Methods And Steps Of Stamping Die Design
There are many types of molds, which can be divided into:
- Metal molds based on processing goals and processing techniques.
- Processing non-metal and powder metallurgy molds.
Today, the editor is talking about the method and process of stamping die design.
Analysis of stamping process of stamping parts
Stamping parts must have excellent stamping technology in order to produce qualified stamping parts in the simplest and most economical way. The process analysis of stamping parts can be completed according to the following methods:
- Read the parts drawing. In addition to the shape and size of the parts, it is important to understand the requirements of the accuracy of the parts and the surface roughness.
- Analyze whether the structure and shape of the parts are suitable for stamping processing.
- Analyze whether the reference selection and scale labeling of the parts are reasonable, and whether the scale, orientation and shape accuracy are suitable for stamping processing.
- Whether the surface roughness requirements of the section of the blanking part are too high.
- Whether there is a large enough production batch.
If the manufacturability of the part is too poor, you should negotiate with the planner and propose a plan to revise the plan. If the production batch is too small, other production methods should be considered for processing.
Stamping Process Planning And Optimal Process Design
- According to the shape and scale of the stamping parts, start to determine the nature of the stamping process, such as: punching, zigzag, deep drawing, bulging, reaming and other stamping die planning methods and processes. Stamping die planning methods and processes.
- Calculate the degree of deformation of each stamping forming method. If the degree of deformation exceeds the limit of deformation, the number of punches in this process should be calculated.
- According to the deformation characteristics and quality requirements of each process, organize a reasonable stamping sequence. Attention should be paid to ensure that the deformation zone in each process is a weak zone. The already formed part (including the punched hole or shape) shall not participate in the deformation in the subsequent process. The polygonal zigzag part must be bent first outside and then bent Inside, it is necessary to organize necessary auxiliary processes and processes such as shaping, leveling, and heat treatment.
- On the premise of ensuring the accuracy of the parts, determine a reasonable process combination method according to the production batch and the blank positioning and discharging requirements.
- To plan two or more process plans, and compare the quality, cost, production rate, mold sharpening and repair, mold life and operational safety, etc., to select the best process plan.
- Start to determine the stamping equipment of each process.
Blank planning and layout design of stamping parts
- According to the nature of the stamping parts, calculate the dimensions of the blanks and make the blank drawings
- According to the nature and scale of the blank, plan the layout drawing and calculate the data utilization rate. To plan a variety of layout plans, select the best plan among them through comparison.
Stamping die design
1. Determine the mold structure method of each process of stamping processing, and make a schematic diagram of the mold.
2. Carry out specific structural planning for the specified 1-2 process molds, and make mold operation diagrams.
The planning method is as follows:
- Determine the type of mold: is it a simple mold, a continuous mold or a composite mold.
- Mold operation parts planning: calculate the dimensions of the convex and concave die edge and the length of the convex and concave molds, determine the structure of the convex and concave molds and the connection and fixation methods.
- Determine the location and distance method of the blank, and plan the corresponding positioning and distance parts.
- Determine the methods of pressing, unloading, ejecting and pushing parts, and plan the corresponding holding plates, unloading plates, and pushing blocks.
- Mold base planning: including the planning of upper and lower mold bases and guiding methods, and standard mold bases can also be selected.
- On the basis of the completion of the above operations, the mold operation drawing is made according to the proportion. First use the double-dotted line to make the blank, and then make the working parts, then make the positioning and distance parts, use the connecting parts to connect the above parts, and finally make the pressing and unloading parts in the appropriate position. According to the specific conditions of the mold, the above sequence can also be adjusted appropriately.
- The operation drawing should indicate the dimensions of the mold's outer contour, the height of the mold closure, the cooperation scale, and the method of cooperation type stamping mold planning and process mold planning. The job map should indicate the requirements of mold production accuracy and technical conditions. The job map should be made in accordance with the national drawing standards, with a standardized title bar and a detailed list of names. If it is a blanking die, make a layout drawing on the upper left corner of the job drawing.
- Calculate the pressure center of the mold and check whether the pressure center and the center line of the mold handle coincide. If they do not coincide, make corresponding corrections to the mold results.
