Microstructure And Mechanical Properties Of Automobile Aluminum Chassis Structural Parts
The structure of castings and the key points of development technology
An automobile chassis structure is shown in Figure 1. Its outline size is 677.79mm×115.40mm×232.42mm, mass is 2.6kg, average wall thickness is 3.5mm, and volume is about 9.88×105mm^3. The projected area of the casting is 86300mm^2, and the material is Al-8Si-Mn-Mg alloy. The casting has multiple thick-walled hot joints, which are easy to form shrinkage holes. Appearance quality requirements of castings: no obvious die casting flow marks, no obvious tortoise cracks, and no bubbles on the surface; internal quality requirements of castings: general casting position holes are below 1mm, bosses and thick meat parts require holes 2mm The following; requirements for air content inside the casting: the air content per 100g of aluminum at the designated filling end of the casting should be less than 15mL, and the designated part of the inner gate should be less than 10mL; the mechanical properties of the casting (after T5 treatment) requirements: tensile strength of 220MPa, yield The strength is 150MPa, the elongation is ≥5%, the impact toughness is ≥6.0J/cm2, the thread tensile test is M10≥60kN, M12≥85kN, the hardness (HRB) is 30; the requirements for the fatigue test of castings: under normal conditions, Withstand the force of 6.1~-4.8kN at the designated point, the frequency is 2Hz, and the damage is not allowed after 20,000 cycles. Under the test conditions, the number of cycles is 40,000 times. According to the above requirements, the production of this casting is relatively difficult.
In the casting development process, in order to shorten the development cycle, numerical simulation software is used for analysis, and with reference to actual production parameters, four different casting methods are adopted (see Figure 2). Plan 1 and Plan 2 adopt comb-shaped pouring method, Plan 3 and Plan 4 adopt fan-shaped pouring method; Compared with Plan 2, Plan 1 uses a more concentrated feed method and Plan 2 uses a more dispersed feed method. ; Compared with Option 4, Option 3 has a shorter main runner and Option 4 has a longer main runner. Use Magma software to simulate and analyze the above four schemes. The results show that: Option 1 runner is too straight, energy loss is large, and the inner gate pouring is not synchronized, which is messy; Option 2 is filled with gas on both sides of the runners, and the solidification analysis casting has shrinkage holes on both sides of the threaded holes; 3 The runner is too short, which is not conducive to the application of high-vacuum die-casting process; Scheme 4 The temperature of the middle pouring part of the casting is higher, and the mold erosion is more likely to be there. Considering the filling fluid state, solidification shrinkage, temperature, etc., Option 4 is better.
Die casting process parameter optimization test
It is produced using Idra's 16000kN horizontal cold chamber die-casting machine, which is equipped with a real-time injection control system. The vacuum valve is a hydraulic high-vacuum stop valve with independent intellectual property rights (see Figure 3), and is equipped with a high-vacuum control system to achieve two-way vacuuming of the cavity and the pressure chamber; the mold surface is sealed with a silicone strip with a diameter of 10 mm ( (See Figure 4); The mold is cooled by oily medium and equipped with thermocouple to accurately control the mold temperature; the core pin is cooled by high-pressure water cooling; the spraying is automatically sprayed by an ABB robot.
In order to obtain the optimal combination of die casting machine setting parameters and high vacuum stroke, 7 sets of parameter combinations were tested under the conditions of setting the aluminum alloy temperature at 690 ℃ and the mold temperature at 200 ℃.
The color penetration test was carried out on the casting, and the results showed that the surface of the casting had no defects such as poor forming, cold separation, cracks, and blisters.
The internal quality of the castings was inspected by X-rays. The results showed that no air shrinkage holes were found in the plate position, and no air holes, shrinkage holes, or shrinkage porosity were found on the boss and thick wall positions of the casting (see Figure 6).
Based on the above analysis, it can be seen that the slow injection speed is 0.3m/s, the vacuum position is 480mm, the die casting speed is 4.0-4.5m/s, the casting pressure is about 76MPa, and the fast injection distance is 620mm is the best combination of parameters.
