Increase The Ferrite Content Of Ductile Iron
Studies have shown that different matrix structures have a greater impact on low-temperature impact toughness at different temperatures, and ferritic ductile iron with higher plasticity can obtain higher impact toughness indicators
4.1.1 Chemical composition
Reduce the elements that promote or stabilize the formation of pearlite, such as: Mn, V, Zr, Nb, Ti, Cr, Mo, W, Cu, Pb, Sb and other elements. Among them, two elements worth mentioning, one is manganese, which is good for spheroidal graphite. The impact toughness and brittle transition temperature of cast iron have a particularly adverse effect. Every increase of 0.1% of manganese content will increase the brittle transition temperature of ductile iron by 10℃~12℃. Therefore, try to choose low manganese pig iron and scrap steel as raw materials; The element is Cu. Although it is a neutral element, the effect of increasing the content of pearlite is not obvious, but with the increase of Cu content, the brittle transition temperature of ductile iron increases, and the impact toughness also decreases.
Properly increase the ferrite forming elements, such as: C, Si, Ca, Ba, Al, Bi and other elements. Among them, the Si element is worth mentioning. As we all know, Si is an element that strongly promotes graphitization and is beneficial to increase the ferrite content. , But the Si content increases, the impact toughness is obviously reduced, the brittle transition temperature increases by 5.5℃~6℃ every time the Si content increases by 01.%, and the ductile iron with Si content of about 4% has all the ferrite matrix, but The brittleness is very high, even at room temperature, it is difficult to use under impact load conditions. Therefore, the Si content in ductile iron with low temperature impact performance requirements is generally controlled at 1.6-2.0%.
4.1.2 Reduce the cooling rate of castings along with the mold
For a certain composition of ductile iron, changing the cooling rate of the eutectic stage can change its matrix structure in a larger range. That is to say, the slower the casting cooling rate is, the higher the ferrite content in the matrix structure, the thicker the casting. The slower the cooling rate, the higher the ferrite content. However, it is necessary to prevent the appearance of coarse crystal grains and graphite balls; different molding materials have different thermal conductivity, resulting in different cooling speeds of the castings. Dry sand or resin sand should be used for modeling materials with slow heat conduction, and the thickness of the mold should be appropriately relaxed. (Commonly known as increasing the amount of sand eaten), try to reduce or eliminate the use of cold iron. For thin-walled parts, appropriately increase the casting temperature to slow down the cooling rate of the castings, and extend the unpacking time as much as possible. If possible, the castings can be concentrated. Place it to slow down heat dissipation.
4.1.3 Heat treatment
It can be seen from Figure 4 and Figure 5 that after the heat treatment process, the ferrite content is increased, the elongation and the impact toughness are greatly improved, and some elements can be diffused at high temperature through the annealing treatment, and the casting matrix The crystal lattice of the structure becomes finer and the grain is refined, and the amount and performance of ferrite are stably improved. At the same time, through the method of heat treatment, the harsh requirements for some elements in the raw and auxiliary materials can be appropriately relaxed. For small and medium castings that fail to meet the requirements, heat treatment measures can be used to make up.
4.2 Refine grains and increase the number of eutectic clusters
As the grain size of the material increases, the fracture stress of the material decreases significantly. When the grain size is larger than a certain critical size, brittle fracture occurs. Refining and reducing the grain size can reduce the brittle transition temperature, thereby increasing Low-temperature impact toughness index of ductile iron.
4.2.1 Synthetic cast iron smelting process
Using scrap steel and re-fired ductile iron as the main raw materials, using graphite to increase C, ferrosilicon or silicon carbide to increase Si to smelt ductile iron. Since the melting point of C and Si is higher than the temperature of molten iron, they enter the molten iron mainly by diffusion and dissolution. There are a large number of [C] crystallites in the molten iron, which are pre-eutectoid or eutectic Graphite is a good foreign nucleation substrate, which is conducive to grain refinement.
4.2.2 Multiple births
The essence of inoculation is to deoxidize and desulfurize to form foreign crystal grains. Its purpose is to increase the graphite nucleation ability, refine the crystal grains, increase the number of graphite balls, and increase the ferrite content. After three incubations, especially 0.3~1mm in the casting process. The Ba-containing inoculant for instant inoculation, although the inoculation volume is small, the inoculation effect is significant.
