The Causes Of Die Bursting During Stamping Die Steel Use
Due to different stamping processes and different working conditions, there are many reasons for die bursting. The following is a comprehensive analysis of the causes of die burst in the design, manufacture and use of the die, and corresponding improvement measures are made.
The mold material is not good, and it is easy to break in the subsequent processing
Die life of different materials is often different. For this reason, two basic requirements are put forward for the materials of the working parts of the die:
- (1) The use performance of the material should have high hardness (58-64HRC) and high strength, and have high wear resistance and sufficient toughness, small heat treatment deformation, and a certain degree of thermal hardness;
- (2) Good process performance. The processing and manufacturing process of die working parts is generally more complicated.
Therefore, it must be adaptable to various processing techniques, such as forgeability, machinability, hardenability, hardenability, quenching crack sensitivity and grinding workability, etc. .
Heat treatment: deformation caused by improper quenching and tempering process
Practice has proved that the thermal processing quality of the mold has a great impact on the performance and service life of the mold. From the analysis and statistics of the causes of mold failure, it can be seen that "accidents" of mold failure caused by improper heat treatment account for more than 40%.
- (1) Forging process This is an important link in the manufacturing process of mold working parts. For high-alloy tool steel molds, technical requirements are usually put forward for the metallographic structure such as the distribution of carbides in the material.
- (2) Preliminary heat treatment should adopt annealing, normalizing or quenching and tempering and other preliminary heat treatment processes depending on the materials and requirements of the mold working parts to improve the structure, eliminate the structural defects of the forging blank, and improve the processing technology. High-carbon alloy die steel undergoes appropriate preliminary heat treatment, which can eliminate the network secondary cementite or chain carbides, spheroidize and refine the carbides, and promote the uniformity of carbide distribution, which is beneficial to ensure quenching and tempering Quality, improve mold life.
- (3) Quenching and tempering are the key links in the heat treatment of the mold. If overheating occurs during quenching and heating, it will not only cause greater brittleness of the workpiece, but also easily cause deformation and cracking during cooling, which will seriously affect the life of the mold. Special attention should be paid to preventing oxidation and decarburization during the quenching and heating of the die, and the heat treatment process specifications should be strictly controlled. When conditions permit, vacuum heat treatment can be used. After quenching, it should be tempered in time, and different tempering processes should be adopted according to the technical requirements.
- (4) Stress-relief annealing die working parts should undergo stress-relief annealing treatment after rough machining. The purpose is to eliminate the internal stress caused by rough machining, so as to avoid excessive deformation and cracks during quenching. For molds with high precision requirements, they need to undergo stress relief and tempering treatment after grinding or electrical machining, which is conducive to stabilizing the precision of the mold and improving the service life.
The mold grinding flatness is not enough, resulting in flexural deformation
The surface quality of mold working parts has a very close relationship with the mold's wear resistance, fracture resistance and adhesion resistance, which directly affects the service life of the mold, especially the surface roughness value has a great impact on the mold life. If the surface roughness value is too large, stress concentration will occur during work, and cracks will easily occur between the peaks and valleys, which will affect the durability of the die, and the corrosion resistance of the workpiece surface, which directly affects the service life of the die And precision, for this, you should pay attention to the following matters:
- (1) During the processing of mold working parts, it is necessary to prevent the phenomenon of grinding and burning the surface of the parts, and the grinding process conditions and process methods (such as grinding wheel hardness, particle size, coolant, feed rate and other parameters) should be strictly controlled;
- (2) During the machining process, prevent macro defects such as knife marks, interlayers, cracks, and impact scars on the surface of the mold working parts. The existence of these defects will cause stress concentration and become the root cause of fracture, resulting in early failure of the mold;
- (3) The use of grinding, grinding and polishing and other finishing and fine processing to obtain a smaller surface roughness value and improve the service life of the mold.
Design process
The mold strength is not enough, the knife edge spacing is too close, the mold structure is unreasonable, the number of template blocks is not enough, there is no backing board, the mold is not guided correctly, and the gap is unreasonable.
- (1) Unreasonable reciprocating feed layout method for layout and overlap, and too small overlap value will often cause rapid wear of the mold or damage to the convex and concave molds. Reasonably choose the layout method and the edge value to improve the life of the mold.
- (2) The precise and reliable guidance of the guide mechanism of the mold has a great impact on reducing the wear of the mold's working parts and avoiding the damage of the convex and concave molds, especially the gapless and small gap blanking molds, composite molds and multi-stations. Progressive dies are more effective. In order to improve the life of the mold, it is necessary to correctly select the guiding form and determine the accuracy of the guiding mechanism according to the nature of the process and the accuracy of the parts.
- (3) The geometric parameters of the cutting edge of the mold (convex and concave mold).
Wire cutting process
The thread cutting is artificially pulled, the thread cutting gap is handled incorrectly, and the metamorphic layer is not affected by the clear angle and the thread cutting.
The cutting edge of the die is mostly processed by wire cutting. Due to the thermal effect and electrolysis of the wire cutting process, a certain thickness of metamorphic layer is produced on the surface of the mold, which causes the surface hardness to decrease, and the appearance of microcracks, etc., makes the wire cutting die prone to early wear, which directly affects the die blanking gap. Keeping and cutting edges are easy to chip and shorten the service life of the mold. Therefore, in the on-line cutting process, reasonable electrical standards should be selected to minimize the depth of the metamorphic layer.
