Repair Welding Methods And Experience Of Several Common Steel Casting Defects
This article introduces common valve steel casting defects and repair welding methods. Scientific repair welding of steel casting defects is an energy-saving remanufacturing engineering technology. This article gives a detailed explanation on the judgment and elimination of defects. Give answers to the repair welding method, frequency, and handling experience after repair welding. The economical and effective practical experience in defect repair welding is summarized.
Defect Treatment
1.Defect Removal
In the factory, carbon arc air gouging is generally used to blow away casting defects, and then a portable angle grinder is used to polish the defective parts to reveal the metallic luster. However, in production practice, carbon steel electrodes are used to remove defects directly with high current and an angle grinder is used to grind the metallic luster. Generally, casting defects can be eliminated by using <4mm-J422 welding rod, 160~180A current, to remove the defects, and the angle grinder will grind the defects into a U shape to reduce welding stress. Defects are removed thoroughly and repair welding is of good quality.
2.Defect Judgment
In production practice, repair welding is not allowed for some casting defects, such as penetrating cracks, penetrating defects (bottom penetration), honeycomb pores, sand and slag that cannot be removed, and shrinkage with an area of more than 65 cm2, etc., and the contract between the two parties Other major defects that cannot be repaired as agreed in the The type of defect should be judged before repair welding.
3.Preheating of defective parts
Carbon steel and austenitic stainless steel castings, where the area of the repair welding part is less than 65cm2, and the depth is less than 20% of the thickness of the casting or 25mm, generally no preheating is required. However, pearlitic steel castings such as ZG15Cr1Mo1V, ZGCr5Mo, etc., due to the high tendency of hardening of steel and easy cracking in cold welding, should be pre-heated. The pre-heating temperature is 200-400℃ (repair welding with stainless steel electrode, and the temperature is a small value). The holding time should not be less than 60min. If the casting cannot be preheated as a whole, oxygen-acetylene can be used to expand the defect part by 20mm and then heat it to 300-350℃ (observe the dim red on the dark side). The large torch neutral torch can be made at the defect and the periphery first. Swing the circumference quickly for a few minutes, then change to slow movement and keep it for 10 minutes (depending on the thickness of the defect), so that the defective part is fully preheated, and then quickly repaired.
Repair Welding Method
1.Claim
When repair welding austenitic stainless steel castings, it should be cooled quickly in a ventilated place. For pearlitic low-alloy steel castings and carbon steel castings with too large repair welding area, the leeward position or windshield should be selected to avoid cracks caused by rapid cooling. For repair welding of a build-up layer, the slag should be removed immediately after repair welding, and hammering uniformly along the defect center outwards to reduce repair welding stress. If the repair welding is carried out in several layers (generally 3 to 4 mm is a repair welding layer), the slag and hammer repair welding area must be removed in time after each layer repair welding. If welding is performed in winter, for ZG15Cr1Mo1V pearlite alloy steel castings, oxygen-acetylene should be repeatedly heated for each repair welding layer, and then quickly repaired to avoid welding cracks.
2.Electrode treatment
Before repair welding, first check whether the electrode is preheated. Generally, the electrode should be dried at 150~250℃ for 1h. The preheated welding rod should be placed in the incubator, so that it can be taken as soon as it is used. The electrode is preheated 3 times repeatedly. If the coating on the electrode surface is peeled off, cracked and rusted, it should not be used.
3.Repair welding times
For pressure-bearing castings, such as valve housings that have been pressure-tested for water seepage, the same part is generally only allowed to be repaired once, and repair welding cannot be repeated, because multiple repair welding will make the grains in the steel coarse and affect the pressure-bearing performance of the casting, unless the casting can be Re-heat treatment after welding. For other non-pressure-bearing repair welding of the same part, it is generally stipulated that repair welding should not exceed 3 times. For carbon steel castings that have more than two repair welds in the same part, they should be treated with stress relief after welding.
4.Repair welding layer height
The repair welding height of the casting is generally about 2mm higher than the plane of the casting to facilitate machining. The repair welding layer is too low, and the welding scar is easy to be exposed after machining. The repairing layer is too high, which is time-consuming, labor-intensive and material-intensive.
Post-Repair Welding
1.Important repair welding
The castings with leakage in the hydraulic test, the castings with repair welding area> 65cm2, and the castings with depth> 20% of the casting wall thickness or 25mm, are considered to be important repair welding in ASTMA217/A217M-2007. It is proposed in the A217 standard for this important repair welding that stress relief treatment or complete reheating treatment should be carried out, and this stress relief treatment or complete reheating treatment must be carried out by an approved method, that is, important repair welding needs to be formulated Repair welding process. ASTMA352/A352M2006 stipulates that stress relief or post-weld heat treatment after important repair welding is mandatory. my country's industry standard JB/T5263-2005 corresponding to A217/A217M defines important repair welding as "heavy defects". But in fact, in addition to casting blanks that can be completely reheated, many defects are often found in the finishing process, and can no longer be completely heat-treated. Therefore, in production practice, it is usually solved by an experienced welder with a pressure vessel welding certificate on the spot.
2.Stress relief
After repairing the defects found after finishing welding, the overall stress relief tempering treatment can no longer be done. Generally, the partial heating and tempering method of oxygen-acetylene flame at the defect site can be used. The neutral flame of a large cutting torch is slowly swayed back and forth, and the casting is heated to a visible dark red (about 740℃) on the surface, and heat preservation (2min/mm, but not less than 30min). Asbestos board should be covered on the defect immediately after stress relief treatment. For the defects on the diameter of the pearlitic steel valve, asbestos plates should be filled in the inner cavity of the diameter to make it cool slowly when repairing welding. This kind of operation is simple and economical, but it requires the welder to have certain practical experience.