Mechanical performance test and analysis
3.1 The influence of vacuum on the structure and mechanical properties of die castings
It can be seen that the high-vacuum (vacuum degree of 97 kPa) die-casting has a higher density, which means that the internal gas content of the die-casting is less. Compared with ordinary vacuum (65kPa vacuum) die castings, the tensile strength, yield strength, elongation and hardness of high vacuum die castings are increased by 21%, 29%, 18%, and 10%, respectively, indicating that high vacuum die castings It has a better promoting effect on improving the mechanical properties of structural parts.
Whether it is high-vacuum die-casting or ordinary vacuum die-casting, the alloy microstructure during high-vacuum die-casting and ordinary vacuum die-casting. Whether it is high-vacuum die-casting or ordinary vacuum die-casting, the Al-8Si-Mn-Mg aluminum alloy structure is composed of relatively coarse α 1-Al and fine round α 2-Al, as well as fine dendritic eutectic Si, etc. composition. Although the Fe content in the alloy is low, a small amount of granular Fe-rich phases can still be observed. Because pressure casting is under high temperature and high pressure, the molten metal fills the cavity in a very short time and solidifies to form. This large cooling rate can make the liquid metal obtain a large degree of subcooling, thereby increasing the number of nucleation The nucleation rate is improved, the eutectic Si has been refined, and the formation of needle-like AlSiFe phase is suppressed. Due to the low degree of vacuum, under ordinary vacuum conditions, very small pore defects can be observed inside the casting.
3.2 The effect of heat treatment on the performance and structure of high vacuum die castings
3.2.1 Mechanical properties
Castings need to undergo aging heat treatment, and the heat treatment conditions are 200 ℃×2 h. Then, a tensile test is performed on the designated positions (positions 1, 2, 3) of the ribs of the castings. It can be seen that the mechanical properties of the die castings vary with the die casting process.
Compared with ordinary vacuum die-casting, high-vacuum die-casting has significantly improved tensile strength, yield strength, elongation and hardness. Among them, the tensile strength is increased by about 21%, the yield strength is increased by about 29%, and the elongation rate is increased by about 21%. Increased by about 18% and hardness by about 10%, it can be seen that high vacuum die casting significantly improves the strength and hardness of die castings.
3.2.2 Impact toughness
The impact test on the designated positions of the die-casting ribs (positions 1, 2, and 3, which are the location sampling points for mechanical performance testing) shows that the impact toughness of the high-vacuum die-castings fully meets the requirements of the castings.
3.2.3 Thread drawing
The M10 and M12 threaded holes of the castings were subjected to thread drawing tests. The M10 thread did not change under the action of 66kN and the M12 thread under the action of 85kN, indicating that the threads of the high vacuum die castings fully meet the force requirements.
3.2.4 Fatigue test
After the castings were subjected to 410150 durability tests, fluorescence detection showed that there were no cracks on the surface of the castings, and the results showed that the fatigue resistance of the high-vacuum die castings met the technical requirements.
3.2.5 Gas content detection
The gas content test is shown in Table 2. From the test results in Table 6, it can be seen that the gas content of the casting body at the inner gate is less than 8.9ml per 100g Al, and the gas content of the casting body at the water tail overflow tank is less than 12ml per 100g Al, which fully meets the casting requirements.
4 Conclusion
- (1) Using numerical simulation, the die-casting forming process and high-vacuum die-casting process parameters of automobile chassis structural parts were optimized, and high-quality castings with external and internal quality meeting the requirements were manufactured.
- (2) High vacuum die casting can significantly improve the mechanical properties of structural parts. Compared with ordinary die-casting, the density of castings during high-vacuum die-casting is increased, and the tensile strength, yield strength, elongation and hardness of the castings are increased by 21%, 29%, 18%, and 10% respectively.
- (3) The test results of durability, drawing and gas content of the castings all meet the technical requirements of the product and meet the mass production conditions.