Selection of Punch Equipment
The punch tonnage, the punching force is not enough, and the die is adjusted too deeply.
The accuracy and rigidity of stamping equipment (such as presses) have an extremely important impact on the life of the die. The stamping equipment has high precision and good rigidity, and the life of the die is greatly improved. For example, the material of the complex silicon steel sheet die is Crl2MoV, which can be used on an ordinary open press with an average regrinding life of 10,000 to 30,000; while on a new precision press, the die’s regrinding life can reach 60,000 to 120,000.
Stamping process
The raw material thickness tolerance of the stamping parts is out of tolerance, material performance fluctuations, poor surface quality (such as rust) or dirty (such as oil stains), etc., will cause increased wear and tear of mold working parts and easy chipping. For this reason, it should be noted:
- (1) Use raw materials with good stamping processability as much as possible to reduce stamping deformation force;
- (2) Before stamping, the grade, thickness and surface quality of the raw materials should be strictly checked, and the raw materials should be wiped clean. If necessary, the surface oxides and rust should be removed;
- (3) According to the stamping process and the types of raw materials, softening treatment and surface treatment can be arranged when necessary, and suitable lubricants and lubricating processes can be selected.
8. Correct use and reasonable maintenance of production operations.
Please keep the source and address of this article for reprinting:The Causes Of Die Bursting During Stamping Die Steel Use
Minghe Die Casting Company are dedicated to manufacture and provide quality and high performance Casting Parts(metal die casting parts range mainly include Thin-Wall Die Casting,Hot Chamber Die Casting,Cold Chamber Die Casting),Round Service(Die Casting Service,Cnc Machining,Mold Making,Surface Treatment).Any custom Aluminum die casting, magnesium or Zamak/zinc die casting and other castings requirements are welcome to contact us.
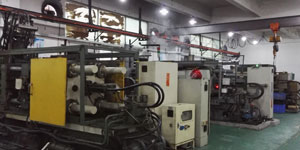
Under the control of ISO9001 and TS 16949,All processes are carried out through hundreds of advanced die casting machines, 5-axis machines, and other facilities, ranging from blasters to Ultra Sonic washing machines.Minghe not only has advanced equipment but also have professional team of experienced engineers,operators and inspectors to make the customer’s design come true.
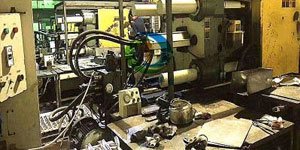
Contract manufacturer of die castings. Capabilities include cold chamber aluminum die casting parts from 0.15 lbs. to 6 lbs., quick change set up, and machining. Value-added services include polishing, vibrating, deburring, shot blasting, painting, plating, coating, assembly, and tooling. Materials worked with include alloys such as 360, 380, 383, and 413.
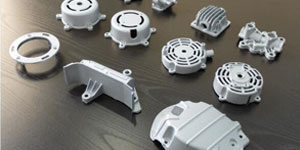
Zinc die casting design assistance/concurrent engineering services. Custom manufacturer of precision zinc die castings. Miniature castings, high pressure die castings, multi-slide mold castings, conventional mold castings, unit die and independent die castings and cavity sealed castings can be manufactured. Castings can be manufactured in lengths and widths up to 24 in. in +/-0.0005 in. tolerance.
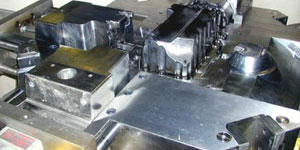
ISO 9001: 2015 certified manufacturer of die cast magnesium, Capabilities include high-pressure magnesium die casting up to 200 ton hot chamber & 3000 ton cold chamber, tooling design, polishing, molding, machining, powder & liquid painting, full QA with CMM capabilities, assembly, packaging & delivery.
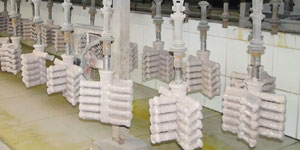
ITAF16949 certified. Additional Casting Service Include investment casting,sand casting,Gravity Casting, Lost Foam Casting,Centrifugal Casting,Vacuum Casting,Permanent Mold Casting,.Capabilities include EDI, engineering assistance, solid modeling and secondary processing.
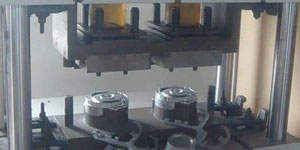
Casting Industries Parts Case Studies for: Cars, Bikes, Aircraft, Musical instruments, Watercraft, Optical devices, Sensors, Models, Electronic devices, Enclosures, Clocks, Machinery, Engines, Furniture, Jewelry, Jigs, Telecom, Lighting, Medical devices, Photographic devices, Robots, Sculptures, Sound equipment, Sporting equipment, Tooling, Toys and more.
What Can we help you do next?
∇ Go To Homepage For Die Casting China
→Casting Parts-Find out what we have done.
→Ralated Tips About Die Casting Services
By Minghe Die Casting Manufacturer |Categories: Helpful Articles |Material Tags: Aluminum Casting, Zinc Casting, Magnesium Casting, Titanium Casting, Stainless Steel Casting, Brass Casting,Bronze Casting,Casting Video,Company History,Aluminum Die Casting |Comments Off