The Analysis Of Cracks In Slewing Bearing Soft Belt
As a key component of construction machinery, slewing bearings are currently used in the market with nearly 10 million units. The main failure modes of the slewing ring are raceway wear, tooth surface wear, raceway cracks and tooth fractures, etc. The tooth surface cracks or fractures directly cause the slewing ring to be scrapped, and the raceway cracks will accelerate the damage of the slewing ring and greatly reduce the slewing ring design life. This paper selects the early cracks during the use of the soft belt of the slewing ring raceway to analyze and propose preventive measures.
1. Crack product description
The cracked product in this article is used for the slewing bearing of a 6t excavator, with a slewing center diameter of 730 and a rolling diameter of 22mm. In order to test the service life of the slewing ring, a loading test was carried out by simulating the actual working conditions as shown in Figure 1. After loading 30,000 revolutions, cracks in the soft zone were found.
- (1) Raw material The material of this product is S48C ring, and the raw material is cylindrical continuous casting and rolling round steel ingot. After being rolled into a ring, it is subjected to quenching and tempering treatment.
- (2) Product processing technology Product processing technology: rough UT→rough turning shape→processing plugging hole→matching plugging→drilling taper pin hole→matching taper pin→rough turning raceway→raceway quenching→tempering→MT→…
The product process adopts scanning induction quenching, after quenching, it is tempered at a low temperature of 180~200℃, and then undergoes MT flaw detection. Due to the scanning induction hardening process of this product, a process soft zone must be reserved at the blockage, as shown between the two lines in Figure 2. After flaw detection, no cracks were found in this product, and subsequent processing was carried out.
2. Crack analysis
- (1) Crack metallographic inspection After the product is subjected to loading test, the product is disassembled and inspected, and it is found that there are two cracks in the product, one is located at the edge of the plugged hole, and the other is located in the heat treatment transition zone. Both cracks are located in the soft zone reserved in the process, and there are obvious signs of wear in the soft zone. There is no abnormality in the rest of the raceway, and there is no abnormality in the built-in rolling elements.After the cracks are cut along the circumferential direction of the raceway, metallographic inspection is carried out, and no abnormal areas of the raceway are sampled to verify the conformity of the scanning surface induction hardening quality.
- (2) Quenching quality compliance inspection. The quality requirements for scanning quenching of this product are: hardness requirements of 55~62HRC, depth of hardened layer not less than 2mm (hardness not less than 45HRC), and induction quenching metallographic structure level of 3~7 , No defects such as cracks.The product is subjected to metallographic inspection, the hardness is 55.9~56.4HRC, the depth of the hardened layer is 3.03~3.26mm, the metallographic structure of induction quenching is level 4, and there is no crack and other defects after MT inspection.
- (3) The industry standard for compliance testing of soft belts "JB/T2300—2011 Slewing Bearing" and "JB/T10839—2008 Construction Machinery and Equipment Single-row Ball Slewing Bearing" have clear technical requirements for soft belts: soft belt width refers to It is the distance between the middle part of the raceway at both ends of the soft belt where the hardness is 50HRC; the width of the soft belt of the ferrule with plugged holes should not be greater than the diameter of the plugged holes plus 35mm.The diameter of the plugging hole of the product is 27mm, and the control standard for the width of the soft tape of the product is less than or equal to 62mm. The width of the soft belt is tested according to the above standards, and the width of the tempered belt is 44.2mm, which meets the standard requirements.
- (4) Analysis of the causes of cracks The main influencing factors of cracks caused by induction quenching are the unqualified quality of raw materials and improper heat treatment process parameters.
As mentioned earlier, after quenching and tempering, a comprehensive MT inspection was carried out on the workpiece. No cracks were found in the workpiece. The crack was found to be visible to the naked eye after the workpiece was loaded. It can be confirmed that the crack is caused by the bearing force.
Analysis of the cause of crack 1: In Figure 4, the crack is located in the transition zone between the matrix and the quenching. The matrix structure area has severe plastic deformation (see Figure 9), and a small amount of martensite appears in the transition zone (see Figure 4) and gradually becomes quenched. The hard zone transitions to the martensite zone (see Figure 7), and the yield strength gradually increases. Between the matrix and the transition zone, stress concentration is likely to occur during the repeated rolling process. After reaching the ultimate yield strength in this zone, cracks will occur and spread along the transition layer.
Analysis of the cause of crack 2: When the workpiece is subjected to induction quenching, the tempering zone is reserved for the process in Figure 5, and the structure is the matrix structure without quenching. It can be seen from the figure that there is a plastic deformation consistent with the direction of loading and running, and serious streamline deformation of the tissue occurs. After the workpiece is loaded, the unquenched yield strength is low. When the stress exceeds the yield limit of the material, plastic deformation is caused. After repeated rolling, the crystal grains slip and separate along the slip surface under the action of the stress. Move the surface to separate the cracks.
