The Reasons For Excessive Carbon Content In the Lost Foam Castings Production
- Unreasonable selection of casting materials. In the selection of casting white mold material, one is the high carbon content; the other is the density of the white mold is too high. As a result, the casting pattern has a high carbon content during thermal decomposition during the pouring process, and the liquid phase and mist free carbon content of the casting during the pouring filling process is high, resulting in an increase in the carburizing probability of the steel casting.
- Choose foam or pre-expanded beads with low carbon content to make castings. At present, the domestically produced polystyrene foam EPS has a carbon content of 92%; the styrene methyl methacrylate copolymer resin STMMAC has a carbon content of 69.6%; the expandable polymethyl methacrylate EPMMA has a carbon content of 60.0 %; The use of EPS material to make the casting mold will increase the carbon content of the molten steel by 0.1% to 0.3% during the casting process. When EPMMA or STMMA is used for the production of the casting mold, the casting is caused by the material of the mold during the pouring process The carbon increase is less than 0.05%.
- Choose the appropriate foam density to make the casting pattern. When ensuring the technical requirements of the pattern making temperature and no other defects caused by the quality of the foam during the production and pouring of the casting, the smaller the foam density of the casting pattern and the less the foam, the better it is to reduce the carburization of the casting.
- Improve the production quality of casting patterns. When the casting pattern can be made as a whole, it should not be made in combination, and the bonding surface of the casting pattern should be minimized. When performing pattern bonding, it is necessary to ensure that the bonding surface of the pattern is smooth and flat, minimize the amount of glue used for bonding, and reduce the amount of thermal decomposition products of the glue to reduce the carbon content of the thermal decomposition products.
- Use low-carbon or carbon-free adhesives. That is, special adhesive for negative pressure casting and bonding should be used for pattern combination bonding, instead of low-quality ordinary adhesives with high carbon content for bonding. And when the pattern is combined and bonded, when ensuring the bonding temperature and bonding strength of the adhesive, the amount of adhesive should be minimized to reduce the thermal decomposition products of the adhesive.
- Choose and determine a reasonable gating system. For the casting process design of the castings, it is necessary to make the castings have the effect of accelerating the gasification of the foamed plastics during the casting process, and minimize and stagger the contact and reaction time of the liquid and solid phases in the thermal decomposition products, thereby reducing or avoiding Carburization of the casting occurs.
- Choose and determine the appropriate pouring temperature and pouring speed of the casting. Due to the different shapes of the same casting such as the casting process, the actual filling temperature of the casting is completely different when the molten steel is poured at the same temperature. If the pouring temperature is increased, the pouring speed will also increase, which will result in faster thermal decomposition of the casting pattern and not easy to complete gasification, which will increase the amount of thermal decomposition products in the liquid phase. At the same time, because the gap between the molten steel and the pattern is small, the liquid phase is After being squeezed out of the gap, the thermal decomposition products are often squeezed between the pattern coating layer and the molten metal, or the cold corners or dead corners where the molten steel flows, causing the contact surface to increase, the carbon concentration and the amount of carburization will also increase. At the same time, pay special attention to the fact that if the casting process is unreasonable, the molten steel pouring temperature is too high and the pouring speed is too fast, it will cause production accidents such as gassing and back spray.
- The flame retardant is added to the pattern to prevent the cracking and combustion of the pattern at high temperature, so that it does not produce or produce less carbon-containing solid products. Such as adding flame retardant 0.5% to 3% chlorinated paraffin, triphosphate, pentabromodiphenyl ether, antimony trioxide, etc. At the same time, add 0.2% to 0.5% dibenzoyl peroxide, dilauroyl peroxide, etc. to accelerate the transformation of flame retardant into gas, thereby reducing the carburizing conditions and conditions during the casting process .
