Slag Inclusion In Lost Foam Casting
Lost foam casting is currently one of the most advanced casting processes in the world. It is hailed as a revolution in the history of casting. It is the "main way of green intensive casting" in the 21st century, and it plays an increasingly important role in casting production. Lost foam casting does have a wide range of adaptability, but not all castings are suitable for lost foam casting.
Some castings can barely be made, but the process yield rate is low or the rejection rate is high. It also has technological limitations. For example, the foam pattern is easy to be deformed by force; compared with the traditional casting method, it also has the problem of pyrolysis and gasification of the foam mold.
The defects of lost foam casting also need to be fully understood and eliminated. Common casting defects in lost foam casting include wrinkles, carbon black, deformation, sand sticking, collapse, pores, slag inclusions, cold partitions, and surface seepage of steel castings. Carbon, etc., let’s talk about the experience and understanding of slag inclusion defects.
Slag inclusion defects in lost foam casting
Slag inclusion defects refer to defects formed by dry sand, paint and other inclusions as molten iron enters the casting during the pouring process. On the surface of the machined castings, you can see spots of white or black-gray inclusions, distributed individually or in pieces. The white is quartz sand particles, and the black-gray is slag, paint, foam model residues and other inclusions after pyrolysis. . This kind of defect is commonly known as "sand ingress" or "slag inclusion", and it is a very common defect in the production of lost foam casting. Almost all factories using lost foam casting are widespread, and it is difficult to completely eradicate them. Only by taking a variety of measures and careful operation in each process can the "slag inclusion" be reduced to a very low level and satisfactory results can be achieved. After the lost foam castings are cooled and boxed before being cleaned, according to the surface conditions of the castings and the pouring system, it can be judged whether there are sand and slag inclusion defects. If the sprue cup, sprue, cross sprue, sprue and gate surface or connection, and the surface of the casting are severely sanded or have cracked sand, it is basically certain that the casting has slag inclusion and sand ingress defects. Smash the sprue rod or sprue bead, you can see white spots on the fracture, and in severe cases, the fracture will form a circle of white spots. Such castings, especially plate-shaped and round cake-shaped castings, will have white and black-gray spot defects on the processing surface after machining. If the process operation procedures are not strictly controlled, the castings produced will seriously affect the quality of the castings and the progress of the order completion.
Causes of slag inclusion and sand ingress defects
Through our long-term observations in production practice, it is proved that from the sprue cup, sprue, cross runner, inner runner to the casting, all parts may cause sand ingress, especially the joint part of the gating system and the casting. In the whole production process, the paint peeling and cracking on the surface of the white mold of the gating system, the paint peeling and cracking at the bonding part of the white mold, the paint peeling and cracking on the surface of the foam white mold, the sprue is not tightly closed and other factors are caused by slag inclusion and sand ingress. The most important cause of defects. Secondly, the selection of process parameters, such as the size of the net head of the pouring system, the pouring temperature, the degree of negative pressure, the particle size of dry sand, etc., as well as the transportation process of the model and the packing operation, all have an impact on the slag inclusion and sand ingress defects of the castings. Great influence. Only by adopting systematic measures and careful operation in these links can the slag inclusion defects of castings be reduced and basically eliminated, and high-quality castings can be obtained. Overcoming the defects of slag inclusion is a systematic project.
