Effect of Drill and Nickel on the Thermal Damage Resistance of 4Cr5Mo2V Die Casting Die Steel
4Cr5 Mo2V is a commonly used die-casting die steel. In the process of die-casting aluminum alloy, due to the erosion and adhesion of molten aluminum, the mold will suffer thermal damage, such as thermal fatigue and thermal melt loss, resulting in a decrease in its hardness and even premature failure.
In order to study whether nickel or dryness can improve the thermal damage resistance of aluminum alloy die-casting molds, 4Cr5 Mo2V steel and 4Cr5Mo2V steel test blocks containing 1% Ni and 1% Co (mass fraction) were prepared, and they were inlaid after quenching and tempering. In the fixed die of the die-casting mold, the ADC12 aluminum alloy with a temperature of 800℃ was subsequently die-casted 200 to 1,000 times, and the macro morphology and surface hardness of the test block were examined.
The results show that after die-casting aluminum alloy 1,000 times, the 4Cr5Mo2V steel test block adhered to aluminum most severely and produced very few net-like cracks; the Ni-containing steel test block slightly adhered to aluminum, and the Co-containing steel test block adhered to aluminum the least, indicating that the content of 1% Co 4Cr5Mo2V steel has the best thermal damage resistance to die-cast aluminum alloys. In addition, compared with the hardness before die-casting aluminum alloy, after 1,000 times die-casting, the surface hardness of 4Cr5Mo2V steel, nickel-containing and dry-containing 4Cr5Mo2V steel specimens decreased by 2.8, 1.8 and 1.4 HRC, that is, multiple die-casting aluminum alloys. The adverse effect on the surface hardness of the nickel-containing and dry 4Cr5Mo2V steel is less than that of the 4Cr5Mo2V steel, which is related to the solid solution strengthening effect of Co and Ni, which is beneficial to improve the aluminum liquid erosion resistance of the mold and make the mold less susceptible to thermal damage.
Aluminum alloy die-casting is a complex high-temperature and high-pressure process. There are many factors that affect the thermal damage (including thermal fatigue and thermal loss) performance of aluminum alloy die-casting molds. Among them, the composition of hot-work die steel is particularly important.
Under normal circumstances, the failure of die casting die due to cracking and plastic deformation can be avoided. Mold cracking is usually caused by accidental mechanical overload or thermal overload, resulting in severe stress concentration. Early thermal fatigue cracking and welding loss (surface thermal damage) of die-casting molds are the main failure modes, and the two often affect each other. 4Cr5Mo2V steel is a widely used hot work die steel, with good wear resistance and plastic deformation resistance. Drill and nickel are commonly used alloying elements, which can effectively increase the strength and hardness of steel, and have a certain effect on resisting thermal damage. Therefore, 4Cr5Mo2V steel, 4Cr5Mo2V containing 1% Ni and 1% Co (mass fraction, the same below) are studied. The steel's resistance to molten aluminum damage is of great significance to guide actual production.
However, most of the methods to study the thermal damage of die-casting die steel before the mouth are to simulate heating and cooling. The die steel sample does not directly contact the molten aluminum, and does not involve the scouring effect of the molten aluminum, such as direct induction heating of the die steel sample. -A. In this paper, three-component mold steel test blocks were prepared and embedded in the die-casting mold to carry out the die-casting test of ADC12 aluminum alloy. Damage performance of molten aluminum.
1.Test Materials And Methods
1.1 Test Materials
The chemical composition of 4Cr5Mo2V steel, 4Cr5Mo2V steel containing 1% Ni (hereinafter referred to as 4Cr5Mo2V + Ni steel) and 4Cr5 Mo2V steel containing 1% Co (hereinafter referred to as 4Cr5Mo2V + Co steel) are shown in Table 1. The test was cast with ADC12 The chemical composition of aluminum alloy is shown in Table 2.
Table 1 Chemical compositions of the investigated die-casting die steels( mass fraction) % | |||||||
Material | C | Cr | Mo | V | Co | Ni | Si |
4Cr5Mo2V steel | 0.39 | 4.65 | 2. 21 | 0.46 | - | - | 0. 23 |
4Cr5Mo2V+Ni steel | 0.38 | 4.72 | 2.34 | 0. 51 | - | 1.02 | 0. 21 |
4Cr5Mo2V+Co steel | 0.41 | 4.67 | 2.40 | 0.48 | 1.03 | - | 0. 24 |
Table 2 Chemical Composition Of The ADC12 Aluminum Alloy % | |||||||||
Element | Cu | Mg | Mn | Fe | Si | Zn | Ti | Pb | Sn |
Quality Score | 1.74 | 0.22 | 0.16 | 0.76 | 10.70 | 0.87 | 0.064 | 0.035 | 0. 010 |
1.2 Test Method
The annealed 4Cr5Mo2V steel, 4Cr5Mo2V + Ni steel and 4Cr5Mo2V + Co steel were processed into test blocks as shown in Figure 1. After vacuum quenching, they were tempered twice, with a hardness of about 47 HRC, and finely ground to remove oxide scale.
