The Causes Of Die-Casting Tooling Bursting
The Causes Of Cracks
- The temperature of the mold is too high during the die-casting production process (it is best to add a cooling system).
- The mold release agent is sprayed unreasonably during the die-casting production process.
- The mold heat treatment is not ideal, mainly due to the hardness (the hardness should not be less than HRC-47).
- The mold steel material is not good, it is recommended to use 8407 or refined H13
Early cracking is generally due to the high forging temperature of the blank forging (commonly known as overburning). Overburning is an irremediable defect, so the forging temperature during the blank manufacturing process should be strictly controlled. The same is true for the quenching process. The heating time should be strictly controlled to prevent decarburization. After the material is selected, it is heat treatment. After a certain amount of production, pay attention to stress relief. Also, the design should be reasonable, try to avoid stress concentration, and pay attention to the size of the R angle. At about 10,000 mold times, the mold should pay attention to tempering to remove the stress. The residual stress of the internal force concentrated processing is not removed. The thermal stress of the die-casting process is not well removed. In short, the crack is the performance of stress concentration. You can use multiple tempering to remove the stress. Can increase mold life.
The main reasons for the cracking of aluminum alloy die-casting molds after a period of production are as follows:
- The mold temperature is too high and the stress is too large
- Mould core material uses 8407, skd61
- Mold heat treatment hardness is too high
- Regular maintenance, 5k times1 tempering, 15k times1 tempering 30k times.
To prevent the die-casting mold from cracking and increase the service life of the mold, the following points must be done:
- 1. The heat treatment of the forming part of the die-casting mold (moving, fixed core, core) requires that the hardness is guaranteed to be HRC43~48 (the material can be SKD61 or 8407)
- 2. The mold should be fully preheated before die-casting production, and its functions are as follows:
- 2.1 Make the mold reach a better thermal balance, make the casting solidification rate uniform and facilitate pressure transmission.
- 2.2 Maintain the fluidity of the die-cast alloy when filled, have good formability and improve the surface quality of the casting.
- 2.3 Reduce pre-production defects and improve die-casting productivity.
- 2.4 Reduce the thermal alternating stress of the mold and increase the service life of the mold.
The specific specifications are as follows:
Alloy Type | Mold Preheating Temperature (℃) |
Aluminum Alloy | 180~300 |
Zinc Alloy | 150~200 |
After the new mold is produced for a period of time, the accumulation of thermal stress is the direct cause of the mold core cracking. In order to reduce the thermal stress, the mold core and slider after a certain period of time should be tempered to eliminate thermal stress.The specific production modes that need to eliminate thermal stress are as follows:
Mold Type | Aluminum Alloy | Zinc Alloy |
First Tempering | <2000 times | <10000 times |
Second Tempering | <10000 times | <20000 times |
Third Tempering | <30000 times | <50000 times |
The aluminum alloy die-casting mold bears huge alternating working stress, and attention must be paid to the mold material, design, processing, heat treatment and operation in order to obtain a long mold life. The following are 25 tips for making the mold achieve a long life:
- High-quality mold materials
- Reasonable design of mold wall thickness and other mold dimensions
- Try to use inserts
- Choose the largest possible corner R when possible
- The distance between the cooling water channel and the profile and corner must be large enough
- Stress relief and tempering should be done after rough machining
- Heat treatment is correct, and quenching and cooling must be fast enough
- Thoroughly polish and remove the EDM metamorphic layer
- The surface cannot be highly polished
- The mold surface should be oxidized
- If selective nitriding, the infiltration layer should not be too deep
- Preheat the mold to the recommended temperature in the correct way
- Slow hammer speed should be used to start die-casting 5-10 pieces
- Reduce the temperature of the molten aluminum as much as possible on the premise of obtaining qualified products
- Do not use too high injection speed of aluminum liquid
- Ensure that the mold is properly cooled, and the temperature of the cooling water should be kept at 40~50℃
- For temporary shutdown, try to close the mold and reduce the amount of cooling water to avoid thermal shock to the mold when restarting
- The coolant should be turned off when the model surface is at the highest temperature
- Not too much spray release agent
- After a certain amount of die-casting, stress relief and tempering
- The main reason is that the temperature is too high. It is recommended to use a thermometer to control the temperature at any time during the die-casting process (the recommended temperature for aluminum alloy die-casting is <650)
- Pay attention to the preheating of the mold to prevent thermal fatigue. (Cracking is mainly caused by thermal fatigue)
- Pay attention to mold processing, it is best to use a machining center to complete, if there is a need for electrical processing, after electrical processing, grinding and polishing procedures should be added.
