The Treatment Of Steel Casting Deformation
In the entire manufacturing process of steel castings, deformation occurs in almost every process. The causes of casting deformation are mainly divided into two categories. One is internal reasons, which are mainly manifested as casting stress deformation and heat treatment stress deformation.
Casting stress deformation refers to the casting stress caused by the different solidification sequence and solidification rate of different parts in the solidification process of the casting. This stress will be released in a certain process after the casting is boxed, which will lead to the deformation of the casting. Heat treatment deformation is mainly due to the reduction of the strength of the casting after thermal expansion and softening during the heat treatment process, the deformation of the casting caused by its own gravity, and the deformation caused by the release of the stress accumulated in the structure during the transformation of the structure.
Generally, the former has a greater impact on the size and shape of castings.
There are many reasons for the deformation of castings, and deformation may occur in every process of the whole production process. If the design structure and process plan are unreasonable, improper modeling, boxing, cleaning or heat treatment operations, etc., can all cause the casting to be deformed. Some of the casting deformations caused by the above-mentioned reasons can be reduced or avoided by improving the design, revising the process, improving the operation level and subjectively strengthening the sense of responsibility. However, it is difficult to avoid the deformation of some castings at the current technical level, so that the correction work for the deformed castings appears.
Generally, the correction methods of casting deformation are divided into two categories, that is, the deformation of the casting is the correction method of pressurization or impact at room temperature (referred to as the cold correction method); the correction method of heating the casting to a certain temperature, pressurizing or squeezing, and supporting (Referred to as thermal correction method).
Cold Correction Method
The cold straightening method is based on the size of the deformed casting and the thickness of the section. It can be hammered, impacted or squeezed at room temperature by using a hand hammer, a large and small straightening machine, a water (oil) press or some simple pressure method. Correction method.
Practice has proved that it is difficult to achieve the expected effect for the correction of general casting deformation by cold correction. However, for the correction of deformation of high manganese steel castings, cold correction can only be adopted (determined by material properties).
The Hot Correction Method
The hot correction method is to heat the deformed casting to above the elastoplastic temperature zone of the material, and restore the deformation of the casting through external forces such as extrusion and bracing, so as to achieve the purpose of correction.
The heating temperature of the thermal correction method is roughly divided into two types. One is high temperature (that is, austenitizing temperature); the other is low temperature, which is the heating temperature of low temperature annealing or high temperature tempering. The two heating temperatures have their own advantages and disadvantages. The "high temperature" requires high requirements for the operator and the operation is difficult, but the correction time is short; the "low temperature" does not require high requirements for the operator, the operation is simple, and the correction success rate is high, but the correction time is relatively long. long. In terms of comprehensive pros and cons, the correction success rate is the main one, so we often use low temperature correction.
According to the heated parts of the deformed castings, the author divides the thermal correction method into two types: the correction method and the local correction method.
The operation of the correction method is simple and convenient, and the correction effect is good; while the local correction method has strict requirements on the correction site, sometimes it is necessary to build a stove, sometimes use a gas cutting gun to manually operate, for a long time baking, poor working conditions, and unsafe, correction The effect is not very satisfactory (theoretically, stress relief treatment should be carried out after correction). Therefore, in actual production, we still focus on the correction method, and try not to use the local correction method (except for individual castings that cannot be used for the correction method).
The correction effect of the correction method depends on the correctness of the correction furnace and heating method. Such as the furnace loading method of deformed castings (including the determination of the correction gap value of the deformed part, the correction of the weight and position of the pressure, the selection of the weight, the stop, the support, the shim, the platform, the wedge, etc.), the correction of the heating temperature ( High temperature or low temperature) determination. The correction gap value (hereinafter referred to as the gap value) is the determining condition of the correction effect.
- (1) No matter what kind of deformation, it cannot be completely eliminated. Only a series of measures can be taken to reduce the amount of deformation and control the amount of deformation within an acceptable range.
- (2) The focus of deformation lies in prevention: starting from the modeling aspect, especially the design of the correction amount through the re-deformation process; starting from the welding aspect, the design of welding anti-deformation braces, the selection of welding parameters, etc.; starting from the heat treatment aspect, focusing on the study of castings The placement of the furnace and the selection of heat treatment parameters.
