On-site Antibacterial Maintenance Of Die-Casting Release Agent
In the high-pressure die-casting industry, traditional mold release agents are used in the process of use. Due to external pollution and other primitives, they usually cause microbial contamination of the mold release agent diluent during use, resulting in clogging of the filter screen and failure of the mold release agent. problem. This article describes how to eliminate the problem of microbial contamination from the origin of microorganisms and how to use the correct maintenance methods for these microorganisms on site.
Release agent is an important material in the production of non-ferrous metal die-casting. It usually plays the role of demolding, preventing the welding of molten metal and the mold, ensuring the smooth ejection of the workpiece, and occasionally lubricating, assisting in filling and lubricating the movable parts (thimble and slider). Moreover, its concentrated liquid and water-based characteristics give the release agent the effect of lowering the mold temperature and reducing the thermal stress of the mold. The release agent also serves to protect the surface of the mold from metal corrosion. Traditional release agents need to be diluted with water during use. At present, the common dilution methods on the market include automatic proportioning and manual proportioning, while the supply of diluents is mainly based on single machine proportioning and centralized proportioning. Mainly. Whether the water quality of the diluent is qualified, whether it contains bacteria, whether the dilution tank and the supply pipeline are clean, to a large extent affect the normal use and efficacy of the release agent. If the on-site management and maintenance of the diluent is not done properly, it will cause bacteria to grow, which will block the filter, flocculation and microorganisms will be generated in the dilution tank, which will cause the release agent to demulsify, block the nozzle, and affect the final use of the release agent. , And there will be unpleasant odors, which will affect the on-site working environment. All of these will lead to reduced die-casting production efficiency, increase labor, and cause a lot of waste of release agent. Among all these influencing factors, the role of microorganisms is very important. This article will discuss the causes of microorganisms, their impact on the site and use of die-casting release agents, and how to do good on-site maintenance to avoid or eliminate these microorganisms.
1 The Causes Of Microorganisms
Microorganisms are ubiquitous in our daily lives, and they are so small that they are usually invisible to the naked eye. Microorganisms are generally divided into four categories: bacteria, molds, viruses and yeasts. They usually have rapid reproduction ability and strong adaptability. The production of microorganisms depends on many conditions, temperature, pH, organic matter content, oxygen content, mineral content, etc. will breed bacteria. For most microorganisms, the most suitable temperature is 25-40°C. The most suitable acid-base conditions for microorganisms are different. The suitable living environment for most bacteria is in the pH range of 5.5-8. 5, while the main living conditions for molds and yeasts are acidic environments. Microorganisms not only multiply in large numbers, such as bacteria, but the bacterial membranes they produce will also be continuously transferred through external media such as water and human bodies. These biological membranes contain one or more types of bacteria or colonies. The main feature of biofilm is extracellular polymer, the main composition is some high molecular substances such as polysaccharides, proteins and nucleic acids. At the die-casting site, there are many media that spread microorganisms, such as water, and external impurities such as oil and other organic matter. Especially in the supply system of the release agent, many conditions are conducive to the survival and reproduction of microorganisms. Once these films have performance, they will adhere to the release agent dilution tank, supply pipes and filter screens. This causes the filter to block and the release agent to fail.
2.Customer Site Microbial Source Analysis And Antibacterial Product Performance Research
We collected microbial film at the contaminated die-casting site and performed laboratory analysis to specify the hazards of microbes. In the process of using the release agent, customer M found grease accumulation in the dilution tank of its machine, and there was a layer of skin on the inner wall. Moreover, due to microorganisms, the filter screen causes the release agent to demulsify and flocculate and become clogged on the screen. And the filter also produced pollution, appearing orange-yellow. We collected some solid and liquid samples from M customers, and then carried out microbiological analysis and testing.
Testing Sample:
Taken from the wall of the dilution tank at the customer's site, the fouling in the supply pipeline and the filter screen is used for microbiological testing and analysis, and the microbial content of the dilution liquid and the dilution water is also analyzed.
Testing Method:
The solid is smeared on a plate, diluted with water and diluent, neutralized, and then the bacteria culture is started. The medium is pasteurized soybean casein agar culture (TSA) and pasteurized Sabouraud agar medium (SDA), the temperature is 30°/25°, and it is carried out under aerobic conditions.