- In the process of brushing the pattern coating layer, anti-carburizing materials can be added. Some anti-carburization catalysts, such as alkali metal salt and limestone powder, are added in the preparation process of the pattern coating, so that the pattern can decompose enough CO and CO2 gas to absorb carbon in the coating layer after pouring, thereby preventing the casting from permeating Carbon; or adding an oxidizer to the coating to promote the transformation of the C and H2 gas after thermal decomposition of the pattern into neutral gas, so that the C and H after thermal decomposition can reduce the penetration into the casting, causing carbon increase or hydrogen embrittlement.
After analyzing and summarizing various possible causes of excessive carbon content in the production of low carbon steel castings in lost foam, the design of the production process and technical parameters of the production of low carbon steel castings in lost foam was modified and adjusted to create a Reasonable and reliable low-carbon steel casting technology conditions set the production operation mode of the system, so as to ensure the technical requirements for the production of qualified low-carbon steel casting products using lost foam.
When adjusting the technical parameter settings of the production operation control process for the production of low-carbon steel castings in the lost foam production, the following points should be paid special attention to:
- When using intermediate frequency smelting, it is necessary to strictly control the batching calculation and the actual batching, material selection and feeding operations of smelting carbon steel. Because the calculation of the ingredients is the key to ensure that the molten steel with qualified composition and the least gas and inclusions are melted to produce high-quality steel casting products. The accuracy of ingredients, selection and feeding is the fundamental guarantee for the quality of casting products. Therefore, a strict sub-inspection system must be carried out for recycled scrap. In particular, it is necessary to remove alloy steel scraps and scraps with unclear materials to ensure that the composition of the smelting ingredients meets the requirements of the casting process technical parameters, which is the first priority in the operation and control of the production of low carbon steel castings in the lost foam.
- Choose foam or pre-expanded beads with low carbon content to make castings. At present, the domestically produced polystyrene foam EPS has a carbon content of 92%; the styrene methyl methacrylate copolymer resin STMMAC has a carbon content of 69.6%; the expandable polymethyl methacrylate EPMMA has a carbon content of 60.0 %; The use of EPS material to make the casting mold will increase the carbon content of the molten steel by 0.1% to 0.3% during the casting process. When the EPMMA or STMMA material is used for the production of the casting mold, the casting is caused by the material of the mold during the pouring process The carbon increase is less than 0.05%.
- Choose the appropriate foam density to make the casting pattern. When ensuring the technical requirements of the pattern making temperature and no other defects caused by the quality of the foam during the production and pouring of the casting, the smaller the foam density of the casting pattern and the less the foam, the better it is to reduce the carburization of the casting.
- Improve the production quality of casting patterns. When the casting pattern can be made as a whole, it should not be made in combination, and the bonding surface of the casting pattern should be minimized. When performing pattern bonding, it is necessary to ensure that the bonding surface of the pattern is smooth and flat, minimize the amount of glue used for bonding, and reduce the amount of thermal decomposition products of the glue to reduce the carbon content of the thermal decomposition products.
- Use low-carbon or carbon-free adhesives. That is, the special glue for negative pressure casting and bonding should be used for the combination of patterns, instead of low-quality ordinary glue with high carbon content for bonding. And when the pattern is combined and bonded, when ensuring the bonding temperature and bonding strength of the adhesive, the amount of adhesive should be minimized to reduce the thermal decomposition products of the adhesive.
- Choose and determine a reasonable gating system. For the casting process design of the castings, it is necessary to make the castings have the effect of accelerating the gasification of the foamed plastics during the casting process, and minimize and stagger the contact and reaction time of the liquid and solid phases in the thermal decomposition products, thereby reducing or avoiding Carburization of the casting occurs.
- Choose and determine the appropriate pouring temperature and pouring speed of the casting. Due to the different shapes of the same casting such as the casting process, the actual filling temperature of the casting is completely different when the molten steel is poured at the same temperature. If the pouring temperature is increased, the pouring speed will also increase, which will result in faster thermal decomposition of the casting pattern and not easy to complete gasification, which will increase the amount of thermal decomposition products in the liquid phase. At the same time, because the gap between the molten steel and the pattern is small, the liquid After being squeezed out of the gap, the thermal decomposition products are often squeezed between the pattern coating layer and the molten metal, or the cold corners or dead corners where the molten steel flows, causing the contact surface to increase, the carbon concentration and the amount of carburization will also increase. At the same time, pay special attention to the fact that if the casting process is unreasonable, the molten steel pouring temperature is too high and the pouring speed is too fast, it will cause production accidents such as gassing and back spray.
