Lost Foam Casting Coating For Large Complex Thin-Walled Shell Parts
A high-power wheeled tractor independently developed by China YTO Group Co., Ltd. has a large rear transmission case and a very complex structure (see Figure 1), with an external dimension of 1050mm×925mm×750mm, and the actual volume of the casting is about 0.085m3. The theoretical weight is about 615kg.
In the trial production of this shell part, the lost foam casting technology was used. The thin-walled shell part with such a large volume and weight and complicated structure was produced by this technology, and there are few reports in the existing journals and magazines. Through many trial productions, it has been found that the castings after pouring have the following three problems: one is the deformation of the casting, which makes it difficult to guarantee the dimensional accuracy of the casting; the second is that iron-clad sand is easily formed in the inner cavity of the casting, which increases the difficulty of cleaning; the third is the surface of the casting. Carbon black defects are generated, causing the casting to be scrapped during processing.
There are many factors that cause the above casting defects, but the coating plays a vital role in the entire lost foam casting process. If the coating itself is not formulated properly and the coating performance is poor, not only can it not effectively solve the problem, but it will cause defects.
- (1) The paint has poor hangability. The paint used in the production test is water-based paint, and the white mold of the rear transmission case is made of polystyrene foam, which is not easy to be wetted or penetrated by the water-based paint. Poor wettability, poor coating, and the paint cannot hang on the surface of the white mold or adheres poorly. On the one hand, it will cause the pattern to be coated multiple times, and the tendency of the white mold to deform during multiple coating and drying processes will increase. ; On the other hand, it will cause uneven coating thickness, even discontinuous coating, and local exposure of the white mold will cause sand sticking defects. Due to the large size of the white mold of the rear transmission case (see Figure 2), the buoyancy generated during dipping will cause the appearance to be broken. Therefore, the application of the white mold uses a combination of spraying and curtain coating. The coating properties put forward higher requirements.
- (2) The strength of the coating is low. The white mold of the rear transmission case has large volume, thin wall and low density. The entire white mold does not have inherent rigidity. The adhesive strength of the coating at room temperature is not high, and it is easy to cause the coating to peel off and damage during the drying and handling of the pattern. It cannot be guaranteed that the pattern has sufficient resistance to deformation during the sand filling and compaction process, resulting in deformation; the high-temperature strength of the coating is not High, under high temperature conditions, it is impossible to prevent the damage of the coating during the casting and forming process of the molten metal, causing collapse, sand sticking and other defects, so that the dimensional accuracy and surface quality of the casting cannot be guaranteed; poor residual strength of the coating will cause It is not easy to clean the coating from the surface of the casting after pouring.
- (3) The air permeability of the coating is poor. Because the material of the trial product is HT250, in the production test, the pouring temperature is controlled at 1380~1430℃, while the material of the white mold is polystyrene foam, which is in the temperature range of 1350~1550℃. , It begins to crack rapidly, burns and vaporizes, and low-molecular-weight polymers rapidly crack, and a large amount of hydrogen and free carbon are precipitated. If the air permeability of the coating is poor, a large amount of pyrolysis products cannot be smoothly exported through the coating, which will cause pores in the casting; if the coating cannot absorb the residue generated during the burning of polystyrene foam, the casting is prone to residual carbon inclusion defects .
Aiming at casting defects caused by coatings in the technical background, it focuses on the development of coating formulations and at the same time explores the mixing process of coatings.
Development of coating formulations
1. Composition and material selection
- (1) Refractory powder lost foam coating has three important requirements for the selection of refractory powder: First, the particle size of the refractory powder should be relatively coarse, but if it is too coarse, the sand resistance of the coating will be affected, and the anti-stick sand will be taken into account. And high air permeability, choose a particle size of 0.08~0.071mm (180/200 mesh); second, the rounder the shape of the refractory powder, the better, the round powder has good air permeability; the third is that the refractory powder has good air permeability; The pyrolysis products of foam plastics must have adsorption capacity. In order to improve the overall performance of the coating, high alumina bauxite clinker powder (particle size 0.08mm) and mica powder (particle size 0.071mm) are selected as refractory powder. The high alumina bauxite powder has a porous structure with rounded grains, which can improve the air permeability of the coating and the adsorption capacity of the foam pyrolysis products; the mica powder is a layered silicate from the structure, which is heat-resistant and wear-resistant , Insulation performance, good elasticity and flexibility, adding a certain proportion of mica powder to the coating can improve the coverage, high temperature air permeability and sinterability of the coating.
