New Process Of W-type Die Cast Aluminum Water-Cooled Base
With the rapid development of power packs, electric vehicles, and subway motor manufacturing technologies, cast aluminum water-cooled frame structures are widely used in motor manufacturing. Green and environmentally friendly energy electric vehicle motors, high-speed EMU power pack generators, airport bus motors, and rail-use urban traffic permanent magnet traction motors mostly use cast aluminum water-cooled bases. The good heat dissipation effect of the water-cooled casting frame is the key to meeting the requirements of motor manufacturing. The main manufacturing process includes metal smelting technology, forming technology, assembly technology, processing technology and other aspects. Whether the structure of the cast aluminum water-cooled machine base is reasonable, and the quality of it directly affects the operating reliability, labor productivity and economic benefits of this type of motor. Application structure Reasonable cast aluminum water-cooled frame structure can improve the operating reliability of this type of motor frame, shorten the manufacturing cycle, save manufacturing costs, and improve labor productivity and economic benefits.
1. Current production technology status of water-cooled frame
1.1 Process method
The manufacturing methods of cast aluminum water-cooled bases in the same industry at home and abroad include: integral sand casting, split sand casting, extrusion molding, etc. The overall casting process is: mold core box manufacturing-sand mold sand core production-alloy smelting-box assembly-pouring-cleaning-finished product. The split casting process is: mold core box manufacturing-sand mold sand core manufacturing-alloy smelting-box assembly-pouring-cleaning-processing-welding-assembly to form a base blank. The extrusion molding process is: mold manufacturing-cast aluminum smelting-pouring aluminum ingots-high-pressure extrusion molding-welding-machine base blanks.
1.2 Shortcomings of traditional crafts and methods
The problem of integral casting cast aluminum water-cooled frame is low yield of the frame and long manufacturing cycle. The biggest problem is difficult to clean the water channel sand core and difficult to fix the water channel sand core; the structure of the split sand cast aluminum water-cooled frame has problems. The production process is cumbersome, the cycle is too long, the quality is difficult to control, and the inner and outer cylinders need to be pre-processed, and the end faces are sealed and welded, which is easy to leak after processing; the extruded cast aluminum water-cooled base structure: limited by the tonnage of the press, large The machine base cannot be realized, and there is the risk of water leakage due to the sealing and welding seam that needs to be processed. Often, the machine base leaks due to welding quality problems, which affects the machine base performance and even causes the motor to be scrapped.
2. Conception and Goal of the New Process Method
By analyzing the shortcomings of traditional process methods, a new process is proposed, the characteristics of which include:
- 1) Inside and outside high pressure one-time molding casting.
- 2) The structural features of the cooling channel are formed at one time with the inner and outer cylinders.
- 3) Eliminates the difficult and long processing steps of the cooling water channel of the machine base.
- 4) The welding seam is controlled on the inner side of the flange, and the welding seam must not be processed, which solves the pressure and water leakage problem of the machine base during the welding process.
- 5) Set up positioning and anti-channeling structures on the wall of the waterway to improve the reliability of the machine base.
- 6) Interference heating sleeve forming.
- a1: inlet
- a2: Waterway
- a3: Inner cylinder weld protection flange and end cover
- a4: Cooling Waterway
- a5: Anti-Water Guide Key
3. The Specific Implementation Process Of The New Process
The process of the new die-casting process is: mold manufacturing-alloy smelting-die casting-hot sleeve-welding-base blank. The inner and outer cylinder water channels are cast into shape by die casting method, no processing is required. Make full use of the characteristics of die-casting, fast speed, high surface finish, using die-casting technology, die-casting into outer and inner cylinders. The W-shaped channel structure and guiding W groove are cast on the inner cylinder as shown in Figure 2; the outer cylinder is cast with a guiding and locking structure, the inner and outer cylinders are preheated at the same time, and then the inner and outer cylinders are heated as shown in Fig. 3.
The seal is welded into a base blank as shown in Figure 4. The advantages of the new process are:
- 1) The inner and outer cylinders are directly formed by die-casting without processing water channels.
- 2) The outer cylinder has an inner flange, and the inner cylinder has an outer flange to protect the weld.
- 3) The inner and outer cylinders are preheated for interference heating.
- 4) Set up guiding and locking devices to ensure the reliability of the base.