4.3 Purify molten iron, reduce slag and inclusions inside and between grains
Material fractures are often transgranular or intergranular fractures. There are inclusions or inclusions inside or between the grains of the material, which weaken the bonding force of the material. Under the action of impact load, it often forms the source of cracks or the path of crack propagation. Reduce the low temperature impact resistance of the material.
4.3.1 Pretreatment of molten iron
4.3.1.1 Deoxidation and desulfurization treatment
For manufacturers who use cupola-circuit duplex smelting, they can adopt the shake-in method or pneumatic desulfurization method for desulfurization to reduce the sulfur content in the original molten iron to less than 0.02%. However, the current desulfurization agent used is large Part of it is CaO or CaC2. This kind of desulfurizer has poor deoxidizing ability, and it is better to properly assist some deoxidizing elements such as Ca, Ba, Al and other elements. For direct smelting using electric furnaces, it is also necessary to deoxidize and desulfurize molten iron.
4.3.1.2 Overheating and standing of molten iron
Increasing the smelting temperature of molten iron can make the inclusions in the raw materials, as well as the slag and inclusions formed during the smelting process, float to the molten iron
On the surface, especially for the use of scrap steel recarburization process, it is necessary to appropriately increase the melting temperature ≥ 1500 ℃ and increase the holding time, otherwise, the carbon cannot be completely dissolved in the molten iron and form slag inclusions. The spheroidized molten iron is allowed to stand for 1 to 3 minutes, which is conducive to the floating of the oxides and sulfides of active metals such as Mg, Ba, Al, and Fe, thereby purifying the molten iron.
4.3.1.3 Multiple coverage and frequent slag removal
More coverage is conducive to the smelting process, reducing the contact time between molten iron and air during the casting process, and reducing the oxygen content in the molten iron; frequent slag removal is conducive to the accumulation of residual oxides and sulfides formed during the smelting process or spheroidizing process , So as to separate the iron from the slag, and ensure that the molten iron before entering the cavity is well purified.
4.3.1.4 Liquid iron filtration
In combination with the casting system, a slag bag with a filter is installed on the mold or in the mold, one is to prevent the passage of solid and liquid slag; the other is to benefit the iron
The liquid is smoothly injected into the cavity to reduce the formation of secondary oxidation slag; the third is to float some slag collection in the slag bag to minimize the entry of primary slag into the cavity.
4.4 Reduce grain boundary segregation elements
Mn, Sb, Sn, As, Ti and other elements are grain boundary segregation elements, so their content should be reduced as much as possible.
4.5 Reduce oxide and sulfide forming elements
Ca, Ba, Al, Mg, rare earth elements are easy to form oxides and sulfides, so their content should be reduced as much as possible
4.6 Special nodulizer and inoculant
The spheroidizing agent and inoculant used to produce low-temperature impact-resistant ductile iron should pay attention to the following three principles
- One is: high stable spheroidization and inoculation effect: this aspect depends on the stability of the composition of the spheroidizing agent itself, the deviation range of the main elements such as Mg, Re, Ca, Ba, etc. should be less than ±0.3%; on the other hand, molten iron The stability of quality, such as the temperature of iron tapping, the stability of S and O content; the third is the stability of the operation process, such as the control of the iron tapping speed and the iron removal position, to prevent the iron from being too slow to make the molten iron direct into the nodulizer.
- The second is: strong inking ability, Mg and Re are the main spheroidizing elements, and they are also strong white-mouth forming elements. It should be mainly Mg, supplemented by Re element, and reasonably match Ca, Ba, Bi and other elements with strong inking ability.
- The third is: lower slag-forming ability, on the one hand, the slag content in the nodulizer and inoculant, such as MgO, rare earth oxides and other foreign slag, should be minimized. At the same time, the content of Ca and Ba in the spheroidizing agent and inoculant should be moderate, because they have strong slag-forming ability.
5. The resolution of a pair of contradictions
The content and amount of Mg, Re, Ca, Ba and other elements in spheroidizing agent and inoculant are in contradiction with the spheroidizing effect and low-temperature impact performance. The addition of Mg, Re, Ca, Ba and other elements in the molten iron is excessive , Will cause the residual molten iron content of the above elements to be higher, and the higher oxidation and sulfidation slag will inevitably affect the impact performance. However, you should not give up eating due to choking. If the above elements are too low, it will also affect the spheroidization effect and matrix tissue, and the effect will not be achieved. According to different molten iron quality, casting size, shape, wall thickness, pouring time and other conditions, select the right special spheroidizing agent, inoculant and supporting process measures.
