The Reconstruction Design Scheme Of Resin Sand In Small Foundry
At present, small foundries occupies an important position in my country's foundry production, but there are common phenomena in small foundries such as low level of technology, low grades of castings, low labor productivity, and harsh environment, which severely restrict the development of my country's foundry industry. . In order to adapt to the situation and broaden the market, it is necessary to improve the appearance quality, internal quality and dimensional accuracy of castings, reduce the rejection rate of castings, and improve production efficiency. In order to achieve this goal, the use of resin sand technology is very necessary. The reconstruction of resin sand in small foundries must use the original equipment as much as possible according to its own economic strength and technical strength to ensure quality, reduce investment, and achieve good benefits.
The design principle of resin sand transformation of small foundry:
- The production line should have fewer links and a compact structure.
- The host of the equipment must be reliable, and the equipment of a reliable manufacturer should be selected according to economic strength.
- The investment should be less, and the auxiliary unit should be prepared by itself as much as possible.
Resin sand production line mainly includes sand mixing molding system and falling sand regeneration system.
The sand mixing molding system includes resin sand sand mixer, pneumatic vibrating table, roller table and other equipment
The correct selection of sand mixing equipment has a great influence on the performance of resin sand. The requirements for the sand mixer are accurate quantitative, uniform mixing and good coating effect, as well as equipment quality, maintenance and product prices. At present, resin sand mixers are generally divided into batch and continuous types. According to the output of the small workshop, the cantilever type continuous resin sand mixer of 5~10t/h can be used. If the core volume is large, a batch-type sand mixer can be used to mix the core sand. Sand enters the sand mixer through the screw feeder from the storage hopper, and the flow rate of the resin and curing agent is controlled by a quantitative pump according to the required ratio.
Non-motorized roller table can be self-made. The use of the stick channel and the transitional modeling trolley can effectively expand the modeling space, and the installation of a vibrating table in the stick channel under the sand mixer can increase the compactness of the sand mold and improve the quality of castings.
According to the characteristics of small-scale casting workshops with multiple varieties and small batches or single-piece production, the molding system should mainly adopt manual molding, without forming a mechanized assembly line.
The resin sand shakeout recycling equipment must meet the quality requirements of recycled sand
There are three main indicators for measuring the quality of reclaimed sand.
- Micropowder content” If the micropowder content is high, the amount of resin added will be high, which will reduce the strength of the resin sand. In order to reduce the content of fine powder, a dust removal system is generally configured to take measures to force dust removal.
- Ignition loss. Small ignition loss is the main factor that causes defects such as porosity in castings. Generally, the ignition loss of iron castings is controlled to be less than 3.0%.
- Sand temperature determines the hardening speed of the sand mold. According to the production cycle, it is necessary to decide whether to configure sand temperature adjustment equipment. If the production is continuous, the furnace is opened every 2 to 3 days, and the sand temperature regulator is not required.
The main item of sand falling recycling equipment is the vibrating sand falling machine. After boxing, the old sand must be crushed first, the sand blocks of different sizes are broken into sand particles, and then the iron and debris in the sand are removed by magnetic separation and sieving. For example, the YZZ series vibration crushing and recycling machine produced by Suzhou Tongli Machinery Factory uses two cross-symmetrical vibration motors installed at the bottom to cause the old sand blocks to collide with each other. The sand blocks are broken during the vibration process. Friction to remove the resin film on the surface of the sand grains and regenerate the old sand. The equipment also has the functions of sand falling, crushing, screening, and regeneration.
The sand conveying and lifting equipment can be flexibly combined
To make the sand treatment system equipment combination of small foundries reasonable and compact. In order to reduce costs, try to use the original sand processing system to reform, horizontal conveying chooses a belt conveyor with magnetic separation, and vertical conveying can choose a bucket elevator. In the conveying process, dust removal equipment for forced dust removal shall be equipped. The sand storehouse can be used for old materials. If the new system can be used, the cone-shaped sand storehouse should be used. The inclination angle of the sand storehouse should be greater than 60° to increase the effective capacity.
Dust removal and winnowing design
In the production of resin sand, there are mainly several sources of dust: the dust formed after the resin film is burnt; the powder formed after the paint is burned; the dust formed by the addition of belts in the original sand and the crushing of sand particles. Therefore, the dust removal equipment is required not only to have sufficient air volume, but also to require an appropriate negative pressure. In the renovated small casting workshop, the original dust removal equipment can be used, and new dust removal points and air ducts can be supplemented. If new equipment is added, a fan with a wind pressure of 5.2kPa can be used. The consumption is 500m³. A sealed silo is installed on the sand silo, and the top of the silo is equipped with a suction port to separate the dust by the flow of sand. In addition, an air suction hood is installed on the upper part of the vibrating sand shaker to absorb dust when the molding sand is vibrated. Install dust removal equipment with adjustable wind power at the exit of the bucket elevator for winnowing.