- Calculate the punching force, and finally select the stamping equipment, and check the relevant dimensions of the die and stamping equipment (closed height, work surface, die handle device dimensions, etc.).
Please keep the source and address of this article for reprinting: Methods And Steps Of Stamping Die Design
Minghe Die Casting Company are dedicated to manufacture and provide quality and high performance Casting Parts(metal die casting parts range mainly include Thin-Wall Die Casting,Hot Chamber Die Casting,Cold Chamber Die Casting),Round Service(Die Casting Service,Cnc Machining,Mold Making,Surface Treatment).Any custom Aluminum die casting, magnesium or Zamak/zinc die casting and other castings requirements are welcome to contact us.
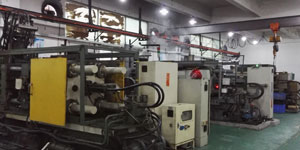
Under the control of ISO9001 and TS 16949,All processes are carried out through hundreds of advanced die casting machines, 5-axis machines, and other facilities, ranging from blasters to Ultra Sonic washing machines.Minghe not only has advanced equipment but also have professional team of experienced engineers,operators and inspectors to make the customer’s design come true.
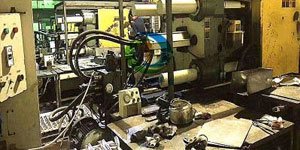
Contract manufacturer of die castings. Capabilities include cold chamber aluminum die casting parts from 0.15 lbs. to 6 lbs., quick change set up, and machining. Value-added services include polishing, vibrating, deburring, shot blasting, painting, plating, coating, assembly, and tooling. Materials worked with include alloys such as 360, 380, 383, and 413.
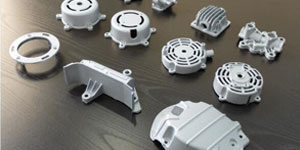
Zinc die casting design assistance/concurrent engineering services. Custom manufacturer of precision zinc die castings. Miniature castings, high pressure die castings, multi-slide mold castings, conventional mold castings, unit die and independent die castings and cavity sealed castings can be manufactured. Castings can be manufactured in lengths and widths up to 24 in. in +/-0.0005 in. tolerance.
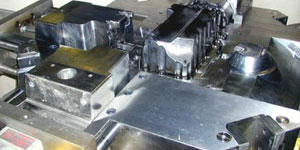
ISO 9001: 2015 certified manufacturer of die cast magnesium, Capabilities include high-pressure magnesium die casting up to 200 ton hot chamber & 3000 ton cold chamber, tooling design, polishing, molding, machining, powder & liquid painting, full QA with CMM capabilities, assembly, packaging & delivery.
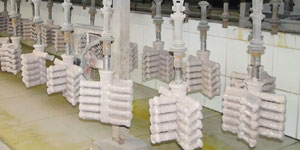
ITAF16949 certified. Additional Casting Service Include investment casting,sand casting,Gravity Casting, Lost Foam Casting,Centrifugal Casting,Vacuum Casting,Permanent Mold Casting,.Capabilities include EDI, engineering assistance, solid modeling and secondary processing.
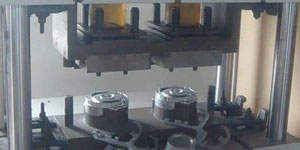
Casting Industries Parts Case Studies for: Cars, Bikes, Aircraft, Musical instruments, Watercraft, Optical devices, Sensors, Models, Electronic devices, Enclosures, Clocks, Machinery, Engines, Furniture, Jewelry, Jigs, Telecom, Lighting, Medical devices, Photographic devices, Robots, Sculptures, Sound equipment, Sporting equipment, Tooling, Toys and more.
What Can we help you do next?
∇ Go To Homepage For Die Casting China
→Casting Parts-Find out what we have done.
→Ralated Tips About Die Casting Services
By Minghe Die Casting Manufacturer |Categories: Helpful Articles |Material Tags: Aluminum Casting, Zinc Casting, Magnesium Casting, Titanium Casting, Stainless Steel Casting, Brass Casting,Bronze Casting,Casting Video,Company History,Aluminum Die Casting |Comments Off