6. Conclusion
In general, as long as the metallurgical quality of molten iron is well controlled, the content of C, Si, Mn, Ca, Ba, Re, and other elements should be controlled, and the content of other elements should be reduced as much as possible. Special nodulizers, inoculants and supporting facilities should be selected. Craftsmanship, strict technological process, perfect testing methods of various parameters. So, it is not very difficult to stably produce low-temperature impact-resistant ductile iron castings.
Please keep the source and address of this article for reprinting:Increase The Ferrite Content Of Ductile Iron
Minghe Die Casting Company are dedicated to manufacture and provide quality and high performance Casting Parts(metal die casting parts range mainly include Thin-Wall Die Casting,Hot Chamber Die Casting,Cold Chamber Die Casting),Round Service(Die Casting Service,Cnc Machining,Mold Making,Surface Treatment).Any custom Aluminum die casting, magnesium or Zamak/zinc die casting and other castings requirements are welcome to contact us.
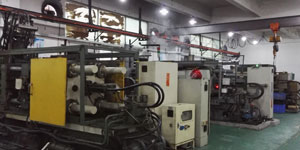
Under the control of ISO9001 and TS 16949,All processes are carried out through hundreds of advanced die casting machines, 5-axis machines, and other facilities, ranging from blasters to Ultra Sonic washing machines.Minghe not only has advanced equipment but also have professional team of experienced engineers,operators and inspectors to make the customer’s design come true.
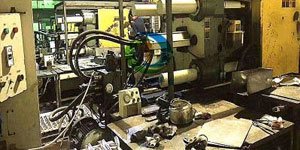
Contract manufacturer of die castings. Capabilities include cold chamber aluminum die casting parts from 0.15 lbs. to 6 lbs., quick change set up, and machining. Value-added services include polishing, vibrating, deburring, shot blasting, painting, plating, coating, assembly, and tooling. Materials worked with include alloys such as 360, 380, 383, and 413.
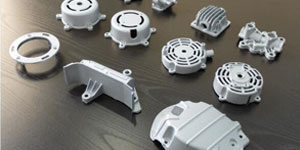
Zinc die casting design assistance/concurrent engineering services. Custom manufacturer of precision zinc die castings. Miniature castings, high pressure die castings, multi-slide mold castings, conventional mold castings, unit die and independent die castings and cavity sealed castings can be manufactured. Castings can be manufactured in lengths and widths up to 24 in. in +/-0.0005 in. tolerance.
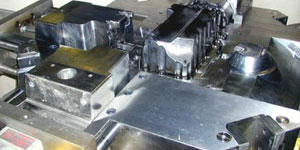
ISO 9001: 2015 certified manufacturer of die cast magnesium, Capabilities include high-pressure magnesium die casting up to 200 ton hot chamber & 3000 ton cold chamber, tooling design, polishing, molding, machining, powder & liquid painting, full QA with CMM capabilities, assembly, packaging & delivery.
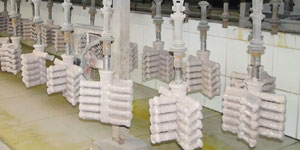
ITAF16949 certified. Additional Casting Service Include investment casting,sand casting,Gravity Casting, Lost Foam Casting,Centrifugal Casting,Vacuum Casting,Permanent Mold Casting,.Capabilities include EDI, engineering assistance, solid modeling and secondary processing.
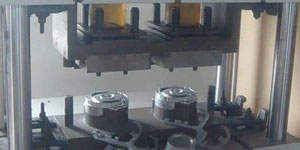
Casting Industries Parts Case Studies for: Cars, Bikes, Aircraft, Musical instruments, Watercraft, Optical devices, Sensors, Models, Electronic devices, Enclosures, Clocks, Machinery, Engines, Furniture, Jewelry, Jigs, Telecom, Lighting, Medical devices, Photographic devices, Robots, Sculptures, Sound equipment, Sporting equipment, Tooling, Toys and more.
What Can we help you do next?
∇ Go To Homepage For Die Casting China
→Casting Parts-Find out what we have done.
→Ralated Tips About Die Casting Services
By Minghe Die Casting Manufacturer |Categories: Helpful Articles |Material Tags: Aluminum Casting, Zinc Casting, Magnesium Casting, Titanium Casting, Stainless Steel Casting, Brass Casting,Bronze Casting,Casting Video,Company History,Aluminum Die Casting |Comments Off