Test Results:
After 7 days of microbial culture test, it was found that there were bacteria in the water samples (Form #1, 2, 3), but the content of sample 1 was lower than that of sample 2. However, all solid samples obtained from the dilution tank of the machine at the site contained a large amount of bacteria (No. 12-23, 27-32, 34-39 in Figure 2 and Figure 3), especially the samples found to contain Pseudomonas aeruginosa. This Pseudomonas genus grows very fast (in sample Nos. 8, 24, 25, 32, and 33 in Figure 4). And the fouling material removed from the filter is green, which also proves that it contains a large amount of Pseudomonas aeruginosa. There are also a large number of colonies in the pipeline and in the dilution tank, which will be carried into the release agent dilution process (Figure 5), thereby clogging the filter screen. It can be seen from the results that the dilution of product A (antibacterial product) is less polluted than product B (especially in the second dilution tank, table 1, samples 4-7).
These serious pollutions are not only caused by the mixing of external oil or other pollutants. If the circulatory system itself is not maintained, it will aggravate microbial pollution. Because once these microbial colonies fall off the wall of the dilution tank, the diluent will quickly become contaminated.
3. On-site Maintenance
From the above analysis and test results, we can see the impact of microbial infection on the use of mold release agents during the die-casting process and the hazards to on-site safety management, such as the aforementioned Pseudomonas aeruginosa, which may cause human diseases. Therefore, we need to do a good job of on-site management of the release agent diluent and its supporting facilities, so as to avoid microbial infection, so that the release agent can maximize its use benefits. The following will focus on how to carry out correct site management.
3.1 Cleaning
Carry out a large wash at least once a year to remove impurities (bacterial film, inorganic substances and residues of the release agent) in the entire system of the release agent. Usually, it is necessary to wash and sterilize regularly to ensure the effective operation of the release agent supply system.
For the usual washing steps and related maintenance products, please refer to the following introduction:
Before chemical washing:
- Use a rag (do not use flannel) to wipe all equipment (such as mixing tanks, pipes) that are in contact with the release agent, and if possible, use high-pressure gas to clean it.
- Remove the nozzle when washing to avoid the accumulation of debris into the nozzle. The nozzles can be washed manually or with washing equipment. When washing it, use Han Gao's Bonderite C-AK 5520 to dilute to 5%. If it is very difficult to wash, you can also add 0.1% of Han髙 product BonderiteC-AD 1270 to improve the washing ability.
The same mixture is also used in subsequent cycles of washing. 5% BonderiteC-AK 5520 and 0./% BonderiteC-AD 1270
When washing, completely empty the mixing tank and add the washing mixture at the same time. Then adjust the power of the equipment to the highest cycle for at least four hours. High power can improve high washing efficiency (mechanical action)
During the washing process, the filter should be removed to avoid clogging. The ball valve performs multiple flow direction switching to ensure that all sediment and bacterial skin can be removed.
The pH of the lotion is very high (10 or more). Avoid direct discharge to the sewer before untreated. The main difference between this waste liquid and the release agent waste liquid is pH. Before discharge, it needs to go through the factory wastewater station or a third-party qualified company for treatment in accordance with local environmental protection regulations.
It should be noted that sodium salts can cause waste accumulation and metal corrosion. Therefore, it is necessary to thoroughly wash the system with clean water after the washing step is completed.
3.2 Sterilization
Flush the system with water until the pH is neutral. Then use water containing similar DBNPA fungicides for pipeline circulation and washing (described below) for at least half an hour. Finally, rinse the pipeline with deionized water without bactericide, see step 3 for details.
Dow Chemical’s BIOBANDB20 is a product containing DBNPA (a solution containing 0.025% BIOBANDB20 is equivalent to 50ppm DBNPA)•DBNPA is a fast-killing bactericide, without oxidants, and can control various bacteria such as good The growth of aerobic bacteria, anaerobic bacteria, fungi, algae and biological sludge.
The rapid killing performance of DBNPA makes it possible to sterilize quickly (as mentioned above, 30 minutes is enough). During the process of flushing and circulation, the ball valve must switch the flow direction many times to ensure that all places in the system can be exposed to the biocide.
It should be noted that DBNPA may cause corrosion of the aluminum surface (see product safety instructions). In the subsequent flushing step, the filter screen needs to be installed to check whether there is any accumulation. If there are any, you need to continue to repeat the first step of the washing process.
After washing, close all the outlets of the equipment, especially the ball valve, to ensure that it will not be contaminated by external pollutants.
DBNPA can be quickly degraded into harmless substances, so it can be safely discharged. Therefore, the final emissions do not contain hazardous materials. There are only detergent residues and stains washed away in the wastewater. Waste water discharge methods and standards are treated in accordance with local laws and regulations.
3.3 Use deionization for final cleaning
After finishing the previous treatment, it is recommended to use deionized water for the final wash (if there is no condition, at least use sterile water) to remove the residue. It should be noted that if there are acidic/oxidizing biocides in the system, it may cause corrosion of pipelines and molds (see product safety manual for details).
