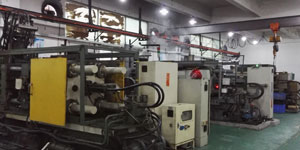
Under the control of ISO9001 and TS 16949,All processes are carried out through hundreds of advanced die casting machines, 5-axis machines, and other facilities, ranging from blasters to Ultra Sonic washing machines.Minghe not only has advanced equipment but also have professional team of experienced engineers,operators and inspectors to make the customer’s design come true.
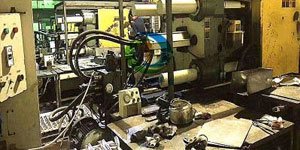
Contract manufacturer of die castings. Capabilities include cold chamber aluminum die casting parts from 0.15 lbs. to 6 lbs., quick change set up, and machining. Value-added services include polishing, vibrating, deburring, shot blasting, painting, plating, coating, assembly, and tooling. Materials worked with include alloys such as 360, 380, 383, and 413.
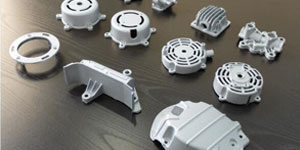
Zinc die casting design assistance/concurrent engineering services. Custom manufacturer of precision zinc die castings. Miniature castings, high pressure die castings, multi-slide mold castings, conventional mold castings, unit die and independent die castings and cavity sealed castings can be manufactured. Castings can be manufactured in lengths and widths up to 24 in. in +/-0.0005 in. tolerance.
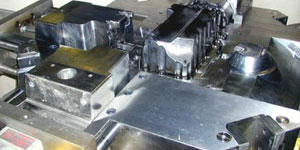
ISO 9001: 2015 certified manufacturer of die cast magnesium, Capabilities include high-pressure magnesium die casting up to 200 ton hot chamber & 3000 ton cold chamber, tooling design, polishing, molding, machining, powder & liquid painting, full QA with CMM capabilities, assembly, packaging & delivery.
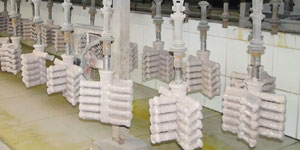
ITAF16949 certified. Additional Casting Service Include investment casting,sand casting,Gravity Casting, Lost Foam Casting,Centrifugal Casting,Vacuum Casting,Permanent Mold Casting,.Capabilities include EDI, engineering assistance, solid modeling and secondary processing.
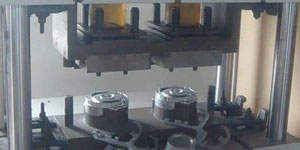
Casting Industries Parts Case Studies for: Cars, Bikes, Aircraft, Musical instruments, Watercraft, Optical devices, Sensors, Models, Electronic devices, Enclosures, Clocks, Machinery, Engines, Furniture, Jewelry, Jigs, Telecom, Lighting, Medical devices, Photographic devices, Robots, Sculptures, Sound equipment, Sporting equipment, Tooling, Toys and more.
What Can we help you do next?
∇ Go To Homepage For Die Casting China
→Casting Parts-Find out what we have done.
→Ralated Tips About Die Casting Services
By Minghe Die Casting Manufacturer |Categories: Helpful Articles |Material Tags: Aluminum Casting, Zinc Casting, Magnesium Casting, Titanium Casting, Stainless Steel Casting, Brass Casting,Bronze Casting,Casting Video,Company History,Aluminum Die Casting |Comments Off