Stainless steel castings are generally not treated after repair welding, but welding should be performed in a ventilated place to make the repair welding area cool quickly. Unless the repair welding shows that it has caused a change in the austenite structure, or is a serious defect. Where the contract and conditions permit, the solution treatment should be redone. Carbon steel castings and various pearlite castings with excessively large and deep defect areas, which are in the cleaning stage of the castings and have entered rough machining but have a finishing allowance, should be subjected to stress relief treatment after repair welding. The stress relief tempering temperature of carbon steel can be set to 600~650℃, the tempering temperature of ZG15Cr1Mo1V and ZGCr5Mo can be set to 700~740℃, and the tempering temperature of ZG35CrMo can be set to 500~550℃. For all steel castings, the stress-relieving tempering time is not less than 120min, and they are cooled to below 100°C with the furnace.
3.Non-destructive testing
For "heavy defects" and "important repair welding" of valve castings, ASTMA217A217M-2007 standard stipulates that if the production of castings meets the requirements of S4 (magnetic particle inspection) supplementary requirements, repair welding should be inspected by magnetic particle inspection of the same quality standard for inspecting the castings. . If the production of castings meets the requirements of S5 (radiographic inspection) supplementary requirements, for castings that leak in the hydraulic test, or any pits that are to be repaired, the depth of which exceeds 20% of the wall thickness or 1in1 (25mm) and the castings are prepared for repair welding. Any repair welding of castings with a pit area larger than about 10in2 (65cm2) must be inspected by the same standard radiographic inspection as the casting. The JB/T5263-2005 standard stipulates that radiographic or ultrasonic testing should be carried out after heavy defects are repaired. That is to say, for heavy defects and important repair welding, effective non-destructive inspection must be carried out, and it can be used after being qualified.
Please keep the source and address of this article for reprinting:Repair Welding Methods And Experience Of Several Common Steel Casting Defects
Minghe Die Casting Company are dedicated to manufacture and provide quality and high performance Casting Parts(metal die casting parts range mainly include Thin-Wall Die Casting,Hot Chamber Die Casting,Cold Chamber Die Casting),Round Service(Die Casting Service,Cnc Machining,Mold Making,Surface Treatment).Any custom Aluminum die casting, magnesium or Zamak/zinc die casting and other castings requirements are welcome to contact us.
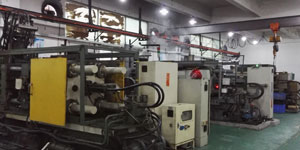
Under the control of ISO9001 and TS 16949,All processes are carried out through hundreds of advanced die casting machines, 5-axis machines, and other facilities, ranging from blasters to Ultra Sonic washing machines.Minghe not only has advanced equipment but also have professional team of experienced engineers,operators and inspectors to make the customer’s design come true.
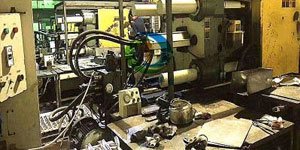
Contract manufacturer of die castings. Capabilities include cold chamber aluminum die casting parts from 0.15 lbs. to 6 lbs., quick change set up, and machining. Value-added services include polishing, vibrating, deburring, shot blasting, painting, plating, coating, assembly, and tooling. Materials worked with include alloys such as 360, 380, 383, and 413.
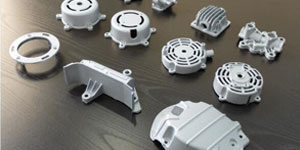
Zinc die casting design assistance/concurrent engineering services. Custom manufacturer of precision zinc die castings. Miniature castings, high pressure die castings, multi-slide mold castings, conventional mold castings, unit die and independent die castings and cavity sealed castings can be manufactured. Castings can be manufactured in lengths and widths up to 24 in. in +/-0.0005 in. tolerance.
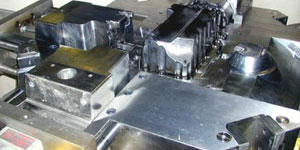
ISO 9001: 2015 certified manufacturer of die cast magnesium, Capabilities include high-pressure magnesium die casting up to 200 ton hot chamber & 3000 ton cold chamber, tooling design, polishing, molding, machining, powder & liquid painting, full QA with CMM capabilities, assembly, packaging & delivery.
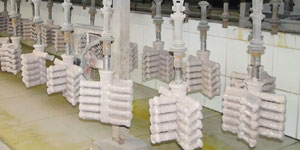
ITAF16949 certified. Additional Casting Service Include investment casting,sand casting,Gravity Casting, Lost Foam Casting,Centrifugal Casting,Vacuum Casting,Permanent Mold Casting,.Capabilities include EDI, engineering assistance, solid modeling and secondary processing.
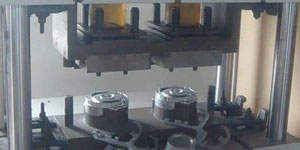
Casting Industries Parts Case Studies for: Cars, Bikes, Aircraft, Musical instruments, Watercraft, Optical devices, Sensors, Models, Electronic devices, Enclosures, Clocks, Machinery, Engines, Furniture, Jewelry, Jigs, Telecom, Lighting, Medical devices, Photographic devices, Robots, Sculptures, Sound equipment, Sporting equipment, Tooling, Toys and more.
What Can we help you do next?
∇ Go To Homepage For Die Casting China
→Casting Parts-Find out what we have done.
→Ralated Tips About Die Casting Services
By Minghe Die Casting Manufacturer |Categories: Helpful Articles |Material Tags: Aluminum Casting, Zinc Casting, Magnesium Casting, Titanium Casting, Stainless Steel Casting, Brass Casting,Bronze Casting,Casting Video,Company History,Aluminum Die Casting |Comments Off