The Forging Technology Of Bow Shackle
Shackles can be seen all the time in life, so do we know about shackles? Let Minghe introduce the improvement of forging process of shackle forging
Wide anvil pressing process
The wide anvil pressing process of bow shackle adopts wide flat anvil surface, large feed rate and arc pressure to improve the internal quality, to forge the internal porosity of ingot and reduce the influence of segregation, so that the forging can get a solid core. For high alloy copper forgings, the center part of bow shackle is forged with 135 upper and lower V-anvil, which is more effective than that of flat anvil grade alloy steel. In addition to forging test with flat anvil, the upper wide anvil and the lower wide anvil are also used. The results show that the latter has a good effect in compacting the loose part in the center, and the latter is better than the latter. The key is to make the anvil face wider, the reduction larger and the contact surface between anvil and steel key larger. To press through the center.
Direct drawing process
The large steel key is directly forged to the size of the forging with a certain forging ratio without pier thickness, and the quality is exactly the same as that of the forging. Therefore, it is generally directly from ingot to forging, unless the subscriber requires forging, or forging bow shackle ratio is insufficient, forging must be carried out. The forging ratio of large ingot should be at least 4:1, which can ensure the center part to be forged. For the forging with thick pier after rough forging, the forging ratio of rough forging should be 2:1, the deformation of thick pier should be at least 50% (pier ratio 2-2.2), and the forging ratio should not be less than 2:1 after rough forging. When the minimum forging ratio cannot be reached, the pier should be lengthened.
Hollow punching technology
In the past, the solid punch was used to punch the core hole, but there were still residual non-metallic inclusions. After that, the 450 mm hollow punch was used to punch the core hole, and then the forging was carried out on the 10000 ton hydraulic press. Finally, the 300 mm hollow punch was used to punch the hole to ensure the quality of the inner hole of the impeller.
Installation of device and debugging shackle. After the shackle is installed, it should be ensured that the pin shaft can rotate in the hole of the object to be lifted, and the BW shackle and BX shackle should be used to repair the shackle. It should be stored in dry, wet and high temperature environment. It can be directly hung on the hook tip. The thickness of the ear plate of the object to be lifted for the installation of the shackle and single leg rigging shall be moderate. After the shackle is installed, the use and operation of the shackle body shall be ensured.
The limit working load and scope of application of the shackle are the test and detection of the shackle. During the lifting process, the objects to be lifted shall not be collided and impacted. The lifting process should be stable as far as possible. It is strictly forbidden to stand below or connect any shackle on the goods. Before use, it is necessary to test the lifting before lifting. Select the limit working load coefficient of the lifting point shackle in high and low temperature environment, and hang the shackle directly into the force center of the hook.
Please keep the source and address of this article for reprinting:The Forging Technology Of Bow Shackle
Minghe Die Casting Company are dedicated to manufacture and provide quality and high performance Casting Parts(metal die casting parts range mainly include Thin-Wall Die Casting,Hot Chamber Die Casting,Cold Chamber Die Casting),Round Service(Die Casting Service,Cnc Machining,Mold Making,Surface Treatment).Any custom Aluminum die casting, magnesium or Zamak/zinc die casting and other castings requirements are welcome to contact us.
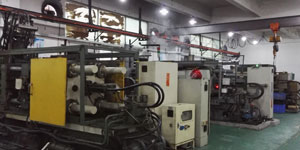
Under the control of ISO9001 and TS 16949,All processes are carried out through hundreds of advanced die casting machines, 5-axis machines, and other facilities, ranging from blasters to Ultra Sonic washing machines.Minghe not only has advanced equipment but also have professional team of experienced engineers,operators and inspectors to make the customer’s design come true.
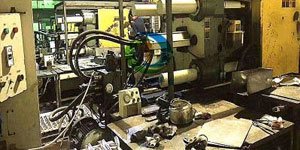
Contract manufacturer of die castings. Capabilities include cold chamber aluminum die casting parts from 0.15 lbs. to 6 lbs., quick change set up, and machining. Value-added services include polishing, vibrating, deburring, shot blasting, painting, plating, coating, assembly, and tooling. Materials worked with include alloys such as 360, 380, 383, and 413.
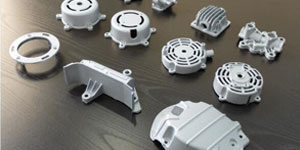
Zinc die casting design assistance/concurrent engineering services. Custom manufacturer of precision zinc die castings. Miniature castings, high pressure die castings, multi-slide mold castings, conventional mold castings, unit die and independent die castings and cavity sealed castings can be manufactured. Castings can be manufactured in lengths and widths up to 24 in. in +/-0.0005 in. tolerance.
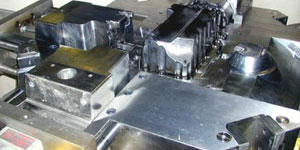
ISO 9001: 2015 certified manufacturer of die cast magnesium, Capabilities include high-pressure magnesium die casting up to 200 ton hot chamber & 3000 ton cold chamber, tooling design, polishing, molding, machining, powder & liquid painting, full QA with CMM capabilities, assembly, packaging & delivery.
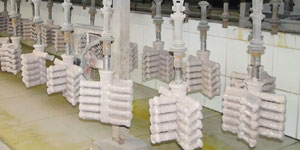
ITAF16949 certified. Additional Casting Service Include investment casting,sand casting,Gravity Casting, Lost Foam Casting,Centrifugal Casting,Vacuum Casting,Permanent Mold Casting,.Capabilities include EDI, engineering assistance, solid modeling and secondary processing.
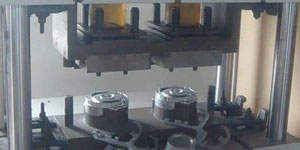
Casting Industries Parts Case Studies for: Cars, Bikes, Aircraft, Musical instruments, Watercraft, Optical devices, Sensors, Models, Electronic devices, Enclosures, Clocks, Machinery, Engines, Furniture, Jewelry, Jigs, Telecom, Lighting, Medical devices, Photographic devices, Robots, Sculptures, Sound equipment, Sporting equipment, Tooling, Toys and more.
What Can we help you do next?
∇ Go To Homepage For Die Casting China
→Casting Parts-Find out what we have done.
→Ralated Tips About Die Casting Services
By Minghe Die Casting Manufacturer |Categories: Helpful Articles |Material Tags: Aluminum Casting, Zinc Casting, Magnesium Casting, Titanium Casting, Stainless Steel Casting, Brass Casting,Bronze Casting,Casting Video,Company History,Aluminum Die Casting |Comments Off