The group number of the test block is embedded in the groove of the fixed mold, and the cavity of the die-cast aluminum alloy is set in the movable mold, as shown in Figure 2. A 500 t horizontal cold chamber die-casting machine and a self-designed mold were used for the die-casting test of ADC12 aluminum alloy sheet, and the aluminum alloy was reused. The temperature of molten aluminum is higher, 800°C, in order to accelerate the test (generally, the die casting temperature of ADC12 aluminum alloy is (650 120)°C). Since the temperature of the molten aluminum is 800℃, which does not reach the melting point of the Fe-A1 intermetallic compound, the resulting compound will exist in the molten aluminum as impurities after falling off. The repeated use of the molten aluminum will also cause the increase of impurities and strengthen the aluminum. The scouring effect of the liquid, thereby accelerating the test.
After the die-casting test, a stereo microscope was used to observe the aluminum adhesion phenomenon on the surface of the test block; an ultra-depth-of-field microscope was used to further observe the degree of aluminum adhesion and whether there were cracks on the surface of the test block.
2.Test Results And Analysis
2. 1 Surface Morphology Of The Test Block
2.1.1 Surface Sticking Aluminum
Figure 3 shows the surface morphology of the three steel test blocks without die casting and after 600,1000 times of die casting. It can be seen from Figure 3 (b, e, h) that after 600 times of die-casting, the 4Cr5Mo2V steel test block has the most serious aluminum sticking.
The 4Cr5Mo2V + Co steel test block sticks to the least aluminum. Figure 3 (c, f, i) shows that the aluminum adhesion on the surface of the three test blocks increased after 1,000 times of die-casting. The surface of the 4Cr5Mo2V steel test block has obvious aluminum adhesion, while the other two test blocks have slight aluminum adhesion. The 4Cr5Mo2V + Co steel test The lump of aluminum is the least and uniform, indicating that the diamond-containing 4Cr5Mo2V steel has the best resistance to liquid aluminum damage, while the 4Cr5Mo2V steel is the worst. The addition of drill and nickel elements is beneficial to stabilize the high temperature hardness of die steel 9-10, and the surface is not easy to "soften" during repeated contact with molten aluminum, so liquid aluminum erosion resistance is better, and aluminum adhesion is slight. During the die-casting test, the molten aluminum enters the cavity to contact the test block, and the uneven structure of the test block, the machining defect area and other local areas will slightly stick to the aluminum. The aluminum in the aluminum-bonded area will react with the steel to form Fe.} Al brittle intermediate compound, which will be broken and peeled under the scouring of the high-pressure aluminum liquid, resulting in pits on the mold surface, and more serious aluminum bonding under the scouring of the aluminum liquid .
2.1.2 Surface Cracks
Figure 4 shows the super-depth of field morphology of 4Cr5Mo2V steel, 4Cr5Mo2V + Ni steel and 4Cr5Mo2V + Co steel specimens after 1,000 times of die casting. It can be seen from Fig. 4(a) that there are a small number of micro-cracks distributed in a nearly net shape on the surface of the 4 Cry Mot V steel test block. The adhered aluminum and molten aluminum react with steel to form Fe.} Al compounds. The coefficient of thermal expansion of Fe.} Al is different from that of the matrix, resulting in a very small amount of microcracks in the adhered aluminum and Fe.} Al and the compounds. The scouring effect of the molten aluminum causes the microcracks to propagate, and the molten aluminum penetrates into the crack and further reacts with the matrix to form Fe 2 Al compounds. In the subsequent repeated die-casting process, the Fe.} Al compounds on the surface of the test block peel off to form pits. After pickling and ultrasonic cleaning, the surface of the test block appeared similar to the net-like aluminum liquid scouring characteristics. Figure 4 (b, c) shows that there are no cracks in the 4Cr5Mo2V + Co steel and 4Cr5Mo2V + Ni steel test blocks, indicating that the addition of 1% drill or molybdenum can not only reduce the surface adhesion of aluminum, but also reduce the cracking tendency of the mold and improve aluminum resistance Liquid damage performance. The addition of nickel and diamond non-carbide forming elements can improve the high-temperature hardness of the mold, and the diamond can also promote the dispersion and precipitation of molybdenum carbide during the tempering process, and enhance the precipitation hardening effect ‘z-} 3. The research by Ling Qian et al. has shown that the addition of austenite stabilizing elements to die-casting die steel can reduce stress concentration. Both drill and nickel are elements that expand the austenite zone, so 4Cr5Mo2V + Ni steel and 4Cr5Mo2V + Co steel die casting mold surfaces are not prone to cracks.