Methods and measures to reduce and overcome slag inclusion defects
Sand ingress and slag inclusion defects are a major problem in lost foam casting production. At present, there are mainly three types of products that have been successfully produced by lost foam casting, namely, wear-resistant parts, pipe fittings and box castings, all of which are rarely processed or not processed. For castings with many processing surfaces and high requirements, the slag inclusion defect is a key problem that needs to be solved. Our experience is that measures can be taken from the following aspects to reduce and eliminate slag inclusion defects:
1. Paint
The role of the lost foam coating is: 1) Improve the surface finish of the casting, reduce the roughness of the casting by 2-3 levels, and improve the surface quality and performance of the casting. 2) Reduce and prevent sand sticking and sand hole defects. 3) It is conducive to sand removal and falling sand. 4), the liquid and gas melted in the lost foam during pouring are smoothly discharged into the casting sand through the coating layer, and the molten metal is prevented from penetrating into the sand mold, preventing the casting from producing pores, metal infiltration and carbon defects. 5) Improve the strength and rigidity of the pattern, prevent deformation and damage during transportation, sand filling and vibration modeling, which is beneficial to improve the dimensional accuracy and yield of castings. Coatings for lost foam casting require a series of strength, air permeability, refractoriness, thermal insulation, explosion resistance and crack resistance, rapid cooling and rapid heat resistance, moisture absorption, cleaning, coating, suspension, non-flowing, etc. Performance, to prevent slag inclusion defects, first requires the coating to have high strength and fire resistance. It is required that the coating layer on the surface of the white mold does not crack or crack during the drying and transportation process, that is, the coating should have sufficient room temperature strength; and during the pouring process, the coating layer will also be affected by the long-term scouring of the high-temperature metal. If it does not fall off or cracks, it has high high temperature strength. When the liquid metal enters the mold, the straight gate is tightly closed, and the coating layer on the surface of the casting and the pouring system does not fall off, cracks and cracks are the primary conditions to prevent slag inclusion defects. If the runner is not tightly sealed, the coating layer will fall off. Cracks and cracks, a large amount of sand, paint and inclusions will enter the metal to form slag inclusion defects. Strength and air permeability are two important properties of coatings. Sometimes the coatings used in the pouring system are required to have higher fire resistance than the casting coatings to resist the long-term erosion of high-temperature metals without falling off and cracking. The operator must ensure the uniformity of the paint during the painting process.
2. Packing operation
During packing, the coating layer on the surface of the model group (model + gating system) is not allowed to have any shedding, cracks or cracks, especially at the junction of the sprue and the runner, the junction of the runner and the inner runner, and the inner As long as there is looseness, cracks, or weak connection between the gate and the mold, sand may enter. This requires high joint strength, thicker paint, sufficient rigidity for the gating system, and braces or reinforcement sleeves when necessary. The pattern group should be stable when placed on the bottom sand of the sand box. It is not allowed to start sanding and vibration modeling when it is placed in the air to avoid shock cracking of the coating layer. Don't add sand directly to the appearance, use a hose to add sand first, and then use the rain shower device to sprinkle sand before shaking and vibrating. When you start to shake the shape, the vibration should be slight and the amplitude should be small, and then vibrate greatly after the dry sand is buried. In the vibration molding, the pouring system, especially the sprue, is not allowed to break or bend, so as to prevent the coating layer from cracking, and the sprue must be tightly sealed to prevent sand from entering. The entire packing, sanding, vibration, and modeling operations must be very careful and careful, and it must be ensured that the coating layer of the pattern group does not fall off, cracks or cracks before pouring. Before pouring, the sprue cup should be cleaned again to ensure that there is no floating sand, dust and debris.
3. Pouring head, temperature and time
The higher the pressure head during pouring, the greater the erosion of the pouring system and the mold, and the greater the possibility of sand ingress caused by the scouring of the coating. The pressure head is different for castings of different sizes. To choose a ladle with appropriate capacity, the ladle should be as low as possible the pouring height, and the ladle mouth should be as close as possible to the pouring cup, and large ladle should be avoided for pouring small jobs. The higher the pouring temperature, the higher the performance requirements of the coating, and the easier it is to produce defects such as sticky sand and slag. The proper pouring temperature should be selected. For gray iron castings, the tapping temperature can be around 1480°C, and the pouring temperature should be 1380-1420°C; the tapping temperature of ductile iron castings should be above 1500°C, and the pouring temperature should be 1420-1450°C; the pouring temperature of steel castings should be 1480-1560°C . The pouring time of a box of iron castings requiring 300-500 kg of molten iron can be controlled within 10-20 seconds.
4. Negative pressure
The pouring process of lost foam casting is generally carried out under vacuum conditions. The role of negative pressure is to compact dry sand, accelerate exhaust, and improve filling capacity. Pouring under vacuum sealing conditions improves the working environment. The degree of negative pressure has a great influence on the quality of castings. Excessive negative pressure increases the possibility of inhaling dry sand and inclusions when the molten metal flows through the cracks and cracks, and also increases the sticky sand defects of the castings. Too fast filling speed increases the scouring ability of the metal to the runner and the mold, and it is easy to cause the paint to fall off and enter the metal, and it is also easy to wash out the paint layer and cause sand to enter. For iron castings, the appropriate negative pressure is generally 0.025-0.04MPa. ,
5. Set up slag blocking, slag skimming and slag collecting risers
Setting slag retaining and slag skimming in the gating system and setting slag collecting risers on the castings and taking slag retaining and slag skimming measures can help improve sand and slag inclusion defects.