Alcohol-based coatings are generally used in the production of resin sand cast iron parts
Spray or brush the alcohol-based paint on the resin sand mold, and then ignite it to achieve surface drying. The application and drying process can be completed within a few minutes, and the production cycle is short. The flow coater can be purchased or self-made according to the variety and batch of castings.
Design examples
After manual sand falling, the old sand enters the vibrating sand shaker through the feeding belt conveyor to complete the sand falling, crushing, screening, regeneration, and enters the bucket elevator through the conveyor belt with magnetic separation, and the new sand is manually added during the conveying process. A winnowing device is installed at the exit of the bucket lift, and the moulding sand after winnowing enters the sand storage bucket via a belt conveyor. During production, the molding sand enters the sand mixer from the sand hopper through the screw feeder.
Conclusion
For the transformation of resin sand in small foundries, we must first make a reasonable choice in the process, maximize the ergonomics, ensure the quality and performance of the main equipment of the equipment, and meet the requirements of the auxiliary equipment, save money as much as possible, and ensure the quality of the raw materials. Quality, in order to produce good castings.
Please keep the source and address of this article for reprinting: The Reconstruction Design Scheme Of Resin Sand In Small Foundry
Minghe Die Casting Company are dedicated to manufacture and provide quality and high performance Casting Parts(metal die casting parts range mainly include Thin-Wall Die Casting,Hot Chamber Die Casting,Cold Chamber Die Casting),Round Service(Die Casting Service,Cnc Machining,Mold Making,Surface Treatment).Any custom Aluminum die casting, magnesium or Zamak/zinc die casting and other castings requirements are welcome to contact us.
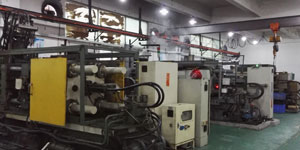
Under the control of ISO9001 and TS 16949,All processes are carried out through hundreds of advanced die casting machines, 5-axis machines, and other facilities, ranging from blasters to Ultra Sonic washing machines.Minghe not only has advanced equipment but also have professional team of experienced engineers,operators and inspectors to make the customer’s design come true.
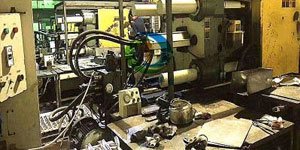
Contract manufacturer of die castings. Capabilities include cold chamber aluminum die casting parts from 0.15 lbs. to 6 lbs., quick change set up, and machining. Value-added services include polishing, vibrating, deburring, shot blasting, painting, plating, coating, assembly, and tooling. Materials worked with include alloys such as 360, 380, 383, and 413.
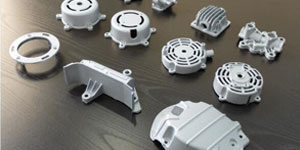
Zinc die casting design assistance/concurrent engineering services. Custom manufacturer of precision zinc die castings. Miniature castings, high pressure die castings, multi-slide mold castings, conventional mold castings, unit die and independent die castings and cavity sealed castings can be manufactured. Castings can be manufactured in lengths and widths up to 24 in. in +/-0.0005 in. tolerance.
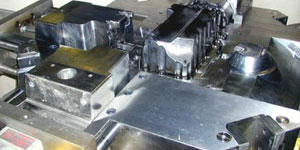
ISO 9001: 2015 certified manufacturer of die cast magnesium, Capabilities include high-pressure magnesium die casting up to 200 ton hot chamber & 3000 ton cold chamber, tooling design, polishing, molding, machining, powder & liquid painting, full QA with CMM capabilities, assembly, packaging & delivery.
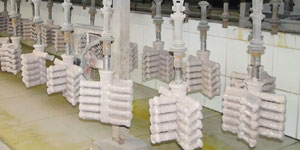
ITAF16949 certified. Additional Casting Service Include investment casting,sand casting,Gravity Casting, Lost Foam Casting,Centrifugal Casting,Vacuum Casting,Permanent Mold Casting,.Capabilities include EDI, engineering assistance, solid modeling and secondary processing.
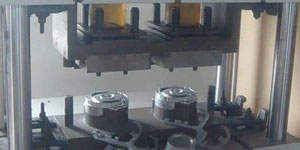
Casting Industries Parts Case Studies for: Cars, Bikes, Aircraft, Musical instruments, Watercraft, Optical devices, Sensors, Models, Electronic devices, Enclosures, Clocks, Machinery, Engines, Furniture, Jewelry, Jigs, Telecom, Lighting, Medical devices, Photographic devices, Robots, Sculptures, Sound equipment, Sporting equipment, Tooling, Toys and more.
What Can we help you do next?
∇ Go To Homepage For Die Casting China
→Casting Parts-Find out what we have done.
→Ralated Tips About Die Casting Services
By Minghe Die Casting Manufacturer |Categories: Helpful Articles |Material Tags: Aluminum Casting, Zinc Casting, Magnesium Casting, Titanium Casting, Stainless Steel Casting, Brass Casting,Bronze Casting,Casting Video,Company History,Aluminum Die Casting |Comments Off