10 Principles To Reduce Defects In Investment Castings
In the production process, foundry enterprises inevitably encounter casting defects such as shrinkage, bubbles, segregation, etc., resulting in low casting yield, and re-reflowing production faces a large amount of manpower and electrical energy consumption. How to reduce casting defects is an issue that has always been of concern to casting professionals.
1. Good castings start from high-quality smelting
Once the casting is to be poured, the smelting process must first be prepared, inspected and processed. If required, the lowest acceptable standard can be used. However, a better option is to prepare and adopt a smelting plan that is close to zero defects.
2. Avoid turbulent inclusions on the free liquid surface
This requires avoiding excessively high flow velocity at the front free surface (meniscus). For most metals, the maximum flow rate is controlled at 0.5m/s. For closed gating systems or thin-walled parts, the maximum flow rate will be increased appropriately. This requirement also means that the drop height of the molten metal cannot exceed the critical value of the "static drop" height.
3. Avoid laminar inclusions of surface condensed shells in molten metal
This requires that during the entire filling process, there should not be any front end of the metal flow to stop the flow in advance. The liquid metal meniscus in the early stage of filling must be kept in a movable state, not affected by the thickening of the surface condensate shells, and these condensed shells will become part of the casting. To achieve this effect, the front end of the molten metal can be designed to be continuously expanded. In practice, only the “uphill” ante bet can achieve a continuous ascent process. (For example, in gravity casting, flow upwards from the bottom of the sprue). This means: bottom-pouring gating system; no “downhill” form of molten metal falling or slipping; no large-area horizontal flow; no front-end flow stop of molten metal due to dumping or waterfall flow.
4. Avoid entrapment (generating bubbles)
Avoid air bubbles generated by the pouring system from entering the cavity. It can be achieved by the following methods: reasonable design of stepped sprue cups; reasonable design of straight runners to fill up quickly; rational use of "dams"; avoiding the use of "well" or other open gating systems; using small cross-section cross runners or The sprue uses ceramic filters near the junction of the runner; uses a degassing device; the pouring process is uninterrupted.
5. Avoid sand core pores
Avoid the bubbles generated by the sand core or sand mold from entering the molten metal in the cavity. The sand core must ensure a very low air content, or use proper exhaust to prevent the sand core pores. Unless you can ensure complete drying, you can not use clay-based sand core or mold repair glue.
6. Avoid shrinkage
Due to the influence of convection and unstable pressure gradient, castings with thick and large cross-sections cannot achieve upward feeding. Therefore, it is necessary to follow all the feeding rules to ensure a good feeding design, use computer simulation technology for verification, and actually cast samples. Control the flash level at the junction of the sand mold and the sand core; control the thickness of the mold coating (if any); control the alloy and mold temperature.
7. Avoid convection
Convection hazards are related to solidification time. Both thin-walled and thick-walled castings are not affected by convection hazards. For medium-thickness castings: reduce convection hazards through casting structure or technology; avoid upward feeding; turn over after pouring.
8. Reduce segregation
Prevent segregation and control it within the standard range, or the area allowed by the customer to exceed the limit. If possible, try to avoid channel segregation.
9. Reduce residual stress
Do not quench the light alloy with water (cold water or hot water) after solution treatment. If the casting stress does not seem large, polymer quenching media or forced air quenching can be used.
10. Given reference point
All castings must be given a positioning datum point for dimensional inspection and processing.
Please keep the source and address of this article for reprinting: 10 Principles To Reduce Defects In Investment Castings
Minghe Die Casting Company are dedicated to manufacture and provide quality and high performance Casting Parts(metal die casting parts range mainly include Thin-Wall Die Casting,Hot Chamber Die Casting,Cold Chamber Die Casting),Round Service(Die Casting Service,Cnc Machining,Mold Making,Surface Treatment).Any custom Aluminum die casting, magnesium or Zamak/zinc die casting and other castings requirements are welcome to contact us.
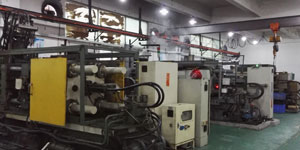
Under the control of ISO9001 and TS 16949,All processes are carried out through hundreds of advanced die casting machines, 5-axis machines, and other facilities, ranging from blasters to Ultra Sonic washing machines.Minghe not only has advanced equipment but also have professional team of experienced engineers,operators and inspectors to make the customer’s design come true.
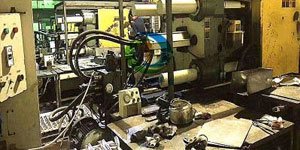
Contract manufacturer of die castings. Capabilities include cold chamber aluminum die casting parts from 0.15 lbs. to 6 lbs., quick change set up, and machining. Value-added services include polishing, vibrating, deburring, shot blasting, painting, plating, coating, assembly, and tooling. Materials worked with include alloys such as 360, 380, 383, and 413.
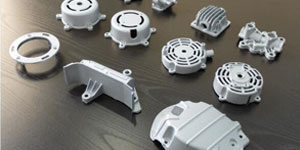
Zinc die casting design assistance/concurrent engineering services. Custom manufacturer of precision zinc die castings. Miniature castings, high pressure die castings, multi-slide mold castings, conventional mold castings, unit die and independent die castings and cavity sealed castings can be manufactured. Castings can be manufactured in lengths and widths up to 24 in. in +/-0.0005 in. tolerance.
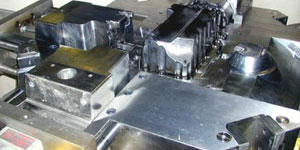
ISO 9001: 2015 certified manufacturer of die cast magnesium, Capabilities include high-pressure magnesium die casting up to 200 ton hot chamber & 3000 ton cold chamber, tooling design, polishing, molding, machining, powder & liquid painting, full QA with CMM capabilities, assembly, packaging & delivery.
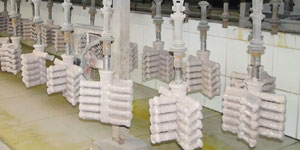
ITAF16949 certified. Additional Casting Service Include investment casting,sand casting,Gravity Casting, Lost Foam Casting,Centrifugal Casting,Vacuum Casting,Permanent Mold Casting,.Capabilities include EDI, engineering assistance, solid modeling and secondary processing.
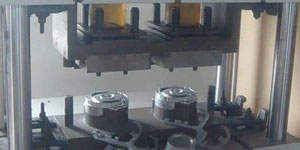
Casting Industries Parts Case Studies for: Cars, Bikes, Aircraft, Musical instruments, Watercraft, Optical devices, Sensors, Models, Electronic devices, Enclosures, Clocks, Machinery, Engines, Furniture, Jewelry, Jigs, Telecom, Lighting, Medical devices, Photographic devices, Robots, Sculptures, Sound equipment, Sporting equipment, Tooling, Toys and more.
What Can we help you do next?
∇ Go To Homepage For Die Casting China
→Casting Parts-Find out what we have done.
→Ralated Tips About Die Casting Services
By Minghe Die Casting Manufacturer |Categories: Helpful Articles |Material Tags: Aluminum Casting, Zinc Casting, Magnesium Casting, Titanium Casting, Stainless Steel Casting, Brass Casting,Bronze Casting,Casting Video,Company History,Aluminum Die Casting |Comments Off