4. Conclusion
The new production process of W-shaped water-cooled frame is a precedent in the domestic professional motor manufacturing industry. Based on the absorption of domestic and foreign cast aluminum frame manufacturing technology, combined with the casting structure, special process methods are used to realize the manufacturing of W-shaped cast aluminum water-cooled frame In the process, the characteristics of pressure casting are fully utilized, preheating interference sleeves are used, weld protection and water leakage prevention structure are cleverly arranged, and the manufacture of W-shaped cast aluminum water-cooled machine base is realized. Shorten the product development cycle, reduce the difficulty and labor intensity of motor production, simplify the manufacturing process of electrical machinery key components, improve the reliability of manufacturing and operation, and effectively control the cost of motor manufacturing.
Please keep the source and address of this article for reprinting: New Process Of W-type Die Cast Aluminum Water-Cooled Base
Minghe Die Casting Company are dedicated to manufacture and provide quality and high performance Casting Parts(metal die casting parts range mainly include Thin-Wall Die Casting,Hot Chamber Die Casting,Cold Chamber Die Casting),Round Service(Die Casting Service,Cnc Machining,Mold Making,Surface Treatment).Any custom Aluminum die casting, magnesium or Zamak/zinc die casting and other castings requirements are welcome to contact us.
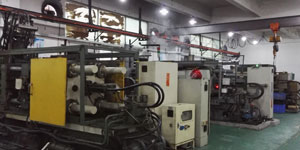
Under the control of ISO9001 and TS 16949,All processes are carried out through hundreds of advanced die casting machines, 5-axis machines, and other facilities, ranging from blasters to Ultra Sonic washing machines.Minghe not only has advanced equipment but also have professional team of experienced engineers,operators and inspectors to make the customer’s design come true.
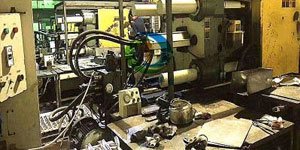
Contract manufacturer of die castings. Capabilities include cold chamber aluminum die casting parts from 0.15 lbs. to 6 lbs., quick change set up, and machining. Value-added services include polishing, vibrating, deburring, shot blasting, painting, plating, coating, assembly, and tooling. Materials worked with include alloys such as 360, 380, 383, and 413.
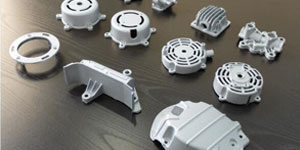
Zinc die casting design assistance/concurrent engineering services. Custom manufacturer of precision zinc die castings. Miniature castings, high pressure die castings, multi-slide mold castings, conventional mold castings, unit die and independent die castings and cavity sealed castings can be manufactured. Castings can be manufactured in lengths and widths up to 24 in. in +/-0.0005 in. tolerance.
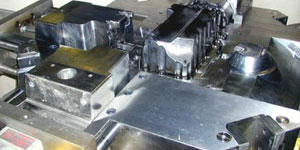
ISO 9001: 2015 certified manufacturer of die cast magnesium, Capabilities include high-pressure magnesium die casting up to 200 ton hot chamber & 3000 ton cold chamber, tooling design, polishing, molding, machining, powder & liquid painting, full QA with CMM capabilities, assembly, packaging & delivery.
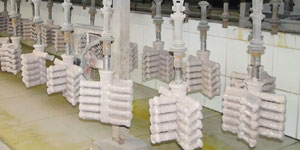
ITAF16949 certified. Additional Casting Service Include investment casting,sand casting,Gravity Casting, Lost Foam Casting,Centrifugal Casting,Vacuum Casting,Permanent Mold Casting,.Capabilities include EDI, engineering assistance, solid modeling and secondary processing.
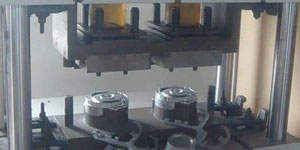
Casting Industries Parts Case Studies for: Cars, Bikes, Aircraft, Musical instruments, Watercraft, Optical devices, Sensors, Models, Electronic devices, Enclosures, Clocks, Machinery, Engines, Furniture, Jewelry, Jigs, Telecom, Lighting, Medical devices, Photographic devices, Robots, Sculptures, Sound equipment, Sporting equipment, Tooling, Toys and more.
What Can we help you do next?
∇ Go To Homepage For Die Casting China
→Casting Parts-Find out what we have done.
→Ralated Tips About Die Casting Services
By Minghe Die Casting Manufacturer |Categories: Helpful Articles |Material Tags: Aluminum Casting, Zinc Casting, Magnesium Casting, Titanium Casting, Stainless Steel Casting, Brass Casting,Bronze Casting,Casting Video,Company History,Aluminum Die Casting |Comments Off