- (2) Binder EPC coating binder is an important part of the coating. It not only imparts the strength and spreadability of the coating, but also affects the air permeability and suspension of the coating. Usually, the combination of inorganic binder and organic binder not only guarantees the strength of the coating at room temperature and high temperature, but also effectively improves the air permeability of the coating. Due to the large volume and thin wall of the transmission case and transmission case, in order to ensure the rigidity, strength and air permeability of the coating, three types of adhesives, white latex, α starch and RSF powder with a wetting effect, are selected. The binding agent is mixed and used in a certain proportion. Especially the selection of RSF powder effectively improves the rigidity, strength and air permeability of the coating.
- (3) The main function of the carrier liquid is to disperse the refractory powder in it. In the lost foam casting, considering the requirements of environmental protection, application, drying, gas generation, and cost, it is easy to use water as the carrier liquid. Make the coating obtain good suspension, brushability and non-flowing properties.
- (4) The suspension of the suspending agent coating directly affects the coating ability and coating quality of the coating, and also affects the operating performance of the coating. Due to the coarse particle size of the refractory powder and the large viscosity of the coating, when preparing the coating, Lithium bentonite and attapulgite are used as suspending agents. Lithium bentonite and attapulgite can form a three-dimensional network structure in water. The combination of the two can improve the suspension of the coating and improve the rheology and process performance of the coating.
There are mainly the following 3 kinds of auxiliary additives.
- ①Defoamer. It is used to eliminate the bubbles formed with the stirring during the production process of the coating.
- ②Surfactant. The main purpose of adding a small amount of surfactant to the coating is to improve the adhesion of the coating to the pattern and facilitate application.
- ③ Antiseptic. In order to facilitate the storage and long-term use of the paint, a certain amount of preservative is added to the paint, which can effectively prevent the paint from mildew, deterioration and loss of viscosity in the season with higher temperatures.
Research on coating performance
1. Test method of coating performance
- (1) The density of the paint is measured by the 100mL graduated cylinder weighing method to determine the density of the paint.
- (2) The suspension stability test of the coating adopts a 100mL graduated cylinder to determine the 6h deposition rate method.
- (3) A Baume meter (used at the production site) is used to test the paint concentration.
- (4) Test of coating thickness: Dip the prepared foam plastic sample block 100mm×100mm×12mm (preferably from a scrapped white mold), immerse it in the mixed paint for 10s, take it out, and put it in a 50°C electric After drying for 3 hours in the drying box, take out the test block and measure the thickness of the coating.
- (5) The high-temperature air permeability and high-temperature strength test of the coating adopts the multifunctional performance tester developed by Huazhong University of Science and Technology.
2. The performance of the lost foam coating is based on the above coating formula
The preparation process of the coating
Many tests have found that the performance of the coating is not only related to the coating formulation, but also related to the formulation process of the coating. The same formulation and different formulation processes have a great impact on the performance of the coating. To obtain a coating with good process performance, the preparation process should ensure that the thixotropic agent, binder and solvent are fully dispersed, and have a strong adsorption with the refractory powder, so that the components of the coating are fully integrated, so that the coating has good thixotropy and Coatability.
1. Paint preparation equipment
High-speed dispersing mixer, roller-type sand mixer.
2. Preparation method
- (1) Preparation of wet powder coating: Pour the weighed refractory powder into a roller sand mixer, mix for 5-10 minutes, and then pour the binder, suspending agent and auxiliary additives into the mixture in sequence In the mill, after mixing for 30-40 minutes, it will be milled and bagged for later use.
- (2) Preparation of slurry paint. Weigh a certain amount of wet powder paint, according to the ratio of powder to water ratio of 1:0.6 to 0.7, weigh a certain amount of water into the paint mixing bucket, and place the paint bucket under the high-speed dispersion mixer. Turn on the high-speed dispersion mixer, and then add the weighed wet powder paint. Stir at high speed (800~900r/min) for about 40 minutes, then stir at low speed (<600r/min) for 2 hours. After mixing the uniform paint, leave it for 24 hours, It is fully matured, and the moisture can be adjusted according to the Baume degree requirements during use.
Conclusion
- (1) Adding an appropriate amount of mica powder to the refractory powder can improve the coating and suspension properties of the coating. When the pattern is applied, a thicker coating can be obtained at one time, reducing the number of times of painting the pattern and simplifying The production process is improved; adding appropriate amount of mica powder to obtain the same coating thickness, the overall weight of the pattern after coating is reduced, which can effectively ensure the stiffness and strength of the pattern; adding appropriate amount of mica powder reduces the bauxite powder coating Sintering temperature, the coating is easy to peel off from the casting after pouring, and the surface of the casting is smooth and clean.
