The Process System Of Powder Forging
Traditional ordinary die forging and mechanical processing methods have been unable to meet the requirements of high quality, high precision, high efficiency, low consumption and low cost in today's industrial production of automobiles and motorcycles. The powder forging process is a relatively competitive, non-cutting metal processing method developed by the organic combination of powder metallurgy process and precision forging.
Powder forging uses metal powder as raw material, pre-formed and pressed, and heated and sintered in a protective atmosphere. As a forging blank, it is forged on a press at one time and realizes flash-free precision die forging to obtain the same density and complex shape as ordinary die forgings. Precision forgings. Requirements of powder forging process:
- Ingredients and mixtures. According to the material and performance requirements of different products, select the appropriate low-alloy steel powder, calculate the ingredients and accurately weigh the powder, and mix it in the mixer until it is evenly distributed.
- Press the preform. The powder is pressed into a preform on the press. The design of the preform should be reasonable, and its density, quality, quality change and size should be strictly controlled to avoid overloading and damaging the mold.
- Sintering. It is carried out in a sintering furnace with a reducing protective atmosphere at a temperature of 1100 to 1130°C to complete alloying. Then, the sintered body is moved into a heat preservation furnace (about 1000°C) in a non-oxidizing atmosphere for heat preservation.
- Closed die forging. At present, there are two forging processes for sintered bodies: one is to use the waste heat of the sintered body to keep it to the forging temperature and immediately forge to save energy; the other is to reheat the sintered body after it has cooled to room temperature, and then perform forging. Energy consumption is relatively increasing. When the sintered body is densified and closed die forging, the sintered body with 80% of the theoretical density can be forged until it is close to 100% of the theoretical density. It must be pointed out that in the forging deformation, the shape of the preform should be designed reasonably to reduce the lateral flow of metal and reduce the wear of the forging die.
The powder forging process not only has the advantages of better powder metallurgy forming performance, but also has the characteristics of forging deformation that can effectively change the structure and performance of metal materials, making powder metallurgy and forging processes have achieved new breakthroughs in production, especially suitable for large batches It produces high-strength, complex-shaped parts, so it has a great development prospect for popularization and application in various industrial sectors.
Please keep the source and address of this article for reprinting:The Process System Of Powder Forging
Minghe Die Casting Company are dedicated to manufacture and provide quality and high performance Casting Parts(metal die casting parts range mainly include Thin-Wall Die Casting,Hot Chamber Die Casting,Cold Chamber Die Casting),Round Service(Die Casting Service,Cnc Machining,Mold Making,Surface Treatment).Any custom Aluminum die casting, magnesium or Zamak/zinc die casting and other castings requirements are welcome to contact us.
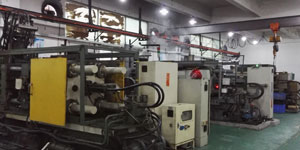
Under the control of ISO9001 and TS 16949,All processes are carried out through hundreds of advanced die casting machines, 5-axis machines, and other facilities, ranging from blasters to Ultra Sonic washing machines.Minghe not only has advanced equipment but also have professional team of experienced engineers,operators and inspectors to make the customer’s design come true.
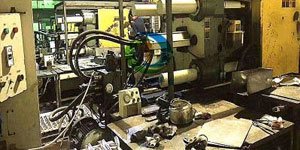
Contract manufacturer of die castings. Capabilities include cold chamber aluminum die casting parts from 0.15 lbs. to 6 lbs., quick change set up, and machining. Value-added services include polishing, vibrating, deburring, shot blasting, painting, plating, coating, assembly, and tooling. Materials worked with include alloys such as 360, 380, 383, and 413.
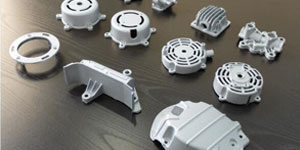
Zinc die casting design assistance/concurrent engineering services. Custom manufacturer of precision zinc die castings. Miniature castings, high pressure die castings, multi-slide mold castings, conventional mold castings, unit die and independent die castings and cavity sealed castings can be manufactured. Castings can be manufactured in lengths and widths up to 24 in. in +/-0.0005 in. tolerance.
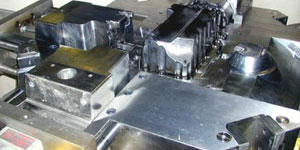
ISO 9001: 2015 certified manufacturer of die cast magnesium, Capabilities include high-pressure magnesium die casting up to 200 ton hot chamber & 3000 ton cold chamber, tooling design, polishing, molding, machining, powder & liquid painting, full QA with CMM capabilities, assembly, packaging & delivery.
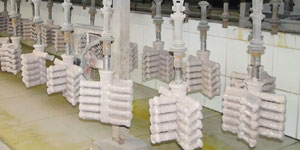
ITAF16949 certified. Additional Casting Service Include investment casting,sand casting,Gravity Casting, Lost Foam Casting,Centrifugal Casting,Vacuum Casting,Permanent Mold Casting,.Capabilities include EDI, engineering assistance, solid modeling and secondary processing.
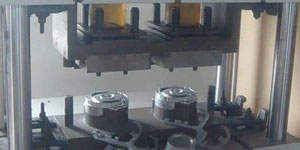
Casting Industries Parts Case Studies for: Cars, Bikes, Aircraft, Musical instruments, Watercraft, Optical devices, Sensors, Models, Electronic devices, Enclosures, Clocks, Machinery, Engines, Furniture, Jewelry, Jigs, Telecom, Lighting, Medical devices, Photographic devices, Robots, Sculptures, Sound equipment, Sporting equipment, Tooling, Toys and more.
What Can we help you do next?
∇ Go To Homepage For Die Casting China
→Casting Parts-Find out what we have done.
→Ralated Tips About Die Casting Services
By Minghe Die Casting Manufacturer |Categories: Helpful Articles |Material Tags: Aluminum Casting, Zinc Casting, Magnesium Casting, Titanium Casting, Stainless Steel Casting, Brass Casting,Bronze Casting,Casting Video,Company History,Aluminum Die Casting |Comments Off