The Production and Application of Casting Wheel Grinder
With the changes in the international and domestic economic situations, market competition has become more intense, and various customers have put forward clear standards for the appearance of castings, and customers have higher and higher requirements for the appearance of castings.
At present, the common problems faced by the foundry industry are the difficulty in recruiting workers and the sharp increase in labor costs, which has brought great pressure to the company's production and operation.
At the same time, due to the relatively backward technology and equipment of shovel grinding, it can only rely on increasing the number of personnel to increase production. The increase in personnel, on the one hand, has led to a tight work site, on the other hand, it has brought great pressure on the safety management of the factory. The use of advanced technology or equipment has become a requirement for current production development.
At present, the main tools used for shovel grinding operations are: electric 180 angular grinder, pneumatic S150 parallel grinder, pneumatic S60 parallel grinder, pneumatic SJ125 angular grinder, etc. In recent years, with the emergence of high-frequency grinders, its no-load and load speeds have been greatly improved compared with current pneumatic equipment. Research on the application of high-frequency grinders in relief grinding of castings will promote the improvement of the efficiency of relief grinding operations in the foundry industry. As well as reducing labor costs are of great significance.
1. Features of high frequency grinder
In electrical engineering, more than 10kHz is called high frequency. However, for power tools, all frequencies higher than the standard grid frequency (50/60Hz) are defined as high frequency. Nowadays, the main frequency used by high-frequency power tools is 300Hz.
Compared with ordinary frequency electric tools and pneumatic tools, the main features of high frequency grinders are as follows:
- (1) The speed drop is small during high-load operation (only 3%~15%), and keep working at a constant speed. It is more efficient than ordinary frequency tools and pneumatic tools (the speed is reduced by 30% to 40%, or even more), so the high frequency machine can improve the grinding efficiency, increase the output, and lower the loss of the diamond grinding wheel. Figure 2 shows the speed comparison of the high-frequency machine and the pneumatic and ordinary motors.
- (2) The structure is simple, the cage rotor has no copper head and no carbon brush design, and has a long service life (up to 10 years). The use of pneumatic tools must not only maintain the tool itself, but also maintain the entire compression system, control system, and connection system. A rated output of 1kW requires a compressor loss of 8kW, which has high noise and vibration during use. With ordinary electric grinders, wearing parts such as carbon brushes and rotors need to be replaced once a month, and the life of the whole machine is about three months.
- (3) Fully enclosed motor and surface cooling system, dust cannot enter the motor, suitable for operation in harsh working environments.
- (4) The power is strong, the best power-to-weight ratio, and can work continuously for 24 hours; the frequency converter is sturdy and durable, the service life is as long as 10-15 years, and basically does not need any maintenance.
2. Research and application of high frequency grinder
The speed of the high-frequency 180 machine under load is reduced to 134r/min, and the speed reduction ratio is only 1.57%, while the speed of the ordinary air-driven 180 machine is reduced by 1000r/min under load, and the speed reduction ratio is 13.88%. Compare the efficiency ratio of the two under load conditions: 8386/6200=1.35, it can be seen that the efficiency of the high-frequency 180 machine is 1.35 times that of the ordinary pneumatic grinder; the same method, the efficiency of the high-frequency 60 machine is tested for the ordinary wind machine 1.93 times.
In order to further verify the effect, and carry out the polishing test of the comparison sample, by measuring the polishing time of the same block, the effect analysis is carried out: the high-frequency 180 machine takes 177s, and the pneumatic 180 machine takes 286s. The efficiency comparison between the two: 177=1.61, and greater than 1.35 in the previous test, which indicates that the amount of grinding per revolution per unit time of the high-frequency machine under load is greater than that of the ordinary pneumatic grinder. At the same time, the high-frequency machine has a very high speed. (Under no-load conditions, the high-frequency 180 machine is 1.18 times that of the ordinary 180 machine, and the high-frequency 60 machine is 1.45 times that of the ordinary 60 machine), so the high-frequency machine has higher efficiency.
3. The effect of using high frequency grinder
After the application of the high-frequency grinder, the subsequent product cleaning speed has been greatly improved. Figure 4 is a machine bed produced for a user, with a weight of 5060kg and a size of 2485mm×1752mm×1177mm. The cleaning cycle is approximately determined by the use of a pneumatic grinder. 27h is shortened to about 17h cleaned by a high-frequency grinder, the cleaning time is reduced by 37%, and the cleaning efficiency is significantly improved.