- Pay attention to the maintenance of the mold (stress relief and tempering)
- It is recommended to use ASSAB 8407 for molds with high life requirements, and the hardness of die-casting molds is recommended not to be higher than 50HRC
Please keep the source and address of this article for reprinting:The Causes Of Die-Casting Tooling Bursting
Minghe Die Casting Company are dedicated to manufacture and provide quality and high performance Casting Parts(metal die casting parts range mainly include Thin-Wall Die Casting,Hot Chamber Die Casting,Cold Chamber Die Casting),Round Service(Die Casting Service,Cnc Machining,Mold Making,Surface Treatment).Any custom Aluminum die casting, magnesium or Zamak/zinc die casting and other castings requirements are welcome to contact us.
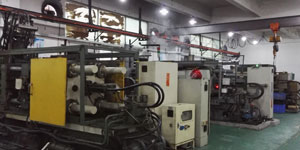
Under the control of ISO9001 and TS 16949,All processes are carried out through hundreds of advanced die casting machines, 5-axis machines, and other facilities, ranging from blasters to Ultra Sonic washing machines.Minghe not only has advanced equipment but also have professional team of experienced engineers,operators and inspectors to make the customer’s design come true.
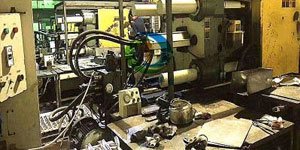
Contract manufacturer of die castings. Capabilities include cold chamber aluminum die casting parts from 0.15 lbs. to 6 lbs., quick change set up, and machining. Value-added services include polishing, vibrating, deburring, shot blasting, painting, plating, coating, assembly, and tooling. Materials worked with include alloys such as 360, 380, 383, and 413.
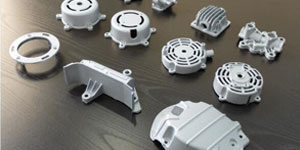
Zinc die casting design assistance/concurrent engineering services. Custom manufacturer of precision zinc die castings. Miniature castings, high pressure die castings, multi-slide mold castings, conventional mold castings, unit die and independent die castings and cavity sealed castings can be manufactured. Castings can be manufactured in lengths and widths up to 24 in. in +/-0.0005 in. tolerance.
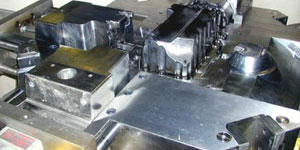
ISO 9001: 2015 certified manufacturer of die cast magnesium, Capabilities include high-pressure magnesium die casting up to 200 ton hot chamber & 3000 ton cold chamber, tooling design, polishing, molding, machining, powder & liquid painting, full QA with CMM capabilities, assembly, packaging & delivery.
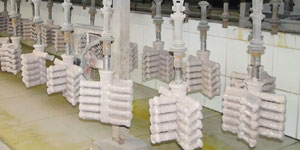
ITAF16949 certified. Additional Casting Service Include investment casting,sand casting,Gravity Casting, Lost Foam Casting,Centrifugal Casting,Vacuum Casting,Permanent Mold Casting,.Capabilities include EDI, engineering assistance, solid modeling and secondary processing.
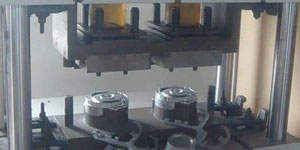
Casting Industries Parts Case Studies for: Cars, Bikes, Aircraft, Musical instruments, Watercraft, Optical devices, Sensors, Models, Electronic devices, Enclosures, Clocks, Machinery, Engines, Furniture, Jewelry, Jigs, Telecom, Lighting, Medical devices, Photographic devices, Robots, Sculptures, Sound equipment, Sporting equipment, Tooling, Toys and more.
What Can we help you do next?
∇ Go To Homepage For Die Casting China
→Casting Parts-Find out what we have done.
→Ralated Tips About Die Casting Services
By Minghe Die Casting Manufacturer |Categories: Helpful Articles |Material Tags: Aluminum Casting, Zinc Casting, Magnesium Casting, Titanium Casting, Stainless Steel Casting, Brass Casting,Bronze Casting,Casting Video,Company History,Aluminum Die Casting |Comments Off