The molten aluminum in the actual die-casting process is very strong against the mold. According to the Fe-A1 phase diagram, the Fe-Al intermetallic compounds formed by the reaction of steel and molten aluminum are mainly FeAlz, Fez A15, FeA13, etc., which are brittle.The Al-rich phase of the aluminum alloy will break away from the matrix and enter the molten aluminum under the scouring of the molten aluminum, leaving pits on the surface of the mold. The combination of part of the aluminum alloy and the mold pits is relatively strong and does not fall off, and further forms Fe A1 compounds. The aluminum, Fe.} Al and compounds adhering there are prone to microcracks during cooling. Die-casting sheet has less liquid aluminum, so it solidifies faster, and the reaction between the mold and the liquid aluminum is slower. Therefore, the surface of the test block has fewer pits due to the reaction of Fe and Al, and more sticky aluminum is produced by the erosion of the aluminum liquid.
2. 2 Surface Hardness
Table 3 is the average value of the surface hardness of the three die steel test blocks after different times of die casting. The data in Table 3 shows that the surface hardness of the three kinds of test blocks all decrease slightly. As the number of die casting molds increases, it is equivalent to repeated tempering of the test block, so the hardness decreases. After 1,000 times of die-casting, the hardness of the 4Cr5Mo2V + Co steel test block has the smallest decrease, which is 1.4 HRC; the 4Cr5Mo2V steel test block has the most obvious decrease.
Obviously, it has dropped by 2. 8 HRC; the surface hardness of the 4Cr5Mo2V + Ni steel test block has dropped by 1. 8 HRC. Stable mold hardness is beneficial to reduce aluminum sticking, that is, it is beneficial to resist die-casting thermal damage.
Table 3 Surface hardness of the test blocks after die casting for different times % | ||||||
Material | No Die Cast | 200 Times | 400 Times | 600 Times | 800 Times | 1000 Times |
4Cr5Mo2V steel | 48.6 | 48.4 | 48.1 | 47.2 | 46.9 | 45.8 |
4Cr5Mo2V+Ni steel | 47.5 | 47.4 | 47.2 | 46.8 | 46.9 | 46.1 |
4Cr5Mo2V+Co steel | 47.7 | 47.5 | 47.1 | 46.5 | 46.2 | 45.9 |
After a long time tempering of the die steel, the martensite decomposes and the secondary carbides become coarser, resulting in a decrease in surface hardness. Both drill and nickel are non-carbide forming elements, which can replace Fe atoms to make the steel solid solution strengthen ‘5 to’ 8, so that the mold has higher high temperature strength and maintains higher hardness after repeated rapid heating and cooling. The China Die Casting Association has studied the element distribution in the quenched and tempered Cr-Mo-V-Ni steel, and found that during the tempering process, Ni elements will be enriched around the carbides, thereby hindering the carbon atoms in the ferrite around the carbides The continuous diffusion of the carbides increases the activation energy of carbide coarsening, hinders the growth of carbides, thereby reducing the hardness decline of nickel-containing 4Cr5Mo2V steel, and improving its resistance to molten aluminum damage.
The China Die Casting Association has studied the thermal stability and microstructure changes of die steel with 1% Ni and without Ni, and found that in the later stage of the thermal stability test, nickel will slow down the hardness of the die steel, thus making the steel better thermally stable Sex. Drilling is an element that expands the austenite phase zone. Adding drill to 4Cr5Mo2V steel can promote the dissolution of carbides during the austenitization process, increase the carbon content of austenite, and increase the stability of austenite, thereby increasing the retained austenite The amount of tensite and the hardness of martensite, and the drill can also promote the dispersion and precipitation of molybdenum carbide during the tempering process, and enhance the precipitation hardening effect z'-1.
The strengthening effect of nickel and drill on the matrix makes the die steel test block still have a higher surface hardness after repeated scouring of the molten aluminum, so that it is more resistant to erosion, which is beneficial to improve the resistance of the test block to the damage of the molten aluminum. The surface hardness of the test block and the degree of aluminum adhesion also show (see Figure 3, Table 3): The drilled 4Cr5 Mo2V steel test block has the least surface pits and aluminum adhesion after 1,000 times of die-casting, that is, the resistance to aluminum liquid damage is the best. Therefore, the strengthening effect of adding 1% Co to steel is greater than adding 1% Ni, both of which are conducive to improving the anti-aluminum damage performance of die steel.