- Recommended water quality:
- Solid content <0.01%
- pH 6-8
- Conductivity<50|is
- Microbial content <103CUFml
If the second step is handled properly, the wastewater from the third step can be directly discharged to the factory wastewater treatment station. This is determined according to local environmental regulations and standards 6
3.4 Monitoring The Water Supply System
Regularly check and replace the tap water filter to prevent microorganisms from growing and accumulating more over time.
In addition, use effective methods to regularly detect the microbial content in the water (do not use bacteria test tablets). When the microbial content in the water is reduced and stabilized, the detection frequency can be reduced.
3.5 Personal Health And Environmental Protection
It is best to use disposable towels instead of flannel during washing. After all processes are completed, clean up the contaminants (stains and used products) at the work site (floor) to avoid subsequent cross-contamination.
Please keep the source and address of this article for reprinting:On-site Antibacterial Maintenance Of Die-Casting Release Agent
Minghe Die Casting Company are dedicated to manufacture and provide quality and high performance Casting Parts(metal die casting parts range mainly include Thin-Wall Die Casting,Hot Chamber Die Casting,Cold Chamber Die Casting),Round Service(Die Casting Service,Cnc Machining,Mold Making,Surface Treatment).Any custom Aluminum die casting, magnesium or Zamak/zinc die casting and other castings requirements are welcome to contact us.
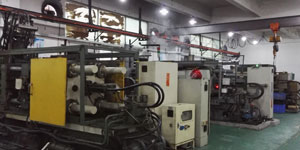
Under the control of ISO9001 and TS 16949,All processes are carried out through hundreds of advanced die casting machines, 5-axis machines, and other facilities, ranging from blasters to Ultra Sonic washing machines.Minghe not only has advanced equipment but also have professional team of experienced engineers,operators and inspectors to make the customer’s design come true.
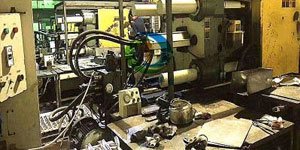
Contract manufacturer of die castings. Capabilities include cold chamber aluminum die casting parts from 0.15 lbs. to 6 lbs., quick change set up, and machining. Value-added services include polishing, vibrating, deburring, shot blasting, painting, plating, coating, assembly, and tooling. Materials worked with include alloys such as 360, 380, 383, and 413.
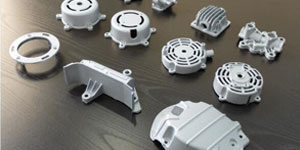
Zinc die casting design assistance/concurrent engineering services. Custom manufacturer of precision zinc die castings. Miniature castings, high pressure die castings, multi-slide mold castings, conventional mold castings, unit die and independent die castings and cavity sealed castings can be manufactured. Castings can be manufactured in lengths and widths up to 24 in. in +/-0.0005 in. tolerance.
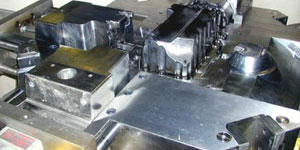
ISO 9001: 2015 certified manufacturer of die cast magnesium, Capabilities include high-pressure magnesium die casting up to 200 ton hot chamber & 3000 ton cold chamber, tooling design, polishing, molding, machining, powder & liquid painting, full QA with CMM capabilities, assembly, packaging & delivery.
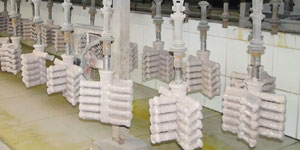
ITAF16949 certified. Additional Casting Service Include investment casting,sand casting,Gravity Casting, Lost Foam Casting,Centrifugal Casting,Vacuum Casting,Permanent Mold Casting,.Capabilities include EDI, engineering assistance, solid modeling and secondary processing.
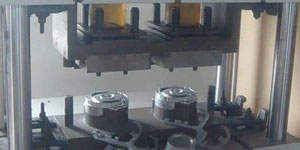
Casting Industries Parts Case Studies for: Cars, Bikes, Aircraft, Musical instruments, Watercraft, Optical devices, Sensors, Models, Electronic devices, Enclosures, Clocks, Machinery, Engines, Furniture, Jewelry, Jigs, Telecom, Lighting, Medical devices, Photographic devices, Robots, Sculptures, Sound equipment, Sporting equipment, Tooling, Toys and more.
What Can we help you do next?
∇ Go To Homepage For Die Casting China
→Casting Parts-Find out what we have done.
→Ralated Tips About Die Casting Services
By Minghe Die Casting Manufacturer |Categories: Helpful Articles |Material Tags: Aluminum Casting, Zinc Casting, Magnesium Casting, Titanium Casting, Stainless Steel Casting, Brass Casting,Bronze Casting,Casting Video,Company History,Aluminum Die Casting |Comments Off