- The flame retardant is added to the pattern to prevent the cracking and combustion of the pattern at high temperature, so that it does not produce or produce less carbon-containing solid products. Such as adding flame retardant 0.5% to 3% chlorinated paraffin, triphosphate, pentabromodiphenyl ether, antimony trioxide, etc. At the same time, add 0.2% to 0.5% dibenzoyl peroxide, dilauroyl peroxide, etc. to accelerate the transformation of flame retardant into gas, thereby reducing the carburizing conditions and conditions during the casting process .
- In the process of brushing the pattern coating layer, anti-carburizing materials can be added. Some anti-carburization catalysts, such as alkali metal salt and limestone powder, are added in the preparation process of the pattern coating, so that the pattern can decompose enough CO and CO2 gas to absorb carbon in the coating layer after pouring, thereby preventing the casting from permeating Carbon; or adding an oxidizer to the coating to promote the transformation of the C and H2 gas after thermal decomposition of the pattern into neutral gas, so that the C and H after thermal decomposition can reduce the penetration into the casting, causing carbon increase or hydrogen embrittlement.
After analyzing and summarizing various possible causes of excessive carbon content in the production of low carbon steel castings in lost foam, the design of the production process and technical parameters of the production of low carbon steel castings in lost foam was modified and adjusted to create a Reasonable and reliable low-carbon steel casting technology conditions set the production operation mode of the system, so as to ensure the technical requirements for the production of qualified low-carbon steel casting products using lost foam. When adjusting the technical parameter settings of the production operation control process for the production of low-carbon steel castings in the lost foam production, the following points should be paid special attention to:
- When using intermediate frequency smelting, it is necessary to strictly control the batching calculation and the actual batching, material selection and feeding operations of smelting carbon steel. Because the calculation of the ingredients is the key to ensure that the molten steel with qualified composition and the least gas and inclusions are melted to produce high-quality steel casting products. The accuracy of ingredients, selection and feeding is the fundamental guarantee for the quality of casting products. Therefore, a strict sub-inspection system must be carried out for recycled scrap. In particular, it is necessary to remove alloy steel scraps and scraps with unclear materials to ensure that the composition of the smelting ingredients meets the requirements of the casting process technical parameters, which is the first priority in the operation and control of the production of low carbon steel castings in the lost foam.
- Choose foam or pre-expanded beads with low carbon content to make castings. At present, the domestically produced polystyrene foam EPS has a carbon content of 92%; the styrene methyl methacrylate copolymer resin STMMAC has a carbon content of 69.6%; the expandable polymethyl methacrylate EPMMA has a carbon content of 60.0 %; The use of EPS material to make the casting mold will increase the carbon content of the molten steel by 0.1% to 0.3% during the casting process. When the EPMMA or STMMA material is used for the production of the casting mold, the casting is caused by the material of the mold during the pouring process The carbon increase is less than 0.05%.
- Choose the appropriate foam density to make the casting pattern. When ensuring the technical requirements of the pattern making temperature and no other defects caused by the quality of the foam during the production and pouring of the casting, the smaller the foam density of the casting pattern and the less the foam, the better it is to reduce the carburization of the casting.
- Improve the production quality of casting patterns. When the casting pattern can be made as a whole, it should not be made in combination, and the bonding surface of the casting pattern should be minimized. When performing pattern bonding, it is necessary to ensure that the bonding surface of the pattern is smooth and flat, minimize the amount of glue used for bonding, and reduce the amount of thermal decomposition products of the glue to reduce the carbon content of the thermal decomposition products.