- (2) In the coating formula, adding a wetting binder RSF powder, the adhesion of the coating to the foam pattern is obviously enhanced, and the strength of the coating is improved, which is very important to ensure the stiffness and strength of the pattern.
- (3) Lithium bentonite and attapulgite are used in combination. According to the mixing process formulated for lost foam coatings, it has been verified that the suspension, thixotropy and coating properties of the coating have been significantly improved. The layer thickness is uniform, avoiding sand sticking defects caused by exposure of the white mold.
Please keep the source and address of this article for reprinting: Lost Foam Casting Coating For Large Complex Thin-Walled Shell Parts
Minghe Die Casting Company are dedicated to manufacture and provide quality and high performance Casting Parts(metal die casting parts range mainly include Thin-Wall Die Casting,Hot Chamber Die Casting,Cold Chamber Die Casting),Round Service(Die Casting Service,Cnc Machining,Mold Making,Surface Treatment).Any custom Aluminum die casting, magnesium or Zamak/zinc die casting and other castings requirements are welcome to contact us.
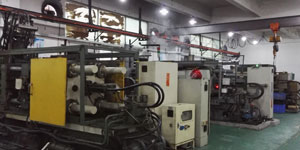
Under the control of ISO9001 and TS 16949,All processes are carried out through hundreds of advanced die casting machines, 5-axis machines, and other facilities, ranging from blasters to Ultra Sonic washing machines.Minghe not only has advanced equipment but also have professional team of experienced engineers,operators and inspectors to make the customer’s design come true.
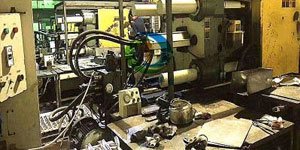
Contract manufacturer of die castings. Capabilities include cold chamber aluminum die casting parts from 0.15 lbs. to 6 lbs., quick change set up, and machining. Value-added services include polishing, vibrating, deburring, shot blasting, painting, plating, coating, assembly, and tooling. Materials worked with include alloys such as 360, 380, 383, and 413.
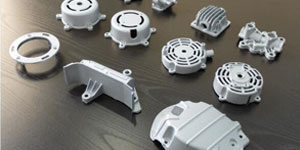
Zinc die casting design assistance/concurrent engineering services. Custom manufacturer of precision zinc die castings. Miniature castings, high pressure die castings, multi-slide mold castings, conventional mold castings, unit die and independent die castings and cavity sealed castings can be manufactured. Castings can be manufactured in lengths and widths up to 24 in. in +/-0.0005 in. tolerance.
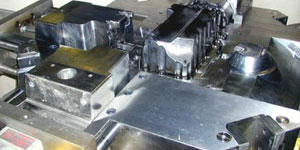
ISO 9001: 2015 certified manufacturer of die cast magnesium, Capabilities include high-pressure magnesium die casting up to 200 ton hot chamber & 3000 ton cold chamber, tooling design, polishing, molding, machining, powder & liquid painting, full QA with CMM capabilities, assembly, packaging & delivery.
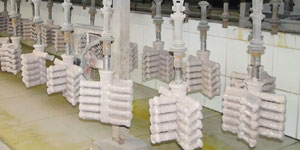
ITAF16949 certified. Additional Casting Service Include investment casting,sand casting,Gravity Casting, Lost Foam Casting,Centrifugal Casting,Vacuum Casting,Permanent Mold Casting,.Capabilities include EDI, engineering assistance, solid modeling and secondary processing.
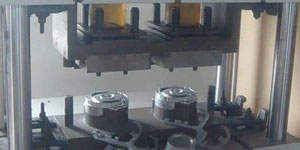
Casting Industries Parts Case Studies for: Cars, Bikes, Aircraft, Musical instruments, Watercraft, Optical devices, Sensors, Models, Electronic devices, Enclosures, Clocks, Machinery, Engines, Furniture, Jewelry, Jigs, Telecom, Lighting, Medical devices, Photographic devices, Robots, Sculptures, Sound equipment, Sporting equipment, Tooling, Toys and more.
What Can we help you do next?
∇ Go To Homepage For Die Casting China
→Casting Parts-Find out what we have done.
→Ralated Tips About Die Casting Services
By Minghe Die Casting Manufacturer |Categories: Helpful Articles |Material Tags: Aluminum Casting, Zinc Casting, Magnesium Casting, Titanium Casting, Stainless Steel Casting, Brass Casting,Bronze Casting,Casting Video,Company History,Aluminum Die Casting |Comments Off