3. Preventive measures
Through the above analysis, it can be concluded that the cracks produced by the product are due to the load failure cracks of the workpiece after the soft zone of the workpiece is loaded. According to the industry's experimental research class, the following measures are adopted to prevent cracks in the soft zone:
- (1) Strictly control the clearance between the plugged and plugged holes.
- (2) Grind and dent the soft zone.
Please keep the source and address of this article for reprinting: The Analysis Of Cracks In Slewing Bearing Soft Belt
Minghe Die Casting Company are dedicated to manufacture and provide quality and high performance Casting Parts(metal die casting parts range mainly include Thin-Wall Die Casting,Hot Chamber Die Casting,Cold Chamber Die Casting),Round Service(Die Casting Service,Cnc Machining,Mold Making,Surface Treatment).Any custom Aluminum die casting, magnesium or Zamak/zinc die casting and other castings requirements are welcome to contact us.
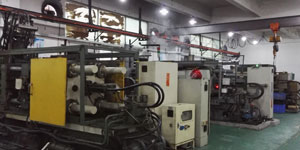
Under the control of ISO9001 and TS 16949,All processes are carried out through hundreds of advanced die casting machines, 5-axis machines, and other facilities, ranging from blasters to Ultra Sonic washing machines.Minghe not only has advanced equipment but also have professional team of experienced engineers,operators and inspectors to make the customer’s design come true.
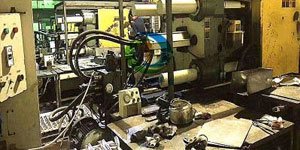
Contract manufacturer of die castings. Capabilities include cold chamber aluminum die casting parts from 0.15 lbs. to 6 lbs., quick change set up, and machining. Value-added services include polishing, vibrating, deburring, shot blasting, painting, plating, coating, assembly, and tooling. Materials worked with include alloys such as 360, 380, 383, and 413.
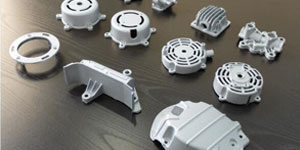
Zinc die casting design assistance/concurrent engineering services. Custom manufacturer of precision zinc die castings. Miniature castings, high pressure die castings, multi-slide mold castings, conventional mold castings, unit die and independent die castings and cavity sealed castings can be manufactured. Castings can be manufactured in lengths and widths up to 24 in. in +/-0.0005 in. tolerance.
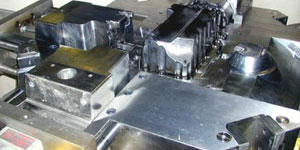
ISO 9001: 2015 certified manufacturer of die cast magnesium, Capabilities include high-pressure magnesium die casting up to 200 ton hot chamber & 3000 ton cold chamber, tooling design, polishing, molding, machining, powder & liquid painting, full QA with CMM capabilities, assembly, packaging & delivery.
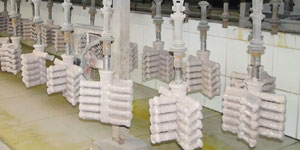
ITAF16949 certified. Additional Casting Service Include investment casting,sand casting,Gravity Casting, Lost Foam Casting,Centrifugal Casting,Vacuum Casting,Permanent Mold Casting,.Capabilities include EDI, engineering assistance, solid modeling and secondary processing.
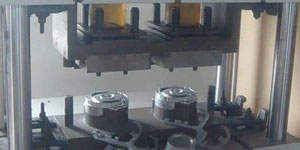
Casting Industries Parts Case Studies for: Cars, Bikes, Aircraft, Musical instruments, Watercraft, Optical devices, Sensors, Models, Electronic devices, Enclosures, Clocks, Machinery, Engines, Furniture, Jewelry, Jigs, Telecom, Lighting, Medical devices, Photographic devices, Robots, Sculptures, Sound equipment, Sporting equipment, Tooling, Toys and more.
What Can we help you do next?
∇ Go To Homepage For Die Casting China
→Casting Parts-Find out what we have done.
→Ralated Tips About Die Casting Services
By Minghe Die Casting Manufacturer |Categories: Helpful Articles |Material Tags: Aluminum Casting, Zinc Casting, Magnesium Casting, Titanium Casting, Stainless Steel Casting, Brass Casting,Bronze Casting,Casting Video,Company History,Aluminum Die Casting |Comments Off