6. Molding sand
The particle size of molding sand is too coarse or too fine to affect the occurrence of slag inclusion and sand sticking defects. Too coarse particle size will increase the sticking sand and slag inclusion defects. Iron castings generally use dry quartz sand (washed sand) with a grain size of 30/50.
7. The use of molten iron purification technology
The whole molding process of lost foam castings must consider the problem of molten iron purification, which is one of the key technologies of lost foam casting. The whole process including molten iron smelting, overheating, and pouring into the mold must consider the purification problem, and filtration technology is one of them.
Please keep the source and address of this article for reprinting: Slag Inclusion In Lost Foam Casting
Minghe Die Casting Company are dedicated to manufacture and provide quality and high performance Casting Parts(metal die casting parts range mainly include Thin-Wall Die Casting,Hot Chamber Die Casting,Cold Chamber Die Casting),Round Service(Die Casting Service,Cnc Machining,Mold Making,Surface Treatment).Any custom Aluminum die casting, magnesium or Zamak/zinc die casting and other castings requirements are welcome to contact us.
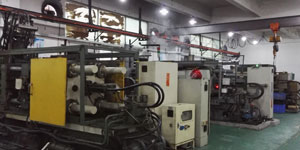
Under the control of ISO9001 and TS 16949,All processes are carried out through hundreds of advanced die casting machines, 5-axis machines, and other facilities, ranging from blasters to Ultra Sonic washing machines.Minghe not only has advanced equipment but also have professional team of experienced engineers,operators and inspectors to make the customer’s design come true.
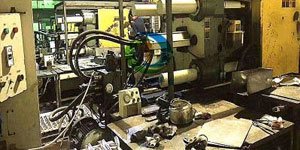
Contract manufacturer of die castings. Capabilities include cold chamber aluminum die casting parts from 0.15 lbs. to 6 lbs., quick change set up, and machining. Value-added services include polishing, vibrating, deburring, shot blasting, painting, plating, coating, assembly, and tooling. Materials worked with include alloys such as 360, 380, 383, and 413.
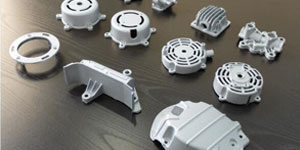
Zinc die casting design assistance/concurrent engineering services. Custom manufacturer of precision zinc die castings. Miniature castings, high pressure die castings, multi-slide mold castings, conventional mold castings, unit die and independent die castings and cavity sealed castings can be manufactured. Castings can be manufactured in lengths and widths up to 24 in. in +/-0.0005 in. tolerance.
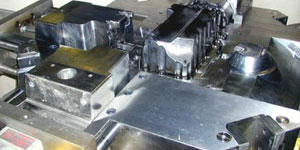
ISO 9001: 2015 certified manufacturer of die cast magnesium, Capabilities include high-pressure magnesium die casting up to 200 ton hot chamber & 3000 ton cold chamber, tooling design, polishing, molding, machining, powder & liquid painting, full QA with CMM capabilities, assembly, packaging & delivery.
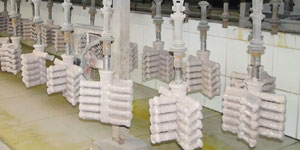
ITAF16949 certified. Additional Casting Service Include investment casting,sand casting,Gravity Casting, Lost Foam Casting,Centrifugal Casting,Vacuum Casting,Permanent Mold Casting,.Capabilities include EDI, engineering assistance, solid modeling and secondary processing.
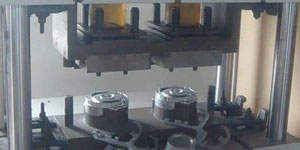
Casting Industries Parts Case Studies for: Cars, Bikes, Aircraft, Musical instruments, Watercraft, Optical devices, Sensors, Models, Electronic devices, Enclosures, Clocks, Machinery, Engines, Furniture, Jewelry, Jigs, Telecom, Lighting, Medical devices, Photographic devices, Robots, Sculptures, Sound equipment, Sporting equipment, Tooling, Toys and more.
What Can we help you do next?
∇ Go To Homepage For Die Casting China
→Casting Parts-Find out what we have done.
→Ralated Tips About Die Casting Services
By Minghe Die Casting Manufacturer |Categories: Helpful Articles |Material Tags: Aluminum Casting, Zinc Casting, Magnesium Casting, Titanium Casting, Stainless Steel Casting, Brass Casting,Bronze Casting,Casting Video,Company History,Aluminum Die Casting |Comments Off