- Use low-carbon or carbon-free adhesives. That is, special adhesive for negative pressure casting and bonding should be used for pattern combination bonding, instead of low-quality ordinary adhesives with high carbon content for bonding. And when the pattern is combined and bonded, when ensuring the bonding temperature and bonding strength of the adhesive, the amount of adhesive should be minimized to reduce the thermal decomposition products of the adhesive.
- Choose and determine a reasonable gating system. For the casting process design of the castings, it is necessary to make the castings have the effect of accelerating the gasification of the foamed plastics during the casting process, and minimize and stagger the contact and reaction time of the liquid and solid phases in the thermal decomposition products, thereby reducing or avoiding Carburization of the casting occurs.
- Choose and determine the appropriate pouring temperature and pouring speed of the casting. Due to the different shapes of the same casting such as the casting process, the actual filling temperature of the casting is completely different when the molten steel is poured at the same temperature. If the pouring temperature is increased, the pouring speed will also increase, which will result in faster thermal decomposition of the casting pattern and not easy to complete gasification, which will increase the amount of thermal decomposition products in the liquid phase. At the same time, because the gap between the molten steel and the pattern is small, the liquid After being squeezed out of the gap, the thermal decomposition products are often squeezed between the pattern coating layer and the molten metal, or the cold corners or dead corners where the molten steel flows, causing the contact surface to increase, the carbon concentration and the amount of carburization will also increase. At the same time, pay special attention to the fact that if the casting process is unreasonable, the molten steel pouring temperature is too high and the pouring speed is too fast, it will cause production accidents such as gassing and back spray.
- The flame retardant is added to the pattern to prevent the cracking and combustion of the pattern at high temperature, so that it does not produce or produce less carbon-containing solid products. Such as adding flame retardant 0.5% to 3% chlorinated paraffin, triphosphate, pentabromodiphenyl ether, antimony trioxide, etc. At the same time, add 0.2% to 0.5% dibenzoyl peroxide, dilauroyl peroxide, etc. to accelerate the transformation of flame retardant into gas, thereby reducing the carburizing conditions and conditions during the casting process .
- In the process of brushing the pattern coating layer, anti-carburizing materials can be added. Add some anti-carburization catalysts, such as alkali metal salt and limestone powder, during the preparation process of the pattern paint, so that the pattern can decompose enough CO and CO2 gas to absorb carbon in the paint layer after pouring, thereby preventing the casting from permeating. Carbon; or adding an oxidizer to the coating to promote the transformation of the C and H2 gas after thermal decomposition of the pattern into neutral gas, so that the C and H after thermal decomposition can reduce the penetration into the casting, causing carbon increase or hydrogen embrittlement.
- Strictly control the quality of sand recycling treatment. Ensure that the production and use of molding sand meet the requirements of process technical parameters, especially the content of dust in the molding sand must be strictly controlled to prevent the air permeability of the casting sand box from being reduced due to the dust, causing the thermal decomposition products of the casting pattern to be unable to be discharged from the casting cavity in time, and Increase the recarburization rate of castings.
- When low-carbon steel castings are produced and poured, the vacuum of the casting flask must be increased. The moulding sand box should adopt the structure of box wall vacuuming. When pouring, the box wall vacuuming can accelerate the escape of thermal decomposition products to the outside of the mold cavity, thereby reducing the concentration and contact time of thermal decomposition products of the pattern, and reducing or avoiding cast steel Carburization and carbon deposition of parts. When the size of molding sand is between 20 mesh and 40 mesh, 0.03MPa~0.06MPa is suitable when casting steel castings. If the negative pressure is too large, it will cause sand sticking and other defects in the casting.
- For the pouring of low carbon steel castings, the bottom pouring method should be used as much as possible to make the filling flow of the molten steel smooth, and the thermal decomposition products of the pattern can smoothly enter the slag collection cavity or riser, thereby reducing and reducing the thermal decomposition of the pattern The contact reaction time of the liquid phase and the solid phase in the product reduces and eliminates the probability of carbon increase. The use of rain pouring system to pouring low-carbon steel castings will increase the working conditions and conditions of carburization, carburization, and carbon deposition of the castings, and cause serious defects in the castings and are not suitable for use.