3.Conclusion
- After die-casting aluminum alloy 1 000 times, the 4Cr5 Mo2V steel sample with drill sticks the least aluminum, and the 4Cr5Mo2V steel sample sticks the most aluminum, that is, the 4Cr5 Mo2V steel with drill has the best thermal damage resistance.
- After die-casting aluminum alloy 1,000 times, the surface hardness of 4Cr5Mo2V steel, 4Cr5Mo2V +Ni steel and 4Cr5Mo2V + Co steel specimens decreased by 2.8, 1.8 and 1.4 HRC, that is, the addition of nickel or drill can significantly improve Thermal damage resistance of 4Cr5Mo2V die-casting die steel.
Please keep the source and address of this article for reprinting: Effect of Drill and Nickel on the Thermal Damage Resistance of 4Cr5Mo2V Die Casting Die Steel
Minghe Die Casting Company are dedicated to manufacture and provide quality and high performance Casting Parts(metal die casting parts range mainly include Thin-Wall Die Casting,Hot Chamber Die Casting,Cold Chamber Die Casting),Round Service(Die Casting Service,Cnc Machining,Mold Making,Surface Treatment).Any custom Aluminum die casting, magnesium or Zamak/zinc die casting and other castings requirements are welcome to contact us.
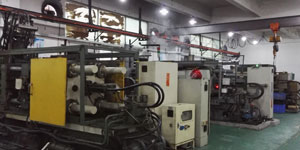
Under the control of ISO9001 and TS 16949,All processes are carried out through hundreds of advanced die casting machines, 5-axis machines, and other facilities, ranging from blasters to Ultra Sonic washing machines.Minghe not only has advanced equipment but also have professional team of experienced engineers,operators and inspectors to make the customer’s design come true.
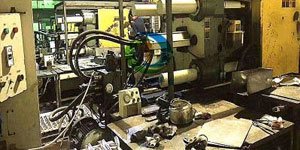
Contract manufacturer of die castings. Capabilities include cold chamber aluminum die casting parts from 0.15 lbs. to 6 lbs., quick change set up, and machining. Value-added services include polishing, vibrating, deburring, shot blasting, painting, plating, coating, assembly, and tooling. Materials worked with include alloys such as 360, 380, 383, and 413.
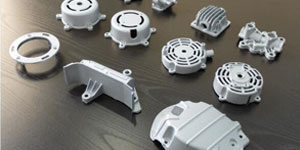
Zinc die casting design assistance/concurrent engineering services. Custom manufacturer of precision zinc die castings. Miniature castings, high pressure die castings, multi-slide mold castings, conventional mold castings, unit die and independent die castings and cavity sealed castings can be manufactured. Castings can be manufactured in lengths and widths up to 24 in. in +/-0.0005 in. tolerance.
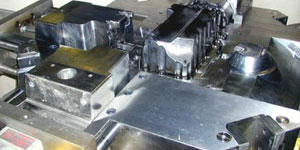
ISO 9001: 2015 certified manufacturer of die cast magnesium, Capabilities include high-pressure magnesium die casting up to 200 ton hot chamber & 3000 ton cold chamber, tooling design, polishing, molding, machining, powder & liquid painting, full QA with CMM capabilities, assembly, packaging & delivery.
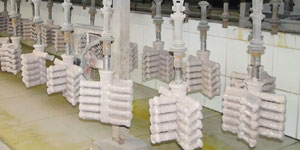
ITAF16949 certified. Additional Casting Service Include investment casting,sand casting,Gravity Casting, Lost Foam Casting,Centrifugal Casting,Vacuum Casting,Permanent Mold Casting,.Capabilities include EDI, engineering assistance, solid modeling and secondary processing.
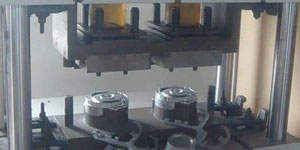
Casting Industries Parts Case Studies for: Cars, Bikes, Aircraft, Musical instruments, Watercraft, Optical devices, Sensors, Models, Electronic devices, Enclosures, Clocks, Machinery, Engines, Furniture, Jewelry, Jigs, Telecom, Lighting, Medical devices, Photographic devices, Robots, Sculptures, Sound equipment, Sporting equipment, Tooling, Toys and more.
What Can we help you do next?
∇ Go To Homepage For Die Casting China
→Casting Parts-Find out what we have done.
→Ralated Tips About Die Casting Services
By Minghe Die Casting Manufacturer |Categories: Helpful Articles |Material Tags: Aluminum Casting, Zinc Casting, Magnesium Casting, Titanium Casting, Stainless Steel Casting, Brass Casting,Bronze Casting,Casting Video,Company History,Aluminum Die Casting |Comments Off