- (3) The control of deformation involves the entire casting and manufacturing process, and it needs to go through various procedures, especially the control of key procedures, in order to do a real anti-deformation work.
Please keep the source and address of this article for reprinting:The Treatment Of Steel Casting Deformation
Minghe Die Casting Company are dedicated to manufacture and provide quality and high performance Casting Parts(metal die casting parts range mainly include Thin-Wall Die Casting,Hot Chamber Die Casting,Cold Chamber Die Casting),Round Service(Die Casting Service,Cnc Machining,Mold Making,Surface Treatment).Any custom Aluminum die casting, magnesium or Zamak/zinc die casting and other castings requirements are welcome to contact us.
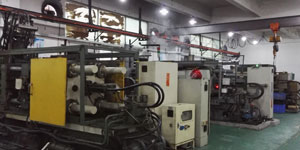
Under the control of ISO9001 and TS 16949,All processes are carried out through hundreds of advanced die casting machines, 5-axis machines, and other facilities, ranging from blasters to Ultra Sonic washing machines.Minghe not only has advanced equipment but also have professional team of experienced engineers,operators and inspectors to make the customer’s design come true.
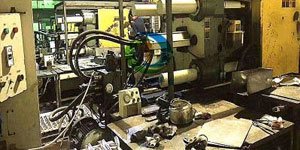
Contract manufacturer of die castings. Capabilities include cold chamber aluminum die casting parts from 0.15 lbs. to 6 lbs., quick change set up, and machining. Value-added services include polishing, vibrating, deburring, shot blasting, painting, plating, coating, assembly, and tooling. Materials worked with include alloys such as 360, 380, 383, and 413.
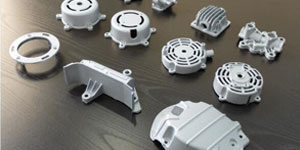
Zinc die casting design assistance/concurrent engineering services. Custom manufacturer of precision zinc die castings. Miniature castings, high pressure die castings, multi-slide mold castings, conventional mold castings, unit die and independent die castings and cavity sealed castings can be manufactured. Castings can be manufactured in lengths and widths up to 24 in. in +/-0.0005 in. tolerance.
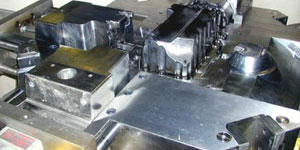
ISO 9001: 2015 certified manufacturer of die cast magnesium, Capabilities include high-pressure magnesium die casting up to 200 ton hot chamber & 3000 ton cold chamber, tooling design, polishing, molding, machining, powder & liquid painting, full QA with CMM capabilities, assembly, packaging & delivery.
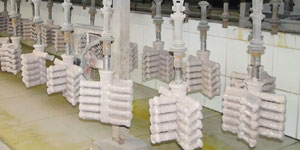
ITAF16949 certified. Additional Casting Service Include investment casting,sand casting,Gravity Casting, Lost Foam Casting,Centrifugal Casting,Vacuum Casting,Permanent Mold Casting,.Capabilities include EDI, engineering assistance, solid modeling and secondary processing.
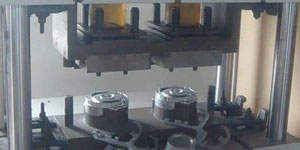
Casting Industries Parts Case Studies for: Cars, Bikes, Aircraft, Musical instruments, Watercraft, Optical devices, Sensors, Models, Electronic devices, Enclosures, Clocks, Machinery, Engines, Furniture, Jewelry, Jigs, Telecom, Lighting, Medical devices, Photographic devices, Robots, Sculptures, Sound equipment, Sporting equipment, Tooling, Toys and more.
What Can we help you do next?
∇ Go To Homepage For Die Casting China
→Casting Parts-Find out what we have done.
→Ralated Tips About Die Casting Services
By Minghe Die Casting Manufacturer |Categories: Helpful Articles |Material Tags: Aluminum Casting, Zinc Casting, Magnesium Casting, Titanium Casting, Stainless Steel Casting, Brass Casting,Bronze Casting,Casting Video,Company History,Aluminum Die Casting |Comments Off