Please keep the source and address of this article for reprinting: The Reasons For Excessive Carbon Content In the Lost Foam Castings Production
Minghe Die Casting Company are dedicated to manufacture and provide quality and high performance Casting Parts(metal die casting parts range mainly include Thin-Wall Die Casting,Hot Chamber Die Casting,Cold Chamber Die Casting),Round Service(Die Casting Service,Cnc Machining,Mold Making,Surface Treatment).Any custom Aluminum die casting, magnesium or Zamak/zinc die casting and other castings requirements are welcome to contact us.
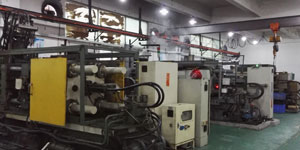
Under the control of ISO9001 and TS 16949,All processes are carried out through hundreds of advanced die casting machines, 5-axis machines, and other facilities, ranging from blasters to Ultra Sonic washing machines.Minghe not only has advanced equipment but also have professional team of experienced engineers,operators and inspectors to make the customer’s design come true.
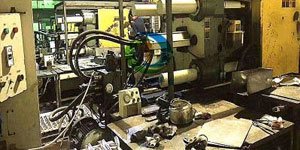
Contract manufacturer of die castings. Capabilities include cold chamber aluminum die casting parts from 0.15 lbs. to 6 lbs., quick change set up, and machining. Value-added services include polishing, vibrating, deburring, shot blasting, painting, plating, coating, assembly, and tooling. Materials worked with include alloys such as 360, 380, 383, and 413.
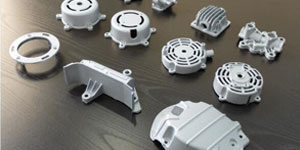
Zinc die casting design assistance/concurrent engineering services. Custom manufacturer of precision zinc die castings. Miniature castings, high pressure die castings, multi-slide mold castings, conventional mold castings, unit die and independent die castings and cavity sealed castings can be manufactured. Castings can be manufactured in lengths and widths up to 24 in. in +/-0.0005 in. tolerance.
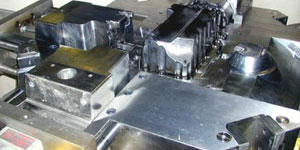
ISO 9001: 2015 certified manufacturer of die cast magnesium, Capabilities include high-pressure magnesium die casting up to 200 ton hot chamber & 3000 ton cold chamber, tooling design, polishing, molding, machining, powder & liquid painting, full QA with CMM capabilities, assembly, packaging & delivery.
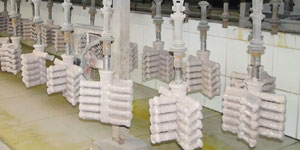
ITAF16949 certified. Additional Casting Service Include investment casting,sand casting,Gravity Casting, Lost Foam Casting,Centrifugal Casting,Vacuum Casting,Permanent Mold Casting,.Capabilities include EDI, engineering assistance, solid modeling and secondary processing.
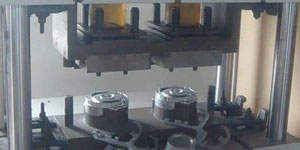
Casting Industries Parts Case Studies for: Cars, Bikes, Aircraft, Musical instruments, Watercraft, Optical devices, Sensors, Models, Electronic devices, Enclosures, Clocks, Machinery, Engines, Furniture, Jewelry, Jigs, Telecom, Lighting, Medical devices, Photographic devices, Robots, Sculptures, Sound equipment, Sporting equipment, Tooling, Toys and more.
What Can we help you do next?
∇ Go To Homepage For Die Casting China
→Casting Parts-Find out what we have done.
→Ralated Tips About Die Casting Services
By Minghe Die Casting Manufacturer |Categories: Helpful Articles |Material Tags: Aluminum Casting, Zinc Casting, Magnesium Casting, Titanium Casting, Stainless Steel Casting, Brass Casting,Bronze Casting,Casting Video,Company History,Aluminum Die Casting |Comments Off