Compared with pneumatic tools, the use of high-frequency machines to polish castings reduces the average cleaning time by about 30%, significantly shortens the cleaning cycle, saves human resources, and promotes the progress of production.
Please keep the source and address of this article for reprinting: The Production and Application of Casting Wheel Grinder
Minghe Die Casting Company are dedicated to manufacture and provide quality and high performance Casting Parts(metal die casting parts range mainly include Thin-Wall Die Casting,Hot Chamber Die Casting,Cold Chamber Die Casting),Round Service(Die Casting Service,Cnc Machining,Mold Making,Surface Treatment).Any custom Aluminum die casting, magnesium or Zamak/zinc die casting and other castings requirements are welcome to contact us.
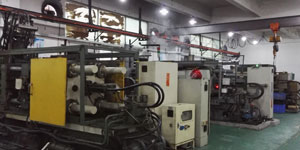
Under the control of ISO9001 and TS 16949,All processes are carried out through hundreds of advanced die casting machines, 5-axis machines, and other facilities, ranging from blasters to Ultra Sonic washing machines.Minghe not only has advanced equipment but also have professional team of experienced engineers,operators and inspectors to make the customer’s design come true.
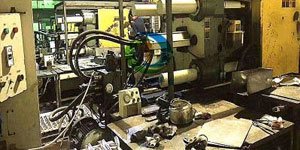
Contract manufacturer of die castings. Capabilities include cold chamber aluminum die casting parts from 0.15 lbs. to 6 lbs., quick change set up, and machining. Value-added services include polishing, vibrating, deburring, shot blasting, painting, plating, coating, assembly, and tooling. Materials worked with include alloys such as 360, 380, 383, and 413.
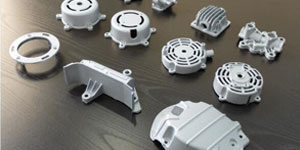
Zinc die casting design assistance/concurrent engineering services. Custom manufacturer of precision zinc die castings. Miniature castings, high pressure die castings, multi-slide mold castings, conventional mold castings, unit die and independent die castings and cavity sealed castings can be manufactured. Castings can be manufactured in lengths and widths up to 24 in. in +/-0.0005 in. tolerance.
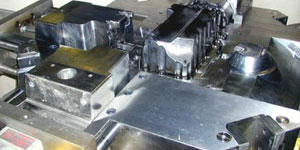
ISO 9001: 2015 certified manufacturer of die cast magnesium, Capabilities include high-pressure magnesium die casting up to 200 ton hot chamber & 3000 ton cold chamber, tooling design, polishing, molding, machining, powder & liquid painting, full QA with CMM capabilities, assembly, packaging & delivery.
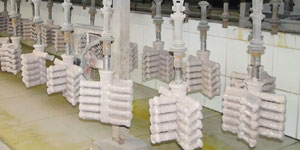
ITAF16949 certified. Additional Casting Service Include investment casting,sand casting,Gravity Casting, Lost Foam Casting,Centrifugal Casting,Vacuum Casting,Permanent Mold Casting,.Capabilities include EDI, engineering assistance, solid modeling and secondary processing.
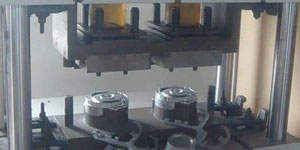
Casting Industries Parts Case Studies for: Cars, Bikes, Aircraft, Musical instruments, Watercraft, Optical devices, Sensors, Models, Electronic devices, Enclosures, Clocks, Machinery, Engines, Furniture, Jewelry, Jigs, Telecom, Lighting, Medical devices, Photographic devices, Robots, Sculptures, Sound equipment, Sporting equipment, Tooling, Toys and more.
What Can we help you do next?
∇ Go To Homepage For Die Casting China
→Casting Parts-Find out what we have done.
→Ralated Tips About Die Casting Services
By Minghe Die Casting Manufacturer |Categories: Helpful Articles |Material Tags: Aluminum Casting, Zinc Casting, Magnesium Casting, Titanium Casting, Stainless Steel Casting, Brass Casting,Bronze Casting,Casting Video,Company History,Aluminum Die Casting |Comments Off