Please keep the source and address of this article for reprinting: Microstructure And Mechanical Properties Of Automobile Aluminum Chassis Structural Parts
Minghe Die Casting Company are dedicated to manufacture and provide quality and high performance Casting Parts(metal die casting parts range mainly include Thin-Wall Die Casting,Hot Chamber Die Casting,Cold Chamber Die Casting),Round Service(Die Casting Service,Cnc Machining,Mold Making,Surface Treatment).Any custom Aluminum die casting, magnesium or Zamak/zinc die casting and other castings requirements are welcome to contact us.
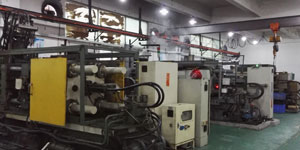
Under the control of ISO9001 and TS 16949,All processes are carried out through hundreds of advanced die casting machines, 5-axis machines, and other facilities, ranging from blasters to Ultra Sonic washing machines.Minghe not only has advanced equipment but also have professional team of experienced engineers,operators and inspectors to make the customer’s design come true.
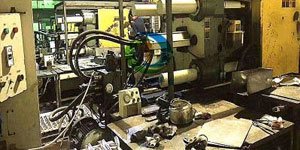
Contract manufacturer of die castings. Capabilities include cold chamber aluminum die casting parts from 0.15 lbs. to 6 lbs., quick change set up, and machining. Value-added services include polishing, vibrating, deburring, shot blasting, painting, plating, coating, assembly, and tooling. Materials worked with include alloys such as 360, 380, 383, and 413.
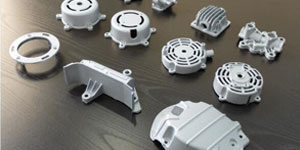
Zinc die casting design assistance/concurrent engineering services. Custom manufacturer of precision zinc die castings. Miniature castings, high pressure die castings, multi-slide mold castings, conventional mold castings, unit die and independent die castings and cavity sealed castings can be manufactured. Castings can be manufactured in lengths and widths up to 24 in. in +/-0.0005 in. tolerance.
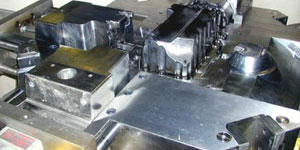
ISO 9001: 2015 certified manufacturer of die cast magnesium, Capabilities include high-pressure magnesium die casting up to 200 ton hot chamber & 3000 ton cold chamber, tooling design, polishing, molding, machining, powder & liquid painting, full QA with CMM capabilities, assembly, packaging & delivery.
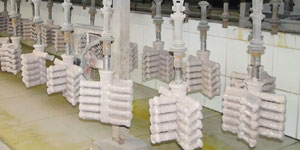
ITAF16949 certified. Additional Casting Service Include investment casting,sand casting,Gravity Casting, Lost Foam Casting,Centrifugal Casting,Vacuum Casting,Permanent Mold Casting,.Capabilities include EDI, engineering assistance, solid modeling and secondary processing.
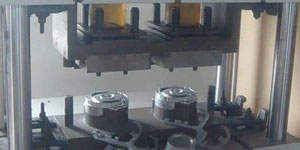
Casting Industries Parts Case Studies for: Cars, Bikes, Aircraft, Musical instruments, Watercraft, Optical devices, Sensors, Models, Electronic devices, Enclosures, Clocks, Machinery, Engines, Furniture, Jewelry, Jigs, Telecom, Lighting, Medical devices, Photographic devices, Robots, Sculptures, Sound equipment, Sporting equipment, Tooling, Toys and more.
What Can we help you do next?
∇ Go To Homepage For Die Casting China
→Casting Parts-Find out what we have done.
→Ralated Tips About Die Casting Services
By Minghe Die Casting Manufacturer |Categories: Helpful Articles |Material Tags: Aluminum Casting, Zinc Casting, Magnesium Casting, Titanium Casting, Stainless Steel Casting, Brass Casting,Bronze Casting,Casting Video,Company History,Aluminum Die Casting |Comments Off